by Jennifer Hart Yim | Feb 28, 2019 | Blog, Strategy, Supply Chain, Warehousing & Materials Handling
If you want to keep your customers satisfied, you need to keep things moving in your facility. Use these tips to keep up the pace and increase warehouse and distribution center efficiency.
Highlights:
- Speed has become the name of the game when it comes to staying competitive in the global supply chain.
- Keep your priorities in mind when organizing your warehouse, including your fastest-moving products.
- Digital technology can take the guesswork out of inventory and warehouse management with employees scanning products every step of the way.
This guest post was written by David Maddenfor Argentus Supply Chain Recruiting, a boutique recruitment firm specializing in Supply Chain Management and Procurement.
Things can always be faster when you work in a warehouse or distribution center. Speed has become the name of the game when it comes to staying competitive in the global supply chain. Major players like Amazon and Walmart have distribution centers all over the world, pumping out packages at lightning speed.
If you want to keep your customers satisfied, you need to keep things moving in your warehouse or distribution center. Use these tips to keep up the pace and make your facility as efficient as possible.
1. Keep your warehouse organized
Nothing stymies operational efficiency like a poorly-organized warehouse. Your facility should have a thoroughly thought-out floor plan that your employees can navigate with ease. The space should be organized so that your staff members can access products and packages without getting in each other’s way. Your employees may need to process different orders simultaneously, so they should have plenty of space to avoid stepping on each other’s toes. Today’s warehouses are much larger than they were in the past, creating more space for speed and efficiency.
Items should be clearly labeled on the shelf and organized in a way that makes sense for your facility. You can group packages by their contents, destination or point of origin. This layout should make sense to your employees, so they’ll be able find the items they need without having to look at a spreadsheet.
2. Prioritize fast-moving products
Keep your priorities in mind when organizing your warehouse. Every element of your chosen layout should favor your fastest-moving products. Bestsellers don’t tend to sit on the shelf for very long, so make sure your employees can easily retrieve them at all times. Your employees shouldn’t have to go all the way to the back just to retrieve a product, especially if it’s one of your most popular items. You can help everyone save time by moving these fast-selling products to the front of your warehouse. They should be kept low to the ground and close to the loading dock.
Your entire warehouse layout should focus on moving better-performing products to the front, while keeping the less popular products at the back. Go over your inventory and rate your products based on how often your employees need to retrieve them. This should inform your thinking as you change the layout of your facility.
3. Automate the data collection process
Running a warehouse these days is all about data. Digital technology can take the guesswork out of inventory and warehouse management with employees scanning products every step of the way. Your facility should collect as much data on your products as possible, including where they’re coming from, when they arrive, what condition they are in, where they’re going and when they’re set to leave. You can use this data to keep tabs on the location of your products. At any given moment, you’ll know exactly how many products are being stored at your facility.
But in order to improve efficiency, you need to automate the data collection process as much as possible. Your staff members should automatically retrieve this data as they go about unloading and scanning items that have just arrived at the facility and getting them ready for the last leg of their journey. You can use handheld scanners and radio frequency identification tags to simplify this process. Automating data collection also reduces costly errors like inaccurate data entry.
Warehouse automation technology is already a $1.9 billion industry, and it’s expected to balloon to $22 billion by the year 2021. If you want to stay competitive, it might be time to invest in automation. You’ll have all the information you need at your fingertips without adding any additional steps to your operations.
4. Use inventory management software
As you collect all this data on the shipping containers and products moving in and out of your facility, you can save time by sending that info right to your company’s inventory management software. This technology helps you make sense of all the data in a matter of seconds. You can quickly see how many products are on the shelf, when shipments need to go out and when new shipments are due to arrive. Software programs are synced to your data collection devices, so you won’t have to worry about entering that information twice.
[bctt tweet=”Artificially intelligent software programs can even help you anticipate future outcomes like inventory shortages, delivery delays and other potential problems. ” username=”Fronetics”]
Certain artificially intelligent software programs can even help you anticipate future outcomes like inventory shortages, delivery delays and other potential problems. They keep a log of the history of your facility’s operations to help better predict what’s going to happen in the future.
5. Save time with cross docking
If you have fast-moving products coming through the door, you can save time with what’s known as cross docking. Instead of putting these products back on the shelf only to have your employees retrieve them hours later, direct them to a temporary staging area for scanning and inventory purposes. This temporary staging area should be close to the loading dock. When the products are ready for the next leg of their trip, your employees can quickly retrieve them and get them out the door without having to look for them on the shelf.
