by Fronetics | Jun 13, 2018 | Blog, Content Marketing, Current Events, Logistics, Marketing, Supply Chain
Most agree the supply chain is integral to our economy. But what, exactly, comprises the U.S. supply chain economy?
Ask a random sampling of 10 people on the street whether or not the supply chain is an integral part of the U.S. economy, and, more than likely, you’ll get at least 8 affirmative responses. But ask that same random sampling to talk in detail about the supply chain economy, the jobs it contains, and how it pertains to innovation, and you’ll most likely hear crickets.
While most Americans recognize the value of the supply chain, the details remain fuzzy. In a recent Harvard Business Review article, economists Mercedes Delgado and Karen Mills attempt to clear things up. They identify the industries that comprise the supply chain economy, quantify the number and quality of jobs it contains, and assess how much it matters for innovation. Here’s a summary of their findings.
What is the supply chain today?
First off, Delgado and Mills define the nature and scope of the supply chain industry, making the key distinction that supply chain industries are B2B, meaning that they sell to businesses and the government, rather than B2C, or business-to-consumer.
Industries that comprise the supply chain include traditional suppliers, like “metal stampers or plastic injection molders — businesses that manufacture parts to be used in a final good.” The authors, however, point out that thinking of the supply chain purely as a manufacturing sector is a flawed model.
In fact, “only 10% of employment in the [U.S. supply chain] economy is in manufacturing, and 90% is in services.” Jobs in this 90% include “many different labor occupations, from operation managers, to computer programmers, to truck drivers.”
Delgado and Mills take their analysis a step further, identifying the subcategory of “supply chain traded services – i.e., those that are sold across regions like engineering, design, software publishing, cloud computing, and logistics services.”
It’s worth noting that supply chain traded services have the highest wages in the supply chain economy, averaging at $80,800 annually — 3 times higher than traditional “service” jobs.
[bctt tweet=”The U.S. supply chain accounts for 37% of domestic jobs, employing some 44 million people at “significantly higher than average wages.”” username=”Fronetics”]
The U.S. supply chain accounts for 37% of domestic jobs, employing some 44 million people at “significantly higher than average wages.” The supply chain also accounts for a high proportion of the innovative activity in the economy as a whole, with STEM jobs, “a proxy for innovation potential,” at “almost five times higher in the supply chain economy than in the B2C economy.”
The authors point out that the prevalence of higher-paying jobs and innovation is a result of the fact that “supply chain industries have downstream linkages to multiple industries, which allows the innovations they create to cascade and diffuse across the economy, potentially increasing the value of those innovations.”
Policy recommendations
After defining and discussing the modern U.S. supply chain economy, Delgado and Mills move toward policy implications.
“Our supply chain economy framework leads to a more optimistic view of the economy,” they write. “If we were to focus on supporting supply chain services, particularly those in traded industries, the result might be more innovation and more well-paying jobs in the United States.”
They make three key recommendations for national economic policy, focused on improving suppliers’ access to skilled labor, buyers, and capital:
- Invest in skilled labor.
- Support regional industry clusters.
- Ensure that suppliers have access to capital.
The bottom line: the supply chain industry is robust and dynamic, with “a crucial role in driving innovation and creating well-paying jobs.”
The idea of “bringing manufacturing back” is stale and reactionary. Delgado and Mills instead suggest that “we must shift our policy solutions to focus on cultivating the supply chain service jobs that will drive America’s economy forward.”
Related posts:
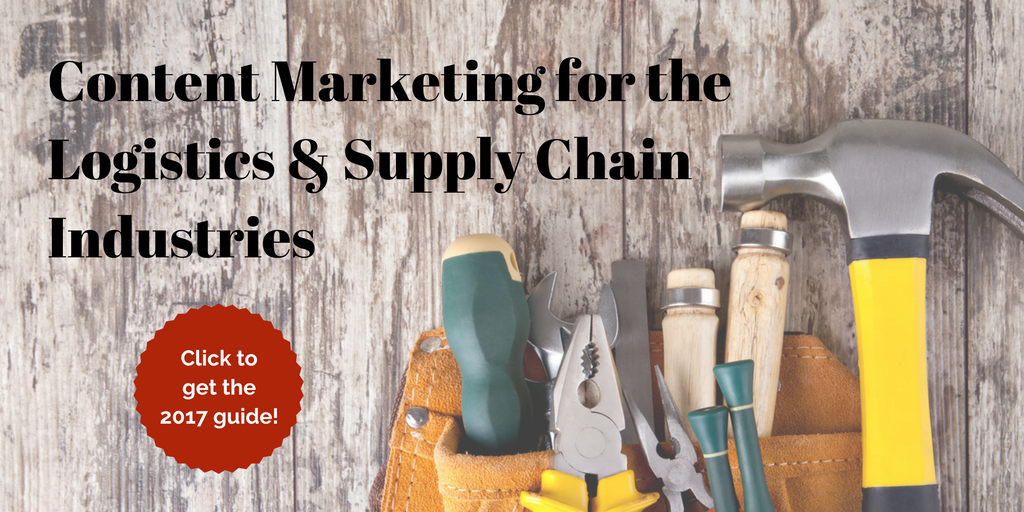
by Jennifer Hart Yim | Jan 30, 2018 | Blog, Current Events, Logistics, Supply Chain
Looking at Tesla’s suppy chain issues, here are the biggest takeaways so you don’t have to repeat their mistakes.
This guest post comes to us from Argentus Supply Chain Recruiting, a boutique recruitment firm specializing in Supply Chain Management and Procurement.
Back in 2016, we posted about Tesla’s ambitious plan to ramp up production of its consumer-grade Model 3 electric car to 500,000 vehicles a year by 2020. At the time, pretty much every analyst agreed that was an ambitious target for a manufacturer without solid experience mass-producing vehicles at that scale. In the two years since, Tesla’s CEO Elon Musk has issued a number of other bold predictions. He’s championed a whole host of emerging technologies. He’s made the world feel like the future could resemble a sci-fi novel – were he to deliver on the herculean tasks of sending humans to mars, shifting the world to solar power production, and figuring out how to directly connect computers to human brains.
But in the meantime, there’s also been the pesky matter of the more mundane – but seemingly no less difficult – task of delivering on the very high demand in the marketplace for Tesla Model 3s. In 2016, the company faced scrutiny for allegedly hiring 140 workers from Eastern Europe for $5 an hour. Then, in 2017, various press outlets reported on a number of issueswith the Model 3’s Supply Chain, specifically issues related to the vehicle’s battery design, as well as issues with manufacturing automation. The result?
Only 220 Model 3s were delivered as of October 2017. We’re sure the company has delivered more cars since then, but that’s a brutal statistic almost two years after over 400,000 consumers paid $1000 each to preorder the car. Investors are growing restive, with the company’s share price down 6.8%, and the company reporting a $671.1 million loss for the 3rd quarter of 2017. Musk has compared the Model 3’s current production state to the “8th circle of hell,” and acknowledged that Tesla won’t hit the goal of 5,000 units produced a month until “sometime in March 2017.”
A great article last month from CIPS’ industry magazine Supply Management dove into some of Tesla’s Supply Chain woes, discussing how the company, still considered a visionary in the industry, has got to this place, as well as some optimistic scenarios for how it can get out of it. Written by Paul Simpson, it’s an interesting account of how Supply Chain issues can stymie a company, even if that company and product have huge positive brand association. Similarly to what we did with analysis of Target’s Canadian misadventure, we wanted to see what lessons we can draw from Tesla’s Supply Chain issues that might be useful in industries other than automotive manufacturing.
