by Jennifer Hart Yim | Jun 22, 2015 | Blog, Manufacturing & Distribution, Strategy, Supply Chain
This article is part of a series of articles written by MBA students and graduates from the University of New Hampshire Peter T. Paul College of Business and Economics.
Melanie Payeur graduated from the University of New Hampshire in 2007 with a degree in Mechanical Engineering. She has since worked in various roles supporting manufacturing and packaging operations in the food and beverage industry.
Do you know where your byproducts go?
Manufacturing often produces some sort of physical byproduct. Examples range from plastic strapping on a pallet of corrugate boxes to carbon dioxide collected off a tank of fermenting beer. Byproducts are the unspoken of and often neglected “cousin” of manufacturing.
Byproducts of manufacturing can be compared to the stage crew at a Broadway show or on a Hollywood movie set. They serve an important purpose. Without the lights, cameras, and curtains, there is no show. Similarly, without plastic strapping, a pallet of corrugate would fall over during transport because it wasn’t properly secured.
The stars of the show are the finished goods on store shelves. Just like people don’t stick around to see the name of the on-set hair-stylist when the credits roll at a movie, consumers often don’t think about the byproducts associated with the packaged food they eat or other goods they purchase. It’s possible that they don’t even know these things exist.
However, consumers are becoming more conscious of supply chain issues. Many have an awareness what Fair Trade is in association with sourcing of products such as coffee and cocoa beans. They discuss agricultural sourcing and the ethical (or not) treatment of animals raised to be part of the food chain. Even the effects of emissions and chemical waste on the environment are among topics of which many consumers have some awareness.
Plastic old, Plastic new
What about the plastic strapping on that pallet of corrugate though? Where does it go? Who even knows it exists other than the operator that cuts it off the pallet in the factory? Could it become a plastic bottle someday? Or a swing set? Maybe it will become plastic strapping again?
While countless other types of byproducts exist, plastic is a particularly interesting example. Fluctuations in the price of petroleum are directly correlated to the price of brand new, non- recycled plastic pellets. It is completely possible, and often realistic, that it is less expensive to create brand new plastic strapping than it is to recycle old strapping.
Trailer Bags and Trash Bowls
Creative and novel uses of byproducts are happening today. One example is a Swiss company called Freitag who produces trendy messenger bags, wallets, and purses from old side panel tarps (popular on tractor trailers in Europe). At the end of their useful life on the road, these tarps are purchased by Freitag and sewn into functional accessories.
Another example specifically related to plastic are Garbage Bowls made famous by Food Network host, Rachael Ray. These bowls are made from recycled pieces of broken plates. There’s a byproduct in there somewhere!
While these are great examples of repurposing byproducts into something new, the truth is that Freitag was originally looking for a material that would create a durable and functional product. Lucky for them, reusing something that might have otherwise been thrown away is a great marketing story. They charge an average of $200 for a standard messenger bag. Is it realistic that the reverse situation can create profits? Can we find another use for production process byproducts which would create a trendy or otherwise highly desirable product?
Can we do better than throwing our byproducts away?
If it’s not a company’s core competency, it probably shouldn’t get into the business of designing handbags. However, as supply chain professionals, we should understand all of the byproducts of our manufacturing process; especially those related to materials that we source as inputs, like plastic strapping.
It is as important to look at the waste stream from our process as it is to examine how we source raw materials. Are we recycling our byproducts? Is there someone who is looking for our ‘trash’ as an input to their process? Do we have the opportunity to have a profitable side business as a coincidental supplier to someone else? At the very least, can we do better than throwing our byproducts away?
An example of success can be seen in the food manufacturing industry. Some companies donate or sell their byproducts to the Bakery Feeds Program. This organization creates animal feed out of food byproducts such as misshapen cupcakes and other edible process waste. It might be cost neutral to dispose of waste in this way, but that is better than otherwise paying for disposal.
I challenge you to examine the waste streams associated with your process. Identify where at least one of your byproducts could go. From here to there and there to here, your byproducts could end up anywhere.
by Jennifer Hart Yim | Jun 18, 2015 | Blog, Logistics, Manufacturing & Distribution, Strategy, Supply Chain
This article is part of a series of articles written by MBA students and graduates from the University of New Hampshire Peter T. Paul College of Business and Economics.
