by Jennifer Hart Yim | Jul 13, 2017 | Blog, Customer Service, Manufacturing & Distribution, Strategy, Supply Chain
Manufacturers who listen and focus on customer experience and service will win in the battle to increase revenue and company size.
This post comes to us from Kevin Jessop of Cerasis, a top freight logistics company and truckload freight broker.
Manufacturers have always struggled to know their customers. But, modern businesses have grown to encompass an omnichannel sales opportunity. Customers can place orders online, by phone, in person and in nearly any other means desirable. Unfortunately, this means manufacturers face an even greater challenge, as more customers translate into greater use of customer service.
In addition, customers are continuing to demand lower prices and free shipping. But, our predictions’ post noted how manufacturers are having trouble with transforming customer input into responsiveness and enhancements to the customer experience. Those who do achieve this feat can realize significant increases in revenue and high returns. But, how do manufacturers turn their focus to the customer experience?
1. Determine What Customers Want Today.
Modern technologies can give manufacturers real-time insight into the ways products are moving in retail and online environments. But, patterns today do not necessarily reflect the needs for tomorrow. As a result, manufacturers must be wary of overproduction and focus on providing the products customers want now, not tomorrow. In other words, manufacturers need analytics from point-of-sale systems, transportation metrics and more. Furthermore, companies must extend the buying cycle to get as much information as possible from consumers.
2. Lengthen the Buying Cycle Through Interaction.
Remember the catch-phrase, “Do you want fries with that?” Well, that concept holds true in the supply chain and for manufacturers alike. Consumers may not always go for what you are offering, but they want you to offer more than you have. Essentially, this creates a stronger level of customer service, and it can turn into additional purchases. More importantly, it gives manufacturers a chance to find out more about what the customer wants.
For example, a customer is a shoe store may purchase shoes, but if offered a new brand of socks, he or she refuses. During the ensuing conversation, the representative finds out that the socks have gathered a bad reputation on social media.
While this example is a bit extreme, it highlights how a longer buying cycle can translate into insights for manufacturers. In addition, a longer buying cycle naturally improves the company’s reputation.
3. Partner With Appropriate Businesses.
Businesses are often grouped into a broad category of competitors, but businesses can work to help manufacturers become more responsive to their consumers. This can include offering like products in package deals, compiling changes in like demographics or sharing information to reduce costs across the scope of both companies’ transportation networks. In fact, manufacturers can collaborate with third-party logistics providers (3PLs), like Cerasis, to realize the benefits of collaboration and taking advantage of business-to-business (B2B) sales through integration of systems, explains Louis Columbus of Supply Chain 24/7.
Essentially, every interaction with another business increases the possible customer base by both the number of employees in the new business and the number of customers working with that specific business. As you go through the chain of business, the opportunity for enhancing customer experiences grows.
4. Take Extra Care of B2B Partners.
B2B sales are more fickle than business-to-customer sales. According to a Gallup study, reports Chief Executive, more than 70 percent of B2B companies are facing setbacks and decreases among their B2B partners because of lacking customer engagement. Since B2B sales often take place behind the public’s perception of the economy, it is important that manufacturers work to create engaging relationships through content-driven, digital experiences. This can include videos demonstrating how products work, informative blog posts that provide something free and helpful to customers and beyond. Of course, the same concept of using digital technology to engage customers can be applied to B2C sales channels as well.
5. Be There for Customers After the Sale.
We have all experienced that disheartening feeling when calling customer service and getting lost or frustrated with the lack of service offered. Manufacturers need to be present to their customers after the sale because the level of customer service provided will be shared widely on social media. More importantly, poor customer service or inability to help customers with product issues or questions will gain a huge following much faster than a positive comment.
For example, manufacturers could send out emails for high-tech products that will require updates, or they may create online video banks to teach customers how to use the products easily. The opportunity for creativity in engaging current and future customers is only limited by your imagination!
Listening to What Customers Say is the Key to a Positive Customer Experience.
These steps go back to one thing, listening. Your company should listen to what internet-connected devices are saying about customers. You should listen to what your B2B partners are saying about your products and customers. Listen to what stakeholders, employees and B2C customers are saying. If you take the time to listen, you can meet the growing expectations of a modern customer base that wants a higher level of service than past generations. Ultimately, manufacturers who do listen and focus on customer experience and service will win in the battle to increase revenue and company size.
This post originally appeared on Cerasis’ blog.
Related posts:
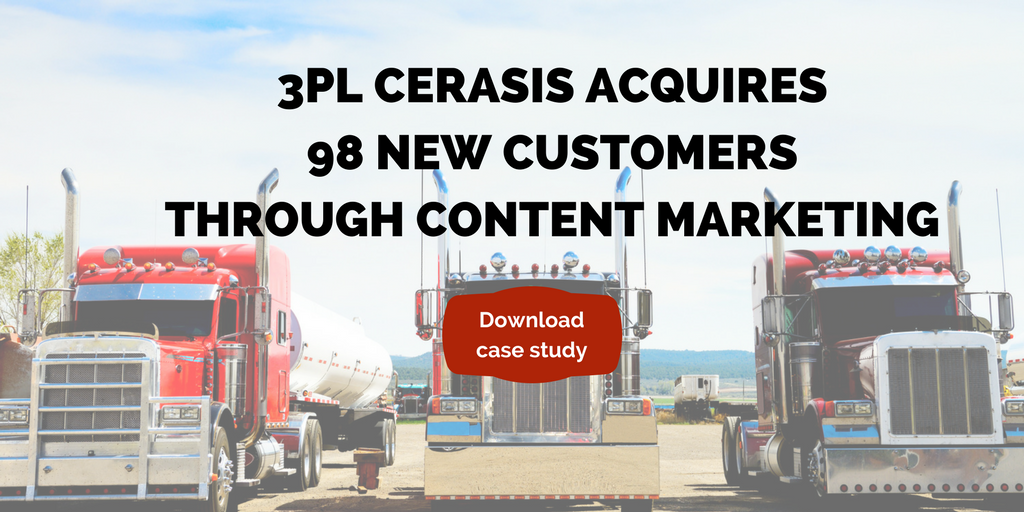
by Fronetics | Jun 21, 2017 | Blog, Current Events, Logistics, Manufacturing & Distribution, Supply Chain, Transportation & Trucking
This post comes to us from Kevin Jessop of Cerasis, a top freight logistics company and truckload freight broker.
The Paris Climate Agreement. Let those words hang for a moment.
Throughout the course of the 2016 election and now the Trump Administration, many Americans have expressed dissatisfaction with the Paris Climate Agreement. True to campaign promises, the new Administration has started the process of removing the U.S. from the agreement, which has major implications for supply chains and shippers around the globe. While the Trump Administration’s impact on supply chains has been discussed previously on Cerasis’ blog, the president’s decision to leave the agreement has shocked the industry, and you need to understand why and what is really going to happen over the next four years.
What Is the Current State of the U.S. in the Paris Climate Agreement?
This may come as a shock, but the Paris Climate Agreement has only been in force since November 4, 2016. As a result, the U.S. has not yet enacted changes under the agreement. The only measure that would have fallen under the Agreement’s terms is the continuation of Customs and Border Protection’s (CBP) rules for maritime statutes.
Lawmakers would have likely passed new legislation to increase environmental scrutiny of supply chains and shippers over the next few years. Moreover, the U.S. would have sent monies to Convention of Countries within the Agreement to help fund eco-conscious goals. The Administration’s actions indicate such changes are not likely to occur, but they could still happen. But, how?
What Is the Timeline for Withdrawal?
The full text of the Paris Climate Agreement is available online through the United Nations Framework Convention on Climate Change (UNFCCC). Article 28 defines the process through which a member of the original Convention may withdraw from the Agreement, and it is a surprise to many to learn that the new Administration cannot simply flip a switch.
Article 28 states that any country wishing to withdrawal may only do so after three years have passed since the agreement went into force. Since the enforcement date was November 4, 2016, a country cannot submit a notification of withdrawal until November 4, 2019. Now, there is another side of the withdrawal.
To prevent countries from withdrawing due to political changes and safeguard the longevity of the planet, any withdrawal still requires a one-year term from the date of notification. In other words, the Administration cannot effectively withdraw from the agreement until at least November 4, 2020.
The 2020 Presidential Election is scheduled for November 3, 2020. This means that if President Trump follows through with submitting a notification of withdrawal in 2019, actual withdrawal will not occur until the day after the 2020 election. Therefore, the question becomes, “How would a notification of withdrawal play out during the election? And if so, will it help or hurt his chances or re-election?”
The precedent for polarization during the previous election cycle indicates President Trump will proceed with plans to withdraw the U.S. from the Agreement when the time comes. The June announcement is merely a call to action to prepare for withdrawal over the next few years. So, what does that mean to both domestic and international supply chains?
The Impact of Withdrawal on Supply Chains.
There are only three countries on the planet, counting the U.S. intention to withdraw, that are not part of the agreement now. This means that every foreign-originating business transaction with U.S. manufacturers, distributors or other partners, except for Syria and Nicaragua, will be at risk. The governments of other countries may look unfavorably at working with U.S. companies due to the new Administration’s plans.
Multiple big-business empires, ranging from Facebook to Goldman Sachs, have condemned the move to withdraw. According to BBC News, part of their rationale is simple. The changes the Agreement dictates reflect existing concerns and actions that many U.S. businesses, including shippers, have already undertaken. Even ExxonMobil, a company whose previous CEO holds the title of Secretary of State, urged the new Administration to remain in the Agreement.
These major companies have already invested time and money in energy-efficienct, eco-conscious programs, and many of their business-to-business partners have followed the same pattern. With the overwhelming majority of the world’s countries committing to this cause, there will be an opening of the “floodgates for businesses, scientists and engineers to unleash high-tech, low-carbon” technologies. As a result, the U.S. could fall further behind the global engineering and science goal, which helps all businesses succeed. In other words, domestic companies may have a more difficult time finding the labor or technologies needed to maintain profitability in the interim.
Is There a Much Darker Side to Withdrawal?
Without getting into a discussion on the science behind global warming, it is important to note things that have happened that may continue if global warming continues. For example, sea levels had risen 2.6 inches from 1993 to 2014, reports the National Oceanic and Atmospheric Administration (NOAA). If left unchecked, numerous ports, businesses, cities and whole seaboards could be lost in the next few decades. To ensure stability and growth along long-term goals, this is a risk that must be mitigated immediately.
The rising sea level is a fact in the heavily disputed conversation about global climate change.
For shippers and supply chains, the risk of not doing anything is too great. Thus, the new Administration means well, but withdrawing from the Agreement is not a change that will impact businesses before 2020. Furthermore, the backlash from the public toward companies that abandon eco-conscious goals could be severe. Shippers could face higher tariffs and additional troubles in shipping goods domestically or abroad.
It is in your company’s best interest to pursue energy-efficiency goals, including working with well-known partners, like Cerasis, to help you reduce waste, eliminate redundancy and continue making healthy profits throughout the future, regardless of who sits in the Oval Office.
This post originally appeared on Cerasis’ blog.
Related posts:
by Jennifer Hart Yim | May 11, 2017 | Blog, Current Events, Logistics, Manufacturing & Distribution, Supply Chain, Transportation & Trucking, Warehousing & Materials Handling
This post comes to us from Adam Robinson of Cerasis, a top freight logistics company and truckload freight broker.
Imagine a world where automation comes together with technology to deliver products without human intervention. An order is placed by a consumer. 3-D printers pick up the details and print the finished product. It’s then picked by robots from the shelves, packaged and placed into a self-driving truck. The trucks leave the facility, and drones are automatically dispatched from the truck to deliver products while moving. The truck never stops until arriving for reloading.
This example generates a huge amount of data that can leverage in the supply chain. But, the same data can have a drastic impact on transportation planners and agencies around the globe. While this example may still be a few years off, it is important that you understand how the top emerging trends in automation will shape supply chains and transportation processes in the coming years.
The Standard Definition & Components of Automation
Today: There is a standard definition of automation in the supply chain. Anything that can be handled via today’s computer systems can be automated. This includes billing, generation of bills of lading, compliance reports, and even movements throughout a factory or warehouse floor.
Historically, automation has been applied to virtual processes, like order auditing or customer service reports. However, the trends in automation are changing to reflect actions that function more like artificial intelligence, not just a search and locate program on the computer.
Additive Manufacturing
What is it?
Additive manufacturing includes all actions in the supply chain that can enhance existing factory production, if not replace it entirely. Additive manufacturing may be handled manually, but automating this process is as simple as turning on the power and connecting to the Internet of Things (IoT).
For example, additive manufacturing might involve the use of 3-D printers to create replacement parts at the store for consumers.
Today’s status: Unfortunately, the capacity of 3-D printers remains in infancy, capable of only producing simplified parts out of liquid polymers.
Virtual Reality Comes to the Forefront.
Meanwhile, Google Glass and other virtual reality tech are changing how customers complete their orders. In addition, the same technology can be overlaid with augmented reality to give repair technicians and individuals greater resource access when making repairs, checking order contents and fulfilling orders.
For example, augmented reality glasses will soon detect package dimensions and classify the package according to dimensional pricing models.
Today’s Status: Today, this technology is limited to automated identification and data capture (AIDC) applications. Advancements in virtual reality over the past year indicate its future might be much closer than “meets the eye.”
Additive manufacturing will gradually move products from warehouses and distribution centers to be closer to end-users. As a result, the amount of last-mile traffic may increase.
Robotics Enhance Inbound and Outbound Logistics for Shippers.
Another trend in automation involves robotics. By definition, robotics are the icons of automation. They perform functions at the request of a system or person, but more of today’s robotic systems are performing duties upon request from an order fulfillment system.
The order process automatically notifies robots in warehouses and triggers the flow of processes as seen in the opening example.
Robotics Improve Inbound and Outbound Logistics.
Robotics are not isolated to warehouse pulling for outbound logistics. They can be used to manage inbound and outbound processes and strategy. Through trends in automation and robotics, supply chain companies will have the tools and resources necessary to ramp up throughput and decrease product cycle from order to delivery. Therefore, more trucks and drivers will be needed, but the looming driver shortage and capacity crunch will trigger another automation trend.
Autonomous Vehicles/ Trucks
Automation begets automation. With advances in technology and the IoT, most major companies, including Uber, Facebook, Google, and Amazon, have launched autonomous vehicle and truck pilot programs.
These driverless vehicle programs will give supply chains access to a new inexhaustible resource for moving products, overcoming the challenges inherent in the driver shortage and capacity crunch.
The driver shortage and capacity crunch are likely to come to a head in 2017, as consumers demand more product, at lower costs and faster than ever before.
Some setbacks have occurred, like the first self-driving car wreck earlier this year. With each setback and challenge, companies have pushed back to overcome the obstacles.
In response to increased interest in driverless vehicles and trucks, the National Transportation Safety Board (NTSB) has issued recommendations and created an advisory panel to review ongoing driverless vehicle advancements and maintain public safety.
Transporters and supply chains will respond to this direction by leveraging the trends in automation and power of data to ensure compliance with increased government oversight, through the agencies you represent.
Companies have already tested cross-country driverless trucks, albeit with a person ready in the cab to take over in the event of a system failure. However, the wide-scale deployment of this level of driverless trucks is far from implementation.
In the interim, more automated vehicle systems will work in tandem with drivers to enhance safety and maintain vehicle control. Similar systems are already deployed in crash and pedestrian detection systems, automated braking and tracking control in today’s vehicles. It is not difficult to apply today’s technology and automated features to the fleets and drivers of 2017.
Trends in Automation: Whats the Potential?
The potential applications of this type of technology can include real-time traffic condition monitoring and warnings, redirecting traffic before pile-ups and accidents occur, similar to Google Maps’ capacity to show traffic congestion in real-time.
Data through such systems can automatically feed back into transportation planners’ systems to automatically change signal phase and timing and enable immediate rerouting or adjustment of traffic flow on a broader scale.
Related posts:
by Jennifer Hart Yim | Mar 16, 2017 | Blog, Logistics, Strategy, Supply Chain, Transportation & Trucking
Try these affordable online tools and mobile applications to help the logistics professional control their business.
This guest post comes to us from Adam Robinson, marketing manager at Cerasis, a top freight logistics company and truckload freight broker.
Logistics professionals require exemplary international online logistics tools to help them carry out their daily businesses with ease and deliver the best for their customers. For any developing business, adopting the widely used and affordable technologies is more economical. Mobile phones can offer incredible services in any business from inventory tracking and shipments to the execution of procurement transactions. Let’s base our discussion on online trucking logistics and mobile applications that can be used in supply chain management on a global basis by the logistic professional to control their business.
Top 8 Online Logistics Tools For Logistics Professionals
1. The Scandit mobile application software
Scandit is one of the top mobile online logistics tools used in international logistics in supply chain management. It is an advanced barcode scanner that is capable of extending bar code scanning to technology savvy inventory manager. Unlike other scanners, the scan in Scandal doesn’t have to be perfect to process data as it can scan hard to reach the barcodes with ease. It is also cross-platform enabled to facilitate ease of data sharing across other networks online.
2. The Easy stock mobile application software
This optimization tool for inventories is cloud based. It systematically limits access from the warehouse locations to minimize cost while maximizing on the availability of highly profitable items. It is one of the essential online logistics tools that can help managers forecast, plan the inventories, and a budget for the available resources. Most logistics prefer integrating the use of this app to automate procurement and replenish other processes to raise the profit margins.
3. The Web fleet Android application
The web fleet Android application is an incredible mobile application suitable for retaining control of the daily operations of your workforce. This app can be accessed through web browsing, where the logistic professionals can manage their business in real time just from their phones or laptops at the comfort of their seats. This application will help you track the daily operations 24 hours to ensure the credibility of your workforce and efficiency in your operations.
4. Service Max mobile app
Service Max mobile app is one of the best and top-selling apps in service management field that every logistic professional should consider using. The app combines the integration of service contracts, management of orders, workforce optimization and monitoring of social media customers. It builds an end-to-end service organization view of your relations with the clients who help you analyze the quality of your services and the reactions of the customers towards them. The feedback shared through social media, such as Twitter, by the people using your services helps you to gauge yourself and point out the areas that require improvement.
5. The Co-pilot Android mobile app
Co-pilot Android mobile app is an incredible online logistics tool employed in international logistics. It offers mapping and direction routing. It facilitates navigation through online tracking of your vehicle for efficiency. The application has additional algorithms that help the truck drivers follow efficient routes to avoid traffic and other obstacles that can delay the delivery. It is with a 100% surely that every logistic will be interested in the quick delivery of his/her business services within the shortest time possible which can be catered for using this application. The app also gives the dynamic information of the various navigation routes such as truck height and weight to ensure smooth navigation in the designated routes.
6. The Logistics mobile app
Logistics is a multipurpose free on-line Android mobile application used for on-line tracking logistics. It can be used to track drivers, shipment of goods, vehicles and client’s operations. Every logistic professional should look for this app to increase the visibility of the entire supply chain with the use of a smartphone. This incredible app will help you monitor and track your logistic operations with ease and confidence.
7. The Evernote online mobile application
Evernote, as well as Eduzaurus, has been rated as the best tool used by professional logistics in organizing important files, documents and images and is, therefore, a widespread global application in the field of supply chain management. It is widely known and used in online filing and storage of documents used in the supply chain. It has an added advantage as compared to other supply chain mobile applications due to its ability to record voice memos when you are away through an inbuilt voice recording technology. This helps the manager to track the success of the workforce when away. With this mobile application, it is a guarantee of success to the managers and logistics in file organization field.
8. The Cerasis Rater — A Web-Based Transportation Management System with Companion Mobile App
The Cerasis Rater allows you to process shipments for the following over-the-road modes:
- Less than truckload
- Small Package, also known as Parcel
- Intermodal
- Full Truckload moves
The Cerasis Rater eliminates the manual process of booking shipments. Before using online logistics tools, you’ve most likely wasted time, energy, and money trying to maintain your carrier rates, calling carriers to try and get the best price, and lost efficiency from having to keep up with paper bills of lading. The Cerasis Rater offers many automation & efficiency benefits to include:
- Process your own shipment, at any time, 24/7 through our web-based portal.
- Upload, store, and maintain your shipper address book with pre-population to maintain accuracy and save time.
- Store your custom commodities, and over time the Cerasis Rater puts the most commonly used to the top of the list for faster processing.
- Choose from multiple carriers whose rates are negotiated specifically to your needs within the system, allowing you to not waste time or energy, and to not leave money on the table at the time of shipment.
- Choose carriers based on rate, transit time, and limit of liability to ensure your cargo and your peace of mind are covered.
- Print batch freight quotes, bills of lading, invoices, and labels all within the same system.
- Create, email, and print bills of lading when you are done processing your freight shipment.
- E-mail notification options customized to your needs.
Related posts:
by Jennifer Hart Yim | Feb 13, 2017 | Blog, Logistics, Strategy, Supply Chain
Supply chains must accept that they cannot equal the power of Amazon’s supply chain without embracing these new trends.
This guest post comes to us from Adam Robinson, marketing manager at Cerasis, a top freight logistics company and truckload freight broker.
Amazon’s supply chain continued push deeper into new and existing markets will define additional trends in the supply chain throughout the coming year. While supply chain entities struggle to stay competitive with the e-commerce giant, more organizations will look for ways to eliminate inefficiencies and boost operations. Fortunately, these five trends may alleviate some of the strains of competition by giving supply chain partners an advantage in the global market.