6. Increase visibility with better lighting
The key to operational efficiency isn’t always as complicated as it seems. Sometimes all you need is better lighting. Warehouses tend to have tall ceilings, and lighting the space, including all those individual shelves, can be a challenge. If you want to be speed up your warehouse operations, everyone should be able to see clearly as they go about their business. Staff members should be able to read labels and use containers without having to squint. Keeping the lights on also helps your employees stay awake, especially if they’re getting a shipment ready in the middle of the night.
Working towards warehouse efficiency
Making your warehouse more efficient starts with having the right layout in place. Your products should be organized according to their popularity. You should automatically collect data on your products as soon as they enter the facility. And always make sure your employees have enough space and light to do their jobs. Follow these steps and you’ll get orders out the door in record time.
Related posts:
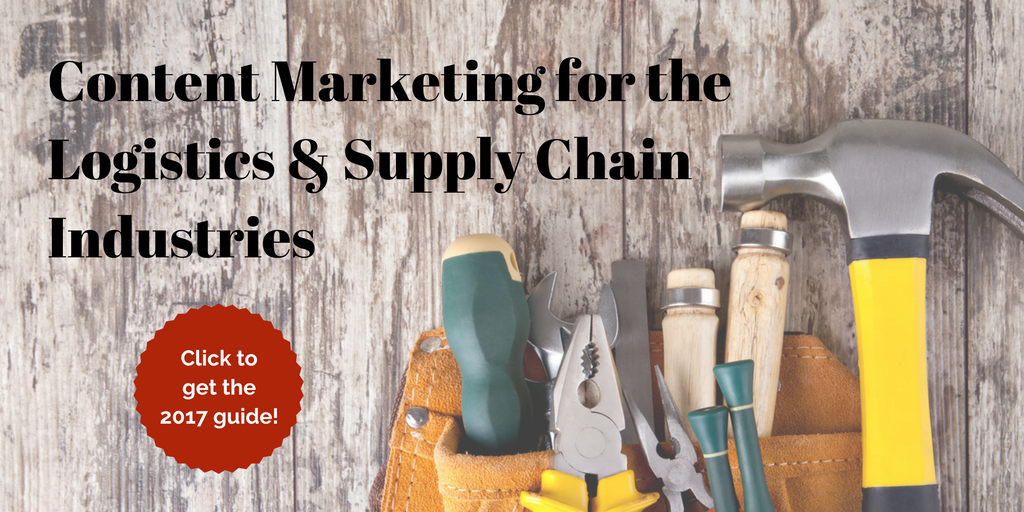
by Jennifer Hart Yim | Nov 15, 2017 | Blog, Supply Chain, Warehousing & Materials Handling
Tracking these logistics metrics can help you identify and tackle issues in your warehouse before they become a problem.
This guest post comes to us from Demetra Mallios at Catch-Up Logistics, a full-service provider of ambient and temperature-controlled food-grade distribution and warehousing services.
The supply chain plays an integral part in maintaining a well-functioning organization. A well-structured and organized warehouse will help you achieve your distribution goals and adequately analyze metrics.
You can think of it like when you are trying to decide what to make for dinner, but cannot remember what food you have in your fridge. If your items are organized and you are aware of what is in your fridge (the warehouse), then you can properly make your dinner decision (packing and preparing for delivery distribution).
While you may be aware of some metrics to track, you might still be missing others. But, that’s where we come in with our list of the top 10 logistics metrics to measure supply chain efficiency in your warehouse.
10 logistics metrics to measure supply chain efficiency in your warehouse
1. On-Time Shipping
A distribution center’s primary objective is clear in its name: It must accurately and efficiently distribute goods that are coming in and out of the warehouse. In other words, the correct product must be placed on the correct transportation method at the appropriate time. In order to complete this task, you must monitor late shipping departures to the warehouse and early completion of freight loading time.
Although it may seem that finishing shipment loads ahead of schedule is a good idea, in reality it could affect the departure and duties of other shipments. So, your business can be sure to monitor these shipment details via a 3PL system. You should also take into account the varying loading and transportation times needed to shift freights before out-bounding product. (Because delaying shipping can be just as bad as receiving the birthday present you ordered for your mom days later, timing matters.)
