by Fronetics | Nov 28, 2017 | Blog, Manufacturing & Distribution, Marketing, Social Media, Supply Chain
Manufacturers who are active and engaged on Facebook are more likely to introduce product innovation than those who are not.
If you’re killing time during business hours on Facebook, you may actually be onto something valuable. Well, no, — scrolling through your sister-in-law’s vacation album is unlikely to help your business. But recent studies show that staying attuned to user feedback on Facebook may actually help manufacturers create better products.
The practice in question, social listening, is the process of monitoring social media to identify and assess what users are saying about a company, individual, brand, product, or service. We’ve written about how social listening can help your business — you can gain market intelligence and learn how your company, products, and services are being perceived.
But two researchers from the Centre for European Economic Research (ZEW) have taken things a step farther. They studied data from nearly 3,000 German manufacturing and service firms to analyze the role that Facebook plays in the innovation process. What they found was that the probability that a company introduced a product innovation was significantly determined by firms’ adoption of a Facebook page and by the activity by users, measured by both quantity and quality.
The researchers, Irene Bertschek and Reinhold Kesler, discuss their findings in detail in this article published in the Harvard Business Review. So you can skip to the bottom line, we’ve pulled out a few key takeaways for manufacturers:
Negative comments are your friend…
…if you take them seriously.
While you might cringe when you seed a negative customer comment on Facebook, what the researchers found was encouraging: “Surprisingly, only the share of negative user comments was significantly predictive of innovation, perhaps suggesting that customers were helping to steer companies away from bad ideas.”
To make this work for you, it’s important that you pay attention to negative reviews, actively engage with them, and pass along relevant information to the people within your company who can address the issues. For more ideas, check out this post for tips on dealing with negative customer comments.
Simply being on social media isn’t enough — you need to be actively and intelligently engaging.
The study found that companies who were “using keywords in their posts that encourage users to leave feedback were significantly more likely to release a new or improved product.”
In other words, to gain the kind of valuable feedback that allows your products and services to improve, you need to be intelligent about soliciting it. “When developing social media strategies,” suggest Bertschek and Kesler, “companies should not only focus on marketing aspects, but also consider the potential for the firm’s innovation success.”
Related posts:
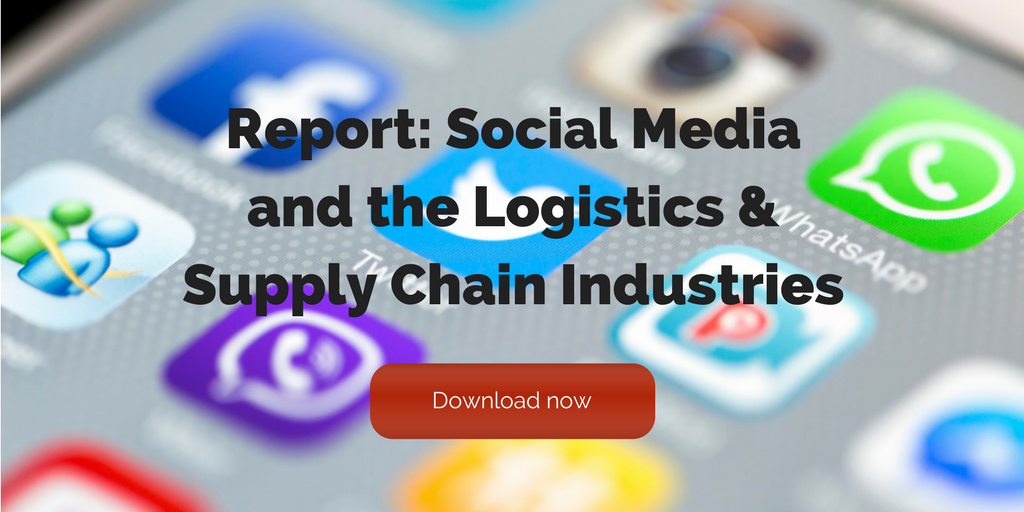
by Fronetics | Nov 16, 2017 | Blog, Current Events, Supply Chain
With the 2017 holidays right around the corner, consumers are digging into their pockets and getting ready to increase sales, especially online.