Top 5 Trends to Know to Compete with Amazon’s Supply Chain
1. Robotics Will Grow More Versatile.
Amazon’s purchase of Kiva Robots changed the landscape of robotics in the supply chain. However, new companies are being created and developed to fill the void. The robotics company Starship released a robot that delivers meals and groceries to people in Euro metro markets. Meanwhile, Lowe’s has created the LoweBot, which boosts customer service, explains Dan Gilmore of Supply Chain Digest.
More companies are turning to robotics to find new ways to bridge the divide between a dwindling number of customer service representatives, including store associates, and maintaining around-the-clock operations. Across the spectrum, robotics will become more versatile and accessible. In other words, robots will gain new movements, capable of picking items from shelves in warehouses and storefronts.
Per IDC Manufacturing Insights, the use of robotics will become more platform based through robot-as-a-service, reducing costs of deployment and maintenance. Furthermore, the speed of operation of robots will increase more than 30 percent by the end of 2017. Clearly, robotics will become more important in 2017 than during any previous year.
2. Technology Will Reshape Procurement Practices.
Better procurement practices translate into better overall sales, but the role of procurement in driving sales’ statistics will change throughout 2017. Today, procurement drives up to 67 percent of sales, explains Johnathan Webb of Forbes magazine, as procurement professionals look for innovative ways to produce effective, superior products.
For example, Johnson & Johnson procurement professionals actively review market trends before making purchases. Upon identifying these trends, a correct forecast of supply demands can be generated. Thus, the role of procurement has become more focused on being physically involved in market news and research, not just signing purchase orders in an office.
3. More Businesses Will Create E-Commerce Platforms.
Amazon’s supply chain empowered the e-commerce market by giving everyone an opportunity to sell their goods online, which has made competing with Amazon difficult at best. Amazon’s supply chain expansion culminated in more companies looking to enter e-commerce without giving shares to Amazon. Companies expanded e-commerce and omnichannel solutions simultaneously as well, reports Steve Banker of Logistics Viewpoints.
For example, Walmart and Kmart redesigned their mobile e-commerce interface for consumers, making shopping and purchasing online easier and integrated with major companies. A simple search for a product on Walmart.com reveals partnered listings with Wayfair and third-party sellers, much like Amazon’s current vendor options. Moreover, customers can make purchases online and have them shipped to the store or their home. At Walmart, customers can even pick up orders without ever getting out of the car now. Ultimately, more businesses will seek out partnerships with bigger companies to stay competitive with Amazon’s bare price points and ease of use.
4. User Preferences Will Enhance Mobile Management Systems.
Traditional warehouse management systems (WMS) lacked integration with other systems. Procurement strategy was not always evident. Accessibility of systems depended on in-house IT departments, and upgrading access terminals could cause extreme delays and problems in operations. However, newer management systems, such as a comprehensive transportation management system (TMS) that integrates warehouse management with transportation management, are starting to offer more accessibility and personalization options.
In other words, accessibility and personalization allow warehouse managers and staff members to define metrics relevant to new products and current operations, test new processes, and effectively manage the flow of goods. Similarly, new mobile options, ranging from Android tablets to compact barcode scanners, will reduce inconsistencies and errors across the supply chain, explains IRMS 360. Paired with the advancements of predictive analytics and the Industrial Internet of Things (IIoT), more data will result in more efficient processes, creating a positive feedback loop throughout an organization.
5. Contingency Planning Will Become a Standard Practice.
Amazon’s supply chain has proven that not planning will result in the failure of small and medium-sized businesses. Furthermore, natural disasters reap $211 billion from the global supply chain annually. Having a larger global footprint is how Amazon’s supply chain has been able to maintain operations in the face of natural or man-made disasters. This is contingency planning.
The IIoT empowers contingency planning by giving supply chain entities real-time data from an endless number of sources, which range from online browsing data to point-of-sale data. Consequently, supply chains can react appropriately and divert resources to maintain operations. But, the key to utilizing this information lies in knowing what to do and how to do it when an event occurs. In other words, more companies will diversify distribution, supplier and storage networks throughout 2017 to prepare for what might happen in the future.
The Big Picture.
Supply chains must accept that they cannot equal the power of Amazon’s supply chain without embracing these new trends. New technologies are great, but chances are Amazon has already implemented them. Rather than falling into despair, you can use these trends to re-evaluate processes and practices in your organization, which will help you stay competitive with Amazon.
The complexities of the global supply chain rely on your willingness to take advantage of new trends and technologies today, as well as tomorrow, so do not squander this opportunity.
Related posts: