by Jennifer Hart Yim | Jun 4, 2018 | Blog, Content Marketing, Current Events, Logistics, Manufacturing & Distribution, Marketing, Supply Chain
3-D printing opens up new revenue opportunities for supply chain, helping companies meet demand in real time, manage inventory without limiting products they offer, and increase lead time.
This article is part of a series of articles written by MBA students and graduates from the University of New Hampshire Peter T. Paul College of Business and Economics.
Spring has finally arrived in New England. However, with spring comes every vehicle’s most dreaded enemy, the pothole! My coworker Will recently fell victim to one such nemesis. His part-sourcing saga has me wondering how soon the narrative may change.
On what started as a normal morning, Will soon found himself calling a tow truck to get his car to the shop and a coworker to get himself to work. An unavoidable pothole caused one of his ball joints to fail, and limping anywhere was not an option. The silver lining of the day was that his very accommodating mechanic agreed that Will could source his own parts.
A sourcing saga ensued.
The layers of research he had to do was frustrating. Which manufacturers make the quality of product he wants? Then which distributors can provide him the quantity he needs when he needs them at the best price?
This meant calls to local auto part stores, price checking against online distributors, verifying brands & model numbers, accounting for lead times, stockouts, shipping and handling fees to determine how to get the best total value of quality, cost, and delivery.
Complex decisions like this are common in many sourcing scenarios.
But does it have to be?
What if distributors could better manage their inventory without limiting the products that they offer or increasing the lead times to their customers?
With 3-D printing, that may soon be attainable.
Rather than holding inventory from various manufacturers, a distributor could have license agreements with manufacturers to print parts on demand.
Revolutionary though this sounds, it’s not an unfamiliar model. Not so long ago, buying music meant going to a physical store to purchase or order an album. Now streaming services have license agreements with record companies to meet consumer demand in real time.
Jay Leno has been 3-D printing parts for his fleet of classic cars for nearly a decade. He admitted that initially the costs were prohibitive for most people. However now that 3-D printers are available at a wide range of price points, it is becoming more economical to print products on demand.
Printing parts with low inventory turns on demand would reduce inventory costs within the entire supply chain, having a positive impact on a company’s bottom line. High-value, low-volume parts like those of late model vehicles are the perfect candidates. In fact, BMW, Porsche, and Mercedes-Benz Trucks have begun 3-D printing spare parts older models and freight trucks.
3-D printing and logistics
The next logical progression to reduce overall supply chain cost is to move production as close to the customer as possible. Logistics companies are positioning themselves to be ready to integrate into this production model.
Both UPS and DHL have recognized the potential for end-of runway 3-D print capabilities and local 3-D “print shops.” UPS has partnered with SAP and Fast Radius to launch its On-Demand 3D Printing Manufacturing Network, which leverages 3-D printing technology, analytics and UPS’s global network to execute production at the location where capacity and logistics are optimum.
This summer, BMW Motorrad will provide spare-part printing capability directly to customers with BMW Motorrad iParts, a mobile 3-D printer designed to travel with you on the back of your BMW Motorrad motorcycle. Customers will use a mobile app to download a part file from the cloud-based library and print parts on the go. Although limited by the size of the printer, Motorrad rides will be able to replace small parts in nearly any location. Customers can even preload files so, no matter where they are — the side of a mountain or the middle of a desert — they can make spare parts.
These companies are not alone in seeing the value of 3-D printing on the go. Amazon made headlines when it first filed for a patent on a 3-D printing delivery truck. That patent was granted at the beginning of this year. Although a launch plan has not been announced, a major player with that capability is a definite catalyst for more innovation at the intersection of 3-D printing and logistics.
The future
[bctt tweet=”It’s clear that logistics and inventory management will not look the same 10 years from now. The question is: when and where it will be economical to print parts on demand?” username=”Fronetics”]
It’s clear that change is coming, logistics and inventory management will not look the same 10 years from now. The question is: when and where it will be economical to print parts on demand? Will it be at an end-of-runway distribution center, a local multipurpose 3-D printing shop, or on-site at repair shops? Will AAA be able to print a new ball joint in a roadside truck and change it out like it was no different than the services they offer for tires and battery today? I can’t wait to find out.
In the meantime, Will had to deal with today’s sourcing options. After many phone calls, dozens of emails, and multiple carpools to work, his car is back on the road. And he believes he got four new ball joints at a good value.
About the author
Ruth DeMott is a quality engineer at Pratt & Whitney currently pursuing an MBA at the University of New Hampshire. She holds a BS in Industrial Engineering from Worcester Polytechnic Institute (class of 2010). She has held roles of increasing responsibility in the manufacturing and quality engineering departments since joining Pratt upon completion of her undergraduate degree. She is involved in the New Hampshire Youth Rugby program, enjoys traveling, putting things together, and spending time with friends and family.
Related posts:
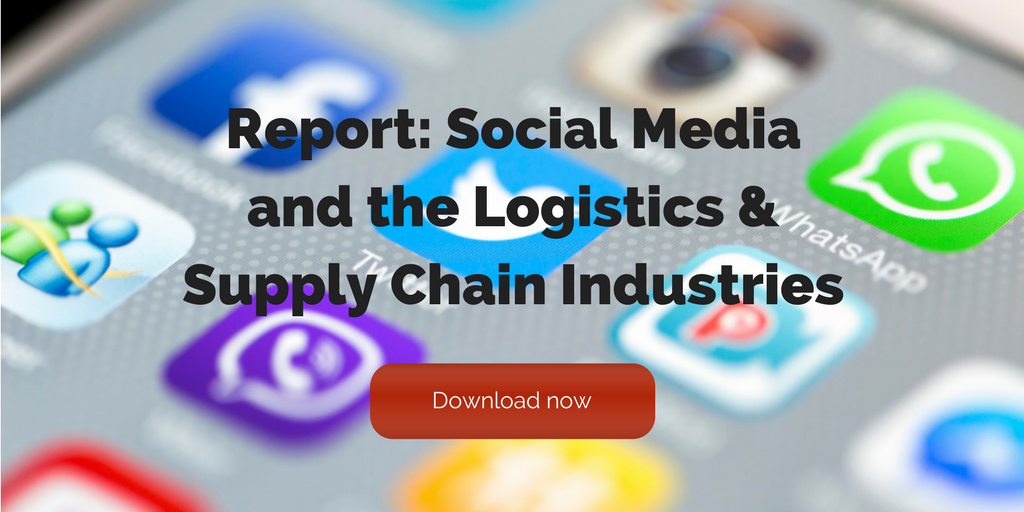
by Elizabeth Hines | May 29, 2018 | Blog, Content Marketing, Current Events, Data Security, Data/Analytics, Manufacturing & Distribution, Marketing, Strategy, Supply Chain
While information-heavy companies employ entire teams dedicated to cyberattacks, American factories have quietly been growing more and more susceptible.
It’s been eight years since the widely publicized Stuxnet virus was released to wreak havoc on its unsuspecting victims. Are we in a better place now to deal with a highly sophisticated next-generation Stuxnet-style attack?
[bctt tweet=”Information heavy companies have entire teams dedicated to cyber defense, while American factories have been left more and more susceptible.” username=”Fronetics”]
Most experts say no. In fact, studies suggest that manufacturers, in particular, are increasingly vulnerable to cyberattacks. While information-heavy companies have grown to employ entire teams dedicated cyber defense, American factories have quietly been growing more and more susceptible.
Time to Pay Attention
Ransomware attacks, in which hackers use malware to encrypt data, systems, or networks until a ransom is paid, are alarmingly common. According to a recent report from Radware, 42% of global companies have dealt with this kind of attack. That number has been steadily rising. The number of companies reporting financially motivated attacks has doubled in the last two years.
Manufacturers — if you haven’t been paying attention yet, it’s time. This summer, about half of the organizations targeted by the sweeping Petya ransomware cyberattack were manufacturers. The recent WannaCry virus actually forced a Honda plant in Japan to halt production.
And there’s a bit more: The Wall Street Journal recently reported on what they call a new type of cyberattack that targets factory safety systems. Hackers who attacked a petrochemical plant in Saudi Arabia last year specifically focused on a safety shut-off system.
Is the WSJ right? Is this a new trend? Will hackers begin targeting control-system computers that manage American factory floors, chemical plants, and utilities on a more regular basis? Maybe.
There are plenty of theories that even the most crippling ransomware attacks like Petya and WannaCry are, at their core, motivated by something other than money, namely sheer pleasure in chaos and disruption. The potential damage to factory production and safety systems is growing. Now is the time to wake up and pay attention.
Factories Growing More Susceptible
Factories and manufacturers are at a heightened risk for a few coinciding reasons.
The complexity of our supply chains is a liability. With parts and materials from diverse and sometimes changing sources, as well as networks that can span all phases of production, our supply chains are large and constantly adapting and, because of this, extremely vulnerable.
The intensity of the manufacturing schedule raises a second issue. Many manufacturing facilities run around the clock, and halting factory production for testing is often cumbersome and costly.
The third reason is, of course, the byproduct of a manufacturing sector that has become steadily more data-driven and dependent on information technology. As manufacturing has steadily merged with technology to create the Industrial Internet of Things, we too have unknowingly created a space in which hackers see the potential for massive amounts of under-protected data, equipment, networks, and intellectual property.
How Can We Prepare
We’ve all heard the mantra, “The first step to solving any problem is admitting you have one.” A core concern has been the manufacturing sector’s inability or unwillingness to face this growing threat.
A report summary issued through a joint venture between MForesight and the Computing Community Consortium warned, “There’s a widespread failure to reckon with the risks.” The report recognizes that solving the issue will be long-term and complicated, but offers a few suggestions, including wide-reaching efforts to increase awareness, collaboration with trusted third-party partners, and cybersecurity research and development.
In the shorter term, maybe this can help. Last year the National Institute of Standards and Technology (NIST) released a Cybersecurity Framework Manufacturing Profile that provides a roadmap to managing cybersecurity and reducing risk to your manufacturing systems.
But I think Sridhar Kota, professor of engineering at the University of Michigan, hit the nail on the head in his article entitled A Plan for Defending U.S. Manufacturers from Cyberattacks, when he wrote: “Cybersecurity needs to become a deeply ingrained part of every manufacturing company’s culture — embedded in management decisions, workforce training, and investment calculations.”
The risks to manufacturers are growing from all-too-common ransomware attacks to sophisticated Stuxnet-style assaults targeting our safety systems. Its’s time that we in the manufacturing sector think of cybersecurity, and cyber defense, in absolutely every decision we make. To do otherwise is reckless.
Related posts:
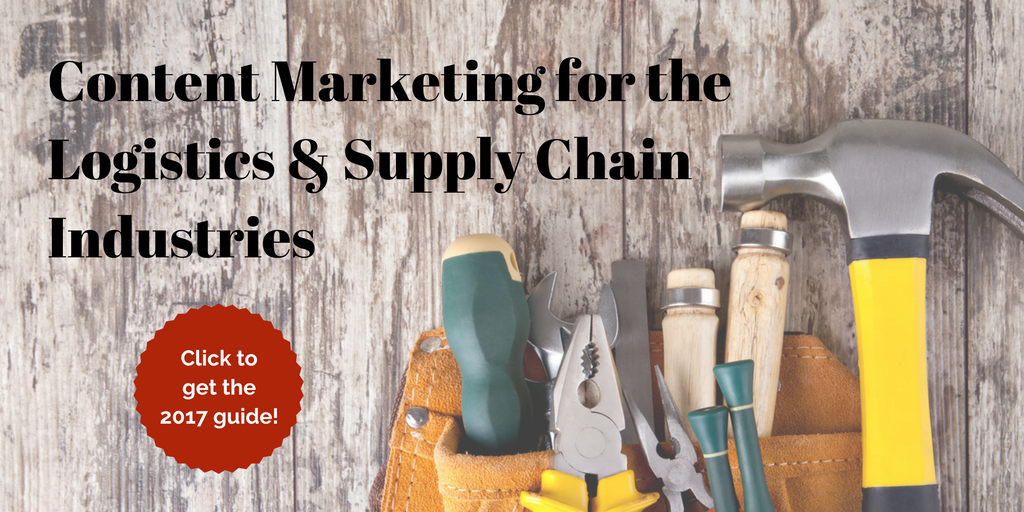
by Elizabeth Hines | Apr 3, 2018 | Blog, Content Marketing, Current Events, Manufacturing & Distribution, Marketing, Supply Chain
In many cases, automation in manufacturing creates leaner, more efficient operations. Efficiency facilitates new opportunities and business growth, which in turn allow for job creation.
The rise of artificial intelligence (AI) and its applications in manufacturing have driven a palpable fear that mass job loss is on the horizon. We have to wonder: is the threat as real and as imminent as many think? Like many things, the answer is more nuanced than a simple yes or no.
A McKinsey Global Institute report predicts that automation could cause the loss of between 39 and 73 million jobs by 2030 in the U.S. alone. Clearly, the AI genie will not be put back into its bottle. However, this doesn’t mean that all jobs across all sectors will be affected evenly.
Generally, low-skill jobs are more susceptible to replacement by AI. This is especially true in industries like retail, which has worked to automate many aspects along the purchase journey, including processes designed to get packages into consumers’ hands faster.
Not the end of the world
Oddly enough, 73 million lost jobs doesn’t spell all doom and gloom. Yes, people will lose jobs — that is inevitable. Automation, however, will create many more.
Think about it: In many cases, automation creates leaner, more efficient operations. Efficiency facilitates new market opportunities and business growth, which in turn allow for expansion and job creation. And these new jobs aren’t the low-skill positions of their pre-automation predecessors. They’re operating new technology, supervising automated processes, and other higher-paying opportunities.
Amazon: Case in point
Consider the retail industry’s brick-and-mortar boom and bust and the rise of e-commerce. As stores shuttered, companies had to downsize the number of individuals they employed. Then, as e-commerce boomed, e-retailing companies were able to bring on more employees — often at higher salaries than in traditional retail.
Amazon’s expansion to the “once-thriving factory town” of Fall River, Mass., offers a prime example. The city, which boasted nearly 20,000 manufacturing jobs in 1991, saw that number dip below 4,000 by 2015 — in large part due to automation. The 2016 arrival of an Amazon fulfillment center was the single largest job-creation event in recent memory.
Employment at the Fall River center has crept above 2,000 in just over a year. And it’s apparent that number will keep rising and that humans won’t be phased out anytime soon. In fact, rather than replace human workers, Amazon’s technology helps each become more efficient. That stimulates Amazon’s growth and the need for more fulfillment centers and more talent to fill those jobs.
While the majority of the Fall River center’s jobs are not skilled and pay reflects that, other benefits such as overtime, tuition aid, and company shares make annual compensation comparable to or better than what local textile mills once paid. Fulfillment center jobs certainly pay above traditional retail and offer employees the opportunity to work withartificial intelligence — rather than in competition with it.
A double-edged sword
AI in the warehouse may stimulate job growth. But those most likely to lose their jobs to automation — low-skill workers — may not possess the transferable skills to be successful in the new wave of jobs created by technology. For example, would a former factory worker who put together boxes for fulfillment be hirable for a position operating custom box-cutting machinery?
Amazon, again, exemplifies a solution. The company offers its workers significant training and education to breach any skill gaps. Those who have never had experience in a warehouse or operating technology will need companies to invest in their training to ensure those who have lost their jobs to automation will have a place in the new economy.
History repeating
This isn’t the first time we’ve encountered such an issue. Before ATMs were the ubiquitous cash-dispensing machines, many thought them the great disruptor of the banking industry. The bank teller’s role was sure to become obsolete.
What actually happened is that ATMs led to more efficiently run banks. While some jobs were lost, banks were actually able to open up more branch locations, which led to the creation of more jobs.
Will automation in the warehouse cause the same scenario to happen? Will organizations become more efficient, allowing them to grow and hire more workers at better, higher paying jobs? In many cases, it looks like it already has.
Related posts:
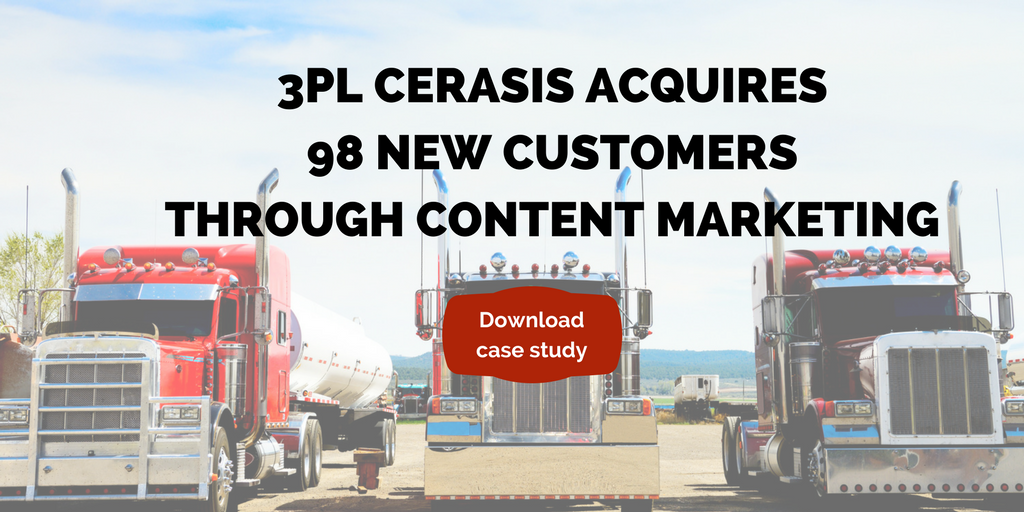
by Fronetics | Feb 12, 2018 | Blog, Current Events, Logistics, Manufacturing & Distribution, Supply Chain
As Cupid spreads his wings, gifts of experience and romantic, at-home options will take over the market for Valentine’s Day 2018.
Consumers will spend a near-record $19.2 billion on Valentine’s Day 2018, up from $18.2 billion in 2017. According to NRF’s annual survey, over half of the country will participate (55%) in the romantic holiday, spending just over $140 on average.
Gifts of experience
A new Valentine’s trend is giving gifts of experience, such as a spa treatment, concert tickets, or a cooking class. Almost half of celebrants said they would prefer a gift of experience, and 23% said they plan on giving a gift of experience. Blue Apron’s Love at First Bite targets couples looking for gifts of experience with a foolproof, stay-at-home option for Valentine’s Day 2018. And they’re not the only ones! Hello Fresh, Plated and even Whole Foods are publishing blog articles and offering meal options for creating the perfect Valentine’s dinner from the comfort of your own kitchen.
Out on the town
The NRF’s survey also found that younger people (ages 18-34) are more likely to take their Valentine out for the evening than older generations. So it’s no surprise that 6 out of 10 younger celebrants (ages 18-34) would also prefer a gift of experience over candy and flowers.
Mobile trend
95% of Americans own a cell phone. The growing connection between smartphones and digital information is starting to take over Valentine’s Day, as well. Over half of participants plan to use their smartphones to assist with Valentine’s Day purchase decisions. Nearly 40% said they plan to use their cell phone to research products and compare prices.
Tradition prevails
Not to worry, though: Celebrants will still purchase plenty of flowers, jewelry and candy to mark the holiday. Celebrants are most likely to give candy as a gift, followed by greeting cards, flowers, and an evening out.
Here’s a look at how U.S. consumers will be celebrating Valentine’s Day 2018.
Valentine’s Day 2018 Supply Chain Infographic
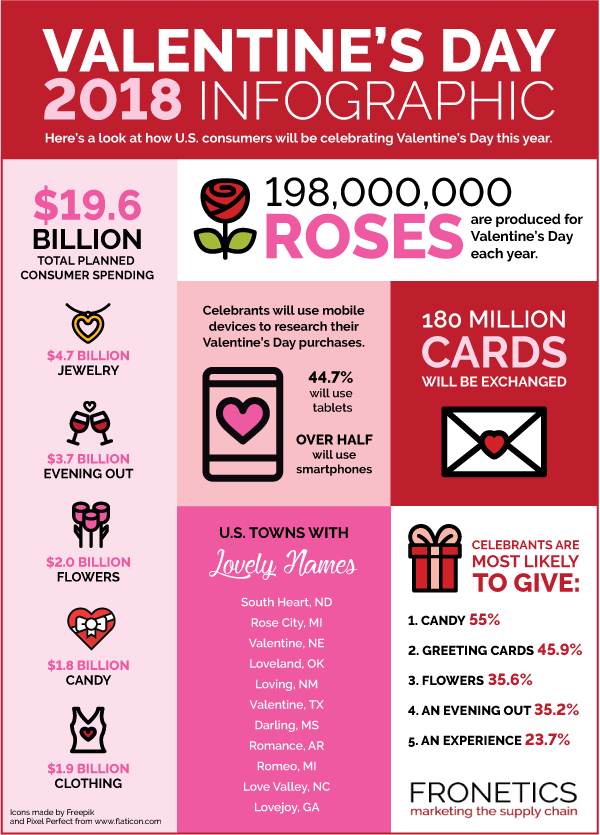
Related posts:
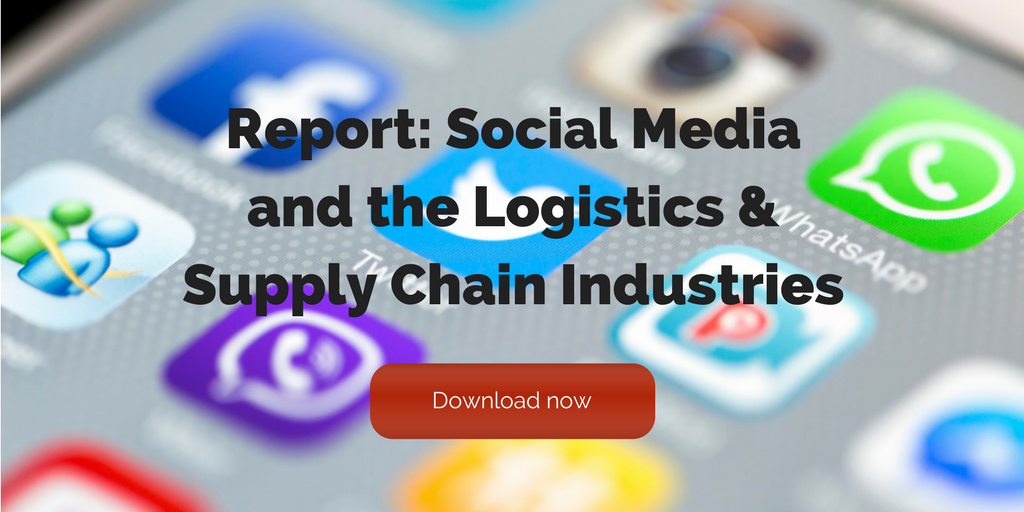
by Jennifer Hart Yim | Dec 7, 2017 | Blog, Logistics, Manufacturing & Distribution, Supply Chain
Within the month, the electronic logging device mandate will take effect. While shippers have known about the mandate for two years, truckers, shippers and carriers are still concerned about how it will impact capacity.
This post comes to us from Adam Robinson of Cerasis, a top freight logistics company and truckload freight broker.
Paired with soaring manufacturing and tightening capacity within the last month, the electronic logging device (ELD) mandate could cause the capacity crunch to worsen. In addition, other regulations, like changing attitudes and backlash at the environmental protection agency (EPA) and struggling infrastructure in Hurricane-affected areas, could cause further capacity problems. To help prevent the worsening of the capacity crunch, let’s take a closer look at how the ELD mandate and other regulations may affect capacity.
What Is the ELD Mandate?
The ELD mandate is a portion of the “Moving Ahead for Progress in the 21st Century” bill, which was passed by the United States Congress in 2012, explains ELDFacts.com. The bill outlines criteria for highway funding and the use of ELDs for use in a trucker’s Record of Duty Status. Today, the record of duty status is used to record compliance with an existing hours of service (HOS) requirements. Although the ELD mandate is a means to tracking HOS requirements, the two laws are completely different. As a result, but the ELD mandate and HOS regulations may have separate impacts on the capacity crunch.
When Does It Take Effect?
The ELD mandate is set to take effect December 18, 2017, and unfortunately, many owner-operator, truckers have not yet completed the installation of ELDs or found an appropriately authorized and licensed ELD vendor, says Jeff Berman of Supply Chain 24/7. However, the Federal Motor Carrier Safety Administration (FMCSA) will not begin requiring inspectors to place commercial motor vehicle drivers without and installed ELD out of service until April 1, 2018.
Even truckers with prior ELDs installed, which may have been installed before 2012, the upcoming ELD deadline has stringent requirements for what type of ELD may be used and who may install it. Truckers with existing ELDs from the pre-ELD mandate period will be automatically grandfathered into the existing list of ELDs at the end of 2019. Therefore, truckers looking to continue driving for the next two years need to have a new, approved ELD installed no later than the April deadline, if not the preferred December deadline. In the interim, politicians are still in debate about if the costs of installing new ELDs is justified under existing regulations, reports Supply Chain Dive. However, part of the reason the FMSCA has not yet rescinded or pushed back implementation revolves around HOS requirements.
What About HOS Regulations and the Capacity Crunch?
The capacity crunch revolves around how much available capacity is being used at any given time in the trucking industry. As a result, capacity is directly tied to the number of drivers which may be operating at any given time simultaneously. According to the FMCSA, the HOS rules are quite specific for property-carrying drivers. These include the following:
- Truckers have an 11-hour driving limit, and truckers may only drive a maximum of 11 hours after 10 consecutive hours off duty. Considering the amount of time required to park a truck, take breaks and other activities, it is nearly impossible for drivers to get in a full, 11 hours of daily driving while still obtaining the 10 required, consecutive hours off duty.
- Drivers now also have a 14-hour absolute driving limit for driving after coming on duty, following 10 consecutive hours of off-duty.
- Drivers must also take breaks and may only drive if eight hours or less have passed since the end of the drivers last off-duty.
- Perhaps the biggest impact for the HOS regulation is its specification of how many hours a driver may work within an eight-day period. If the driver drives for seven consecutive days, a trucker may not drive more than 60 hours on duty in the same period. Similarly, driver may not drive more than 70 hours with it in eight consecutive days. This consecutive. Can only restart after a driver takes 34 or more hours off duty.
Considering the HOS requirements, think about what this means for driver completing a two-way trip that requires 10 hours each way. The driver may now be limited to only making 14 total roundtrips within a seven-day period. Prior to the HOS requirement implementation, the same driver could have successfully completed an extra two trips by adding 2.5 hours to the daily driving schedule. Under the new HOS guidelines, the number of trips drivers may make is severely limited.
The Big Picture
The HOS requirements directly revolve around the ELD implementation and vice versa. The ELD will be used to track and monitor drivers existing adherence to HOS regulations, so regulations may adversely affect existing trucking capacity. Shippers need to consider how the ELD mandate and HOS regulations will result in a tightening of the existing capacity upon implementation, and even if the impact is not immediate, it will come to fruition within the next year. Shippers forgoing implementation of the ELD mandate within their fleets could face stiff penalties and other setbacks due to enforcement actions taken by the FMSCA.
Related posts:
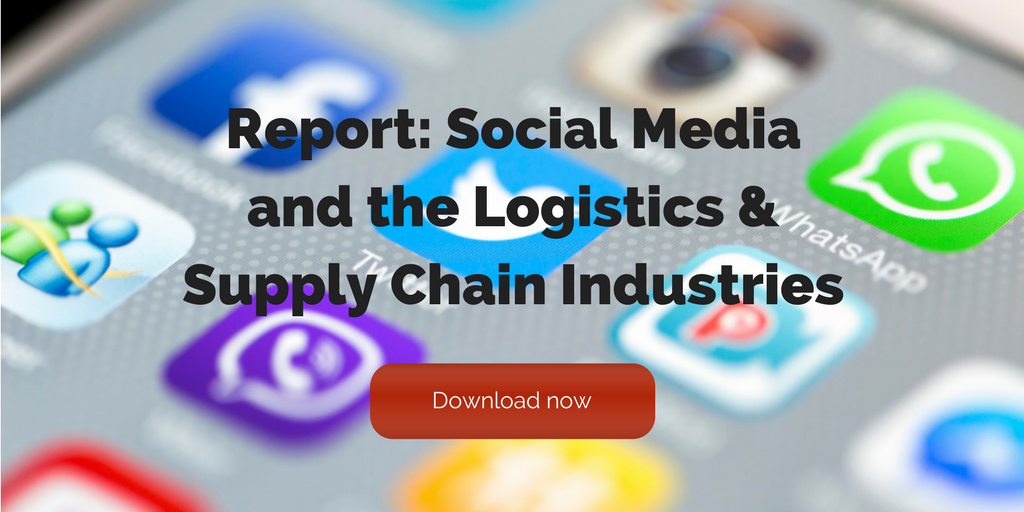
by Fronetics | Nov 28, 2017 | Blog, Manufacturing & Distribution, Marketing, Social Media, Supply Chain
Manufacturers who are active and engaged on Facebook are more likely to introduce product innovation than those who are not.
If you’re killing time during business hours on Facebook, you may actually be onto something valuable. Well, no, — scrolling through your sister-in-law’s vacation album is unlikely to help your business. But recent studies show that staying attuned to user feedback on Facebook may actually help manufacturers create better products.
The practice in question, social listening, is the process of monitoring social media to identify and assess what users are saying about a company, individual, brand, product, or service. We’ve written about how social listening can help your business — you can gain market intelligence and learn how your company, products, and services are being perceived.
But two researchers from the Centre for European Economic Research (ZEW) have taken things a step farther. They studied data from nearly 3,000 German manufacturing and service firms to analyze the role that Facebook plays in the innovation process. What they found was that the probability that a company introduced a product innovation was significantly determined by firms’ adoption of a Facebook page and by the activity by users, measured by both quantity and quality.
The researchers, Irene Bertschek and Reinhold Kesler, discuss their findings in detail in this article published in the Harvard Business Review. So you can skip to the bottom line, we’ve pulled out a few key takeaways for manufacturers:
Negative comments are your friend…
…if you take them seriously.
While you might cringe when you seed a negative customer comment on Facebook, what the researchers found was encouraging: “Surprisingly, only the share of negative user comments was significantly predictive of innovation, perhaps suggesting that customers were helping to steer companies away from bad ideas.”
To make this work for you, it’s important that you pay attention to negative reviews, actively engage with them, and pass along relevant information to the people within your company who can address the issues. For more ideas, check out this post for tips on dealing with negative customer comments.
Simply being on social media isn’t enough — you need to be actively and intelligently engaging.
The study found that companies who were “using keywords in their posts that encourage users to leave feedback were significantly more likely to release a new or improved product.”
In other words, to gain the kind of valuable feedback that allows your products and services to improve, you need to be intelligent about soliciting it. “When developing social media strategies,” suggest Bertschek and Kesler, “companies should not only focus on marketing aspects, but also consider the potential for the firm’s innovation success.”
Related posts:
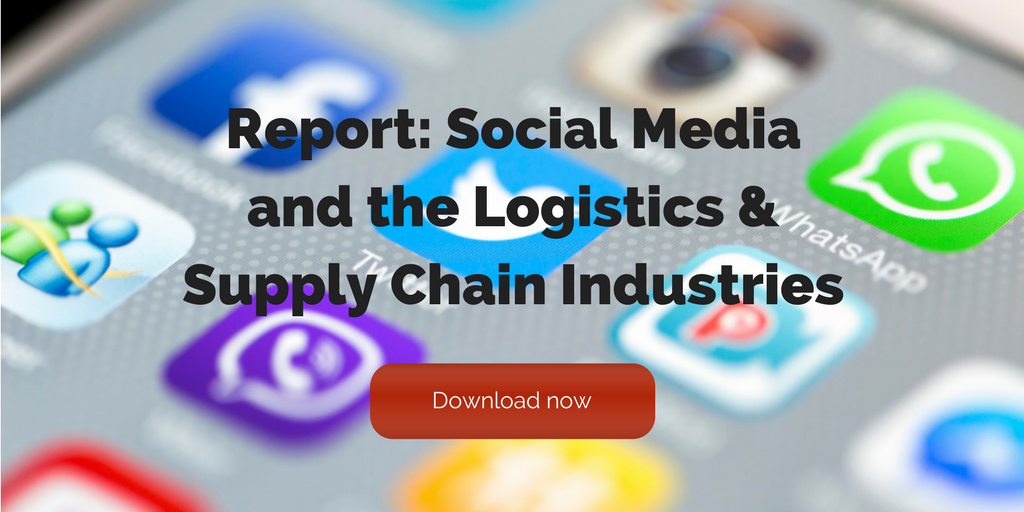