by Elizabeth Hines | Apr 3, 2018 | Blog, Content Marketing, Current Events, Manufacturing & Distribution, Marketing, Supply Chain
In many cases, automation in manufacturing creates leaner, more efficient operations. Efficiency facilitates new opportunities and business growth, which in turn allow for job creation.
The rise of artificial intelligence (AI) and its applications in manufacturing have driven a palpable fear that mass job loss is on the horizon. We have to wonder: is the threat as real and as imminent as many think? Like many things, the answer is more nuanced than a simple yes or no.
A McKinsey Global Institute report predicts that automation could cause the loss of between 39 and 73 million jobs by 2030 in the U.S. alone. Clearly, the AI genie will not be put back into its bottle. However, this doesn’t mean that all jobs across all sectors will be affected evenly.
Generally, low-skill jobs are more susceptible to replacement by AI. This is especially true in industries like retail, which has worked to automate many aspects along the purchase journey, including processes designed to get packages into consumers’ hands faster.
Not the end of the world
Oddly enough, 73 million lost jobs doesn’t spell all doom and gloom. Yes, people will lose jobs — that is inevitable. Automation, however, will create many more.
Think about it: In many cases, automation creates leaner, more efficient operations. Efficiency facilitates new market opportunities and business growth, which in turn allow for expansion and job creation. And these new jobs aren’t the low-skill positions of their pre-automation predecessors. They’re operating new technology, supervising automated processes, and other higher-paying opportunities.
Amazon: Case in point
Consider the retail industry’s brick-and-mortar boom and bust and the rise of e-commerce. As stores shuttered, companies had to downsize the number of individuals they employed. Then, as e-commerce boomed, e-retailing companies were able to bring on more employees — often at higher salaries than in traditional retail.
Amazon’s expansion to the “once-thriving factory town” of Fall River, Mass., offers a prime example. The city, which boasted nearly 20,000 manufacturing jobs in 1991, saw that number dip below 4,000 by 2015 — in large part due to automation. The 2016 arrival of an Amazon fulfillment center was the single largest job-creation event in recent memory.
Employment at the Fall River center has crept above 2,000 in just over a year. And it’s apparent that number will keep rising and that humans won’t be phased out anytime soon. In fact, rather than replace human workers, Amazon’s technology helps each become more efficient. That stimulates Amazon’s growth and the need for more fulfillment centers and more talent to fill those jobs.
While the majority of the Fall River center’s jobs are not skilled and pay reflects that, other benefits such as overtime, tuition aid, and company shares make annual compensation comparable to or better than what local textile mills once paid. Fulfillment center jobs certainly pay above traditional retail and offer employees the opportunity to work withartificial intelligence — rather than in competition with it.
A double-edged sword
AI in the warehouse may stimulate job growth. But those most likely to lose their jobs to automation — low-skill workers — may not possess the transferable skills to be successful in the new wave of jobs created by technology. For example, would a former factory worker who put together boxes for fulfillment be hirable for a position operating custom box-cutting machinery?
Amazon, again, exemplifies a solution. The company offers its workers significant training and education to breach any skill gaps. Those who have never had experience in a warehouse or operating technology will need companies to invest in their training to ensure those who have lost their jobs to automation will have a place in the new economy.
History repeating
This isn’t the first time we’ve encountered such an issue. Before ATMs were the ubiquitous cash-dispensing machines, many thought them the great disruptor of the banking industry. The bank teller’s role was sure to become obsolete.
What actually happened is that ATMs led to more efficiently run banks. While some jobs were lost, banks were actually able to open up more branch locations, which led to the creation of more jobs.
Will automation in the warehouse cause the same scenario to happen? Will organizations become more efficient, allowing them to grow and hire more workers at better, higher paying jobs? In many cases, it looks like it already has.