Ben Minerd received his B.S. in Computer Engineering from the University of New Hampshire in 2011 and will be completing his MBA from UNH in May 2015. When not working as a systems engineer, Ben enjoys skiing, hiking, and flying drones.
Some of you technologically curious readers may be familiar with Moore’s Law which predicted that the number of transistors in a dense integrated circuit would double every two years. What all that nerd speak (as a nerd I can use that phrase) boils down to is that the processing capability of electronic chips is increasing at a crazy rate. Like, scary fast.
On the flip side, electronics are really cheap these days. Yes, the $10,000 Apple Watch might be a tad pricey, but I’m talking about the industry as a whole. You can buy a computer that fits in your pocket for $200 that is many hundreds, maybe thousands, of times more powerful than my first computer and I’m one of those whiny millennial youngsters.
How can consumer electronics companies afford to sell their scary fast devices this cheaply? One reason is that the devices are being made by other devices (cue ominous music), as automation and electronics manufacturing are natural complements of each other. But another big factor in the cheap tech equation is the ever-increasing separation of technology development from technology manufacturing.
Contract Manufacturing
Big name companies like Apple, Google, Microsoft, and Amazon are doing less and less of their own widget building these days in favor of contract manufacturing (or CM). Contract manufacturing is essentially the outsourcing of your products’ fabrication and assembly to some other company (who is hopefully better at it than you are).
In theory, using a contract manufacturer should lower your costs and give you access to capabilities that you wouldn’t have access to otherwise. This is especially true of small businesses looking to produce physical goods (versus intangibles like software), where the up-front cost of building your own factory is immense and maybe even a non-starter. Or maybe you’re a big tech company who isn’t good at making hardware (ahem, Google) and you want to stick to your core competencies.
Whatever your reason, contract manufacturing is the unicorn that will slash your costs with its rainbow laser beam eyes. Well, maybe not entirely.
Hidden Costs
To loosely paraphrase Pee-wee Herman, every decision we make in business has a big ‘but’. For the economist reader, you can equate this with TANSTAAFL—There Ain’t No Such Thing As A Free Lunch. One action almost always leads to some other potentially unexpected outcome. Certain people have even gone so far as to say this is always the case (some guy named Isaac Newton).
One of the biggest contributors to hidden costs within contract manufacturing is the loss of control over your production processes. While this might be obvious or even desired, there may be some complications as a result of this new relationship that you hadn’t thought of previously.
Communication is always an important topic, but even more so when it comes to contract manufacturing. Not only may your production team physically reside on the other side of the globe, but things like language, culture, and time zone differences can make it difficult to keep good lines of communication open.
Quickly ramping up or ramping down production to meet changing demand can become a lot more challenging, too. This is partly due to the nature of the shared resources that you are buying access to when you team up with a CM.
A classic example of a culmination of these issues came from Cicso in the early 2000’s, back when out-sourcing was in its infancy. Cisco had been riding the surging wave of growth in the telecommunications industry which starting leading to supplier shortages. Shortly thereafter, the bottom fell out of telecom and Cisco forgot to turn off the contract manufacturing tap. Before long, Cisco’s raw-parts inventory rose by more than 300% from Q3 to Q4 2000, leading to a $2.2 billion write-off of inventory. Wall Street responded as you might expect, causing Cisco’s stock to fall by 50%.
The Human Cost
Perhaps the greatest hidden cost is one that may never make it to your company’s balance sheet: exploitation of workers in the developing countries where many contract manufacturers do business. It’s no secret that the biggest driver behind outsourcing is low labor costs. While it’s not always apples-to-apples to compare a production worker’s wage in China to one in the U.S., by any measurement the difference is more than a factor of 10 (although that number is dropping).
This dirty little secret of the consumer electronics industry came to light in 2012 when it was discovered that Foxconn, the largest electronics CM with over $100 billion in revenue and manufacturer of the Apple iPad, was mistreating some of their workers. Conditions grew so bad that in some cases workers decided to jump to their death rather than survive in that environment.
