by Fronetics | Aug 29, 2016 | Blog, Content Marketing, Logistics, Manufacturing & Distribution, Marketing, Strategy, Supply Chain, Warehousing & Materials Handling
Fronetics designed a content marketing strategy that helped the logistics software company realize increases in new business and sales revenue.
Your company is doing pretty well. You have a nice website and a social media account or two. And you’ve experienced year-over-year growth. Why would you do anything differently?
Just ask TotalTrax, a provider of real-time vehicle, driver, and inventory tracking technologies for manufacturing and warehouse operations. Despite a decade of positive growth, the company realized there were many untapped opportunities for new business. So the TotalTrax team hired Fronetics Strategic Advisors to create and implement a new, data-driven marketing strategy that could increase web traffic, lead generation, and brand awareness.
After a comprehensive audit of TotalTrax’s digital assets, Fronetics was able to recommend a course of action and implement a multi-channel content marketing program. The program included such steps as:
- Creating a blog and posting regular targeted content
- Consistently posting on TotalTrax’s social media accounts
- Implementing paid search, email marketing, and other strategies
After just 24 months, TotalTrax realized significant gains in web traffic, lead generation and nurturing, and — most importantly — new business and sales revenue.
To learn more about how content marketing helped TotalTrax grow business, download our case study below.

Related posts:
by Elizabeth Hines | Aug 31, 2015 | Blog, Strategy, Supply Chain, Warehousing & Materials Handling
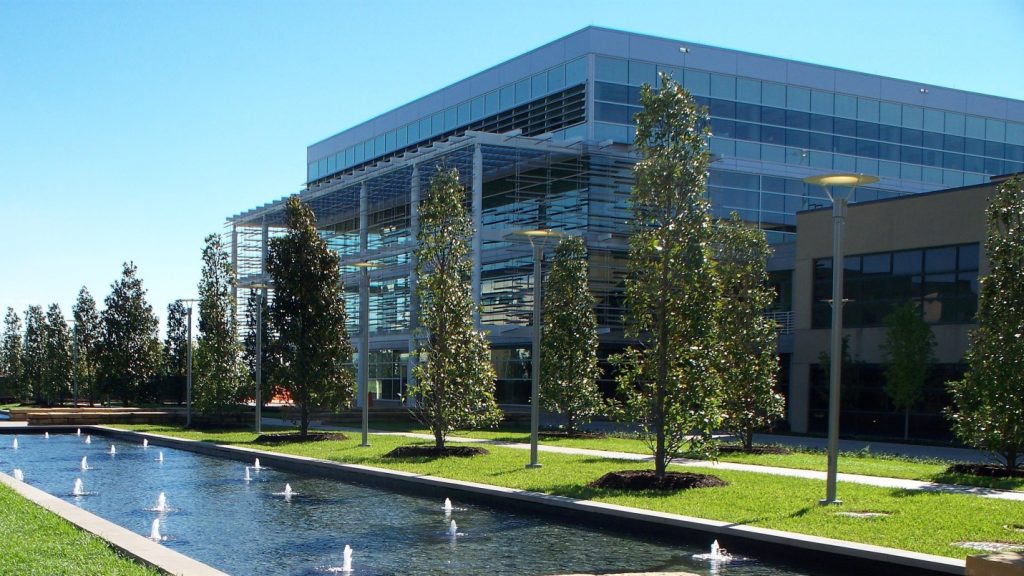
Going green in the warehouse is no longer an afterthought, but a necessity to boost the bottom line. With the US Green Building Council reporting nearly 172,000 gross square meters being certified LEED (Leadership in Energy & Environmental Design) every day in the U.S., it speaks volumes about the widespread industry acceptance of sustainable design.
Once an afterthought, the “greening” of warehouses and distribution centers has emerged as one of the most effective tools to boost the bottom line. With so many external pressures on profit margins, energy savings have the potential to provide that much sought-after way out. Needless to say, we have moved well beyond simply dimming or turning off the lights (although not to be neglected).
If you have not considered such increasingly common green features such as white roofs to reflect sun light, prismatic lenses for skylights, solar panels, and high-efficiency lighting, you should know others are moving ahead.
A one-million square-foot distribution center in Fort Worth, Texas, for example, where temperatures frequently hit triple-digits, hardly needs to turn on the HVAC since the company installed an integrated fan control system, which uses 26 networked warehouse fans 24 feet in diameter. Designed to move high volumes at low speeds to cool indoor temperatures, it operates to the tune of 12% to 50% savings in heating and cooling costs.