Related posts:
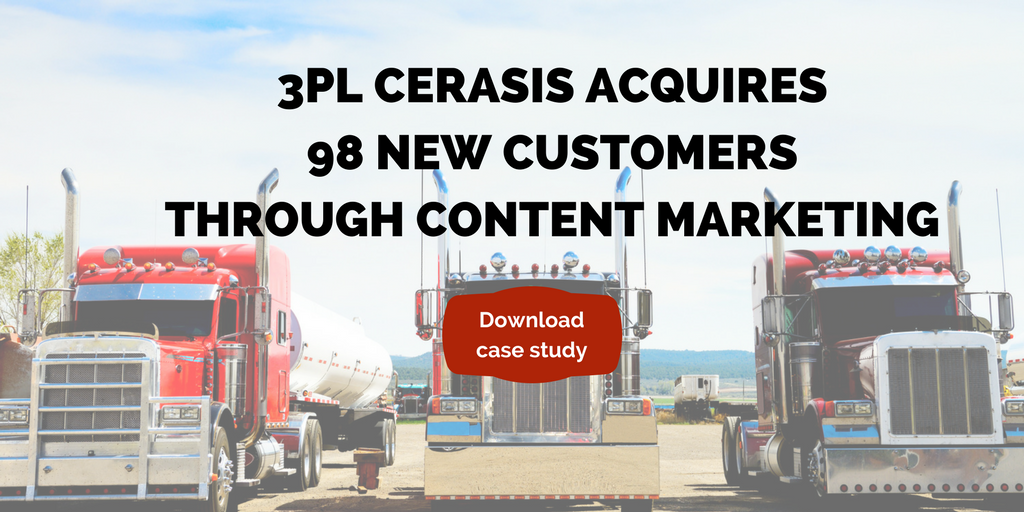
by Elizabeth Hines | Nov 23, 2016 | Blog, Strategy, Supply Chain, Warehousing & Materials Handling
The evolution of driverless robotic vehicles continues unabated. But what will it take for them to overtake certain warehouse tasks?
A lucky few have already experienced it — the thrill of taking their hands off the steering wheel and letting the car take care of the driving. As a reporter from the Guardian rode in the driver’s seat of a multi-million euro research vehicle “Jack” by Audi on the autobahn, she observed it carried out maneuvers so smoothly “it felt like the car was participating in a courtly dance with others on the road.”
Despite such glowing reviews and the unabated evolution of driverless vehicles, Jack and many its counterparts will not be available for mass consumption for another decade or so.
AGVs and today’s warehouse
In the world of material handling, the notion of driverless has been around for 60 years since the first Automated Guided Vehicle (AGV) appeared in a grocery warehouse. High-tech warehouse operations are already used to the sight of AGVs performing tasks, such as the vertical storage and retrieval of pallets and the loading and unloading of pallets onto outbound trailers.
Driverless robotic vehicles, on the other hand, have generally been assigned to low complexity and repetitive horizontal movement of materials, as well as assisted order picking that involves a high degree of machine and human interaction. Although it may sometimes sound as if driverless vehicles are about to phase out forklift drivers altogether, Toyota Material Handling, which has developed an Autopilot AGV driverless forklift range, notes in a blog post that “there is still value in human operators in an automated warehouse. Human operators are far more capable of identifying issues in the immediate environment and any problems with picking orders. The role of the human operator in an automated warehouse will be more dynamic and varied as the ‘grunt work’ is now tasked to the automated system.”
This argument echoes the challenge that makers of driverless automobiles have expressed: In order for the technology to reach the next level of effectiveness, it has to assume “human” qualities. While the driverless car comes to a complete stop at the sight of a yellow light, the human driver is more likely to speed up to beat the red light, a fact that has been blamed for a number of collisions during testing of a Google autonomous vehicle prototype.
The potential of driverless vehicles
That being said, driverless robotic vehicles hold enormous potential. In an interesting webcast on DC Velocity — which addresses the technology’s role in distribution operations that include horizontal transport and full-case picking applications — two experts tout ROI and productivity gains.
DC Velocity Senior Editor David Maloney and Marc Wulfraat, president of global supply chain and logistics consulting firm MWPVL International, estimate a three-year ROI is possible and that 20-25% productivity gains for order picking are realistic, as long as certain obstacles are overcome. For example, old legacy applications rarely integrate well with newer real-time technologies. If the two are forced together, it may happen at the expense of speedy processes, thus negating the effect of why the driverless technology was introduced in the first place.
Maloney and Wulfraat explain: “In high-density full-case picking environments (e.g., grocery distribution), an order selector can pick 175 – 200 cases/hr or one case every 18 – 20 seconds. If a 5-second delay due to system latency is introduced, then this would result in a major decrease (19 – 24%) in order selection productivity to 141 – 157 cases/hr. In a facility shipping 1 million cases/week with labor cost of $23/hour fully loaded, this would add around $1.6 M of warehouse labor expense to the operation. Clearly, this type of technology cannot add any system latency, which suppliers are working hard to guarantee.”
Another challenge arises when multiple vehicles have to pass within the same operating aisle. Considering the minimum clearance that it takes for a robotic vehicle to pass another without safety sensors bringing it to a halt could pose a problem in distribution centers with narrow aisle widths.
Still, in the big scheme such challenges pale in comparison to how far the technology has already come. When it comes to automating the horizontal transfer of products in a warehouse or distribution center, driverless robotic vehicles are undoubtedly the answer.
What do you consider to be the main challenges to full-scale adoption of driverless robotic vehicles in the warehouse or DC?
This article originally appeared on EBN Online.
Related posts: