by Fronetics | Feb 13, 2014 | Blog, Content Marketing, Logistics, Marketing, Social Media, Supply Chain
Despite the considerable amount of attention paid to demand generation, many companies (including some companies actively employing a demand generation strategy) do not have a clear understanding of what demand generation actually is.
When asked to define demand generation, a common response is: the generation of demand. Another common response: a marketing strategy. An honest response: I don’t know; what the heck is demand generation?
Demand generation is the creation of awareness and excitement about your company and your products and services. Demand generation is not a one-off; rather it is a continuous process of engaging and nurturing both current and future customers. Demand generation helps you attract new customers and engage (or re-engage) current customers. Demand generation grows your business.
Components of a demand generation strategy include: blogs, social media, podcasts, video, newsletters, email, white papers, and case studies. These components work together. They position your company as a thought leader, expert, and influencer in your industry. They build trust. Importantly, they drive engagement and communication. The foundation of demand generation is the creation and sustaining of relationships between your company and your customers – current and future.
According to DemandGen, 90 percent of business buyers say when they’re ready to buy, they’ll find you. How will they find you? When B2B buyers were asked to rank where they turn to find a new solution, 46 percent listed a “web search” as their first source for information. The leading choice for both the second and third ranked sources was vendor web sites.
With respect to social media, DemandGen found that blogs are considered to be the social media channel with the biggest impact on the researching process (46 percent). LinkedIn was also found to be a place where buyers turned to conduct research (41 percent).
The survey also found that content had a significant impact on the decision to buy. Nearly two-thirds of respondents said “a vendor’s content had a significant impact on their buying decision,” and 34 of respondents “strongly agreed that the winning vendors provided a better mix of content to guide them through each stage of the researching and decision-making process.”
What is the take away? The take away is that a company with a strong presence and a demand generation strategy is more likely to be successful than a company who does not have a strong presence or a demand generation strategy.
What is the different between a successful demand generation strategy and one that falls flat? A successful strategy incorporates communication, engagement, and quality content. Furthermore, a successful demand generation strategy is built upon an understanding of customer needs and interests –real, not perceived.
At Fronetics we work with our clients to design and implement a demand generation strategy that is right for them – for their company and for their customers. We know how to create awareness and excitement about our clients’ companies and their products and services. We also know how to help our clients engage with and nurture their customers.
Through our demand generation service, Engage, we help companies acquire new customers and grow their businesses by penetrating new markets and deepening their presence and impact in existing markets. If you are interested in learning more about Engage and about creating a successful demand generation strategy, we’d love to talk with you.
by Fronetics | Feb 13, 2014 | Blog, Content Marketing, Logistics, Marketing, Social Media, Supply Chain
Despite the considerable amount of attention paid to demand generation, many companies (including some companies actively employing a demand generation strategy) do not have a clear understanding of what demand generation actually is.
When asked to define demand generation, a common response is: the generation of demand. Another common response: a marketing strategy. An honest response: I don’t know; what the heck is demand generation?
Demand generation is the creation of awareness and excitement about your company and your products and services. Demand generation is not a one-off; rather it is a continuous process of engaging and nurturing both current and future customers. Demand generation helps you attract new customers and engage (or re-engage) current customers. Demand generation grows your business.
Components of a demand generation strategy include: blogs, social media, podcasts, video, newsletters, email, white papers, and case studies. These components work together. They position your company as a thought leader, expert, and influencer in your industry. They build trust. Importantly, they drive engagement and communication. The foundation of demand generation is the creation and sustaining of relationships between your company and your customers – current and future.
According to DemandGen, 90 percent of business buyers say when they’re ready to buy, they’ll find you. How will they find you? When B2B buyers were asked to rank where they turn to find a new solution, 46 percent listed a “web search” as their first source for information. The leading choice for both the second and third ranked sources was vendor web sites.
With respect to social media, DemandGen found that blogs are considered to be the social media channel with the biggest impact on the researching process (46 percent). LinkedIn was also found to be a place where buyers turned to conduct research (41 percent).