The National Retail Federation is estimating that holiday sales will be up 3.6-4% from last year, totaling $678.5 billion in holiday spending. What’s more, consumers will be hitting the malls earlier than ever. More and more retailors are forgoing the traditional Thanksgiving dinner to open their stores during the holiday. Major retailers, including Target, Kohls, and Toys “R” Us, will open their doors at 5 p.m. on Thanksgiving Day.
“[Thanksgiving] was a strong weekend for retailers, but an even better weekend for consumers, who took advantage of some really incredible deals. In fact, over one third of shoppers said 100% of their purchases were on sale,” said NRF President and CEO Matthew Shay in 2016.
The NRF is estimating that the average consumer will spend $967.13 during the holiday season, almost $300 of which will be spent during Thanksgiving weekend.
Holiday spending can be broken up into three major categories:
- Gifts
- Items such as food, decorations, flowers and greeting cards
- Other non-gift items consumers buy for themselves and their families
For the first time in NRF’s survey history, online shopping has become the most popular shopping destination. In fact, 59% of consumers will head to their computers for holiday spending, where most will benefit from free shipping (94%).
“While many consumers are holding off until November or later to start their holiday shopping, retailers should be prepared for high traffic online and in stores come Thanksgiving weekend,” Prosper Insights Principal Analyst Pam Goodfellow says. “Although sales will remain an important factor for most consumers, many will lean on convenient locations and easy-to-use websites or mobile apps along with free shipping to complete their purchases.”
2017 holidays supply chain infographic
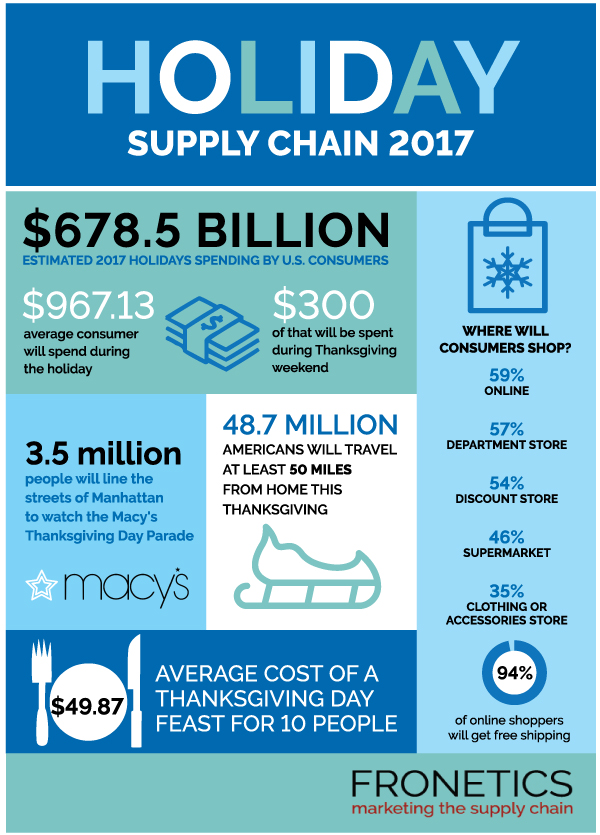
(Made with Canva)
From all of us at Fronetics, have a wonderful Thanksgiving!
Related posts:
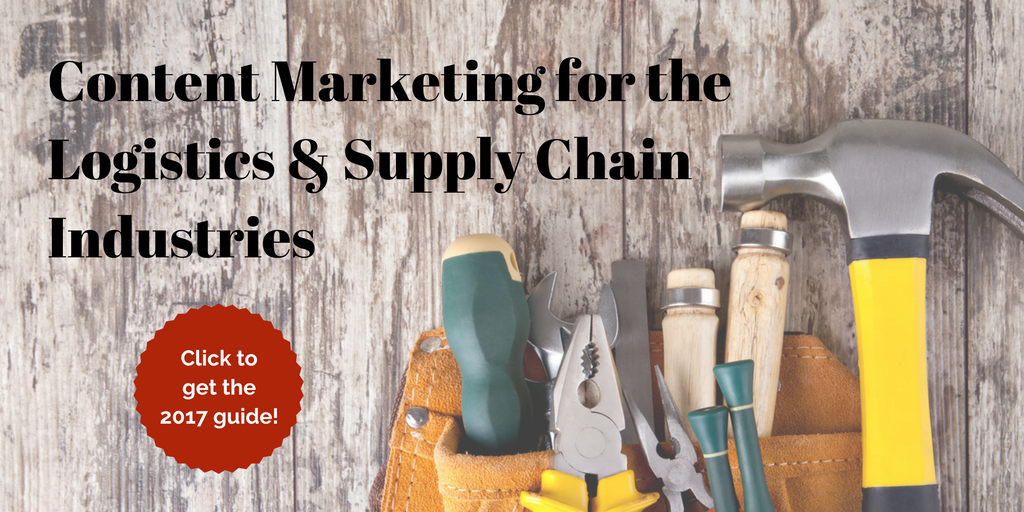
by Jennifer Hart Yim | Nov 15, 2017 | Blog, Supply Chain, Warehousing & Materials Handling
Tracking these logistics metrics can help you identify and tackle issues in your warehouse before they become a problem.
This guest post comes to us from Demetra Mallios at Catch-Up Logistics, a full-service provider of ambient and temperature-controlled food-grade distribution and warehousing services.
The supply chain plays an integral part in maintaining a well-functioning organization. A well-structured and organized warehouse will help you achieve your distribution goals and adequately analyze metrics.
You can think of it like when you are trying to decide what to make for dinner, but cannot remember what food you have in your fridge. If your items are organized and you are aware of what is in your fridge (the warehouse), then you can properly make your dinner decision (packing and preparing for delivery distribution).
While you may be aware of some metrics to track, you might still be missing others. But, that’s where we come in with our list of the top 10 logistics metrics to measure supply chain efficiency in your warehouse.
10 logistics metrics to measure supply chain efficiency in your warehouse
1. On-Time Shipping
A distribution center’s primary objective is clear in its name: It must accurately and efficiently distribute goods that are coming in and out of the warehouse. In other words, the correct product must be placed on the correct transportation method at the appropriate time. In order to complete this task, you must monitor late shipping departures to the warehouse and early completion of freight loading time.
Although it may seem that finishing shipment loads ahead of schedule is a good idea, in reality it could affect the departure and duties of other shipments. So, your business can be sure to monitor these shipment details via a 3PL system. You should also take into account the varying loading and transportation times needed to shift freights before out-bounding product. (Because delaying shipping can be just as bad as receiving the birthday present you ordered for your mom days later, timing matters.)
2. Warehouse Capacity
While there are measures out there to monitor inventory, it is essential that you complete manual observation as well. A distribution center needs to be aware of its ability to increase or decrease its loading times, create more storage space, and accurately track inventory. Currently, many distribution centers incorporate RFID measures to check inventory. However, you should not underestimate the need for manual observation in order to successfully analyze the listed criteria.
3. Accurate Order Fulfillment
Another highly important metric is, of course, the accuracy of the order picking processes. When your employee goes to retrieve a pallet of a specific product, you want to be able to measure how quickly and accurately that task is completed. However, realistically, human error will sometimes occur, which makes the tracking of the picking and moving process vital. A distribution center does not want to be in a situation in which it is unaware of lost, damaged, or misplaced product.
4. Properly Storing Incoming Product
This metric relates to the previous one about order fulfillment, in that it requires a similar tracking process. Accurate inbound storage is essential for accurate outbound deliveries. Without a well-organized inventory in the receiving end, the outbound end will have trouble accurately and efficiently fulfilling orders.
Additionally, the incoming product needs to be recorded correctly, so that inventory capacity can consistently be updated. Furthermore, incoming product and procedures can vary depending on the type of warehouse and storage facility you are operating. For instance, Catch-Up Logistics focuses on food storage. Therefore, it is essential that the product is placed in the correct freezer, cooler, or ambient temperature zone. If this is not done properly, not only will we ruin the product, but we will also lose credibility in our ability to provide high-quality warehousing services.
5. Peaks in Warehouse Capacity
Changes in product demand can, of course, influence the amount of inventory you are willing to hold in your warehouse distribution center. For instance, the holiday season will result in a peak in inventory, as companies need to store more seasonal product. With Catch-Up Logistics, Thanksgiving is a prime example, as our turkey inventory grows and distribution needs to be timely.
6. Total and Individual Cycle Times
In order to be sure that your warehouse is running efficiently, you should be tracking the cycle times. The total cycle time refers to the time needed to properly place the product in inventory from its time of arrival and then ship it from the distribution center. Individually, you can record the dock-to-load time, picking, packing, and preparing the freight for shipping times. This will enable you to see whether or not a certain process is underperforming and can be improved.
7. Damaged Products
You are bound to deal with damaged product at some point while either receiving inventory or moving it. Thus, it is important to record whether or not the product was already damaged upon arrival or if it was due to mishandling in the distribution center. Knowing this data and taking proper action to reduce such mishaps will help improve the efficiency of your warehouse.
8. Employee Turnover Rate
Because working in a distribution center can be exhausting, it is common for employees to search for other job opportunities. However, being able to minimize the turnover with incentives and an improved working environment can benefit the business. It is best to try and maintain employment, instead of consistently searching for new workers and spending the time and resources to train them, only to have them leave in a few months.
9. Accurate Tracking of Trailers
If your warehouse distribution center makes use of trailers for shipping product, it is essential that you are aware of their location at all times. (For instance, Catch-Up Logistics utilizes trailers for shipping.) A great method for tracking this information is through the use of a GPS tracking system.
10. Recording Temperatures
If you have a food storage warehouse facility, it is essential to install a temperature-monitoring system. At Catch-Up Logistics, we monitor the daily temperatures of all the freezers, coolers, and ambient temperature storage spaces to ensure the optimal temperature for proper food storage and health reasons. Additionally, such a system will notify you of any irregular changes in temperature so that you can immediately solve an arising problem before the food product becomes unusable.
There are many aspects to maintaining a well-functioning warehouse distribution system, as demonstrated from the list of metrics above. Although these tracking suggestions may at first appear excessive and time-consuming, they will help you improve the efficiency of your warehouse.
Being aware of potential issues will allow you to tackle the problem before it has a chance to further develop. So, what are you waiting for? If you have not already begun using these metrics, you should consider implementing them as soon as possible!
Related posts:
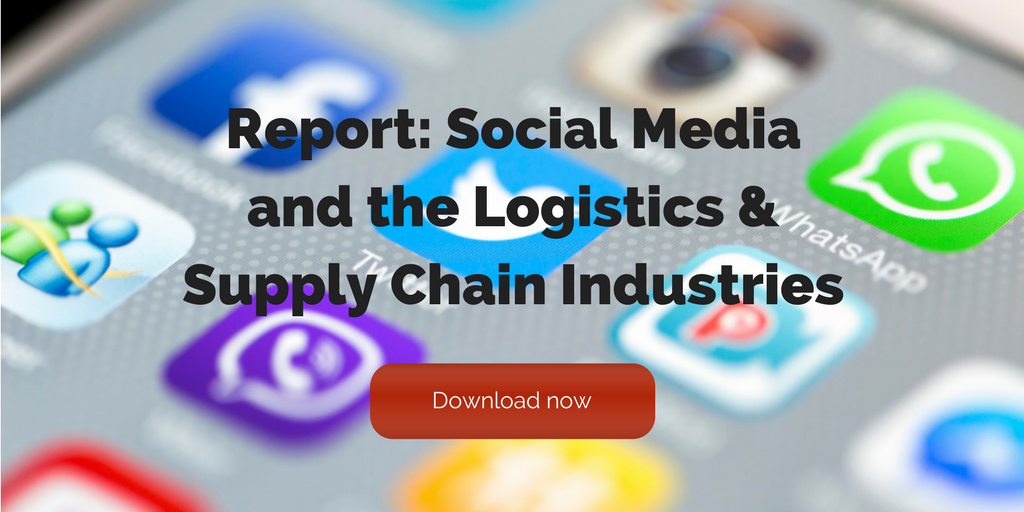
by Jennifer Hart Yim | Nov 14, 2017 | Blog, Current Events, Manufacturing & Distribution, Strategy, Supply Chain
No doubt 3D technology has transformed the world of business. There are numerous inspiring ways by which 3D technology has to reshape the future.
This post comes to us from Adam Robinson of Cerasis, a top freight logistics company and truckload freight broker.
If you are also instructed to learn about the impact of this revolutionary technology then you are at the right spot. Here are seven ways in which this new 3D trend will shape the future of manufacturing sector:
1. Boost Local Production
According to a recent survey based report it is come to know that 3D technology will allow the manufacturer to double the mass production level. It will enable the producers to reach their targets without increasing each unit production cost.
It will also reduce the shipment costs as a local manufacturer will no need to bring material from other countries. Instead, they could easily install 3D manufacturing plant in their own factory to cut the extra cost.
This way local business will easily boost their production process as well as reduce the cost of manufacturing.
2. More Customized Products
When you will engage 3D technology in the manufacturing process, you will get a chance to produce customized goods. It means that you could build everything from clothes to cars in a unique way.
According to a report, it is revealed that in coming years mobile users will get the opportunity to use 3D printing app.
In additional professional designers with also use 3D printing techniques to enter into the new age of industrial design. So, if you want to develop customized products to drive more revenue then you should use 3D printing method.
3. Best For Creativity
It is true to say that 3D technology is the best tool for creative lovers. This is because it enables manufacturer to open up new possibilities to grab the attention of more customers,
Many experts have predicted that the introduction of 3D technology will enable the creativity lovers to fulfill their every desire in an innovative manner.
Whether you want to design a phone or furniture mode, 3D technology will soon make it possible for you to accomplish your goals perfectly.
4. Avoid Copyright Issues
We all know the importance of copyrights to safeguard ones intellectual property. This is why businessmen hire lawyers to overcome a number of legal disputes that are rising due to copyright.
It is anticipated that 3D printing will secure the creativity of artists as everyone will hold ownership of their 3D design.
In case, you are also concerned because of the copyright issue then this technology will help you to overcome legal issues quickly.
5. A New Tool For Large-Scale Producers
Suffice to say that 3D technology is best tool for countries which are totally dependent on manufacturing industry. For instance, as China heavily depends on the manufacturing industry, 3D printing will enable China to target a huge domestic market.
In addition, it will also assist countries that are rapidly moving toward manufacturing sector. It gives them the great benefit to switch their operations to mass-manufacturing level all over the world. This strategy will benefit every growing economy to step in the next level in the coming future.
6. Build New Horizons For Every Industry
The 3D technology will revolutionize production process of every industry including the healthcare sector, education sector as well as food industry. The reason behind this is that scientists are working on 3D models that will facilitate every industry so that more people will take benefit from it.
From research, it is come to know that a popular hospital has printed a jawbone by 3D printer. If you also engage in health sectors then you will also find yourself building human body parts in a 3D manner. Many experts have also researched that 3D tools will also help to assemble chemical compounds and printing drugs.
7. Reduce Crime
It is predicted that new 3D technology will reduce the crime level. This is because people can keep guns that are made on 3D printers to secure themselves from criminals.
In addition, people can create CCTV camera and other 3D technology to catch the criminal in an easy manner. Moreover, it will also help in the production process of military equipment and chemical weapons.
Wrap-Up…
Therefore, it could be said now that 3D printing will offer uncountable benefits to small scales as well as the large-scale manufacturing industry to drive more revenue. If you also belong to the manufacturing industry then you should also tap into the potential of this superb technology.
Related posts:
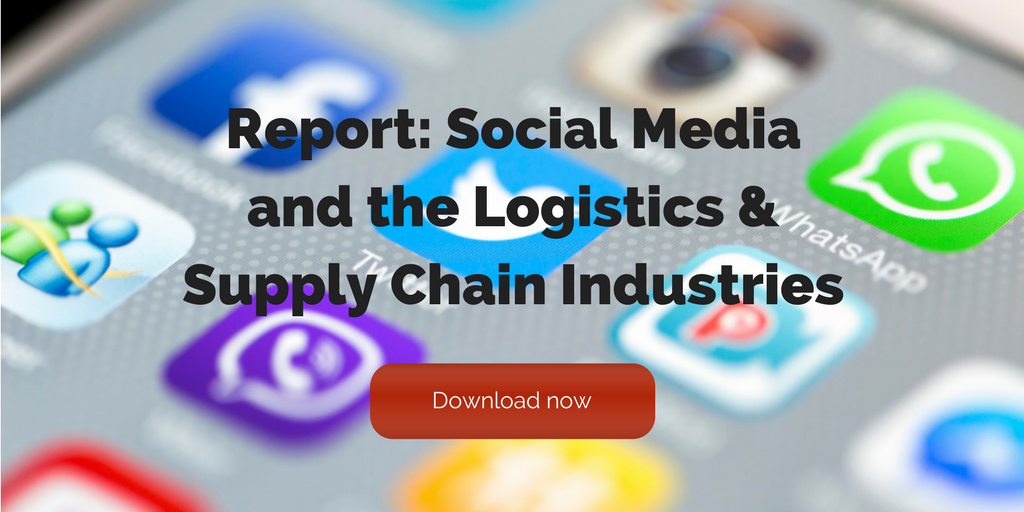
by Elizabeth Hines | Nov 13, 2017 | Blog, Consumer Electronics, Current Events, Manufacturing & Distribution, Strategy, Supply Chain
As sales and consumer desire continue to increase for drones and home assistants, the second-life market has a huge opportunity for growth.
Consumers are becoming ever-more enamored with their gadgets and toys. Drones and home assistants are becoming more ubiquitous in our homes (and flying around our skies). However, when these machines run their course — either because they break, or a newer model comes out — is there still use for them?
The market for gadgets
The marketplace for drones is an ever-growing one. Last year drone sales increased by an astounding 60%, and revenue grew to $4.5 billion. The drone market can be segmented into two categories — personal and commercial. Personal drones, which many consumers use for photography, is predicted to grow 40% this year, while commercial drones, which can be used for survey maps and delivery services, are expected to grow 60%.
While personal-use drones dominate unit sales, commercial-drone sales — which make up only about 6% of the market — are projected to represent 60% of the market’s revenue. This is due to the high cost of commercial drones, some with costs that exceed $100,000.
Home assistants are another intriguing category on the rise. These products are intended to control various devices in your home, such as thermostats, lighting, and security. These products also allow an individual to shop online using voice commands.
The frontrunner for this market has been Amazon’s Echo devices. As the primary nature of Amazon’s business is e-retail, the Echo device plays perfectly into this. By making it simple and easy to make Amazon purchases through voice command, these devices have great potential to bolster Amazon’s bottom line.
While this market is still in its early stages, Gartner Research expects tremendous growth, projecting $2.1 billion in consumer spending on personal home assistants by the year 2020.
The second-life market
So what becomes of these products as we replace them with newer models? Smart phones offer a sensible comparison when looking at the second-life market for these products. In 2016, consumers sold or traded in used cell phone devices for an average of $140 per device, generating a total of $17 billion worldwide. This selling and trading doesn’t just end after one transaction. It is predicted that at least 10% of premium ($500 and up) smartphones will have at least three users before they are retired.
We can draw a parallel about second-life potential between drones/home assistants and cell phones. Advances in technology render previous models obsolete or, at best, out of date. Consumers who can afford them will gravitate toward newer products. As with cell phones, they will generally look to recoup some of the cost for the newer product by selling or trading in the old one. These can then be sold to consumers looking for less expensive, older models. Even in the case of drones that crash, parts can be salvaged and sold to individuals that are looking to build their own drones.
The markets for these products are all still in early stages, so second-life markets are still in growth stages as well. As sales and consumer desire continue to increase for drones and home assistants, their life cycle will go on long after the first owners have moved on to newer models.
This post originally appeared on EBN Online.
Related posts:
by Fronetics | Nov 2, 2017 | Blog, Data/Analytics, Logistics, Strategy, Supply Chain
In a recent study, MIT found that companies that focus on 5 key initiatives to improve their supply chain analytics can have a big impact on their bottom line.
Some supply chain companies are leaning on the power of analytics to help streamline their processes and get ahead of their competitors. But many companies have struggled to embrace the relationship between using analytics and implementing changes that can improve business performance.
The study, published by the MIT Sloan Management Review, asked 353 participants to discuss their understanding of their companies’ analytics systems. The results showed that though most companies have an analytics system in place, very few are using the results to implement necessary changes.
Obstacles to fully utilizing analytics included inaccurate data, cost, and lack of timely data. But the benefits far outweigh the challenges. Hanesbrand Inc., for example, used predictive analytics to make changes in their inventory processes and have since seen an increase in their production and purchase orders.
So how can your company start to incorporate supply chain analytics into your company culture?
Here are 5 tips to help kick-start your analytics implementation:
1. Supply chain analytics initiatives need a top-down mandate
In order to achieve analytical success that has an influence over organizational process, it’s imperative that upper-level management use the analytical systems. Executives need to promote and utilize the systems. Buy-in from managers and team members will be seamless when it’s coming from the top. David Dittmann, director of business intelligence and analytics services at Procter & Gamble Co., stresses that “it is impossible to win over thousands of people one small analytics victory at a time. Analytics must be a top-down mandate to succeed from an organizational perspective.”
2. The simpler the model, the more likely the use
If you want your company to embrace an analytics system, it’s important that the model is simple and easy to grasp. If employees don’t understand how to use the analytics or apply the results, they won’t take the time to implement the system. The more complex a system is, the greater the potential for team members to dismiss it. The Cleo Integration Suite (CIS), for example, promotes itself as an easy-to-use platform that can integrate seamlessly into your pre-existing software. CIS understands that supply chain companies need systems that are elementary to incorporate to achieve results.
3. Business knowledge is essential
Executives in the survey noted that an in-depth understanding of business processes and their effect on the bottom line is critical to supply chain analytics success. To develop the most effective model, companies need to have insight into all of the processes that make their company successful and be able to incorporate the results into these processes. Without this foundational information, the analytics are just “fun facts.”
4. Trust in the numbers
Time is a key factor in successful analytics implementation. In order to achieve timely results, organizations have to trust in the numbers the analytics provides them. “Trust can be built through a closed-loop change management effort that is centered on performance metrics that accurately reflect the current state of the supply chain system.” writes Melissa R. Bowers, Adam G. Petrie, and Mary C. Holcomb. Once these metrics are in place, it is easy to gauge the results against past processes.
Coca-Cola Global implemented a check-and-balances system to cultivate trust in their analytics. Anytime an employee chose to override the analytics system, it gave them feedback to see if their manual adjustments resulted in an improvement or a setback, creating trust in the employees and their dependence on the data.
5. Implement mechanisms to help develop analytics professionals gain business knowledge
Many supply chain companies are hiring analytics professionals to help implement these systems into their organizations. Though experts in their field, it’s important for these trained analytics professionals to learn about all aspects of your business. This business knowledge creates an open relationship between the business and the analytics, creating more opportunities for the numbers to aid in the processes.
Out are the days of order tracking and point of sales data, and in are the days of big data and analytics. Supply chain companies are quickly realizing the need to understand and implement these analytics systems into their day-to-day processes. Creating efficiency and savings using these systems is easier than you think.
Related posts:
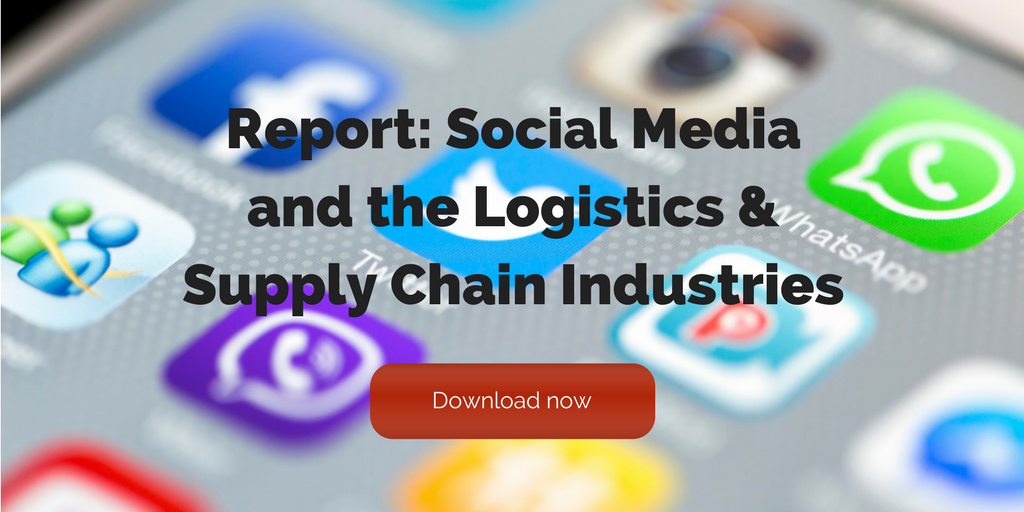