by Fronetics | Nov 1, 2017 | Blog, Manufacturing & Distribution, Strategy, Supply Chain
Manufacturing companies are hoping to continue their revenue growth in 2018 by focusing on 3 key areas.
KLR has released the results of its annual manufacturing industry outlook report, and the optimism following last year’s elections will continue straight through 2017.
With promises of tax reform, decreased federal regulations and looser trade agreements, manufacturers have slowly seen revenue growth throughout the U.S. markets. That growth is projected to continue into 2018.
56% of respondents expect business will continue to increase throughout the year.
And though manufacturing companies are striving to control their costs and cut back on unnecessary expenses, many companies reported increasing their marketing budgets, including technology, to invest in the future of their revenue growth.
So where is the additional money going? Manufacturing companies are investing their profits back into new products, expanding markets and breaking into new territories.
Here are the top 3 priorities for manufacturing companies in 2018.
1. Increasing share in existing markets
Over the next 12 to 18 months, 64% of the manufacturers surveyed expect their growth to come mainly from increased market share and organic growth in existing domestic markets. Manufacturing companies are looking to increase their market share through innovation, strengthening customer relationships, reliable hiring practices, and staying ahead of their competitors.
2. Seeking new markets for products and services
Manufacturing companies are trying to think outside of the box when it comes to expanding their markets. Avon got its big break when it took the now-dated approach of selling products door to door. By trying a different avenue, it was able to increase revenue without fighting for retail space with other corporate giants. Like Avon, companies are working hard to come up with innovative ways to break into untapped markets.
3. Developing new products and services in response to changing consumption patterns
Using social media platforms and other marketing tools, it’s easy for manufacturing companies to stay in touch with their customers. This engagement provides the best insight into the types of products, features and solutions your customers are looking for. Based on this crowdsourcing, or social listening, companies are able to develop products that they know will resonate with consumers and their changing needs. Though product development can be expensive and risky, incorporating customers into the conversation helps manufacturing companies minimize risk.
Despite growth throughout 2017, there are still challenges that manufacturing companies face. How are manufacturers coping with these challenges? They are adjusting their priorities and focusing on these three areas to continue growing their business and, ultimately, their sales.
Related posts:
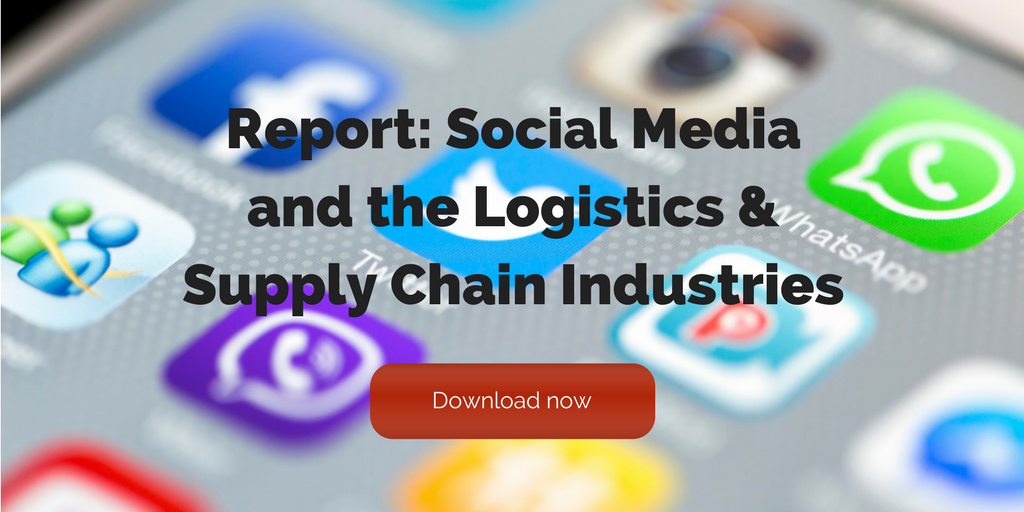
by Elizabeth Hines | Aug 22, 2016 | Blog, Logistics, Manufacturing & Distribution, Strategy, Supply Chain
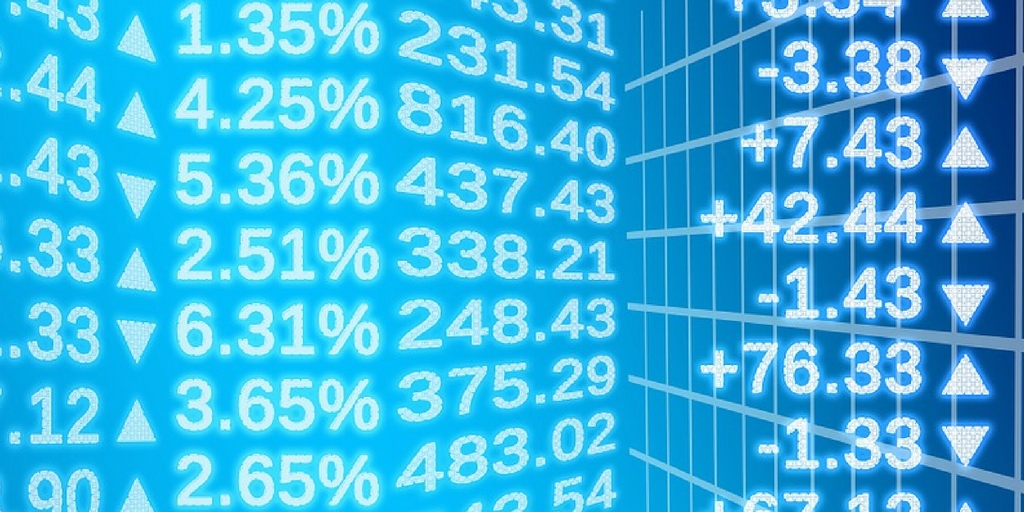
Improve your company’s financial performance by implementing a risk-management strategy that plans for everyday events and disruptions.
Supply chain disruptions can have a significant impact on business and financial performance. A recent PwC and the MIT Forum for Supply Chain Innovation survey found a strong correlation between the maturity of businesses’ risk-management processes and reduced decline in operational performance indicators in the face of disruption.
A supply chain company’s need for a well-developed risk-management strategy is clear. That means planning for disruptions beyond the big-impact events, like environmental catastrophes, cyber attacks, and geopolitical instability. Companies need to be better prepared to handle day-to-day bumps in the road.
Managing everyday risks
Managers will often consider cataclysmic events but ignore the smaller risks that create friction in the supply chain. Dealing with these smaller factors in a reactive and piecemeal fashion is inefficient and ineffective and can significantly hurt your company.
Consider the following tips when developing an effective risk-management strategy that focuses on the everyday risks:
1) Employ a robust strategy that is always evolving.
Consider all of the factors that currently influence your supply chain, and be vigilant in terms of new technologies or emerging risks that could impact operations in the future.
2) Put a leader in charge.
Choose someone experienced in crisis management, negotiation, and critical problem-solving. This leader should be skilled in diplomacy and remaining calm under pressure.
3) Make sure the strategy is flexible.
A strategy that it uncompromising and rigid can exacerbate issues.
4) Define your comprehensive process.
Develop a clearly defined process to mitigate events such as cash-flow issues, inventory risk, competitor interruptions, client credit risk and default, data backup and recovery, key client attrition, employee satisfaction and retention, social media use and abuse, and reputation recovery.
5) Include human resources in the strategy.
Consider moving employees into new roles as a solution. Moving an employee into a new role permanently (or for a specified period to deal with an event) can help mitigate issues.
6) Don’t hide the issue.
If there is a problem, be sure that the clients hear about the problem from you. Be clear, concise, and honest when you contact clients. Explain what the issue is and what you are doing to address it.
7) Get everyone on board.
Take the time to make sure everyone is educated about the strategy and who is in charge. If just one person knows the strategy, it will not be effective.
Related posts:
by Fronetics | Feb 4, 2016 | Blog, Leadership, Strategy, Supply Chain
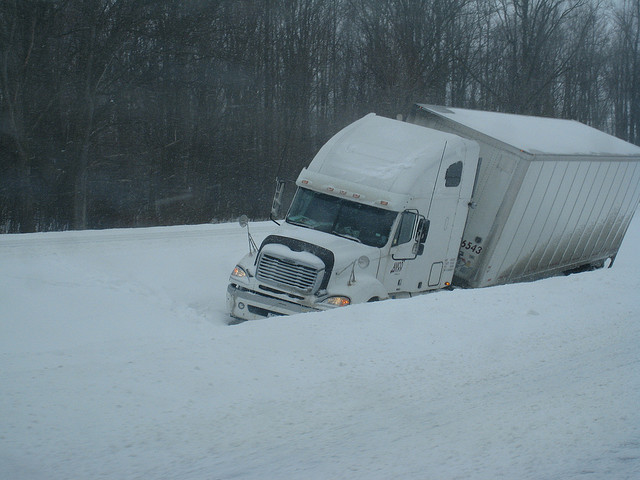
When it comes to leading during difficult times in the supply chain, planning is critical. So is flexibility.
Winter storm Jonas is estimated to have cost $1 billion USD, although some believe the cost could go as high as $3 billion USD, as it paralyzed a large swath of the mid-Atlantic and Northeast. Some 30 inches of snow touched down on several East Coast cities, which cancelled over 12,000 flights and kept people out of work for days.
When difficult times strike, having a plan is critical. For example, with electricity still working, business doesn’t need to come to a close for days on end. Researchers who did a study at Chinese company C-trip encourage people to work from home during storms: “We encourage companies to do a trial the next time an opportunity presents itself — like bad weather, traffic congestion from major construction, or a disruptive event (such as a city hosting the Olympics or the World Cup) — to experiment for a week or two. We think working from home can be a positive experience, both for the company and its employees, as our research with C-trip showed. More firms ought to try it.”
The supply chain can be disrupted in many ways: natural disaster, terrorism, fluctuation in materials. When the problem hits, it’s good to have a plan, but one can’t always be prepared for every scenario. According to the president of global public affairs for UPS, Laura Lane, who had her share of difficult times when she was a young foreign officer in Rwanda during the genocide in 1994, “You have to make decisions that will result in the greatest good — and from that perspective, every decision becomes crystal clear.”
Lane shared her thoughts about how to handle difficult situations in the supply chain with The Wall Street Journal recently.
Look for leaders everywhere
Lane believes that it’s not only C-suite managers who can handle disaster. Being open to ideas and letting specialists rise from the ranks could be a game-changer in critical situations. “Don’t judge people based on their years of experience. Greatness can emerge from anyone on your team — people with decades of experience, or those just starting out.”
Don’t let fear stop you
When you are ultimately responsible for a huge decision involving lots of people and money, fear can infiltrate the mind and body quickly. Remember that you’re in the position you hold for a reason. Don’t let self-doubt or uncertainty about how things will play out delay your decision making. See boundaries and obstacles are new opportunities to find alternatives. Lane says, “Challenge how things are done, and rewrite the rules, if needed,” she says.
Think of the larger vision
Remember what the goals of the company are, and that people have been put in specific roles for reasons. Remember that your situation most likely involves teamwork, and that you can rely on the support, ideas, and voices of others, especially when the vision of the company becomes foggy in the stress of the moment. “Delivering on your promises and grounding your actions in your values is what is needed to be a great leader. You have to believe in the greater good of what you’re doing and then bring others along with you in realizing the bigger vision.”
You may also like:
by Fronetics | Nov 25, 2015 | Blog, Data Security, Data/Analytics, Strategy
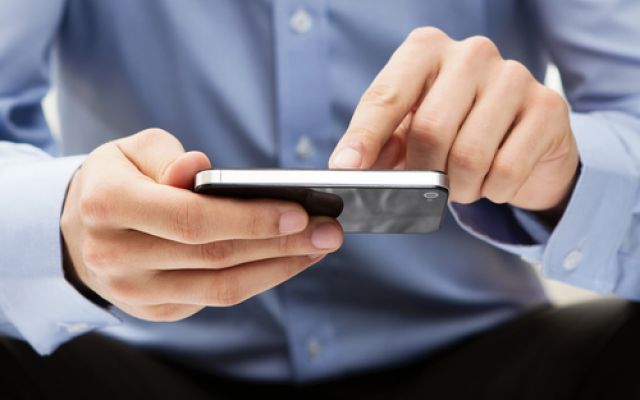
Apple has been making lives easier for years with its personal electronics devices, and its new step towards security will bring relief to many people and, in the age of BYOD (bring your own device) many businesses with be grateful. An increase in two digits, from four to six, might not sound like a big difference, but, in fact, it is. With a four digit passcode there are only 10,000 possible combinations, and the bump up to six digits allows for 1 million possible combinations. According to the website Cult of Mac, “With a brute-force computer, it takes on average 40 seconds to attempt every passcode; theoretically, it would take a maximum of 111 hours, or 4.5 days, for a computer to crack a four-digit passcode. Bump it up to a six-digit passcode and it’d take the same machine 11,000 hours, or 458 days.”
