by Fronetics | Feb 18, 2016 | Blog, Strategy, Supply Chain
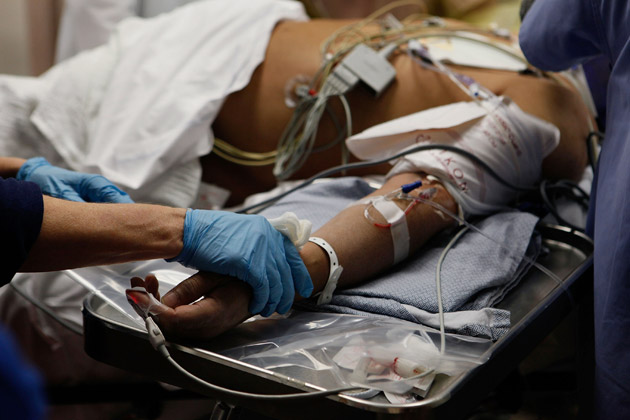
The health care supply chain could cut billions of dollars in cost by adopting practices well established in other industries.
Take the case of a typical Asian laptop manufacturer, for example. As a result of a top-notch supply chain, a European customer can place an order and receive a pallet of freshly assembled computers in just over a week. Ask a pharmaceutical manufacturer for a delivery, on the other hand, and the lead time stretches to 75 days.
The case is further illustrated by the difference in operational metrics between the health care supply chain and the supply chain for fast-moving consumer goods (FMCG). Whether you look at days in inventory, obsolescence, or manufacturing lead time, the FMCG is invariably so efficient that the health care supply chain looks sluggish in comparison.
But such a significant performance gap also means even minor efficiency gains could have a big impact, according to a McKinsey report. An industry that spends in the excess of $340 billion annually on pharmaceuticals and medical devices would benefit from examining every part of its supply chain to not only speed up lead time and boost ROI, but also provide safer and more affordable products to end customers around the world, the consulting firm argues.
The shortcomings so far stem from an inability to tackle challenges that today add substantial cost to the health care supply chain. Big-ticket challenges include:
- Increased regulatory scrutiny
- Expanding product portfolios
- Drug recalls
- Drug shortages
- Counterfeiting
- Supply-chain security breaches
- Medication errors in the developed world
Although transforming a supply chain is an incredibly complex undertaking, McKinsey notes:
“…if the sector adopted straightforward advances well established in other industries, we estimate that total costs (from the supply chain and external areas, such as patient care) could fall by $130 billion.”
Industry research does indeed show every member of the value chain – from pharmaceuticals and medical suppliers to pharmacies and hospitals – that embraces opportunities to optimize the health care supply chain reaps the rewards in increased profitability. In most cases, the impact on profits ranged from 10 to 20 percent.
So which area of the supply chain offers the greatest opportunity for improvement?
Senior supply chain executives in the pharmaceutical and medical device industries overwhelmingly place improved collaboration at the top of the list. To overcome cultural barriers and make transactional relationships more productive, McKinsey suggests the following approach:
“…six essential steps can make the difference between a productive collaboration and a frustrating one: companies must collaborate in areas where they have a solid footing; agree on sophisticated benefit-sharing models; select partners for the potential value of the collaboration, as well as their capabilities and willingness to act as a team; dedicate resources to the collaboration and involve senior leadership in it; jointly manage performance and measure impact; and start out with a long-term perspective.”
Collaboration is still only a small piece in the supply chain puzzle that also includes better market, product, and customer segmentation; greater agility; improved benchmarking and measurements; and the establishment of global standards for data exchange. To put it all together, it is imperative for the health care supply chain to follow the lead of high performing industries.
You may also like: Improving Efficiency in the Healthcare Supply Chain
by Fronetics | Feb 17, 2016 | Blog, Content Marketing, Manufacturing & Distribution, Marketing, Social Media, Supply Chain
The US manufacturing index is at its lowest level since 2009. This is sobering news for the industry and for the economy. Within the industry, it is clear that the road ahead is not flat, straight, or even smooth. For companies to not just survive, but to also succeed, action needs to be taken.