Bottom Line
Contract manufacturing might very well still be the right choice for you, just keep in mind that you may have more “unknown unknowns” than you had, well, known about. The more you can discuss with your CM candidate up front, the better your relationship will likely be. Also, some of these “gotcha’s” can be planned for in the agreement between you and your CM, so don’t skimp on the up-front work. And remember, there is no unicorn with rainbow laser beam eyes. That I know of.
by Jennifer Hart Yim | May 21, 2015 | Blog, Strategy, Supply Chain
This article is part of a series of articles written by MBA students and graduates from the University of New Hampshire Peter T. Paul College of Business and Economics.
Lindsey Marley completed dual undergraduate degrees in Business and History at Southern New Hampshire University. She is in her final semester of the MBA program at the University of New Hampshire. In her free time she enjoys traveling, reading, and spending time with her husband and their two dogs.
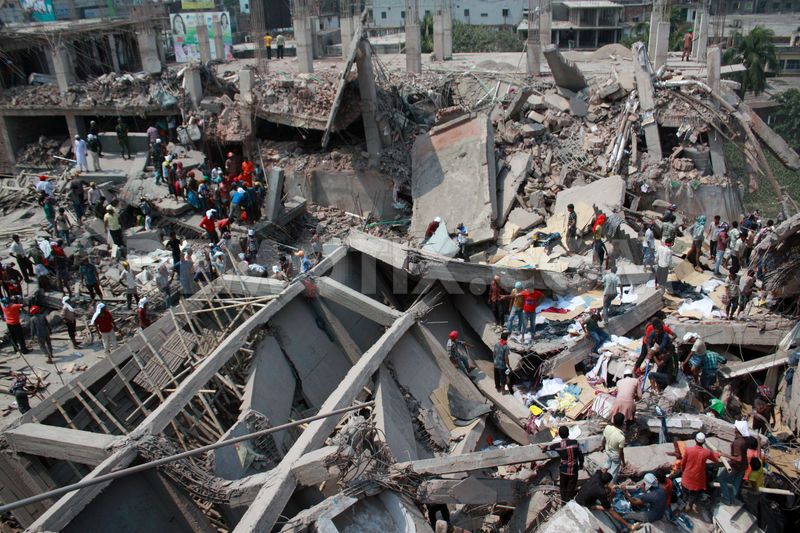
On November 24, 2012 there was a deadly fire at a garment manufacturing company which killed 112 people in Dhaka, Bangladesh. Another manufacturing facility in Dhaka collapsed on April 24, 2013 killing 142 people. The ready-made garment manufacturing industry in Bangladesh has grown to $19 billion dollars and is reported to be one of the most unsafe industries in the world. The consequences of corporations being lax in the sourcing of their products can have horrific consequences for people, the environment, and the company. Consumers in developed countries are demanding companies be more responsible in their sourcing as a result of the wealth of information found on the Internet about the production of goods and services.
Responsible Sourcing
The concept of responsible sourcing is in itself still being developed; however, responsible sourcing generally consists of two parts – people and the environment. There are several organizations which have provided guidelines to assist companies in developing their own code of conduct including:
One such industry-specific coalition, which was created in response to numerous tragedies such as those described above, is the Alliance for Bangladesh Worker Safety which was founded in 2013 by a group of North American apparel companies and retailers.
Alliance: A Global Response
The Alliance created a binding five-year agreement to improve worker safety among the largest importing companies of Bangladesh garments. Some of the most well-known participants include Limited, Carter’s Inc, Fruit of the Loom, Gap Inc, Kohl’s Department Stores, LL Bean, Macy’s, Target Corporation, and Wal-Mart Stores, Inc. The Alliance is accomplishing its mission through the use of a collective fund which was $42 million at the time of its creation.
The International Labour Organization has assisted the Alliance in the creation of an operational guide. The Alliance focuses on opening lines of communication between employees and management to ensure worker safety. Interviews with employees regarding existing safety practices and training are conducted and then safety discussions are coordinated between those employees and members of management. The Alliance also requires assessments be completed of garment manufacturing plants by independent engineers to certify worker safety and the structural soundness of facilities. After the initial evaluation and recommendations, the independent auditors return to confirm the changes previously discussed have been made as well as to assess the manufacturer’s ongoing compliance.
Had the Alliance been in place prior to the fire in 2012 the auditors would have found the illegally stored mounds of fabric and yarn, which accelerated the spread of flames, and required the materials to be stored in a more appropriate and safe manner. Another aspect of the fatal fire which could have been prevented was the allegation of factory managers directing employees to ignore the fire alarm. This wasted precious time for workers to exit the building safely. Ultimately, this lead many employees, trapped by the flames and smoke, to jump from upper floors to the rooftops of surrounding buildings or to their deaths. The tripartisan relationship that is created between the Alliance, employees, and management representatives is critical to ensure a clear, consistent message regarding basic employee safety. This communication helps to empower workers and could have encouraged them to challenge management’s direction to disregard the alarm when the fire broke out.
With regard to the building collapse of 2013, it was determined the four upper floors had been constructed illegally without permits. The three pronged scope of the Alliance (worker safety, fire safety, and structural soundness) again could have prevented this tragedy. In this situation, management at the garment manufacturing facility were aware of structural concerns before the collapse, but as in the case of the fire, ignored the risk and kept the factory open. Engineers working for the Alliance drill into factory walls to determine the structural integrity of the concrete and rebar used during construction to determine structural soundness.
Your Span of Control
These examples highlight the importance of maintaining a large span of control throughout your supply chain to ensure responsible sourcing. It is no small task to exercise this breadth of control for any company; however, companies can utilize the resources provided by the organizations listed above to develop their own requirements for responsible sourcing and supplier relationships. Companies can derive the maximum consumer exposure by enforcing responsible sourcing across their entire supply chain. It is also important to engrain this behavior into the culture particularly among employees who have the most interactions with the ultimate consumer.
Communicating to Your Customers
Consumer communication is the final piece of the responsible sourcing puzzle which brings together the voluntarily socially responsible company with their expecting consumer base. Responsible sourcing without informing consumers is a waste of good public relations. Many companies bury the information about their responsible sourcing efforts on the corporate website where consumers have to hunt for the information. Some coalitions and third party companies provide the insignia to compliant participants as a means of notifying consumers of their membership, but that is not always an option. If possible, a company’s commitment to responsible sourcing should be quickly and clearly communicated on its product packaging, in its digital footprint, and in the way it conducts and manages its supply chain.
The fast food giant Chipotle consistently communicates its commitment to responsibly sourced ingredients in its signage, website, commercials, and in its direct to consumer communications at the individual locations. The pervasive nature of the company’s responsible sourcing efforts has been strongly rewarded by its ever-growing customer base. In a time where consumers are switching brands to support socially responsible companies, it is imperative to keep a company’s responsible sourcing objectives, actions, and accomplishments at the forefront of consumer’s minds.
by Jennifer Hart Yim | May 21, 2015 | Blog, Strategy, Supply Chain
This article is part of a series of articles written by MBA students and graduates from the University of New Hampshire Peter T. Paul College of Business and Economics.
Lindsey Marley completed dual undergraduate degrees in Business and History at Southern New Hampshire University. She is in her final semester of the MBA program at the University of New Hampshire. In her free time she enjoys traveling, reading, and spending time with her husband and their two dogs.
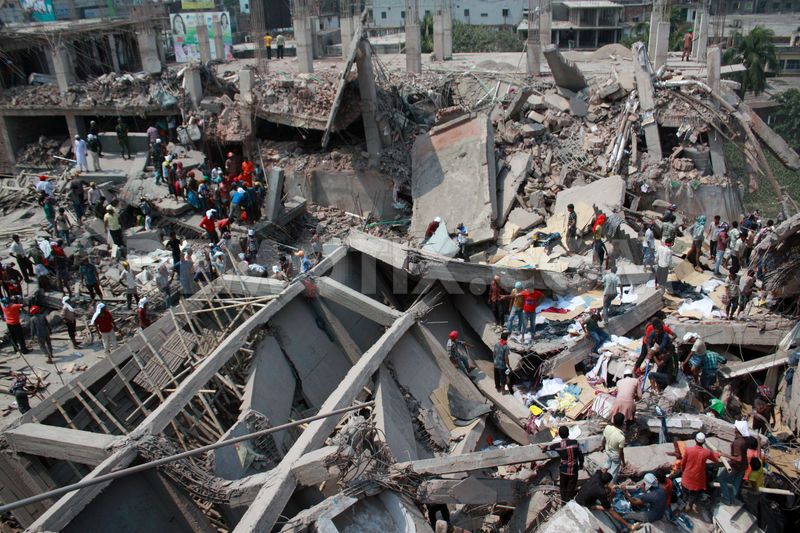
On November 24, 2012 there was a deadly fire at a garment manufacturing company which killed 112 people in Dhaka, Bangladesh. Another manufacturing facility in Dhaka collapsed on April 24, 2013 killing 142 people. The ready-made garment manufacturing industry in Bangladesh has grown to $19 billion dollars and is reported to be one of the most unsafe industries in the world. The consequences of corporations being lax in the sourcing of their products can have horrific consequences for people, the environment, and the company. Consumers in developed countries are demanding companies be more responsible in their sourcing as a result of the wealth of information found on the Internet about the production of goods and services.
Responsible Sourcing
The concept of responsible sourcing is in itself still being developed; however, responsible sourcing generally consists of two parts – people and the environment. There are several organizations which have provided guidelines to assist companies in developing their own code of conduct including:
One such industry-specific coalition, which was created in response to numerous tragedies such as those described above, is the Alliance for Bangladesh Worker Safety which was founded in 2013 by a group of North American apparel companies and retailers.
Alliance: A Global Response
The Alliance created a binding five-year agreement to improve worker safety among the largest importing companies of Bangladesh garments. Some of the most well-known participants include Limited, Carter’s Inc, Fruit of the Loom, Gap Inc, Kohl’s Department Stores, LL Bean, Macy’s, Target Corporation, and Wal-Mart Stores, Inc. The Alliance is accomplishing its mission through the use of a collective fund which was $42 million at the time of its creation.
The International Labour Organization has assisted the Alliance in the creation of an operational guide. The Alliance focuses on opening lines of communication between employees and management to ensure worker safety. Interviews with employees regarding existing safety practices and training are conducted and then safety discussions are coordinated between those employees and members of management. The Alliance also requires assessments be completed of garment manufacturing plants by independent engineers to certify worker safety and the structural soundness of facilities. After the initial evaluation and recommendations, the independent auditors return to confirm the changes previously discussed have been made as well as to assess the manufacturer’s ongoing compliance.
Had the Alliance been in place prior to the fire in 2012 the auditors would have found the illegally stored mounds of fabric and yarn, which accelerated the spread of flames, and required the materials to be stored in a more appropriate and safe manner. Another aspect of the fatal fire which could have been prevented was the allegation of factory managers directing employees to ignore the fire alarm. This wasted precious time for workers to exit the building safely. Ultimately, this lead many employees, trapped by the flames and smoke, to jump from upper floors to the rooftops of surrounding buildings or to their deaths. The tripartisan relationship that is created between the Alliance, employees, and management representatives is critical to ensure a clear, consistent message regarding basic employee safety. This communication helps to empower workers and could have encouraged them to challenge management’s direction to disregard the alarm when the fire broke out.
With regard to the building collapse of 2013, it was determined the four upper floors had been constructed illegally without permits. The three pronged scope of the Alliance (worker safety, fire safety, and structural soundness) again could have prevented this tragedy. In this situation, management at the garment manufacturing facility were aware of structural concerns before the collapse, but as in the case of the fire, ignored the risk and kept the factory open. Engineers working for the Alliance drill into factory walls to determine the structural integrity of the concrete and rebar used during construction to determine structural soundness.
Your Span of Control
These examples highlight the importance of maintaining a large span of control throughout your supply chain to ensure responsible sourcing. It is no small task to exercise this breadth of control for any company; however, companies can utilize the resources provided by the organizations listed above to develop their own requirements for responsible sourcing and supplier relationships. Companies can derive the maximum consumer exposure by enforcing responsible sourcing across their entire supply chain. It is also important to engrain this behavior into the culture particularly among employees who have the most interactions with the ultimate consumer.
Communicating to Your Customers
Consumer communication is the final piece of the responsible sourcing puzzle which brings together the voluntarily socially responsible company with their expecting consumer base. Responsible sourcing without informing consumers is a waste of good public relations. Many companies bury the information about their responsible sourcing efforts on the corporate website where consumers have to hunt for the information. Some coalitions and third party companies provide the insignia to compliant participants as a means of notifying consumers of their membership, but that is not always an option. If possible, a company’s commitment to responsible sourcing should be quickly and clearly communicated on its product packaging, in its digital footprint, and in the way it conducts and manages its supply chain.
The fast food giant Chipotle consistently communicates its commitment to responsibly sourced ingredients in its signage, website, commercials, and in its direct to consumer communications at the individual locations. The pervasive nature of the company’s responsible sourcing efforts has been strongly rewarded by its ever-growing customer base. In a time where consumers are switching brands to support socially responsible companies, it is imperative to keep a company’s responsible sourcing objectives, actions, and accomplishments at the forefront of consumer’s minds.
by Jennifer Hart Yim | May 20, 2015 | Blog, Manufacturing & Distribution, Strategy, Supply Chain, Warehousing & Materials Handling
This article is part of a series of articles written by MBA students and graduates from the University of New Hampshire Peter T. Paul College of Business and Economics.
David Chadwick is an MBA student at the University of New Hampshire with a background in retail store management and electrical engineering.
If technology continues to advance, humans may be obsolete in the supply chain as a result of both automation and RFID utilization. Both technologies have been introduced into the supply chain over the past decade, resulting in a major shift in performance and costs. While automation is a process which can navigate product throughout facilities, RFID can improve efficiency dramatically as well as being the major driver for the elimination of human involvement in the supply chain.
RFID (Radio Frequency Identification) is a form of extremely low-power data communication between a RFID scanner and an RFID tag. The tags are placed on any number of items, ranging from individual parts to shipping labels. The RFID tag itself consists of a microchip and antennae, usually without a battery to power it. The tags can be printed using special printers, which wirelessly load the identifying information to the tags. The information on the tags can be used for a wide variety of tasks. When an item goes through the RFID scanners, information is read from the tag, which could include any amount of information, such as:
- Order ID number
- Product bin location
- Order status
- Serial numbers for individual product components
- Location logs
The information is not limited to just holding ID and serial numbers. Since the information can be updated and transferred through any RFID receiver when in range, it can be joined with other software to update databases, send information online, and more. The amount of information that RFID can provide can be matched with order management systems to track shipment and stock locations automatically as the products move through warehouses and trucks. Powerful receivers can also track the exact location of products within a warehouse in real time, instead of relying on time and location logs to determine the location. This has been a major benefit to UPS, who’ve had RFID tracking chips in their warehouses for over ten years.
The largest problem facing supply chain management today is the potential for the occurrence of devastating errors. These errors could lead to trucks leaving product behind, not stocking to capacity, losing product, or delivering to the wrong locations. There are numerous reasons for such errors to occur, but the most common factor in their inception is human error. Much of the errors faced result from manual inspection and control over product flow in warehouses by humans. Many systems still operate using written data tables and checklists, which can be written incorrectly. Despite major advancements in technology over the past decade, the digital world is being sourced by analog supply chains. This is an aspect which RFID control can create beneficial change.
RFID can lead to completely autonomous warehouses and distribution centers. This can be seen in current warehouses with high levels of automation, where picking machines transport bins of product to a central sorting area to be boxed, before returning to their location. Zebra uses this technique to ensure product location accuracy as a means of reducing lost merchandise. Zebra places a great deal of importance on product visibility and transparency as well as accuracy in locations. Implementation of RFID into this system can ensure that both the correct product and the correct quantities of product are collected at both points, thereby eliminating errors seen in traditional analog supply networks. Coupled with the potential for self-driving trucks and the ever expanding internet of things in the cloud, product information can be tracked at all stages of shipment and storage, increasing accuracy, efficiency, and accountability. Where warehouses and receiving departments had to endure a certain amount of shrinkage of products in the past, a fully utilized RFID-enabled supply network can determine exactly where product is at all times, ensuring that theft is discovered immediately and enforced.
While the reduction of human interaction in the supply chain and warehouses in general can be eliminated with enough technology, it is uncertain to what degree this technology will be implemented in all aspects of supply chain management. While there are huge benefits to operating in such a system, the major negatives include high initial costs and restructuring costs associated with implementing this network into existing, analog networks. Humanity may not be completely removed from the supply chain in the future, but this technology, as well as more advanced techniques for automation, will increase the efficiency and reduce the costs required to operate these newer supply chains dramatically while significantly reducing errors and inefficiencies.