Another example is the corporate campus of Somerset Tire Service in Bridgewater, N.J., which is constructed as a net-zero facility, by using a roof-mounted, 1.2 megawatt photovoltaic array. In less than five years, the system will have paid for itself.
And, to cite a third example, consider a recently completed building for Coca-Cola where clear glass brings in an abundance of natural light. In combination with integrated daylight tubes, which automatically reduce or turn off when the sensors determine there is enough ambient light, the facility can frequently operate without any artificial lighting.
Optimizing the building envelope and lighting solutions can yield as much as 40% in energy savings. Lighting is indeed the low-hanging fruit of going green, especially if your lighting system is pushing 20 years. Other common strategies such as dimming, occupancy sensing, and scheduling can be combined with more advanced lighting control strategies such as daylight harvesting (as in the Coca-Cola example), task tuning (light is adjusted depending on the needs of the space), demand response (light is adjusted at peak times based on signals from electric utilities), and specific software for energy management. These strategy combinations can save up to 70% in energy costs.
But let’s not forget that the good-old “location, location, location”. It’s ever-important as well.
One analyst put it this way: “Anytime you can reduce transportation distance, time, and costs for your network, you are also providing a green benefit… While there is much that can be done within a warehouse to save energy, optimizing the network is where some of the biggest bang for the buck can be found.”
When it comes to cutting energy costs in warehouses and distribution centers, where do you see the greatest potential for savings?
Fronetics Strategic Advisors is a leading management consulting firm. Our firm works with companies to identify and execute strategies for growth and value creation.
Whether it is a wholesale food distributor seeking guidance on how to define and execute corporate strategy; a telematics firm needing high quality content on a consistent basis; a real estate firm looking for a marketing partner; or a supply chain firm in need of interim management, our clients rely on Fronetics to help them navigate through critical junctures, meet their toughest challenges, and take advantage of opportunities. We deliver high-impact results.
We advise and work with companies on their most critical issues and opportunities: strategy, marketing, organization, talent acquisition, performance management, and M&A support.
We have deep expertise and a proven track record in a broad range of industries including: supply chain, real estate, software, and logistics.
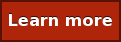
by Jennifer Hart Yim | May 20, 2015 | Blog, Manufacturing & Distribution, Strategy, Supply Chain, Warehousing & Materials Handling
This article is part of a series of articles written by MBA students and graduates from the University of New Hampshire Peter T. Paul College of Business and Economics.
David Chadwick is an MBA student at the University of New Hampshire with a background in retail store management and electrical engineering.
If technology continues to advance, humans may be obsolete in the supply chain as a result of both automation and RFID utilization. Both technologies have been introduced into the supply chain over the past decade, resulting in a major shift in performance and costs. While automation is a process which can navigate product throughout facilities, RFID can improve efficiency dramatically as well as being the major driver for the elimination of human involvement in the supply chain.
RFID (Radio Frequency Identification) is a form of extremely low-power data communication between a RFID scanner and an RFID tag. The tags are placed on any number of items, ranging from individual parts to shipping labels. The RFID tag itself consists of a microchip and antennae, usually without a battery to power it. The tags can be printed using special printers, which wirelessly load the identifying information to the tags. The information on the tags can be used for a wide variety of tasks. When an item goes through the RFID scanners, information is read from the tag, which could include any amount of information, such as:
- Order ID number
- Product bin location
- Order status
- Serial numbers for individual product components
- Location logs
The information is not limited to just holding ID and serial numbers. Since the information can be updated and transferred through any RFID receiver when in range, it can be joined with other software to update databases, send information online, and more. The amount of information that RFID can provide can be matched with order management systems to track shipment and stock locations automatically as the products move through warehouses and trucks. Powerful receivers can also track the exact location of products within a warehouse in real time, instead of relying on time and location logs to determine the location. This has been a major benefit to UPS, who’ve had RFID tracking chips in their warehouses for over ten years.
The largest problem facing supply chain management today is the potential for the occurrence of devastating errors. These errors could lead to trucks leaving product behind, not stocking to capacity, losing product, or delivering to the wrong locations. There are numerous reasons for such errors to occur, but the most common factor in their inception is human error. Much of the errors faced result from manual inspection and control over product flow in warehouses by humans. Many systems still operate using written data tables and checklists, which can be written incorrectly. Despite major advancements in technology over the past decade, the digital world is being sourced by analog supply chains. This is an aspect which RFID control can create beneficial change.
RFID can lead to completely autonomous warehouses and distribution centers. This can be seen in current warehouses with high levels of automation, where picking machines transport bins of product to a central sorting area to be boxed, before returning to their location. Zebra uses this technique to ensure product location accuracy as a means of reducing lost merchandise. Zebra places a great deal of importance on product visibility and transparency as well as accuracy in locations. Implementation of RFID into this system can ensure that both the correct product and the correct quantities of product are collected at both points, thereby eliminating errors seen in traditional analog supply networks. Coupled with the potential for self-driving trucks and the ever expanding internet of things in the cloud, product information can be tracked at all stages of shipment and storage, increasing accuracy, efficiency, and accountability. Where warehouses and receiving departments had to endure a certain amount of shrinkage of products in the past, a fully utilized RFID-enabled supply network can determine exactly where product is at all times, ensuring that theft is discovered immediately and enforced.
While the reduction of human interaction in the supply chain and warehouses in general can be eliminated with enough technology, it is uncertain to what degree this technology will be implemented in all aspects of supply chain management. While there are huge benefits to operating in such a system, the major negatives include high initial costs and restructuring costs associated with implementing this network into existing, analog networks. Humanity may not be completely removed from the supply chain in the future, but this technology, as well as more advanced techniques for automation, will increase the efficiency and reduce the costs required to operate these newer supply chains dramatically while significantly reducing errors and inefficiencies.
by Jennifer Hart Yim | May 20, 2015 | Blog, Manufacturing & Distribution, Strategy, Supply Chain, Warehousing & Materials Handling
This article is part of a series of articles written by MBA students and graduates from the University of New Hampshire Peter T. Paul College of Business and Economics.
David Chadwick is an MBA student at the University of New Hampshire with a background in retail store management and electrical engineering.
If technology continues to advance, humans may be obsolete in the supply chain as a result of both automation and RFID utilization. Both technologies have been introduced into the supply chain over the past decade, resulting in a major shift in performance and costs. While automation is a process which can navigate product throughout facilities, RFID can improve efficiency dramatically as well as being the major driver for the elimination of human involvement in the supply chain.
RFID (Radio Frequency Identification) is a form of extremely low-power data communication between a RFID scanner and an RFID tag. The tags are placed on any number of items, ranging from individual parts to shipping labels. The RFID tag itself consists of a microchip and antennae, usually without a battery to power it. The tags can be printed using special printers, which wirelessly load the identifying information to the tags. The information on the tags can be used for a wide variety of tasks. When an item goes through the RFID scanners, information is read from the tag, which could include any amount of information, such as:
- Order ID number
- Product bin location
- Order status
- Serial numbers for individual product components
- Location logs
The information is not limited to just holding ID and serial numbers. Since the information can be updated and transferred through any RFID receiver when in range, it can be joined with other software to update databases, send information online, and more. The amount of information that RFID can provide can be matched with order management systems to track shipment and stock locations automatically as the products move through warehouses and trucks. Powerful receivers can also track the exact location of products within a warehouse in real time, instead of relying on time and location logs to determine the location. This has been a major benefit to UPS, who’ve had RFID tracking chips in their warehouses for over ten years.
The largest problem facing supply chain management today is the potential for the occurrence of devastating errors. These errors could lead to trucks leaving product behind, not stocking to capacity, losing product, or delivering to the wrong locations. There are numerous reasons for such errors to occur, but the most common factor in their inception is human error. Much of the errors faced result from manual inspection and control over product flow in warehouses by humans. Many systems still operate using written data tables and checklists, which can be written incorrectly. Despite major advancements in technology over the past decade, the digital world is being sourced by analog supply chains. This is an aspect which RFID control can create beneficial change.
RFID can lead to completely autonomous warehouses and distribution centers. This can be seen in current warehouses with high levels of automation, where picking machines transport bins of product to a central sorting area to be boxed, before returning to their location. Zebra uses this technique to ensure product location accuracy as a means of reducing lost merchandise. Zebra places a great deal of importance on product visibility and transparency as well as accuracy in locations. Implementation of RFID into this system can ensure that both the correct product and the correct quantities of product are collected at both points, thereby eliminating errors seen in traditional analog supply networks. Coupled with the potential for self-driving trucks and the ever expanding internet of things in the cloud, product information can be tracked at all stages of shipment and storage, increasing accuracy, efficiency, and accountability. Where warehouses and receiving departments had to endure a certain amount of shrinkage of products in the past, a fully utilized RFID-enabled supply network can determine exactly where product is at all times, ensuring that theft is discovered immediately and enforced.