The Age of Flexible Work Arrangements & BYOD
Companies and employees are increasingly going the route of allowing personal devices to be used in the workplace, and allowing people to work from home. According to a recent study by the Quarterly Review of Economics, people who work from home are more productive (the study showed a 13% increase), less exhausted, and less likely to leave a job. As more people work from home and on the road, and want to immediate access to their personal and professional information, BYOD has become popular.
According to a thorough Ponemon Institute study on the security impact of mobile device use by employees, many employees want to use their cell phones, but don’t have a full grasp of how security is being impacted or could be breached. Here are some telling numbers:
- 70% of respondents said that BYOD makes them more productive because they have access to personal and professional information in one spot
- A total of 62% of the respondents reported that access to corporate information via mobile devices is “essential” to productivity
- 38% said that they are more efficient and work time was reduced by roughly 30 minutes
- Only 20% of participants reported receiving training on security of corporate content on mobile devices. Of those who were trained, 74% reported that it was not helpful in reducing security threats on mobile devices.
- 66% said that they “frequently” or “sometimes” download apps that aren’t approved by their companies
- Only 19% check for viruses or malware, and 22% believe this behavior invites any danger to their company
Can a Passcode Fix Security Problems
Apple’s new security option is going to help, no doubt. Breaching a password is one issue, but security concerns extend beyond passwords. One of the major benefits of Apple’s new passcode option is that many companies will have to review their mobile device policies. Emails, client information, legal documents, finances, and other important information are sent from and stored in mobile phones. To say this is delicate information is an understatement.
Here are some suggestions for tightening security:
- Review all vulnerabilities in security including devices, networks, and applications
- Require password protection
- Have detailed security protocols for each electronic device
- Determine which activities can be performed and which can’t on devices
- Consider periodic IT check-ups on devices
In the modern workplace, being able to balance flexibility with security is key to a productive and safe business. Properly training employees, setting clear expectations, and instilling trust in employees is important. If employees are trusted they will want to protect your company’s valuable information, but they can’t do the right thing without clear and accessible policies.
This post originally appeared on Electronics Purchasing Strategies.
by Fronetics | Oct 14, 2015 | Blog, Marketing, Social Media, Strategy, Supply Chain
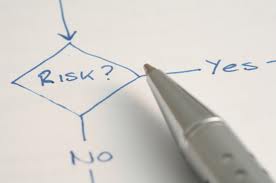
A study conducted by Accenture found that supply chain risk management is seen by companies as a priority. Seventy-six percent of companies who participated in the survey described supply chain risk management as important or very important, and 25 percent of respondents reported that they are planning to make increased investments of at least 20 percent in supply chain risk management in the next two years.
Social media is one place where an investment should be made.
Social media is not just for kids. Social media is not just for socializing. Social media is a business tool that can play an important role in supply chain risk management. Here are three reasons why your company should invest in social media.
News in real time
Social media is the new “newswire.” It has supplanted the AP, Dow Jones, and Bloomberg for breaking news. The earthquake in China, the Boston Marathon bombing, the death of Obama bin Laden, and the engagement of Prince William to Kate Middleton were all stories that broke on Twitter. Stories that played out over social media include the horsemeat scandal and Apple’s China supply chain sage.
When it comes to supply chain risk management, knowing what is happening in real time is vital. Whether it is learning about an earthquake that happened near your manufacturing facility, or monitoring the path and intensity of a hurricane – real time information will enable your company to make more informed and timelier decisions on how to manage or mitigate risk.
Identify emerging risks
In addition to providing timely information on events such as natural disasters and terror attacks, social media is a tool that can be used to identify additional risks to your company and supply chain. Specifically, social media can be used to identify risks such as weak links in your supply chain, missteps made by a supply chain partner, and customer concerns/dissatisfaction.
Managing and mitigate risks
A survey found that 89 percent of consumers began doing business with a competitor following a poor customer experience. The survey also found that 50 percent of consumers give a brand only one week to respond to a question before they stop doing business with them.
Social media is a great tool to provide customers with a great customer experience – fast. By engaging a dissatisfied customer over social media, listening to their concerns and addressing them – you are more likely to retain that customer and gain more customers. As the adage goes: “It is less expensive to retain a current customer than attain a new customer.”
Additionally, because social media allows for information to be distributed to a large number of people instantaneously, it is an effective tool for letting customers and partners know you are on top of an issue, or for altering them of an upcoming disruption.
When it comes to supply chain risk management communication and information is vital – social media is an effective tool to add to your company’s risk management toolkit. Get your company off the social media starting line.
This was previously published on Electronics Purchasing Strategies.