2. Warehouse Capacity
While there are measures out there to monitor inventory, it is essential that you complete manual observation as well. A distribution center needs to be aware of its ability to increase or decrease its loading times, create more storage space, and accurately track inventory. Currently, many distribution centers incorporate RFID measures to check inventory. However, you should not underestimate the need for manual observation in order to successfully analyze the listed criteria.
3. Accurate Order Fulfillment
Another highly important metric is, of course, the accuracy of the order picking processes. When your employee goes to retrieve a pallet of a specific product, you want to be able to measure how quickly and accurately that task is completed. However, realistically, human error will sometimes occur, which makes the tracking of the picking and moving process vital. A distribution center does not want to be in a situation in which it is unaware of lost, damaged, or misplaced product.
4. Properly Storing Incoming Product
This metric relates to the previous one about order fulfillment, in that it requires a similar tracking process. Accurate inbound storage is essential for accurate outbound deliveries. Without a well-organized inventory in the receiving end, the outbound end will have trouble accurately and efficiently fulfilling orders.
Additionally, the incoming product needs to be recorded correctly, so that inventory capacity can consistently be updated. Furthermore, incoming product and procedures can vary depending on the type of warehouse and storage facility you are operating. For instance, Catch-Up Logistics focuses on food storage. Therefore, it is essential that the product is placed in the correct freezer, cooler, or ambient temperature zone. If this is not done properly, not only will we ruin the product, but we will also lose credibility in our ability to provide high-quality warehousing services.
5. Peaks in Warehouse Capacity
Changes in product demand can, of course, influence the amount of inventory you are willing to hold in your warehouse distribution center. For instance, the holiday season will result in a peak in inventory, as companies need to store more seasonal product. With Catch-Up Logistics, Thanksgiving is a prime example, as our turkey inventory grows and distribution needs to be timely.
6. Total and Individual Cycle Times
In order to be sure that your warehouse is running efficiently, you should be tracking the cycle times. The total cycle time refers to the time needed to properly place the product in inventory from its time of arrival and then ship it from the distribution center. Individually, you can record the dock-to-load time, picking, packing, and preparing the freight for shipping times. This will enable you to see whether or not a certain process is underperforming and can be improved.
7. Damaged Products
You are bound to deal with damaged product at some point while either receiving inventory or moving it. Thus, it is important to record whether or not the product was already damaged upon arrival or if it was due to mishandling in the distribution center. Knowing this data and taking proper action to reduce such mishaps will help improve the efficiency of your warehouse.
8. Employee Turnover Rate
Because working in a distribution center can be exhausting, it is common for employees to search for other job opportunities. However, being able to minimize the turnover with incentives and an improved working environment can benefit the business. It is best to try and maintain employment, instead of consistently searching for new workers and spending the time and resources to train them, only to have them leave in a few months.
9. Accurate Tracking of Trailers
If your warehouse distribution center makes use of trailers for shipping product, it is essential that you are aware of their location at all times. (For instance, Catch-Up Logistics utilizes trailers for shipping.) A great method for tracking this information is through the use of a GPS tracking system.
10. Recording Temperatures
If you have a food storage warehouse facility, it is essential to install a temperature-monitoring system. At Catch-Up Logistics, we monitor the daily temperatures of all the freezers, coolers, and ambient temperature storage spaces to ensure the optimal temperature for proper food storage and health reasons. Additionally, such a system will notify you of any irregular changes in temperature so that you can immediately solve an arising problem before the food product becomes unusable.
There are many aspects to maintaining a well-functioning warehouse distribution system, as demonstrated from the list of metrics above. Although these tracking suggestions may at first appear excessive and time-consuming, they will help you improve the efficiency of your warehouse.
Being aware of potential issues will allow you to tackle the problem before it has a chance to further develop. So, what are you waiting for? If you have not already begun using these metrics, you should consider implementing them as soon as possible!