The survey also found that content had a significant impact on the decision to buy. Nearly two-thirds of respondents said “a vendor’s content had a significant impact on their buying decision,” and 34 of respondents “strongly agreed that the winning vendors provided a better mix of content to guide them through each stage of the researching and decision-making process.”
What is the take away? The take away is that a company with a strong presence and a demand generation strategy is more likely to be successful than a company who does not have a strong presence or a demand generation strategy.
What is the different between a successful demand generation strategy and one that falls flat? A successful strategy incorporates communication, engagement, and quality content. Furthermore, a successful demand generation strategy is built upon an understanding of customer needs and interests –real, not perceived.
At Fronetics we work with our clients to design and implement a demand generation strategy that is right for them – for their company and for their customers. We know how to create awareness and excitement about our clients’ companies and their products and services. We also know how to help our clients engage with and nurture their customers.
Through our demand generation service, Engage, we help companies acquire new customers and grow their businesses by penetrating new markets and deepening their presence and impact in existing markets. If you are interested in learning more about Engage and about creating a successful demand generation strategy, we’d love to talk with you.
by Fronetics | Jan 28, 2014 | Blog, Logistics, Marketing, Social Media, Strategy, Supply Chain
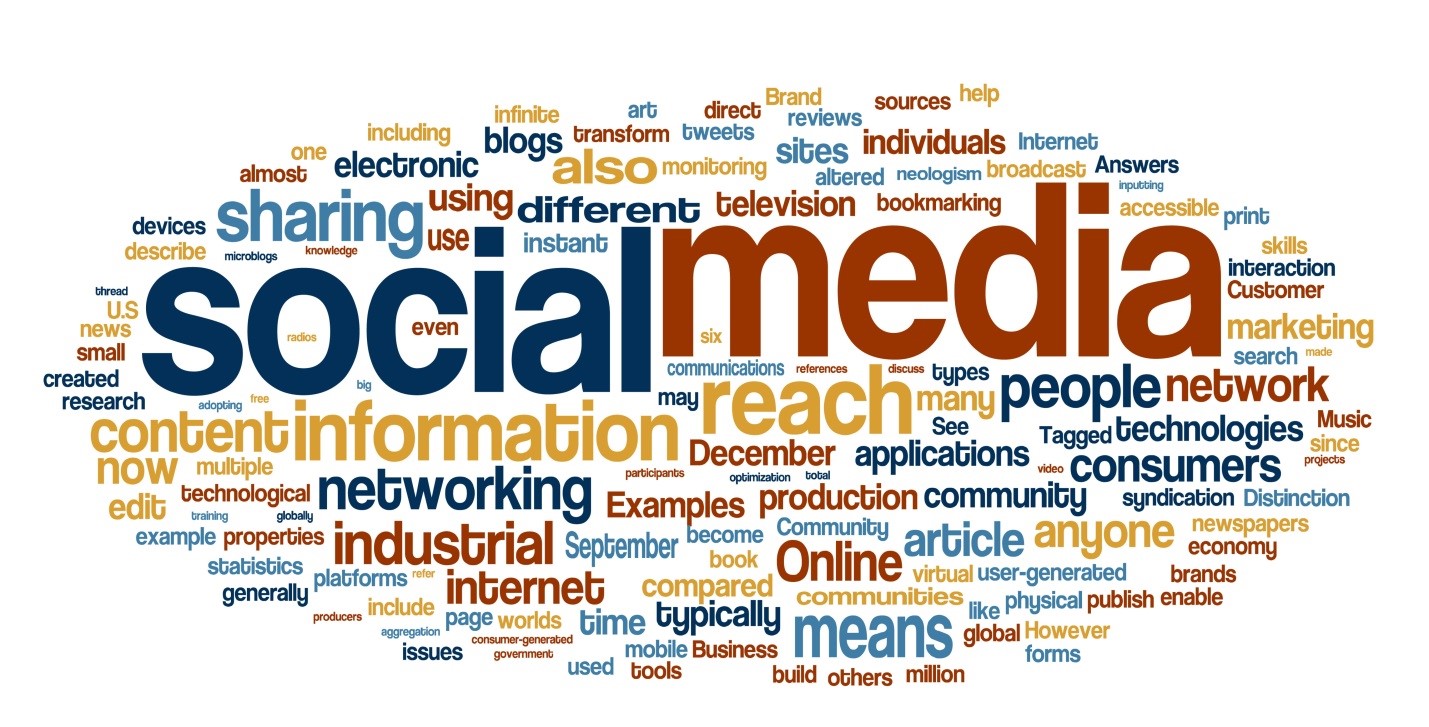
Social media and social media technologies have rapidly changed the way companies do business across every type of industry. Social media brings businesses closer to their customers, provides a platform for communication and building thought leadership, and when executed properly it can help drive business and provide a significant return on investment. Businesses that ignore social media forgo these opportunities and miss out on potential business development opportunities.
According to The McKinsey Global Institute, 90 percent of companies who were using social media or social technologies for their business reported benefiting from their efforts in 2012. And how could they not? Utilizing a social media technology can increase a company’s reach into their industry and provides optimal channels for communicating with their customers.
The supply chain and logistics industries are two industries that have not adopted social media and social technologies as quickly as others. Business owners in these have a difficult time seeing past the “social” aspect of these technologies and understanding what the implied benefits of using social technologies can mean for their business. Many find themselves asking “why?” instead of “how?” when considering implementing a social media strategy, and ultimately allocate resources elsewhere within their businesses.
The Fronetics white paper, Social Media and the Logistics and Supply Chain Industries: Why Not Participating is a Risk You Can’t Afford to Take, provides meaningful insights into why supply chain and logistics companies need to be using social media and the value of these technologies. Learn how to move past the barriers to adoption, how to leverage social technologies, and learn what a social presence can mean for your business.
To learn more about why your business needs social media, download Social Media and the Logistics and Supply Chain Industries: Why Not Participating is a Risk You Can’t Afford to Take today.
by Fronetics | Jan 28, 2014 | Blog, Logistics, Marketing, Social Media, Strategy, Supply Chain
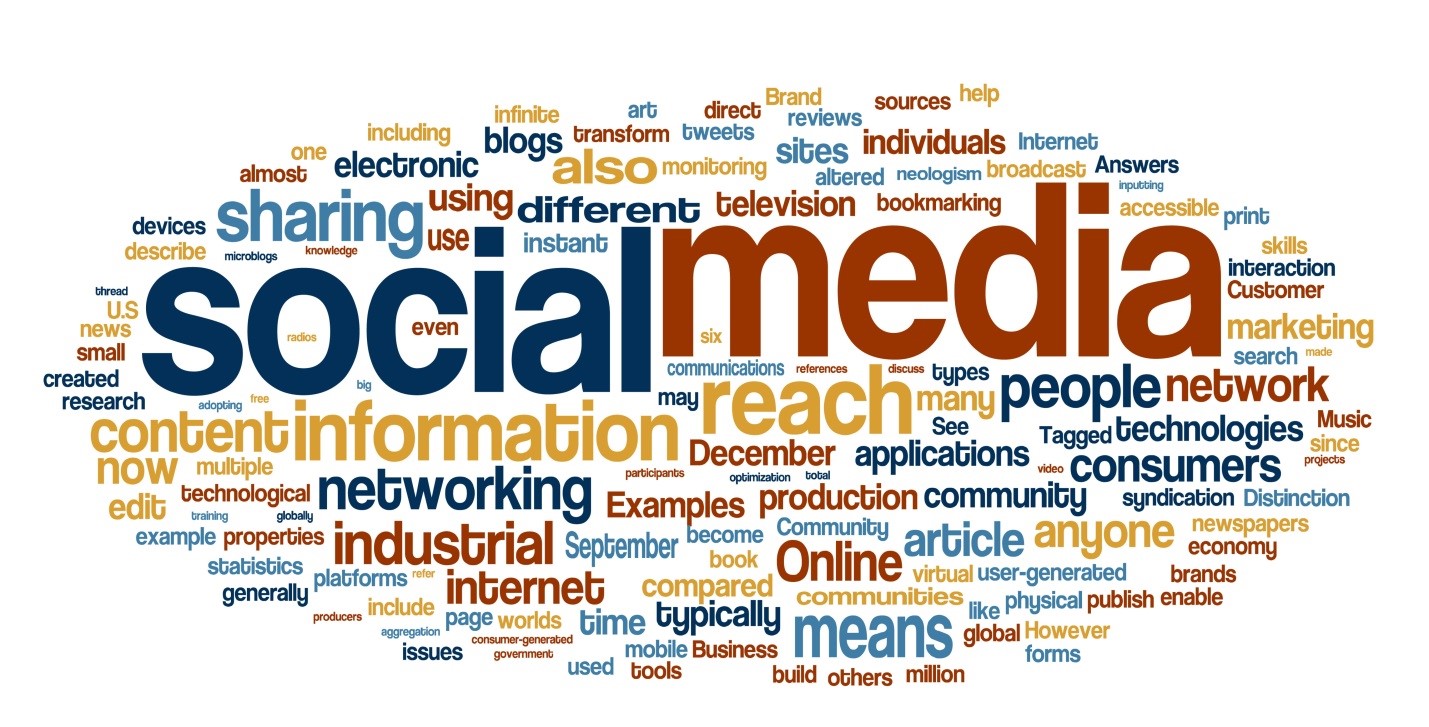
Social media and social media technologies have rapidly changed the way companies do business across every type of industry. Social media brings businesses closer to their customers, provides a platform for communication and building thought leadership, and when executed properly it can help drive business and provide a significant return on investment. Businesses that ignore social media forgo these opportunities and miss out on potential business development opportunities.
According to The McKinsey Global Institute, 90 percent of companies who were using social media or social technologies for their business reported benefiting from their efforts in 2012. And how could they not? Utilizing a social media technology can increase a company’s reach into their industry and provides optimal channels for communicating with their customers.
The supply chain and logistics industries are two industries that have not adopted social media and social technologies as quickly as others. Business owners in these have a difficult time seeing past the “social” aspect of these technologies and understanding what the implied benefits of using social technologies can mean for their business. Many find themselves asking “why?” instead of “how?” when considering implementing a social media strategy, and ultimately allocate resources elsewhere within their businesses.
The Fronetics white paper, Social Media and the Logistics and Supply Chain Industries: Why Not Participating is a Risk You Can’t Afford to Take, provides meaningful insights into why supply chain and logistics companies need to be using social media and the value of these technologies. Learn how to move past the barriers to adoption, how to leverage social technologies, and learn what a social presence can mean for your business.
To learn more about why your business needs social media, download Social Media and the Logistics and Supply Chain Industries: Why Not Participating is a Risk You Can’t Afford to Take today.
by Elizabeth Hines | Jan 28, 2014 | Blog, Strategy, Supply Chain
This article was previously published on EBN.
Looking for a way to make your supply chain more efficient? You might want to consider reusable packaging.
Reusable packaging includes pallets, racks, bulk containers, bins, dollies, handheld containers, and dunnage typically made from durable materials such as plastic, wood, and metal. Traditional packaging solutions are designed for one-time use, but reusable packaging can withstand the rigors of the supply chain for five years or more.
Using reusable packaging can make your supply chain more efficient from both an operational and environmental standpoint.
Operationally, reusable packaging can help you reduce overall packaging costs, product damage, labor cost, required warehouse/transport space, costs per trip, energy usage, and the number of trips you make. It can improve workplace efficiency and workplace safety. Studies have found that, on average, reusable packaging generates 29 percent fewer greenhouse gas emissions and 95 percent less solid waste than single-use packaging, and it consumes 39 percent less energy.
Let’s look at a couple of examples that offer lessons for the electronics supply chain.
ANG Newspapers (ANG) in California has the largest daily circulation among newspapers in the East Bay and the third largest in the San Francisco Bay Area. Facing the high costs of wooden pallet breakage and waste removal (wood waste) and seeking to improve its distribution system, ANG made the switch to reusable pallets. The switch has reduced annual labor costs by $46,000 and prevented 37 tons of wood waste per year. Additionally, less space is needed to store pallets, and the company has improved operations and worker safety. It realized a return on investment (ROI) of 125 percent.
Another example: Ghirardelli Chocolate Co. was spending $520,000 a year for 580,000 cardboard boxes for internal distribution. The boxes tended to collapse when they were stacked. This damaged the product and generated $2,700 of disposal costs for soiled cardboard. To reduce packaging costs and cardboard waste and to improve its environmental performance, Ghirardelli invested in reusable totes. The investment will provide the company with a net savings of $1.95 million, eliminate 350 tons of cardboard waste per year, and decrease repetitive stress injuries. What’s more, the company has realized an ROI of 325 percent.
Though reusable packaging is generally better suited for closed-loop systems, it is possible to increase your supply chain efficiency by using reusable packaging and working with third-party poolers.
Want to learn more about reusable packaging? Jerry Welcome, president of the Reusable Packaging Association, wrote an article for Packaging Revolution on how to determine if reusable packaging can boost your profits. Also, the Reusable Packaging Association provides calculators to help companies estimate the environmental and economic differences between one-way and reusable packaging systems.
The US market for returnable transport packaging (RTP) is estimated to exceed $1.1 billion. The Priority Metrics Group projects that the RTP market will grow at a compound annual rate of 6.1 percent over the next few years. By 2017, it expects the global market to reach $6.75 billion.
Reusable packaging may not be right for everyone, but the industry is growing, and the benefits can be large.
by Elizabeth Hines | Jan 28, 2014 | Blog, Strategy, Supply Chain
This article was previously published on EBN.
Looking for a way to make your supply chain more efficient? You might want to consider reusable packaging.
Reusable packaging includes pallets, racks, bulk containers, bins, dollies, handheld containers, and dunnage typically made from durable materials such as plastic, wood, and metal. Traditional packaging solutions are designed for one-time use, but reusable packaging can withstand the rigors of the supply chain for five years or more.
Using reusable packaging can make your supply chain more efficient from both an operational and environmental standpoint.
Operationally, reusable packaging can help you reduce overall packaging costs, product damage, labor cost, required warehouse/transport space, costs per trip, energy usage, and the number of trips you make. It can improve workplace efficiency and workplace safety. Studies have found that, on average, reusable packaging generates 29 percent fewer greenhouse gas emissions and 95 percent less solid waste than single-use packaging, and it consumes 39 percent less energy.
Let’s look at a couple of examples that offer lessons for the electronics supply chain.
ANG Newspapers (ANG) in California has the largest daily circulation among newspapers in the East Bay and the third largest in the San Francisco Bay Area. Facing the high costs of wooden pallet breakage and waste removal (wood waste) and seeking to improve its distribution system, ANG made the switch to reusable pallets. The switch has reduced annual labor costs by $46,000 and prevented 37 tons of wood waste per year. Additionally, less space is needed to store pallets, and the company has improved operations and worker safety. It realized a return on investment (ROI) of 125 percent.
Another example: Ghirardelli Chocolate Co. was spending $520,000 a year for 580,000 cardboard boxes for internal distribution. The boxes tended to collapse when they were stacked. This damaged the product and generated $2,700 of disposal costs for soiled cardboard. To reduce packaging costs and cardboard waste and to improve its environmental performance, Ghirardelli invested in reusable totes. The investment will provide the company with a net savings of $1.95 million, eliminate 350 tons of cardboard waste per year, and decrease repetitive stress injuries. What’s more, the company has realized an ROI of 325 percent.
Though reusable packaging is generally better suited for closed-loop systems, it is possible to increase your supply chain efficiency by using reusable packaging and working with third-party poolers.
Want to learn more about reusable packaging? Jerry Welcome, president of the Reusable Packaging Association, wrote an article for Packaging Revolution on how to determine if reusable packaging can boost your profits. Also, the Reusable Packaging Association provides calculators to help companies estimate the environmental and economic differences between one-way and reusable packaging systems.
The US market for returnable transport packaging (RTP) is estimated to exceed $1.1 billion. The Priority Metrics Group projects that the RTP market will grow at a compound annual rate of 6.1 percent over the next few years. By 2017, it expects the global market to reach $6.75 billion.
Reusable packaging may not be right for everyone, but the industry is growing, and the benefits can be large.