by Fronetics | May 2, 2019 | Blog, Content Marketing, Logistics, Manufacturing & Distribution, Marketing, Strategy, Supply Chain
As automation technologies become increasingly sophisticated, companies throughout the supply chain are realizing the beneficial impact of automation on materials handling.
Highlights:
- Manufacturers of automation technologies are predicted to grow significantly over the next 5 years.
- Automating the “first mile” of the supply chain helps reduce labor challenges and leads to increased productivity.
- Robotics technologies offer greater capacity for data collection, facilitating informed process decisions.
While the impact of automation on the “last mile” of the supply chain is often the subject of public interest, automation in the “first mile” deserves just as much attention. Advanced robotics are increasingly ensuring accuracy — while minimizing or even eliminating human involvement in various processes — at every stage of the supply chain. Industry experts are predicting an ever-growing impact of automation on materials handling, with companies reaping the benefits up and down the supply chain.
Particularly in the materials-handling sector, human capital is increasingly difficult to recruit and maintain. Additionally, labor costs in global markets such as India and China are rising. Naturally, companies are increasingly inclined to replace or redeploy human labor, with the help of automated material-handling systems.
Not to mention, the increasing sophistication of machine-learning capabilities or AI within available automation technologies allows for even greater productivity. And there’s strong reason to believe that we’re only seeing the beginning of what automation can do. Vendors who create these technologies are investing heavily in R&D, aggressively attempting to expand their product offerings to meet specific industry demands while complying with the complex standards and regulations in place.
Quantifying the costs and impact of automation on materials handling
The robust growth in the robotics-equipment-manufacturing sector demonstrates that the materials-handling industry is investing in automation. Thanks to the demand for high-performance robotics systems, New Equipment Digest (NED) predicts that within the materials-handling-equipment sector, the robotics segment will grow by over 8%, reaching $20 billion by the year 2024. The overall material-handling-equipment market is expected to surpass $190 billion by the same year, according to a growth forecast report by Global Market Insights, Inc.
“Growing automation capabilities in the manufacturing space coupled with increasing penetration of advanced technologies, such as IoT, RFID, and AI, are expected to drive the material-handling-equipment market growth,” predicts the NED. These technologies are already increasing productivity and throughput in the materials-handling sector and reducing the potential for human error. The predicted growth in the manufacturing of robotics equipment points to the increasingly positive impact of automation supply chain-wide.
Of course, automation is not without its challenges. Companies face technical issues involved in implementation, not to mention the large capital outlay required to invest in costly equipment and technologies. With increased technical sophistication and network utilization, there are threats to cybersecurity, requiring companies to invest in measures to protect their technology.
Robotics-equipment manufacturers recognize that while automation offers significant benefits for materials handling, companies need to study potential impact before making these costly investments.
Many manufacturers are offering tools for quantifying the impact of automation on materials handling. OTTO Motors, a manufacturer of self-driving-vehicles, offers an ROI calculator, allowing potential buyers the opportunity to receive an easy ROI estimate. Manufacturers are also increasingly offering simulations of materials-handling systems, allowing potential customers to determine efficacy, test designs, and study new procedures without disrupting operations.
Realizing the benefits of automation for materials handling
Beyond the well-known benefits, such as decreased costs and increased productivity, automating materials-handling processes can offer a variety of additional advantages to companies’ first-mile operations. In fact, streamlining these processes and reducing costs has its own positive repercussions throughout a company’s operations, as it allows for increased speed, productivity, and accuracy operation-wide.
[bctt tweet=”Automating materials-handling processes has its own positive repercussions throughout a company’s operations, as it allows for increased speed, productivity, and accuracy operation-wide.” username=”Fronetics”]
Additional benefits of automating materials handling include:
- The access to real-time data provided by automated technologies allows for more complete Key Performance Indicators (KPIs).
- Labor shortages and high turnover are some of the primary challenges in materials handling – automation shields manufacturers from these challenges, while allowing human labor to be repurposed into more intricate tasks.
- Implementing technology in the materials-handling phase of the supply chain can connect to other automated processes within the factory.
- The availability of data and the ability to leverage it allows adjustments to be made in real time, meaning more flexible manufacturing.
The bottom line is that, while it can be costly at the outset, automation at the front end of the supply chain, namely materials handling, offers rich and diverse benefits sector-wide.
Related posts:
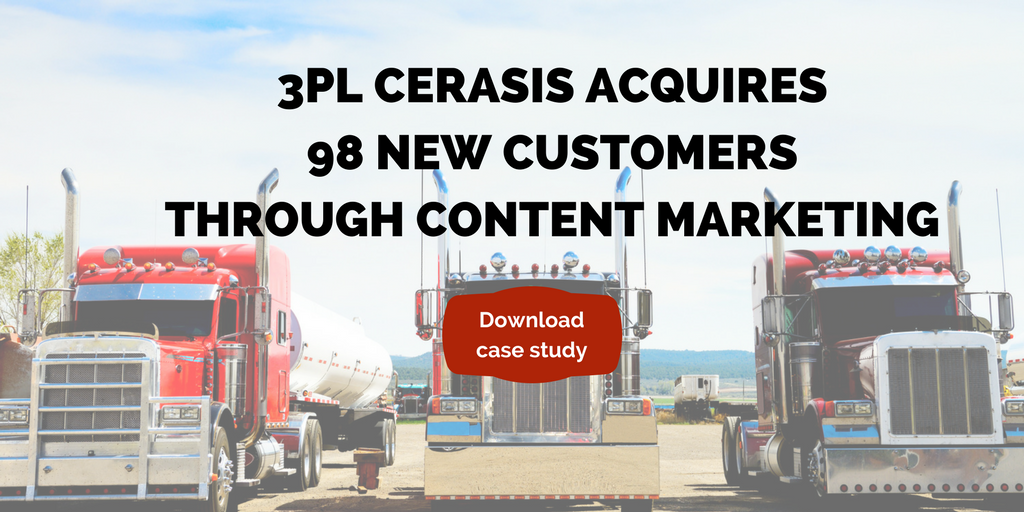
by Fronetics | Apr 18, 2019 | Blog, Current Events, Manufacturing & Distribution, Robotics & Automation, Supply Chain
A McKinsey & Company report studied the impact of automation in manufacturing driven by rapid advances in robotics, AI, and machine learning.
Highlights:
- New robotics technologies are cheaper, faster, and smarter than before.
- 87% of hours workers spend in production could be automated with existing technologies.
- Learn what four factors to consider when making decisions about automation.
Since the industrial revolution, automation has been a major disruptor in manufacturing. Once again, a new generation of robotics and related technologies is reshaping the face of the manufacturing and distribution industries. In fact, American manufacturing has made a recent comeback, thanks in large part to the widespread use of automation and robotics.
Automation technologies that were once cost-prohibitive are now more achievable — and the return on investment is greater than ever before. The new generation of robots are not only far less expensive than their ancestors, but they are also more versatile, flexible, and able to learn new tasks, even those that were far too difficult for machines just a few short years ago.
[bctt tweet=”The new generation of robots are not only far less expensive than their ancestors, but they are also more versatile, flexible, and able to learn new tasks, even those that were far too difficult for machines just a few short years ago.” username=”Fronetics”]
Robots are now capable of, for example, “picking and packing irregularly spaced objects, and resolving wiring conflicts in large-scale projects in, for example, the aerospace industry,” according to a recent report from McKinsey & Company. Not only that, artificial intelligence is leveling the playing field between human and machine, and “increasing the potential for automating work activities in many industries. In one recent test, for example, computers were able to read lips far more accurately than professionals.”
Quantifying the impact of automation on manufacturing
McKinsey’s study, which covered 46 countries and about 80% of the global workforce, determined that a tremendous amount of working hours could be eliminated or repurposed by automation with technology that is already here.
The study found that “87% of the hours spent on activities performed by workers in production occupations are automatable — the most of any manufacturing occupation.”
And it doesn’t stop there. “Even among other occupations in manufacturing (for example, engineering, maintenance, materials movement, management, and administration), however, there is still significant opportunity, with approximately 45 percent of these working hours automatable as well.”