Related posts:
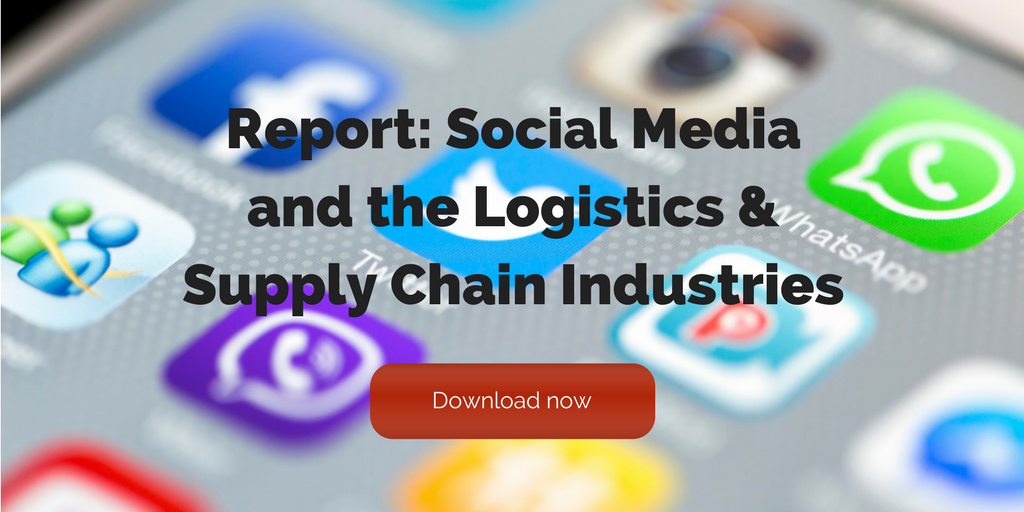
by Jennifer Hart Yim | May 16, 2017 | Blog, Current Events, Manufacturing & Distribution, Supply Chain, Warehousing & Materials Handling
Despite significant technological advancement, drones may have a limited impact on supply chain optimization in the near future.
This article is part of a series of articles written by MBA students and graduates from the University of New Hampshire Peter T. Paul College of Business and Economics.
From the military designs of the early 20th century to modern commercial development in 2017, drones have been making their presence widely known in the market. While military drones may have paved the way for commercial drone development, they have quite different purposes.
Drones provide much value, where traditional alternatives (such as helicopters or planes) fall short. Drone usage in supply chain optimization is still in its infancy. However, I am not convinced that drones are the solution going forward.
Note: For my analysis, I will be focusing on commercial drone usage in the supply chain.
A Timeline of Major Military Drone Development
- 1918: Kettering Bug. First modern drone concept used as a “flying bomb.”
- 1935: DH82B Queen Bee. Used as target practice for anti-aircraft weapon training.
- 1964: Lightning Bug 147SC. Used for surveillance.
- 2001: MQ-9 Reaper. Used as a hunter predator.
Source
Drones provide many advantages, such as mobility, cost effectiveness, ability to move goods, and camera technology. Although drone development is rapidly advancing, many challenges currently exist. Limited battery life, constrained operational range, collision liability, proneness to hacking, and even invasion of privacy are all legitimate challenges.
Commercial Drone Fast Facts
- Made of light composite materials.
- Typically have two to five rotors.
- Controlled by either remote control or GPS.
- Flight time ranges, but generally falls between 12-27 minutes.
- Battery powered.
- Operational range varies from 200 meters to 7 kilometers.
Current Drone Usage in the Supply Chain
Large retailers such as Walmart and Amazon are already investing significant capital in drone technology. On December 6, 2016, Amazon successfully completed its first beta trial of drone package delivery, called Prime Air, in Cambridge, U.K.
Here’s how it works:
- Customers place their orders online as usual.
- The package is prepped at the regional fulfillment center.
- Drones are then dispatched from the center with the package.
- Customers place QR codes on their property to indicate the drop-off point.
- The package is delivered at the customer’s address within 30 minutes.
- The drone is operated by GPS and handles up to five pounds of cargo.
To reinforce this effort, Amazon is currently expanding Prime Air in other parts of the U.K., France, Germany, and Italy. In addition, the company is seeking up to 1,300 small warehouse locations across Europe, with a prioritization for facilities near urban areas.
Walmart, on the other hand, is taking a different approach to managing their supply chain. Instead of focusing on package delivery, Walmart is testing the use of drones to monitor inventory in their warehouses.
Employees currently catalog merchandise with hand-held scanning devices and often need to use forklifts in the warehouse. Instead, the drone could move up and down the shelves cataloging inventory at a much quicker rate. Walmart claims that the drones “could help catalog in as little as a day what now takes employees about a month.” This program is expected to begin in at least one distribution center in 2017.
What about Legal Issues?
In the United States, commercial drone usage is still pretty limited. Below is a highlight of Federal Aviation Administration (FAA) commercial drone regulations.
- Must have a Remote Pilot (no GPS allowed).
- Must be less than 55 lbs.
- Must undergo pre-flight check.
- Must keep aircraft in sight.*
- Must fly under 400 feet.*
- Must fly during the day.*
- Must not fly over people.*
- Must not fly from a moving vehicle.*
*Indicates that these regulations can be waived.
Supply chain drone usage in the United States is currently limited due to these regulations. In the future, I expect many of these regulations to ease or change outright with advancements in drone technology. When this will occur is unknown.
However, other countries such as the United Kingdom are quicker to enact regulations by virtue of the Civil Aviation Authority (CAA). As a result, companies like Amazon have already been testing drones for supply chain optimization there.
Significant Hurdles
Although drone technology is gaining much media attention, there are legitimate challenges to drone commercialization in the supply chain.
While many legislative bodies attempt to develop drone regulations, concrete legislation is lacking in many countries due to fluid technological changes. In order for the market to fully develop, a legislative framework needs to be established. Companies will be reluctant to invest significantly in drone technology until legal parameters are established.
Another challenge is in regard to insurance and liability. With potentially thousands of (unmanned) drones flying only hundreds feet above the ground, insurance will surely be required. In the event of a drone collision with individuals, property, aircraft, or other drones, who then is liable? If the drone is piloted by a human, would he/she be liable? On the other hand, if the drone is GPS-enabled, would the technology be to blame? Surely some of these questions will be answered in contracts between insurance companies and suppliers, but with such uncertainty, premiums will undoubtedly be high.
Then there’s the question of rural vs. urban delivery. Amazon Prime Air is predominately testing drone delivery in rural areas. However, 80.7% of U.S. and 90.1% of the U.K. population live in urban areas.
Package deliveries in urban areas are via mailbox, left by the door, or hidden (to avoid theft). In other words, human judgement is used to deliver the package most appropriately. For customers in large apartment buildings, drone delivery is very limited. Perhaps these limitations could be offset with designated landing areas on rooftops, despite the fact that additional effort by the customer may be needed to retrieve the package.
Last, but certainly not least, is the impact of weather conditions. Wind, rain, snow, and extreme cold/heat all impact drone performance. Since current drones are not very heavy, any significant wind will 1) blow the drone around making it harder to control, and 2) use additional battery life to remain stable. Since drones incorporate many electronic components, rain and snow increase the chance of malfunction.
Furthermore, most drones utilize Lithium Polymer batteries — these batteries are prone to weaker performance in extreme cold and heat. According to Batteryuniversity.com, most Li-ion batteries stop functioning below -4°F. Additionally, battery performance is reduced 40% at 104°F and 50% at 113°F. The combination of all these weather conditions certainly provides logistical challenges for drone delivery and supply chain usage.
Is There Any Hope for Drones in the Supply Chain?
The short answer is yes, but in a limited manner.
With the logistical and technological challenges regarding drone delivery, I just can’t see e-commerce firms effectively managing the process outside of rural areas with optimal weather conditions. In the future, this could change, but it would require significant legal, technological, and customer adjustment for the process to be superior over the current state.
However, drones open other opportunities for supply chain optimization, such as warehouse inventory management (as with Walmart), infrastructure monitoring, surveying, or even security. For example, shipping firms such as FedEx or UPS could utilize drones to monitor traffic and optimize drivers’ routes based on real-time data. Additionally, energy companies could use drones — as opposed to helicopters or planes — to monitor pipelines. Finally, engineers could use drones to inspect dams, highways, and buildings more efficiently.
I have no doubt that the drone market will continue to expand. According to Visualcapitalist.com, by 2025, the U.S. economy is expected to see an increase of $82 billion and creation of at least 100,000 jobs. However, their impact to supply chain optimization remains vague to me.
About the Author
Matt Steckowych graduated from the University of New Hampshire in 2011, with a B.S. in Business Administration and is currently enrolled in the part-time M.B.A. program. He is a Salesforce.com Administrator at John Hancock in Portsmouth, NH.
Related posts:
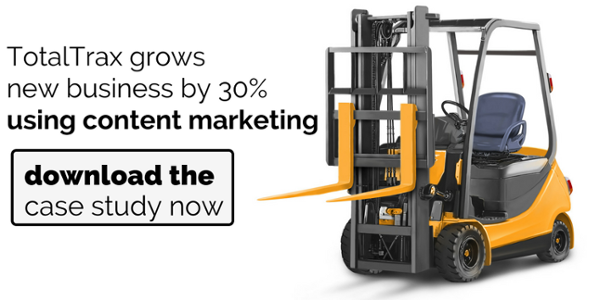
by Jennifer Hart Yim | May 11, 2017 | Blog, Current Events, Logistics, Manufacturing & Distribution, Supply Chain, Transportation & Trucking, Warehousing & Materials Handling
This post comes to us from Adam Robinson of Cerasis, a top freight logistics company and truckload freight broker.
Imagine a world where automation comes together with technology to deliver products without human intervention. An order is placed by a consumer. 3-D printers pick up the details and print the finished product. It’s then picked by robots from the shelves, packaged and placed into a self-driving truck. The trucks leave the facility, and drones are automatically dispatched from the truck to deliver products while moving. The truck never stops until arriving for reloading.
This example generates a huge amount of data that can leverage in the supply chain. But, the same data can have a drastic impact on transportation planners and agencies around the globe. While this example may still be a few years off, it is important that you understand how the top emerging trends in automation will shape supply chains and transportation processes in the coming years.
The Standard Definition & Components of Automation
Today: There is a standard definition of automation in the supply chain. Anything that can be handled via today’s computer systems can be automated. This includes billing, generation of bills of lading, compliance reports, and even movements throughout a factory or warehouse floor.
Historically, automation has been applied to virtual processes, like order auditing or customer service reports. However, the trends in automation are changing to reflect actions that function more like artificial intelligence, not just a search and locate program on the computer.
Additive Manufacturing
What is it?
Additive manufacturing includes all actions in the supply chain that can enhance existing factory production, if not replace it entirely. Additive manufacturing may be handled manually, but automating this process is as simple as turning on the power and connecting to the Internet of Things (IoT).
For example, additive manufacturing might involve the use of 3-D printers to create replacement parts at the store for consumers.
Today’s status: Unfortunately, the capacity of 3-D printers remains in infancy, capable of only producing simplified parts out of liquid polymers.
Virtual Reality Comes to the Forefront.
Meanwhile, Google Glass and other virtual reality tech are changing how customers complete their orders. In addition, the same technology can be overlaid with augmented reality to give repair technicians and individuals greater resource access when making repairs, checking order contents and fulfilling orders.
For example, augmented reality glasses will soon detect package dimensions and classify the package according to dimensional pricing models.
Today’s Status: Today, this technology is limited to automated identification and data capture (AIDC) applications. Advancements in virtual reality over the past year indicate its future might be much closer than “meets the eye.”
Additive manufacturing will gradually move products from warehouses and distribution centers to be closer to end-users. As a result, the amount of last-mile traffic may increase.
Robotics Enhance Inbound and Outbound Logistics for Shippers.
Another trend in automation involves robotics. By definition, robotics are the icons of automation. They perform functions at the request of a system or person, but more of today’s robotic systems are performing duties upon request from an order fulfillment system.
The order process automatically notifies robots in warehouses and triggers the flow of processes as seen in the opening example.
Robotics Improve Inbound and Outbound Logistics.
Robotics are not isolated to warehouse pulling for outbound logistics. They can be used to manage inbound and outbound processes and strategy. Through trends in automation and robotics, supply chain companies will have the tools and resources necessary to ramp up throughput and decrease product cycle from order to delivery. Therefore, more trucks and drivers will be needed, but the looming driver shortage and capacity crunch will trigger another automation trend.
Autonomous Vehicles/ Trucks
Automation begets automation. With advances in technology and the IoT, most major companies, including Uber, Facebook, Google, and Amazon, have launched autonomous vehicle and truck pilot programs.
These driverless vehicle programs will give supply chains access to a new inexhaustible resource for moving products, overcoming the challenges inherent in the driver shortage and capacity crunch.
The driver shortage and capacity crunch are likely to come to a head in 2017, as consumers demand more product, at lower costs and faster than ever before.
Some setbacks have occurred, like the first self-driving car wreck earlier this year. With each setback and challenge, companies have pushed back to overcome the obstacles.
In response to increased interest in driverless vehicles and trucks, the National Transportation Safety Board (NTSB) has issued recommendations and created an advisory panel to review ongoing driverless vehicle advancements and maintain public safety.