In August 2015 Bruce McDuffee, Principal at Knowledge Marketing for Industry, released the second edition of the Manufacturer’s Growth Manifesto. If you haven’t read this, you need to do so – today. In the Manifesto, McDuffee spells out how manufacturers can achieve growth rates of 10%, 20%, and even 30%.
The key to attaining a double digit growth rate is changing your marketing strategy and adapting to buyers’ new habits. Specifically:
- Stop pitching products and start helping people.
- Start educating your audience utilizing your particular experts and expertise for FREE.
- Stop advertising product features and benefits of a product.
- Start promoting your useful, helpful papers, webinars, seminars, videos, etc. (not product information) to foster meaningful engagement.
- Admit to yourself and your team that your products are perceived as a commodity and it will take more than product revisions, releases and enhancements to gain the attention of your target audience.
McDuffee concedes that for those who have not previously embraced and engaged in this approach to marketing, “You may be thinking, WTF?”
It may seem counterintuitive, but the results are real. Your company will be able to achieve those double digit growth rates and realize these benefits:
- Reciprocity, credibility and trust in the minds of the people in your target audience.
- Top-of-Mind Awareness (T.O.M.A.) in the minds of your prospective customers so they remember your firm first when the day comes around and they need to buy.
- Higher prices, more sales, more market share, and higher growth rates.
Success, however, depends on believing in this approach and incorporating it into your overall business strategy.
Research conducted by the Content Marketing Institute (CMI) found that while 82% of manufacturers use content marketing, only 26% say that their efforts are successful. A lack of buy-in/vision from higher ups is one of the key challenges identified by CMI. Another challenge that was reported was creating and executing a strategy; only 20% of respondents reported that they had a documented strategy. Notable though, is that 58% of the most effective companies reported that they have a documented strategy.
This approach is not relevant only to manufacturing. Companies across industries and verticals should take notice. Cerasis, a top North American third party logistics company offering logistics solutions with a strong focus on LTL freight management, shifted their marketing strategy and realized positive results. Within 25 months Cerasis realized a 14% increase in revenue. This increase was directly attributable to inbound marketing. In addition to this stream of revenue, the company’s sales team was able to generate revenue totaling $20 million during this period – more than double the previous two years combined.
Those numbers are not small potatoes. If you haven’t checked out the Manufacturer’s Growth Manifesto, make the time.
You may also like:
This was originally published on Electronics Purchasing Strategies.
by Fronetics | Feb 4, 2016 | Blog, Leadership, Strategy, Supply Chain
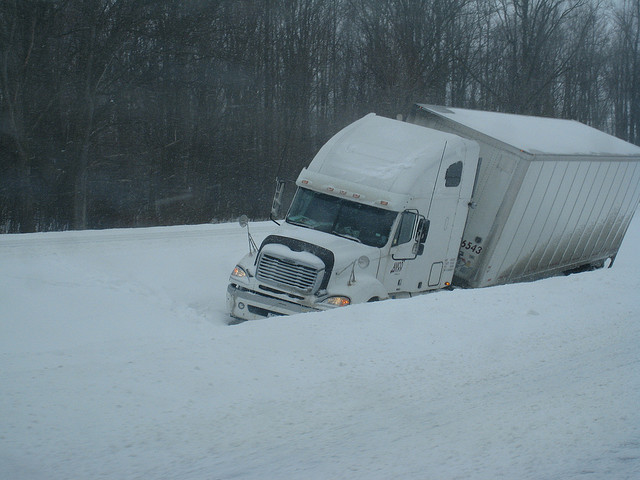
When it comes to leading during difficult times in the supply chain, planning is critical. So is flexibility.
Winter storm Jonas is estimated to have cost $1 billion USD, although some believe the cost could go as high as $3 billion USD, as it paralyzed a large swath of the mid-Atlantic and Northeast. Some 30 inches of snow touched down on several East Coast cities, which cancelled over 12,000 flights and kept people out of work for days.
When difficult times strike, having a plan is critical. For example, with electricity still working, business doesn’t need to come to a close for days on end. Researchers who did a study at Chinese company C-trip encourage people to work from home during storms: “We encourage companies to do a trial the next time an opportunity presents itself — like bad weather, traffic congestion from major construction, or a disruptive event (such as a city hosting the Olympics or the World Cup) — to experiment for a week or two. We think working from home can be a positive experience, both for the company and its employees, as our research with C-trip showed. More firms ought to try it.”
The supply chain can be disrupted in many ways: natural disaster, terrorism, fluctuation in materials. When the problem hits, it’s good to have a plan, but one can’t always be prepared for every scenario. According to the president of global public affairs for UPS, Laura Lane, who had her share of difficult times when she was a young foreign officer in Rwanda during the genocide in 1994, “You have to make decisions that will result in the greatest good — and from that perspective, every decision becomes crystal clear.”
Lane shared her thoughts about how to handle difficult situations in the supply chain with The Wall Street Journal recently.
Look for leaders everywhere
Lane believes that it’s not only C-suite managers who can handle disaster. Being open to ideas and letting specialists rise from the ranks could be a game-changer in critical situations. “Don’t judge people based on their years of experience. Greatness can emerge from anyone on your team — people with decades of experience, or those just starting out.”
Don’t let fear stop you
When you are ultimately responsible for a huge decision involving lots of people and money, fear can infiltrate the mind and body quickly. Remember that you’re in the position you hold for a reason. Don’t let self-doubt or uncertainty about how things will play out delay your decision making. See boundaries and obstacles are new opportunities to find alternatives. Lane says, “Challenge how things are done, and rewrite the rules, if needed,” she says.
Think of the larger vision
Remember what the goals of the company are, and that people have been put in specific roles for reasons. Remember that your situation most likely involves teamwork, and that you can rely on the support, ideas, and voices of others, especially when the vision of the company becomes foggy in the stress of the moment. “Delivering on your promises and grounding your actions in your values is what is needed to be a great leader. You have to believe in the greater good of what you’re doing and then bring others along with you in realizing the bigger vision.”
You may also like:
by Fronetics | Feb 1, 2016 | Blog, Strategy, Supply Chain
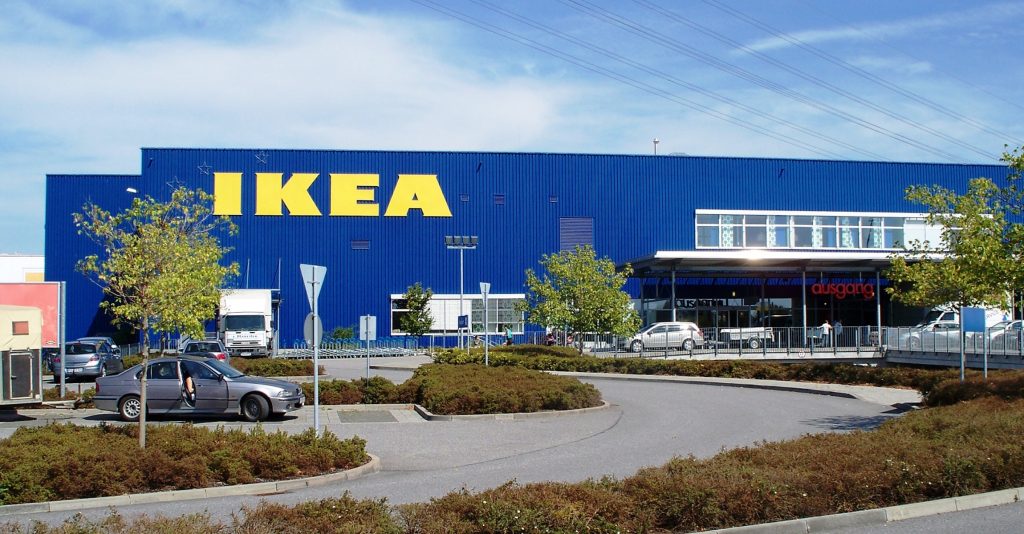
Reverse logistics presents unique challenges and opportunities. To meet these challenges and take advantage of these opportunities, companies need to be both prepared and flexible.
