by Fronetics | Apr 9, 2015 | Blog, Leadership, Strategy, Supply Chain
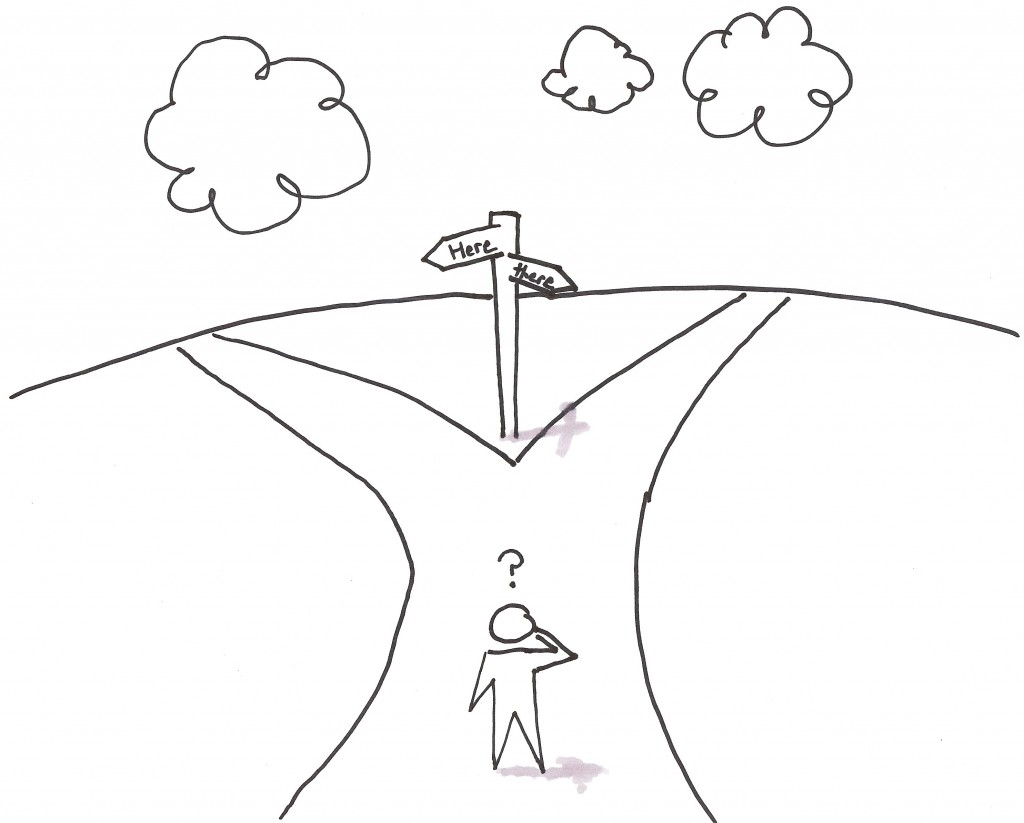
Change management is the process of taking an individual or a group of people from a current state to a more desired state. Its recent prevalence, and often necessity, is heavily due to new technology and globalization. As humans we experience change constantly, on micro and macro levels. Today alone, around 350,000 babies will be born and 150,000 people will die. Gas prices might have dropped recently or your favorite flavor of potato chips might be discontinued. Stock prices rise and fall by the second. Nearly everything changes, yet the word change is often scary or stressful, especially when applied to the workplace.
Alan L. Milliken wrote in his article The Importance of Change Management in the Supply Chain that the key components of a successful business are process, technology, and people. He terms this the “Triad of Operational Excellence.” How is this “triad” involved in change management?
Process:
Sometimes process is the reason for implementing change. Are the processes in the supply chain preventing timely order fulfillment? Can the current process ensure proper, safe, and secure delivery? Are current processes compliant with regulations, nimble enough to weather unexpected change, efficient and modern enough to match innovative competitors? These are all good points to assess. When implementing change is it critical to understand a company’s current capabilities, what needs to be changed, and whether the current systems and finances can support change.
Technology:
Often change management can be spurred by a need for technological growth. If the end-to-end supply chain has antiquated practices, and one member of the chain is transitioning to modern technology, the rest of the players involved may feel the need to change despite being resistant to new technologies or feeling overwhelming by the cost and steps required to transition.
Some companies with decades or a century of business behind them, may be nervous about shifting to a social media driven, on-demand paradigm. There are many benefits to modernizing, and seeing the long-term view of how technology and media can assist business is critical. One company that has made changes to the way they present their business is the packaging supply company, Laddawn. Overhauling their website and providing customers with new purchasing capabilities has put them at the forefront amongst competitors. According to CEO, Ladd Lavallee, “It’s difficult for manufacturers to invest in service, or service technologies, because production can easily consume our time and money. But we need to make our customers’ lives easier if we want to keep winning their business in a shrinking world.”
People:
If leaders aren’t on board with a change management process their frustration or hesitation can seep into others’ mindsets. Studies have shown that emotional contagion occurs in society, and in business. People who cultivate a positive mind-set perform better in the face of challenge. When Bert’s Bee’s was rapidly growing on the global market, then-CEO, John Replogle, worked positive emotional contagion into his workplace, realizing, “Leaders, by virtue of their authority, exert a disproportionate impact on the mood of those they supervise.” He saw this change as an opportunity for people to grow as the company was growing.
In a sweeping meta-analysis of 225 academic studies, Sonja Lyubomirsky, Laura King, and Ed Diener found that happy employees have, on average, 31% higher productivity; their sales are 37% higher; their creativity is three times higher. According to executive coach and business consultant, Sara Regan, of Common Focus Consulting, thoughtful leadership during change is critical to success and employee satisfaction, “The biggest mistake I see leaders make is that they are too late in bringing others into the process. It usually creates more work in the end since it heightens anxiety and resistance then making the leader push harder instead of listen. The way in which leaders approach change impacts the end results but also the ongoing trust and engagement of the team.”
Certainly there are times when change is not necessary in a company, but when it is, aligning the process, technology, and people are key to reaching a new, more successful and desired state.
by Fronetics | Apr 9, 2015 | Blog, Leadership, Strategy, Supply Chain
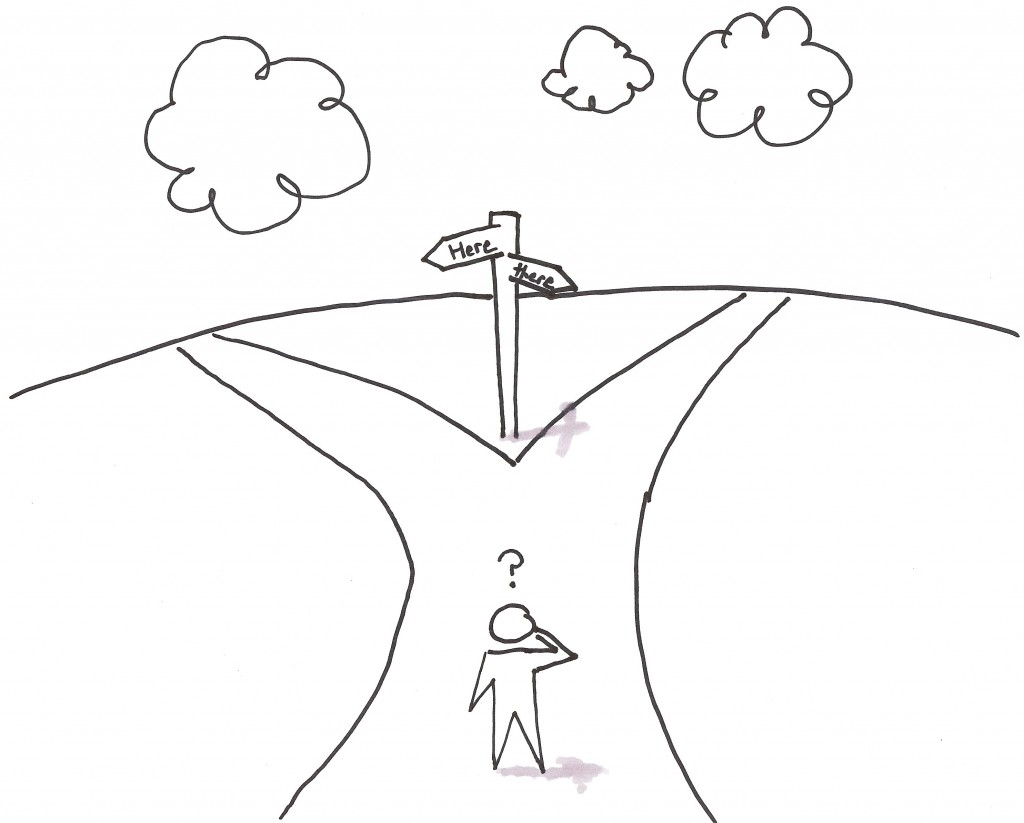
Change management is the process of taking an individual or a group of people from a current state to a more desired state. Its recent prevalence, and often necessity, is heavily due to new technology and globalization. As humans we experience change constantly, on micro and macro levels. Today alone, around 350,000 babies will be born and 150,000 people will die. Gas prices might have dropped recently or your favorite flavor of potato chips might be discontinued. Stock prices rise and fall by the second. Nearly everything changes, yet the word change is often scary or stressful, especially when applied to the workplace.
Alan L. Milliken wrote in his article The Importance of Change Management in the Supply Chain that the key components of a successful business are process, technology, and people. He terms this the “Triad of Operational Excellence.” How is this “triad” involved in change management?
Process:
Sometimes process is the reason for implementing change. Are the processes in the supply chain preventing timely order fulfillment? Can the current process ensure proper, safe, and secure delivery? Are current processes compliant with regulations, nimble enough to weather unexpected change, efficient and modern enough to match innovative competitors? These are all good points to assess. When implementing change is it critical to understand a company’s current capabilities, what needs to be changed, and whether the current systems and finances can support change.
Technology:
Often change management can be spurred by a need for technological growth. If the end-to-end supply chain has antiquated practices, and one member of the chain is transitioning to modern technology, the rest of the players involved may feel the need to change despite being resistant to new technologies or feeling overwhelming by the cost and steps required to transition.
Some companies with decades or a century of business behind them, may be nervous about shifting to a social media driven, on-demand paradigm. There are many benefits to modernizing, and seeing the long-term view of how technology and media can assist business is critical. One company that has made changes to the way they present their business is the packaging supply company, Laddawn. Overhauling their website and providing customers with new purchasing capabilities has put them at the forefront amongst competitors. According to CEO, Ladd Lavallee, “It’s difficult for manufacturers to invest in service, or service technologies, because production can easily consume our time and money. But we need to make our customers’ lives easier if we want to keep winning their business in a shrinking world.”
People:
If leaders aren’t on board with a change management process their frustration or hesitation can seep into others’ mindsets. Studies have shown that emotional contagion occurs in society, and in business. People who cultivate a positive mind-set perform better in the face of challenge. When Bert’s Bee’s was rapidly growing on the global market, then-CEO, John Replogle, worked positive emotional contagion into his workplace, realizing, “Leaders, by virtue of their authority, exert a disproportionate impact on the mood of those they supervise.” He saw this change as an opportunity for people to grow as the company was growing.
In a sweeping meta-analysis of 225 academic studies, Sonja Lyubomirsky, Laura King, and Ed Diener found that happy employees have, on average, 31% higher productivity; their sales are 37% higher; their creativity is three times higher. According to executive coach and business consultant, Sara Regan, of Common Focus Consulting, thoughtful leadership during change is critical to success and employee satisfaction, “The biggest mistake I see leaders make is that they are too late in bringing others into the process. It usually creates more work in the end since it heightens anxiety and resistance then making the leader push harder instead of listen. The way in which leaders approach change impacts the end results but also the ongoing trust and engagement of the team.”
Certainly there are times when change is not necessary in a company, but when it is, aligning the process, technology, and people are key to reaching a new, more successful and desired state.
by Elizabeth Hines | Apr 1, 2015 | Big Data, Blog, Data/Analytics, Logistics, Supply Chain
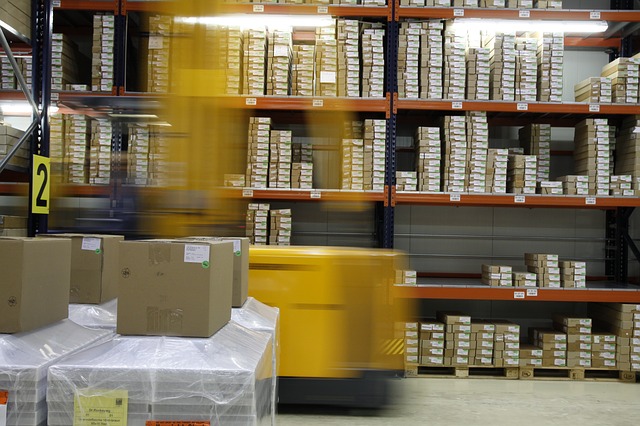
A distribution center struggling with a high number of forklift truck impacts found a way to leverage big data to address a nagging, costly warehouse issue. The company had installed a telematics solution on its forklift trucks, but could not determine the cause of the impacts. The time and location of impacts were known, as well as the identity of the drivers involved, but the company still needed to pull in more data sources for an effective assessment.
Forget for a moment the potential of adopting big data analytics throughout the entire supply chain and consider instead how big data can untangle and integrate seemingly unrelated masses of data to solve small problems in a warehouse or distribution center. That’s exactly what this company did.
By analyzing the link between environmental factors inside the distribution center and the forklift impact records, the culprit was swiftly identified: fast-moving thunderstorms that caused the humidity level to rise so quickly that the dehumidifiers could not keep up, increasing the risk of drivers losing control on the slippery concrete floor. That knowledge helped the company prevent sliding accidents by using a function of the telematics solution to reduce the maximum speed of the trucks when the humidity hit a certain level.
Indeed, distribution centers and warehouses present ideal environments — microcosms — for big data applications. Modern facilities are loaded with sensors and detectors to track every pallet and every piece of material handling equipment in real-time. Managers see the benefits in increased productivity, improved inventory flow, optimized equipment usage, and more. However, for that Eureka moment, organizations should also apply big data analytics across these multiple sources of data to uncover patterns that will drive even more, and perhaps surprising, operational improvements.
Rather than looking at data in isolation, a holistic approach holds significantly more power. Managers typically keep careful track of the performance of lift trucks, batteries, and chargers. But it is not until those entities are reviewed as a single system and matched with data coming off the lift trucks that a new level of revelations can be had.
Look for big data analytics to further raise the IQ of our “smart” warehouses and DCs. Inbound Logistics sums it up this way: “Accessing the right information to make smart decisions in the warehouse is one main reason why the demand for big data has grown so much — and so rapidly — in the distribution sector.”
Do you think distribution center and warehouse managers do enough to leverage big data?
by Elizabeth Hines | Apr 1, 2015 | Big Data, Blog, Data/Analytics, Logistics, Supply Chain
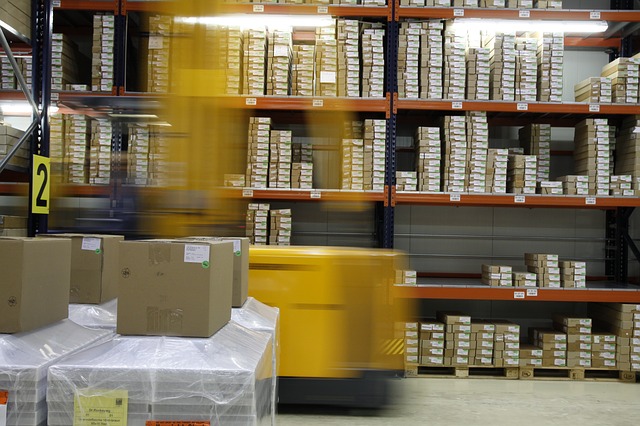
A distribution center struggling with a high number of forklift truck impacts found a way to leverage big data to address a nagging, costly warehouse issue. The company had installed a telematics solution on its forklift trucks, but could not determine the cause of the impacts. The time and location of impacts were known, as well as the identity of the drivers involved, but the company still needed to pull in more data sources for an effective assessment.