While the reduction of human interaction in the supply chain and warehouses in general can be eliminated with enough technology, it is uncertain to what degree this technology will be implemented in all aspects of supply chain management. While there are huge benefits to operating in such a system, the major negatives include high initial costs and restructuring costs associated with implementing this network into existing, analog networks. Humanity may not be completely removed from the supply chain in the future, but this technology, as well as more advanced techniques for automation, will increase the efficiency and reduce the costs required to operate these newer supply chains dramatically while significantly reducing errors and inefficiencies.
by Fronetics | Feb 24, 2015 | Blog, Supply Chain, Warehousing & Materials Handling
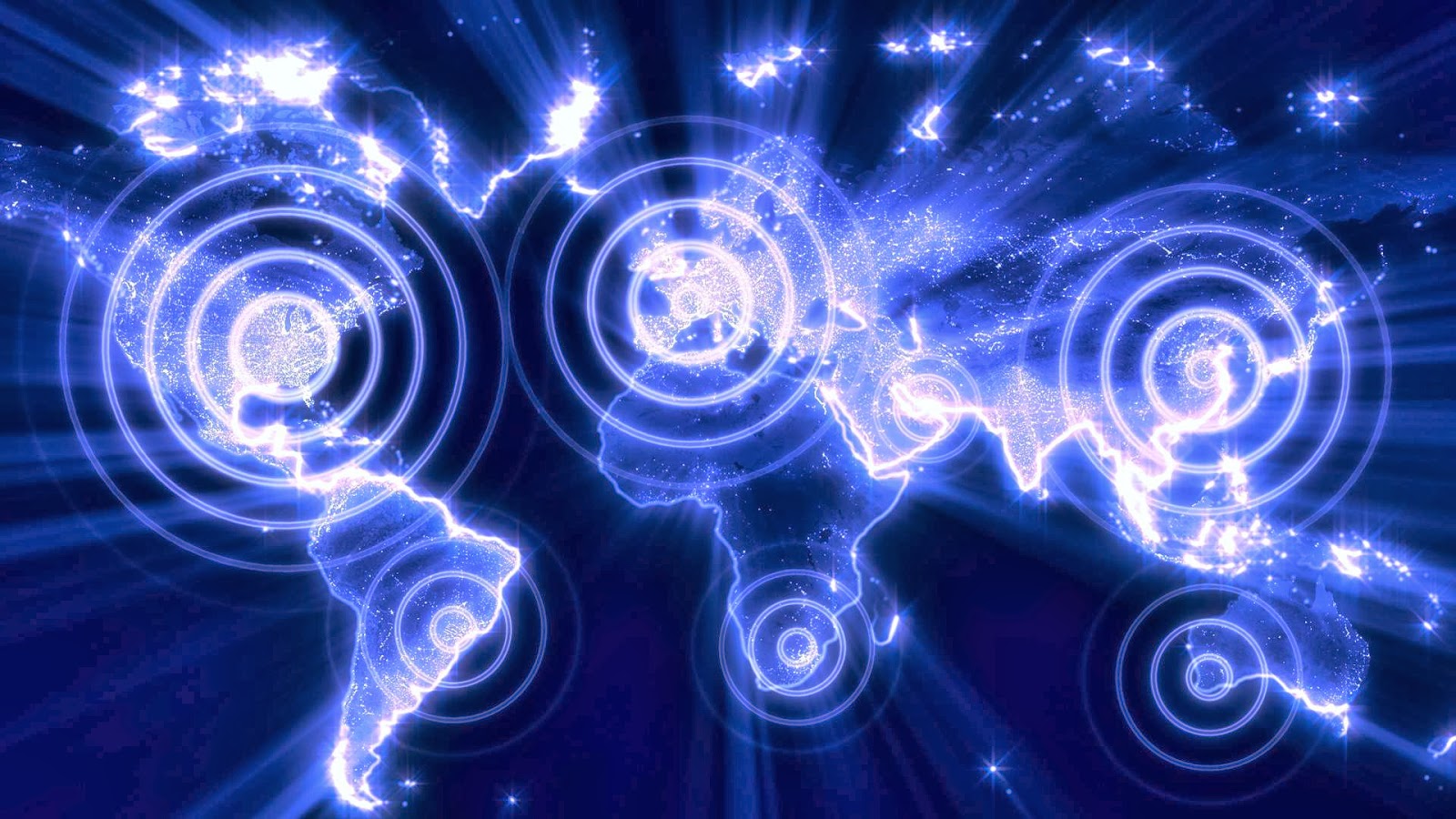
As more warehouses and distribution centers turn to intelligent, high-tech solutions, it is important to take advantage of technology to optimize the efficiency and ultimately increase the revenue of your business.
Smart technology now stretches into virtually every aspect of our lives, so it should come as no surprise that distribution centers worldwide are finding unique ways to leverage these smart technologies to increase efficiencies, reduce operating costs, and improve safety. A closer look at today’s available technology shows just how intelligent the tools for the materials handling, logistics, and supply chain industry have become and the transformative impact they can have on operations. Innovations such as voice tasking, warehouse robotics technology, microprocessors, and the talking lift truck are fundamentally changing the way business is being done. Those who stay on top of these innovations gain an invaluable lead on the competition.
One such company realizing significant benefit from employing new technologies is Genco Supply Chain Solutions. Looking to improve routing and slot optimization while simplifying the receiving and retrieving processes at their 200,000-square-foot facility, Genco started using the Total Trax Sky-Trax Solution. TotalTrax Smart Truck Solutions turns traditional material handling vehicles into smart trucks. Image processing technology transmits images to a centralized monitoring system, giving supervisors real-time access to the warehouse. Genco’s results after implementation: a 12% increase in facility throughput, 99.9% inventory accuracy, a 20% increase equipment utilization, and a reduction of more than 50% in training time.
“With gained visibility to inventory and vehicle movement, we are now able to analyze each operator’s performance, including the amount of idle time and time spent with no load,” Cary Cameron, Genco’s vice president of strategic technologies, said in a press release. “The data and reporting Sky-Trax provides allows us to analyze the root cause [using Lean Six Sigma] and measure processes we’ve never been able to see before.”
Value is delivered in increased accountability and visibility as supervisors can make critical dispatching decisions in real-time and review historical data for improving operations. In numbers, the use of smart trucks for automatic inventory tracking routinely translates into 30% higher productivity. Drivers can focus on what they do best: driving. Customers can also count on substantial labor savings and improved OSHA safety compliance as a result of the uninterrupted monitoring of the warehouse.
As more warehouses and distribution centers turn to intelligent, high-tech solutions, it is important to take advantage of technology to optimize the efficiency and ultimately increase the revenue of your business. Keeping up with this kind of innovation can help any organization achieve better business results. Even more importantly, you should make sure your organization uses its smart system for a breadth of capabilities and applications to ensure getting the most out of it.
Is your business using smart technologies? If so, which ones have had the biggest impact?
by Fronetics | Feb 24, 2015 | Blog, Supply Chain, Warehousing & Materials Handling
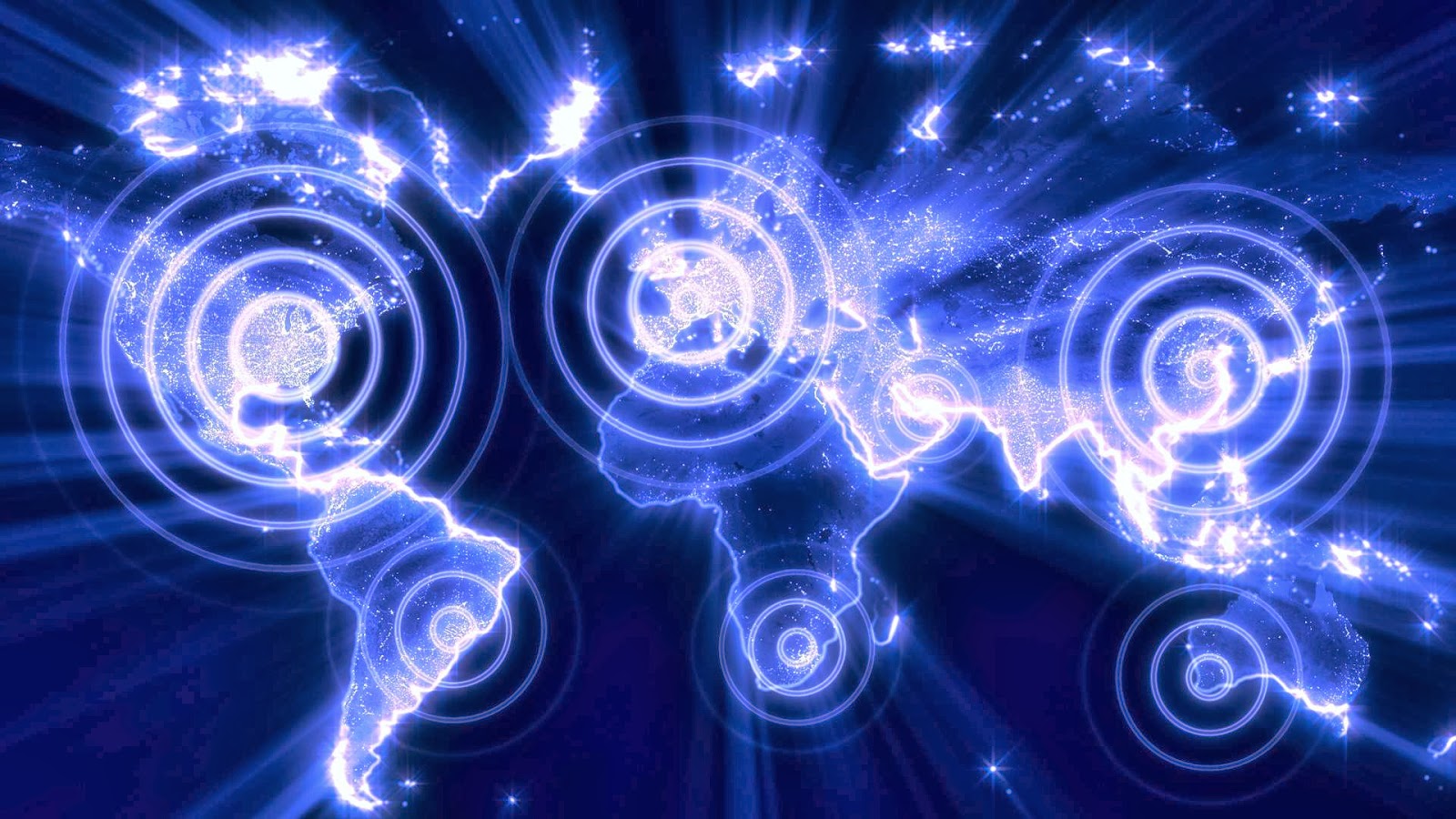