Transporters and supply chains will respond to this direction by leveraging the trends in automation and power of data to ensure compliance with increased government oversight, through the agencies you represent.
Companies have already tested cross-country driverless trucks, albeit with a person ready in the cab to take over in the event of a system failure. However, the wide-scale deployment of this level of driverless trucks is far from implementation.
In the interim, more automated vehicle systems will work in tandem with drivers to enhance safety and maintain vehicle control. Similar systems are already deployed in crash and pedestrian detection systems, automated braking and tracking control in today’s vehicles. It is not difficult to apply today’s technology and automated features to the fleets and drivers of 2017.
Trends in Automation: Whats the Potential?
The potential applications of this type of technology can include real-time traffic condition monitoring and warnings, redirecting traffic before pile-ups and accidents occur, similar to Google Maps’ capacity to show traffic congestion in real-time.
Data through such systems can automatically feed back into transportation planners’ systems to automatically change signal phase and timing and enable immediate rerouting or adjustment of traffic flow on a broader scale.
Related posts:
by Fronetics | Mar 23, 2017 | Big Data, Blog, Current Events, Data/Analytics, Internet of Things, Logistics, Manufacturing & Distribution, Strategy, Supply Chain, Talent, Warehousing & Materials Handling
Our series by MBA students and graduates at Peter T. Paul College of Business and Economics highlights some of the most pressing issues in supply chain management today.
A few years ago, the Wall Street Journal called supply chain management the “hot new MBA.” Many universities have been introducing related degree programs, majors, and concentrations in response to a growing demand for new hires with supply chain expertise. Graduates of these programs are heavily recruited by employers, which is helping to attract ambitious, young talent to the industry.
Fronetics had the opportunity to collaborate with some of these rising stars by inviting MBA students from the University of New Hampshire Peter T. Paul College of Business and Economics to author guest posts on our blog. They covered a variety of pertinent topics, from the Internet of Things and Big Data to pet food and Chipotle. Their pieces are summarized below.
In the coming weeks, we’ll be partnering with another MBA class at UNH to author a second series of posts covering some of the most pressing issues in supply chain management today. Make sure you receive our blog e-newsletter (sign up to the right) or follow us on social media so that you don’t miss out.
Steve Mondazzi writes about how the Internet of Things is now being used to improve factory workflow, increase material tracking, and optimize distribution to maximize revenues. Everything from turning lights on and off to security systems can be controlled from your smartphone, and that technology is moving to the manufacturing industry. Mondazzi examines Mark Morely’s theory that the IoT will impact the industry in three main ways: pervasive visibility, proactive replenishment, and predictive maintenance. He also explores hurdles to implementation — such middleware and a common protocol for businesses regarding IoT. Read article
Mikayla Cadoret focuses on the barriers to entry in the pet food industry. New brands have three options: manufacture product themselves, choose a co-packer who uses a private label, or choose a co-packer who will manufacture the food to the specifications of the brand. She discusses the challenges of those choices as well as high-profiles recalls resulting from co-packer error. She recommends strategies that companies implement to keep tabs on co-packers’ sourcing and manufacturing. Read article
Nicole Brooks explores Amazon’s mission to be earth’s most consumer-centric company. The e-commerce giant not only offers low prices, it also exceeds consumer expectations and shifts industry standards with benefits like same-day shipping. Brooks examines Amazon’s biggest technological assets, and looks forward to up-and-coming innovations like Kiva robots in warehouses, drones, Prime Air, and Amazon Business. Read article
Corey Ducharme discusses the traditional four-step problem-solving method and how it isn’t effective in solving needle-in-a-haystack issues resulting from limited business resources. Six sigma can address these issue with its six-step process. With the addition of an analysis phase, solutions become more effective, leading to better results and higher revenue for businesses. Read article
David Chadwick explores whether advances in radio-frequency-identification technology (RFID) will render humans obsolete in the supply chain. RFID could dramatically improve efficiency and accuracy in warehouses by reducing the need for human interaction. But it is uncertain to what degree this technology will be implemented in all aspects of supply chain management. Read article
Dario Cavegn discusses how increasing size and complexity of global supply chains open them up to increased risk. Supply chain disruptions can vary from insignificant to extremely threatening. But regardless of disruption size, supply chains can remain resilient with a business continuity plan, which acts as a road map to continue operations during or after a disruption. Cavegn outlines the development process from analysis to feedback. Read article