The cost and logistics of automating
In general, the study found that automation allowed wages to increase globally and profits to grow. The authors emphasize the fact that in order to capture long-term value from automation, manufacturers’ best bet is to implement technologies in phases, capturing value at each phase, allowing for future investment.
Many complex factors come into play when it comes to meeting the challenges associated with automation, deciding what to automate, and when to implement technologies to best capture long-term value. Cost is just one element, albeit an important one.
McKinsey suggests considering the following four factors when making decisions about what to automate:
- Technical feasibility
- Cost associated with developing and deploying necessary hardware and software
- Cost of labor and resultant “supply-and-demand dynamics”
- Benefits beyond labor substitution, such as increased output and quality, and fewer errors
An American manufacturing renaissance
The Association for Advancing Automation has predicted that “American manufacturing’s embrace of robotics will ensure a new manufacturing renaissance in this country.” Already, we’re seeing a steady trickle of companies reversing outsourcing trends, as it’s becoming profitable again for manufacturing to take place in the United States, rather than relying on cheap labor abroad.
As more operations embrace automation — and as we continue to witness rapid advances in robotics, AI, and machine learning — American manufacturers won’t be the only ones to reap the benefits. Many experts are predicting that automation in manufacturing will create new, better paying jobs.
Optimists include our own CEO Frank Cavallaro, who recently wrote: “From what I see now … I still feel optimistic that AI and automation will create leaner, more efficient operations that will, in turn, create new (even if different) jobs. To me, it still looks like the ones winning from the increasing technological advances in the manufacturing industry are, in fact, we humans.”
Related posts:
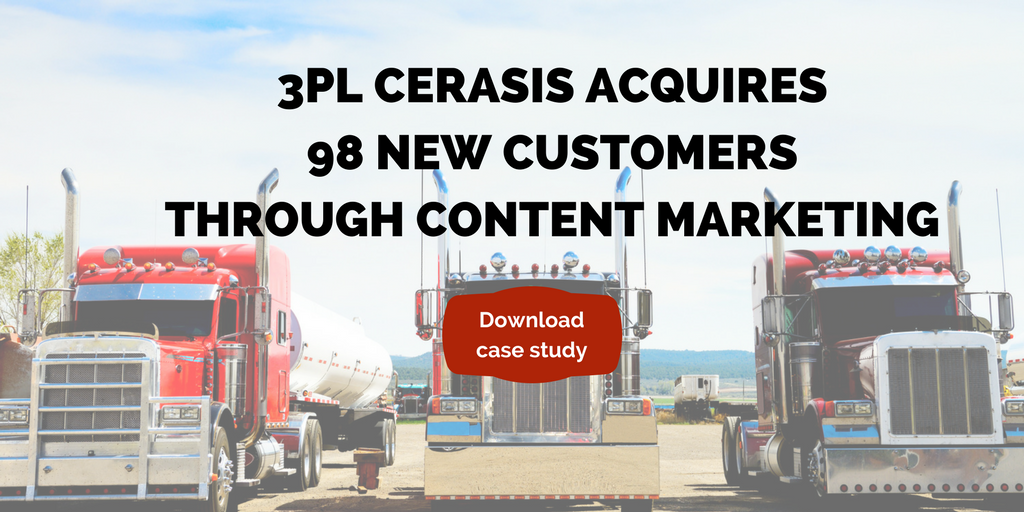
by Jennifer Hart Yim | May 11, 2017 | Blog, Current Events, Logistics, Manufacturing & Distribution, Supply Chain, Transportation & Trucking, Warehousing & Materials Handling
This post comes to us from Adam Robinson of Cerasis, a top freight logistics company and truckload freight broker.
Imagine a world where automation comes together with technology to deliver products without human intervention. An order is placed by a consumer. 3-D printers pick up the details and print the finished product. It’s then picked by robots from the shelves, packaged and placed into a self-driving truck. The trucks leave the facility, and drones are automatically dispatched from the truck to deliver products while moving. The truck never stops until arriving for reloading.
This example generates a huge amount of data that can leverage in the supply chain. But, the same data can have a drastic impact on transportation planners and agencies around the globe. While this example may still be a few years off, it is important that you understand how the top emerging trends in automation will shape supply chains and transportation processes in the coming years.
The Standard Definition & Components of Automation
Today: There is a standard definition of automation in the supply chain. Anything that can be handled via today’s computer systems can be automated. This includes billing, generation of bills of lading, compliance reports, and even movements throughout a factory or warehouse floor.
Historically, automation has been applied to virtual processes, like order auditing or customer service reports. However, the trends in automation are changing to reflect actions that function more like artificial intelligence, not just a search and locate program on the computer.
Additive Manufacturing
What is it?
Additive manufacturing includes all actions in the supply chain that can enhance existing factory production, if not replace it entirely. Additive manufacturing may be handled manually, but automating this process is as simple as turning on the power and connecting to the Internet of Things (IoT).
For example, additive manufacturing might involve the use of 3-D printers to create replacement parts at the store for consumers.
Today’s status: Unfortunately, the capacity of 3-D printers remains in infancy, capable of only producing simplified parts out of liquid polymers.
Virtual Reality Comes to the Forefront.
Meanwhile, Google Glass and other virtual reality tech are changing how customers complete their orders. In addition, the same technology can be overlaid with augmented reality to give repair technicians and individuals greater resource access when making repairs, checking order contents and fulfilling orders.
For example, augmented reality glasses will soon detect package dimensions and classify the package according to dimensional pricing models.
Today’s Status: Today, this technology is limited to automated identification and data capture (AIDC) applications. Advancements in virtual reality over the past year indicate its future might be much closer than “meets the eye.”
Additive manufacturing will gradually move products from warehouses and distribution centers to be closer to end-users. As a result, the amount of last-mile traffic may increase.
Robotics Enhance Inbound and Outbound Logistics for Shippers.
Another trend in automation involves robotics. By definition, robotics are the icons of automation. They perform functions at the request of a system or person, but more of today’s robotic systems are performing duties upon request from an order fulfillment system.
The order process automatically notifies robots in warehouses and triggers the flow of processes as seen in the opening example.
Robotics Improve Inbound and Outbound Logistics.
Robotics are not isolated to warehouse pulling for outbound logistics. They can be used to manage inbound and outbound processes and strategy. Through trends in automation and robotics, supply chain companies will have the tools and resources necessary to ramp up throughput and decrease product cycle from order to delivery. Therefore, more trucks and drivers will be needed, but the looming driver shortage and capacity crunch will trigger another automation trend.
Autonomous Vehicles/ Trucks
Automation begets automation. With advances in technology and the IoT, most major companies, including Uber, Facebook, Google, and Amazon, have launched autonomous vehicle and truck pilot programs.
These driverless vehicle programs will give supply chains access to a new inexhaustible resource for moving products, overcoming the challenges inherent in the driver shortage and capacity crunch.
The driver shortage and capacity crunch are likely to come to a head in 2017, as consumers demand more product, at lower costs and faster than ever before.
Some setbacks have occurred, like the first self-driving car wreck earlier this year. With each setback and challenge, companies have pushed back to overcome the obstacles.
In response to increased interest in driverless vehicles and trucks, the National Transportation Safety Board (NTSB) has issued recommendations and created an advisory panel to review ongoing driverless vehicle advancements and maintain public safety.
Transporters and supply chains will respond to this direction by leveraging the trends in automation and power of data to ensure compliance with increased government oversight, through the agencies you represent.
Companies have already tested cross-country driverless trucks, albeit with a person ready in the cab to take over in the event of a system failure. However, the wide-scale deployment of this level of driverless trucks is far from implementation.
In the interim, more automated vehicle systems will work in tandem with drivers to enhance safety and maintain vehicle control. Similar systems are already deployed in crash and pedestrian detection systems, automated braking and tracking control in today’s vehicles. It is not difficult to apply today’s technology and automated features to the fleets and drivers of 2017.
Trends in Automation: Whats the Potential?
The potential applications of this type of technology can include real-time traffic condition monitoring and warnings, redirecting traffic before pile-ups and accidents occur, similar to Google Maps’ capacity to show traffic congestion in real-time.
Data through such systems can automatically feed back into transportation planners’ systems to automatically change signal phase and timing and enable immediate rerouting or adjustment of traffic flow on a broader scale.
Related posts:
by Jennifer Hart Yim | Feb 13, 2017 | Blog, Logistics, Strategy, Supply Chain
Supply chains must accept that they cannot equal the power of Amazon’s supply chain without embracing these new trends.
This guest post comes to us from Adam Robinson, marketing manager at Cerasis, a top freight logistics company and truckload freight broker.
Amazon’s supply chain continued push deeper into new and existing markets will define additional trends in the supply chain throughout the coming year. While supply chain entities struggle to stay competitive with the e-commerce giant, more organizations will look for ways to eliminate inefficiencies and boost operations. Fortunately, these five trends may alleviate some of the strains of competition by giving supply chain partners an advantage in the global market.
Top 5 Trends to Know to Compete with Amazon’s Supply Chain
1. Robotics Will Grow More Versatile.
Amazon’s purchase of Kiva Robots changed the landscape of robotics in the supply chain. However, new companies are being created and developed to fill the void. The robotics company Starship released a robot that delivers meals and groceries to people in Euro metro markets. Meanwhile, Lowe’s has created the LoweBot, which boosts customer service, explains Dan Gilmore of Supply Chain Digest.
More companies are turning to robotics to find new ways to bridge the divide between a dwindling number of customer service representatives, including store associates, and maintaining around-the-clock operations. Across the spectrum, robotics will become more versatile and accessible. In other words, robots will gain new movements, capable of picking items from shelves in warehouses and storefronts.
Per IDC Manufacturing Insights, the use of robotics will become more platform based through robot-as-a-service, reducing costs of deployment and maintenance. Furthermore, the speed of operation of robots will increase more than 30 percent by the end of 2017. Clearly, robotics will become more important in 2017 than during any previous year.
2. Technology Will Reshape Procurement Practices.
Better procurement practices translate into better overall sales, but the role of procurement in driving sales’ statistics will change throughout 2017. Today, procurement drives up to 67 percent of sales, explains Johnathan Webb of Forbes magazine, as procurement professionals look for innovative ways to produce effective, superior products.
For example, Johnson & Johnson procurement professionals actively review market trends before making purchases. Upon identifying these trends, a correct forecast of supply demands can be generated. Thus, the role of procurement has become more focused on being physically involved in market news and research, not just signing purchase orders in an office.
3. More Businesses Will Create E-Commerce Platforms.
Amazon’s supply chain empowered the e-commerce market by giving everyone an opportunity to sell their goods online, which has made competing with Amazon difficult at best. Amazon’s supply chain expansion culminated in more companies looking to enter e-commerce without giving shares to Amazon. Companies expanded e-commerce and omnichannel solutions simultaneously as well, reports Steve Banker of Logistics Viewpoints.
For example, Walmart and Kmart redesigned their mobile e-commerce interface for consumers, making shopping and purchasing online easier and integrated with major companies. A simple search for a product on Walmart.com reveals partnered listings with Wayfair and third-party sellers, much like Amazon’s current vendor options. Moreover, customers can make purchases online and have them shipped to the store or their home. At Walmart, customers can even pick up orders without ever getting out of the car now. Ultimately, more businesses will seek out partnerships with bigger companies to stay competitive with Amazon’s bare price points and ease of use.
4. User Preferences Will Enhance Mobile Management Systems.
Traditional warehouse management systems (WMS) lacked integration with other systems. Procurement strategy was not always evident. Accessibility of systems depended on in-house IT departments, and upgrading access terminals could cause extreme delays and problems in operations. However, newer management systems, such as a comprehensive transportation management system (TMS) that integrates warehouse management with transportation management, are starting to offer more accessibility and personalization options.
In other words, accessibility and personalization allow warehouse managers and staff members to define metrics relevant to new products and current operations, test new processes, and effectively manage the flow of goods. Similarly, new mobile options, ranging from Android tablets to compact barcode scanners, will reduce inconsistencies and errors across the supply chain, explains IRMS 360. Paired with the advancements of predictive analytics and the Industrial Internet of Things (IIoT), more data will result in more efficient processes, creating a positive feedback loop throughout an organization.
5. Contingency Planning Will Become a Standard Practice.
Amazon’s supply chain has proven that not planning will result in the failure of small and medium-sized businesses. Furthermore, natural disasters reap $211 billion from the global supply chain annually. Having a larger global footprint is how Amazon’s supply chain has been able to maintain operations in the face of natural or man-made disasters. This is contingency planning.
The IIoT empowers contingency planning by giving supply chain entities real-time data from an endless number of sources, which range from online browsing data to point-of-sale data. Consequently, supply chains can react appropriately and divert resources to maintain operations. But, the key to utilizing this information lies in knowing what to do and how to do it when an event occurs. In other words, more companies will diversify distribution, supplier and storage networks throughout 2017 to prepare for what might happen in the future.
The Big Picture.
Supply chains must accept that they cannot equal the power of Amazon’s supply chain without embracing these new trends. New technologies are great, but chances are Amazon has already implemented them. Rather than falling into despair, you can use these trends to re-evaluate processes and practices in your organization, which will help you stay competitive with Amazon.
The complexities of the global supply chain rely on your willingness to take advantage of new trends and technologies today, as well as tomorrow, so do not squander this opportunity.
Related posts:
by Fronetics | Nov 26, 2014 | Blog, Manufacturing & Distribution, Supply Chain
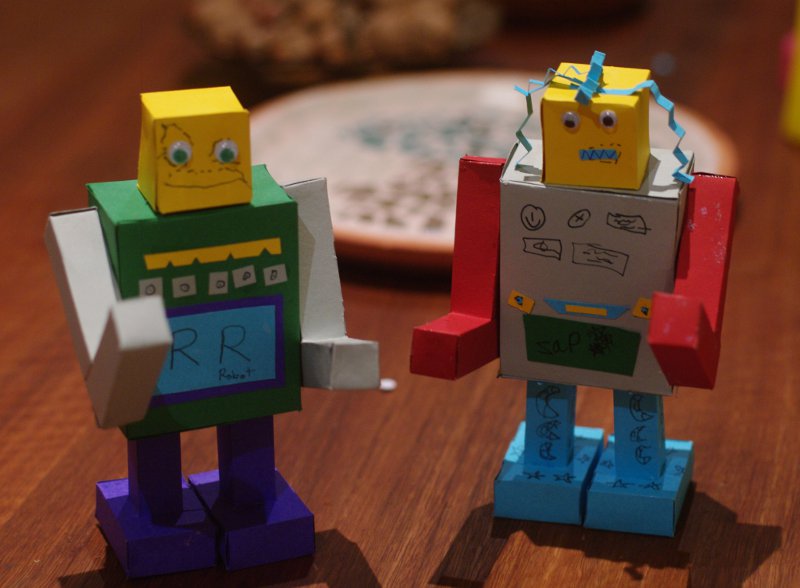
MIT’s Julie Shah was named one of MIT Technology Review’s 35 Innovators Under 35 in 2014. In an interview with Will Knight, Shah discusses the possibility of collaboration between human robots:
“In factories there are usually physical barriers between people and robots. Originally, this was for safety—industrial robots were unwieldy and unyielding. Although robots are increasingly designed to safely share human work spaces, even in these settings, people do one set of jobs and robots do another.
Imagine if robots could be truly collaborative partners, able to anticipate and adapt to the needs of their human teammates. Such robots could greatly extend productivity. That possibility is really exciting to me.”
Shah is working companies including BMW, Boeing, and Embraer to develop robots that can interact intelligently with human co-workers.
According to Shah:
“If you can develop a robot that’s capable of integrating into the human part of the factory-if it just has a little bit of decision-making ability, a little bit of flexibility- that opens up a new type of manufacturing process more generally.”
Research conducted by Shah has found that teams made up of humans and robots collaborating efficiently can be more productive than teams made of either humans or robots alone. Shah’s experiments have shown that the collaborative process reduced human idle time by 85%. Additionally, Shah found that workers seem to be comfortable with the idea of robotic coworkers.
Are you ready for a robot to join your team? What are your thoughts on teams made up of humans and robots?