As more warehouses and distribution centers turn to intelligent, high-tech solutions, it is important to take advantage of technology to optimize the efficiency and ultimately increase the revenue of your business.
Smart technology now stretches into virtually every aspect of our lives, so it should come as no surprise that distribution centers worldwide are finding unique ways to leverage these smart technologies to increase efficiencies, reduce operating costs, and improve safety. A closer look at today’s available technology shows just how intelligent the tools for the materials handling, logistics, and supply chain industry have become and the transformative impact they can have on operations. Innovations such as voice tasking, warehouse robotics technology, microprocessors, and the talking lift truck are fundamentally changing the way business is being done. Those who stay on top of these innovations gain an invaluable lead on the competition.
One such company realizing significant benefit from employing new technologies is Genco Supply Chain Solutions. Looking to improve routing and slot optimization while simplifying the receiving and retrieving processes at their 200,000-square-foot facility, Genco started using the Total Trax Sky-Trax Solution. TotalTrax Smart Truck Solutions turns traditional material handling vehicles into smart trucks. Image processing technology transmits images to a centralized monitoring system, giving supervisors real-time access to the warehouse. Genco’s results after implementation: a 12% increase in facility throughput, 99.9% inventory accuracy, a 20% increase equipment utilization, and a reduction of more than 50% in training time.
“With gained visibility to inventory and vehicle movement, we are now able to analyze each operator’s performance, including the amount of idle time and time spent with no load,” Cary Cameron, Genco’s vice president of strategic technologies, said in a press release. “The data and reporting Sky-Trax provides allows us to analyze the root cause [using Lean Six Sigma] and measure processes we’ve never been able to see before.”
Value is delivered in increased accountability and visibility as supervisors can make critical dispatching decisions in real-time and review historical data for improving operations. In numbers, the use of smart trucks for automatic inventory tracking routinely translates into 30% higher productivity. Drivers can focus on what they do best: driving. Customers can also count on substantial labor savings and improved OSHA safety compliance as a result of the uninterrupted monitoring of the warehouse.
As more warehouses and distribution centers turn to intelligent, high-tech solutions, it is important to take advantage of technology to optimize the efficiency and ultimately increase the revenue of your business. Keeping up with this kind of innovation can help any organization achieve better business results. Even more importantly, you should make sure your organization uses its smart system for a breadth of capabilities and applications to ensure getting the most out of it.
Is your business using smart technologies? If so, which ones have had the biggest impact?