Ikea, a company known for innovation, is facing the enigma of reverse logistics head on. As part of the company’s sustainability strategy, Ikea is challenging the perception that its products are disposable by creating opportunities to recycle and reuse products.
In a recent interview with Fast Company, Chief Sustainability Officer Steve Howard outlined several of the company’s initiatives. They include programs that allow consumers to return plastics, batteries, furniture, compact fluorescent light bulbs, mattress, and textiles to the store. These items are then sold “as-is” or recycled.
These programs have proven successful. For example, in just a few months, over 6 tons of batteries were collected in Moscow, and 25 tons of used textiles were collected in Norwegian stores last year.
Ikea is looking at other ways it can provide end-to-end supply chain solutions. One idea is to take returned products and recycle them into other products. In his interview with Fast Company, Howard shares: “We would basically be taking old bookshelves, old furniture, or an old door that’s finished its first life and sending it into new products. You’ll have a kitchen that used to be a bookshelf, without seeing any visible difference in them. It’s not a revolution, but you have to actually fundamentally change your supply chain to do that.”
Ikea has recognized that old, broken, and unwanted products are an opportunity. Through these innovative reverse logistics initiatives, Ikea is not only acting in a more sustainable manner and reducing the company’s environmental footprint, it is also increasing engagement with consumers and creating positive economic opportunities for the company.
Similar articles:
by Fronetics | Jan 28, 2016 | Blog, Logistics, Supply Chain
Fronetics names the best of the best blogs in the logistics and supply chain industries.
The logistics and supply chain industries are catching on to how successful a blog can be as part of an inbound marketing strategy. Companies are creating content that not only fuels conversation about industry best practices, trends, and issues, but also helps drive business to their websites.
Fronetics Strategic Advisors conducted a survey in January 2016 to determine the top logistics and supply chain blogs in the industry. Here are the results:

Dallas, TX-based Transplace is a 3PL and technology provider serving manufacturers, retailers, and consumer and chemical packaged goods companies. Logistically Speaking is the company’s thought leadership blog. It tells “the latest and the greatest supply chain and transportation stories” through Infographics, interviews with logistics executives, and informative articles offering information and advice.
Readers love: the weekly “TIP list,” or Transportation Industry’s Progression, which curates a short list of articles concerning trending topics and advancements in the industry
Transplace’s CEO Tom Sanderson shares information, opinions, and analysis of factors affecting the supply chain — including company economic data, freight transportation regulation and legislation, and carrier and 3PL financial performance. The blog is rich with charts and graphs that offer big-picture insight on what’s going within the industry.
Readers love: Sanderson’s no-nonsense breakdown of the most pressing issues facing the supply chain
Jennifer Cortez, Director, Marketing Communications, is thrilled with Transplace being recognized by Fronetics and the industry:
“We are thrilled to be recognized as the top logistics and supply chain blogs in 2015. At Transplace, we pride ourselves on providing timely and relevant content to our customers and the industry. Our goal this year is to further connect Transplace and our thought leaders with emerging industry trends.”
Procurious is a UK-based online business network with news, education, discussion forums, and events for procurement and supply chain professionals. The blog goes beyond industry insights — it’s a savvy guide to career advancement and skill development. Articles are written for the modern-day professional, in sync with Procurious’s forward-thinking brand.
Readers love: original series like Life & Style and #firstmovers, which cover interesting, relevant topics in the procurement world.
Thank you to all who took our survey to find the top logistics and supply chain blogs!
Fronetics Strategic Advisors is a management consulting firm with a focus on inbound marketing. We create and execute successful strategies for growth and value creation. Unlike other firms, our approach is data driven. We know ROI is important, so we track and measure results to drive success. Read about our approach to inbound marketing, or get in touch.