Here are our biggest takeaways for what can be learned from Tesla’s Supply Chain woes:
- If you’re not confident that your production and Supply Chain are up to snuff, don’t overpromise to the consumer. Elon Musk has made a cottage industry out of bold pronouncements about the future, and he’s delivered on some of them before. It’s why he’s gained a reputation as a visionary. Musk had to know that promising to quickly scale up production to 500,000 cars a year was an unrealistic goal. He’s also someone who believes in setting big goals as a way of achieving the impossible. But even with that in mind, it’s possible he also underestimated the inevitable difficulties in mass-producing a product with 10,000 individual parts, and that’s led to way too many 2 a.m. nights tinkering with robotics on factory floors.For his part, Musk acknowledged that he’s now trying not to make pronouncements about production timelines.
- Take ownership for Supply Chain failures rather than blaming suppliers. Even if suppliers are failing to deliver, consumers (and, relevant to Tesla, shareholders) will almost always blame the company itself rather than those suppliers – and rightly so. They’re the ones who selected those suppliers, after all. In Tesla’s case, Musk took personal ownership over the decision to select the system integration subcontractor that’s behind the latest delays – instead of blaming his Supply Chain staff. Depending on your perspective, you can either look at this as a visionary CEO being transparent about Supply Chain difficulties, or a manufacturer throwing a supplier under the bus.
- Great companies need a Supply Chain guru. Simpson quotes an argument by American journalist Travis Hoium, who said that “Elon Musk Needs his Own Tim Cook to Take Over Operations.” Drawing a parallel to Steve Jobs, Hoium argues that Musk needs an operations genius who can match his vision for the future and product development excellence with Supply Chain execution. Sometimes business leaders – especially those with the vision of someone like Elon Musk – overrate their own ability to understand the intricacies of managing complex Supply Chains, to their detriment. Tesla’s issues underscore the importance of having the right talent in place to avoid the murky waters of Supply Chain failure – and figure out how to right the ship if things go awry.
Despite these numerous issues, it looks like – for now – Tesla is facing more heat from shareholders than consumers. Anticipation for the Model 3 is still high, showing that a strong product and brand can trump some Supply Chain issues. But these issues are starting to have a real impact on Tesla’s share price and bottom line, and the pressure is on. Let’s see how this story develops as 2018 proceeds.
Related posts:
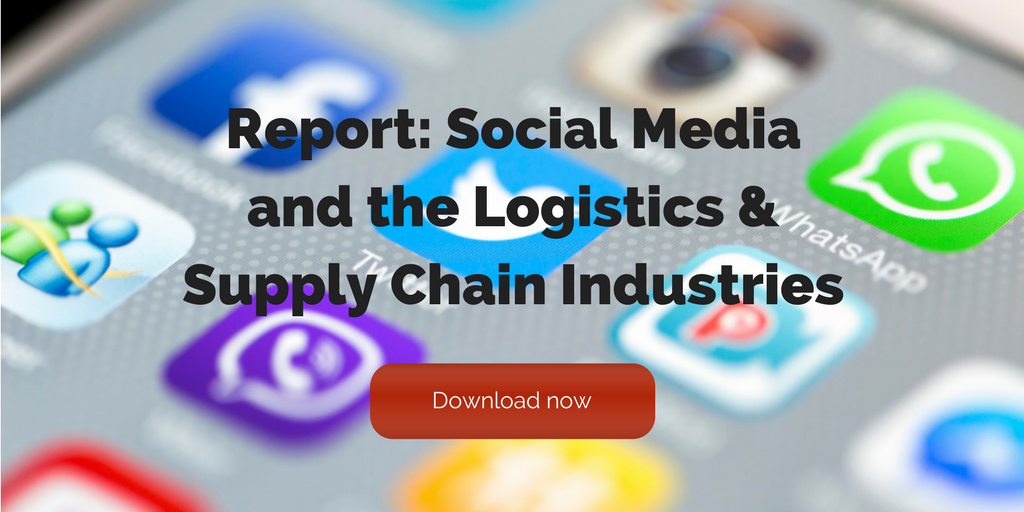