Forget for a moment the potential of adopting big data analytics throughout the entire supply chain and consider instead how big data can untangle and integrate seemingly unrelated masses of data to solve small problems in a warehouse or distribution center. That’s exactly what this company did.
By analyzing the link between environmental factors inside the distribution center and the forklift impact records, the culprit was swiftly identified: fast-moving thunderstorms that caused the humidity level to rise so quickly that the dehumidifiers could not keep up, increasing the risk of drivers losing control on the slippery concrete floor. That knowledge helped the company prevent sliding accidents by using a function of the telematics solution to reduce the maximum speed of the trucks when the humidity hit a certain level.
Indeed, distribution centers and warehouses present ideal environments — microcosms — for big data applications. Modern facilities are loaded with sensors and detectors to track every pallet and every piece of material handling equipment in real-time. Managers see the benefits in increased productivity, improved inventory flow, optimized equipment usage, and more. However, for that Eureka moment, organizations should also apply big data analytics across these multiple sources of data to uncover patterns that will drive even more, and perhaps surprising, operational improvements.
Rather than looking at data in isolation, a holistic approach holds significantly more power. Managers typically keep careful track of the performance of lift trucks, batteries, and chargers. But it is not until those entities are reviewed as a single system and matched with data coming off the lift trucks that a new level of revelations can be had.
Look for big data analytics to further raise the IQ of our “smart” warehouses and DCs. Inbound Logistics sums it up this way: “Accessing the right information to make smart decisions in the warehouse is one main reason why the demand for big data has grown so much — and so rapidly — in the distribution sector.”
Do you think distribution center and warehouse managers do enough to leverage big data?
by Fronetics | Mar 23, 2015 | Blog, Supply Chain, Talent
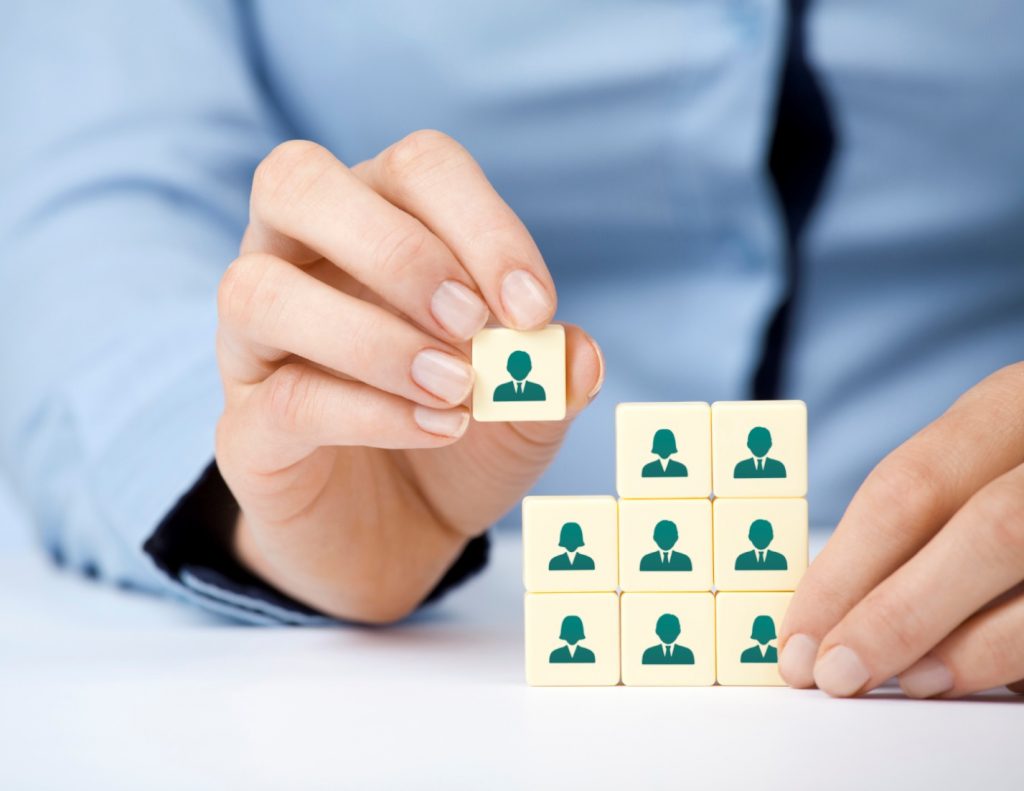
What you need to know about the supply chain talent gap.
The supply chain talent gap has been called a “perfect storm.” Few topics are shrouded in such doom and gloom. Every report cites doomsday statistics of the impending crisis when, by 2025, 60 million baby boomers will exit the workforce, leaving a gigantic gap when 40 million millennials take their place. To make matters worse, the retirement exodus is only one factor contributing to the sinking ship. Future supply chain professionals need to master not only the hard analytical skills but also the soft leadership skills fueled by the transition from an industrial economy to an economy grounded in service and information. In numbers, it means only 20% of the workforce will possess the skills required of 60% of all new supply chain jobs.
But listen up, all you forward-thinking millennials and midlevel supply chain managers with cross-functional expertise. There’s some good news: The market can’t get enough of you.
Yes, amid all the dire facts, there is opportunity. There has never been a better time to be, so to speak, on the other side of the table — a college graduate or a motivated professional looking for a career with upward mobility? What other field of work can offer as much promise to new recruits and current employees as the supply chain industry?
Just as all reports predict a brewing crisis, they also tout talent management as the primary remedy. For a self-motivated individual, fresh out of college or in the midst of a corporate climb, this focus on professional development presents a smorgasbord of options. Many companies have taken note and adopted a strategy of action for recruiting and retaining new talent. A growing number of university program offerings reflect a strengthening partnership between academia and the supply chain industry. Many supply chain companies are building partnerships with academic programs to offer internship opportunities; a move that’s creating strong early relationships with students and will likely have a positive effect on future recruitment efforts. A company that can offer its current staff competitive salaries in addition to cross-functional training is much better positioned to meet the challenges of the talent shortage and the evolving nature and demands of the supply chain.
Another way companies within the logistics and supply chain industries are attracting top talent is through their use of social media. Considering the global reach and vast talent pool of LinkedIn’s 300 million users, the business-focused social network is helping companies with open positions that might require a unique and specific skill set to connect with candidates across the globe.
What’s clear is that companies that follow a plan of inaction will be left behind. This new talent pool will swiftly turn down a company that remains stuck on strict functional divisions and favors the old siloed approach to doing business. Many supply chain managers have grown up in such divided organizations themselves, so they have been slow to take appropriate action to retain and train talent, according to a Supply Chain Insights survey, leaving those better prepared with a competitive advantage.
If a company does not appeal to the desires of top candidates, individuals will take their talent elsewhere. And there will always be another company to welcome them. As Rebooting Work author Maynard Webb points out in a 2013 interview with Elance, in order for companies to remain competitive they’ll need to adapt to the modern workforce. “Companies have traditionally thought of people as a disposable resource,” he says. “They have valued their buildings much more than employees… this doesn’t make sense in a world where the best people can choose to work wherever they want. Businesses have to realize that some jobs can be done from anywhere, anytime, and save the brick and mortar buildings for the few jobs that demand a physical presence.”
Touting the unlimited opportunities and unparalleled growth in the supply chain field should be part of turning the tide. Sure, there is a lot of talk about doom, but mainly for those companies that fail to attract and retain top talent.