Josh Hutchins explores the limitations of big data. The real value lies in the analytics applied to the data. As an example, Solid Gold Bomb drove its prospering t-shirt business into the ground from an oversight and misapplication of data. Hutchins concludes that companies must have an intimate understanding of big data applications to avoid a similar fate. Read article
Michael Hickey discusses third-party logistics providers as a resource for a company’s operations arm. 3PLs offer an outsourcing opportunity for order fulfillment, inventory and warehouse management, as well as transportation of finished goods. But businesses should ask themselves these questions when determining whether a 3PL is a good fit for their needs. Read article
Sarah Hebert discusses Chipotle’s high-profile pork-supplier conundrum. The chain cut their pork supply by a third due to a supplier’s violation of their animal welfare standards. While this affected sales by 7-8%, Chipotle embraced the situation as a strategic PR opportunity. But behind the scenes, the company was scrambling to address long-term supply concerns associated with its rapid growth. Hebert asks, “At what point do you scale back the growth for the sake of maintaining brand integrity?” Read article
Connor Harrison discusses GM’s recall of 2.6 million vehicles. The company’s faulty ignition switches were linked to 13 deaths and 31 front-end collisions, but the company managed to contain the crisis. Harrison examines the root causes of the issue, including faulty ignition switches from GM’s supplier Delphi, a strained business relationship, and legal complications. Read article
Related posts:
by Elizabeth Hines | Jan 18, 2017 | Blog, Logistics, Strategy, Supply Chain, Warehousing & Materials Handling
Having a modern, flexible supply chain is important to finding the way out of inventory dilemmas.
Imagine your irritation when you try to place an order online and are greeted by the message: “We apologize for the inconvenience, but this item is out of stock.”
However, even if the item is in stock, your mood is likely to sour if delivery will take more than a few days — and, even worse, you also have to pay for shipping. If you’re anything like me, you will quickly find an equivalent product that’s available immediately and ready to be shipped that same day.
It’s in the light of this hyper-competitive environment that the current inventory crisis should be seen. To sum it up from the perspective of warehouse owners: these are good times. Warehouse rents are hitting new highs as vacancy rates sit below five percent in many major cities.
From the viewpoint of retailers, on the other hand, it’s a significant challenge. Excess inventory is building even as consumer demand remains relatively high. Well aware of the consequences of not meeting ever-rising consumer expectations, retailers have felt compelled to stock up to — at all costs — avoid that irritating “out-of-stock” disclaimer. On the other hand, a chock-full warehouse is not necessarily good for business or speedy fulfillment.
Modernity and flexibility are key
This is when the importance of having a modern, flexible supply chain really comes into play:
- How quickly can the supply chain adjust to changes in demand?
- What’s the visibility up and down the supply chain?
- How aware is each link of what others are doing?
- How fast can inventory be refocused?
Some companies like Nordstrom have invested in cloud-based supply chain services. In Nordstrom’s case, the acquisition of a minority stake in DS Co., a supply chain software firm, which links inventory management between retailers and suppliers, was designed to facilitate direct shipments from vendors to customers, thereby circumventing the need for more inventory space. When suppliers and retailers track the inventory of one another, the risk of out-of-stock disappointments is reduced and risk is shifted up the supply chain.
Put to practice, it means that an order placed on the luxury retailer’s website is routed to the manufacturer, which then ships the item directly from its warehouse to the buyer. The Wall Street Journal noted Nordstrom’s investment comes “as retailers are racing to compete with e-commerce companies such as Amazon.com Inc. to provide convenience and speedy delivery to customers while keeping costs down.”
J.C. Penney is also shifting gears to avoid inventory gluts. The new business model essentially turns part of the store into a showroom for one of its suppliers, Ashley Furniture. Instead of keeping inventory in store or in distribution centers, all orders will be shipped straight to the consumer from Ashley Furniture.
Drones are not surprisingly part of solving the inventory dilemma. Walmart, for example, is testing the use of drones to catalog inventory, finishing in one day what it takes employees a whole month to get done. The intent is partly to make the giant retailer’s supply chain more efficient.
Clearly, traditional retailers are exploring new territory to meet consumer demand.
What do you think is key to solving the inventory crisis?
This post originally appeared at EBN Online.
Related posts: