by Fronetics | Jul 14, 2015 | Blog, Logistics, Manufacturing & Distribution, Strategy, Supply Chain
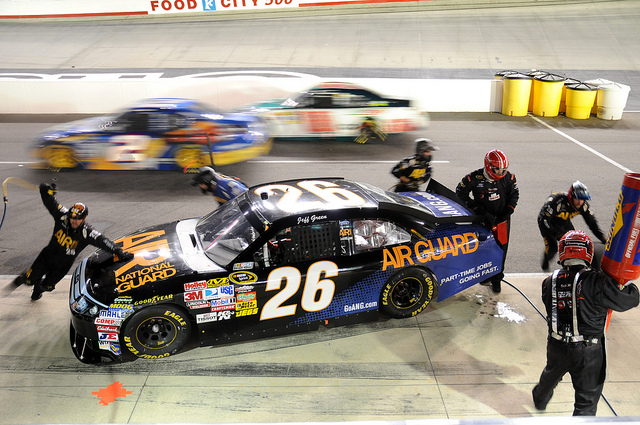
To see lean perfected – study the NASCAR pit. In a matter of seconds, the pit crew has changed tires, wiped down the windshield, filled up fuel, and given the driver a drink of water. Everything is in the right place at the right time. If only every distribution center would run that smoothly. What’s clear is that mastering inventory levels is central to the equation of eliminating waste, but inventory management is becoming a vexing problem for some organizations – compounded by multi-channel distribution, inadequate demand forecasting, and a lack of communication among appropriate parties.
Taking a closer look at the experiences of forerunner companies in their quests to master lean inventory management might just help your company avoid these top three snags.
Failure to Adapt Business Processes
In an effort to reduce merchandise sitting around on warehouse racks, some organizations take lean too far. The problem, in this case, is one of business process rather than software. While management sees the financial impact of cutting inventory, they tend to pay less attention to how it will affect operations. The heads of distribution quite frequently are not even invited to take part in the decision and find out only when fewer cases and pallets show up at receiving. Adapting business processes to involve the managers of procurement, finance, operations, and sales and marketing, is key to maximizing efficiency. In other words, open up the silo by building it in to your formal and informal processes.
Failure to Collaborate
Even with sophisticated demand forecasting models on hand, input from all parties is needed for an accurate assessment of inventory levels. And although demand forecasting can help an organization plan around high-level “what if” scenarios, it may not always be able to break it down on a granular level or take into account the increasing number of variables associated with multi-channel distribution. Collaboration is crucial.
Failure to Align Objectives
Sometimes the answer to the issue of inventory levels is counterintuitive. Even with lean as the driving force, the notion of optimization cannot be left out. In some instances, it makes sense to increase rather than minimize inventory if it will contribute to lowering your overall supply chain costs. Your business and inventory strategies need to align.
Despite the fact that in recent years the lean revolution has hit manufacturing, many organizations, especially retailers and wholesalers, have yet to apply lean principals. And among those who do dabble in lean, the focus tends to be on suppliers upstream rather than adding value to the end customer. As more and more businesses seek to tighten the management of their inventory in order to increase efficiencies, opportunities to address end customer value will emerge. Paul A. Myerson, professor in supply chain management, identifies store- and distribution operations as prime candidates since that’s where the most waste can be cut. He writes:
Distribution is all about optimizing the trade-offs between handling costs and warehousing costs, and maximizing the warehouse’s total cube—utilizing its full volume, while maintaining low materials handling costs and minimizing travel time.
Mastery of lean management principals will come for companies that are both successful in identifying new efficiency opportunities within their existing supply chain and navigating around the pitfalls of businesses that have instituted similar inventory management techniques.
Fronetics Strategic Advisors is a leading management consulting firm. Our firm works with companies to identify and execute strategies for growth and value creation.
Whether it is a wholesale food distributor seeking guidance on how to define and execute corporate strategy; a telematics firm needing high quality content on a consistent basis; a real estate firm looking for a marketing partner; or a supply chain firm in need of interim management, our clients rely on Fronetics to help them navigate through critical junctures, meet their toughest challenges, and take advantage of opportunities. We deliver high-impact results.
We advise and work with companies on their most critical issues and opportunities: strategy, marketing, organization, talent acquisition, performance management, and M&A support.
We have deep expertise and a proven track record in a broad range of industries including: supply chain, real estate, software, and logistics.
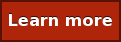
by Fronetics | Jul 6, 2015 | Big Data, Blog, Data/Analytics, Internet of Things, Logistics, Marketing, Strategy, Supply Chain
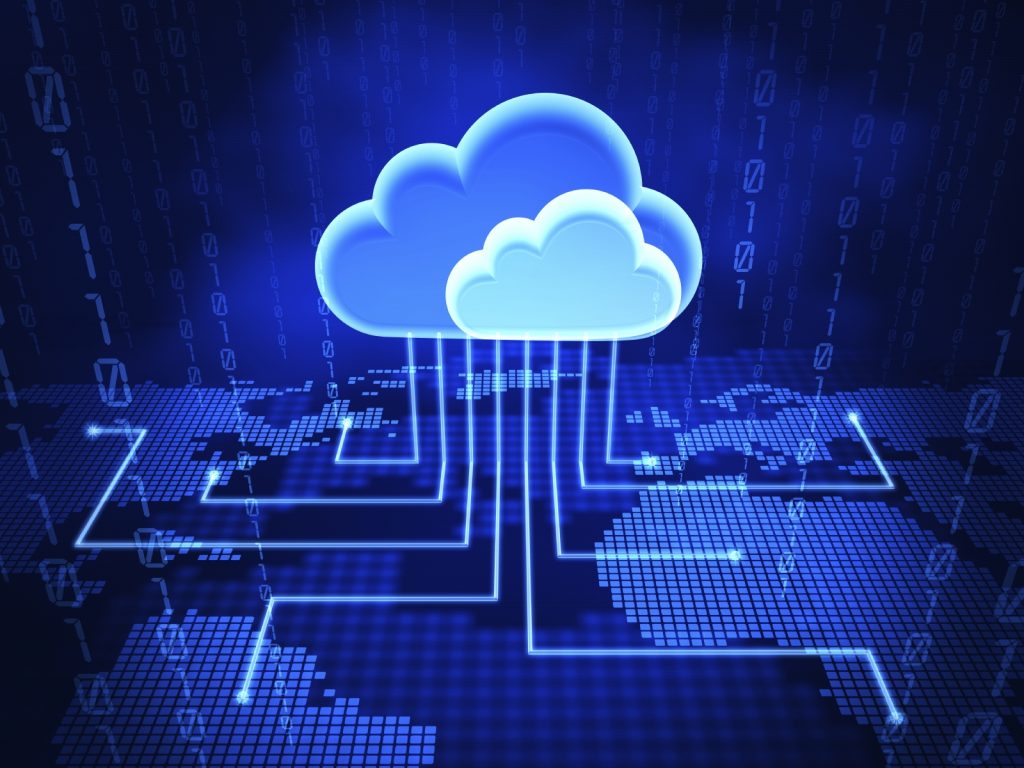
The battle for competitiveness in the cloud.
In this age of radical transformation for supply chains, top companies are tying together prevailing concepts, like big data and the Internet of Things (IoT), with cloud-based computing. Supply chains are being reimagined as digital networks that track not only physical goods, but also people, data, and money. As such, global technology giants continue to invest heavily in cloud computing.
The Chinese e-commerce company Alibaba Group Holding, Ltd. recently announced that it is launching its first international venture – a cloud computing hub in Silicon Valley, proving the fierce competition for market share is stiffening both globally and on the home turf. Notably, all five top-ranked companies listed by the 2013 Strategy & Global Information, Communications and Technology 50 study bet their future on cloud technologies. The companies (IBM, Microsoft, SAP, Oracle, and Cisco Systems) could not, until recently, be perceived as direct competitors, and now they all wield cloud-based portfolios as their competitive weapon of choice.
Analysts note:
The industry leaders are seeking dominant positions, wanting to become the kings of the cloud. As a group, they are putting distance between themselves and the second tier of followers.
For further proof data analytics is driving competition for cloud customers, we can look to a new report by Market & Research that shows data analytics and cloud computing are expected to record a combined growth of 26% annually over the next five years. The implication is that demand is hardly going to lessen as an increasing number of organizations need cloud solutions to manage and store the huge amounts of data that they use to transform manufacturing processes, fine-tune supply chains, forecast customer behavior, and optimize inventories – to name a fraction of potential applications.
And cloud-based computing is even moving the needle of interest in industries that seem inherently averse to making data and information more easily accessible. For example, concerns about data encryption, auditing controls, and transparency have stymied the adoption of cloud-based computing in the financial industry. According to a report by the Cloud Security Alliance, only 28% of American financial institutions have a cloud-based strategy in place, but as a sponsor of the report, Dr. Chenxi Wang, vice president of Cloud Security and Strategy at CipherCloud points out:
Cloud has made solid inroads in this industry with many firms looking to harnessing the power of cloud. There’s plenty of room for growth, particularly for providers who can fill the void for the auditing and data protection controls that are at the top of respondents’ cloud wish list.
Meanwhile, the public cloud services market alone could grow into a $100 billion industry by 2017, according to researcher IDC. Is your business prepared to leverage cloud computing for its supply chain activities? It’s coming, ready or not.
Fronetics Strategic Advisors is a leading management consulting firm. Our firm works with companies to identify and execute strategies for growth and value creation.
Whether it is a wholesale food distributor seeking guidance on how to define and execute corporate strategy; a telematics firm needing high quality content on a consistent basis; a real estate firm looking for a marketing partner; or a supply chain firm in need of interim management, our clients rely on Fronetics to help them navigate through critical junctures, meet their toughest challenges, and take advantage of opportunities. We deliver high-impact results.
We advise and work with companies on their most critical issues and opportunities: strategy, marketing, organization, talent acquisition, performance management, and M&A support.
We have deep expertise and a proven track record in a broad range of industries including: supply chain, real estate, software, and logistics.
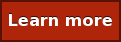
by Fronetics | Jun 23, 2015 | Blog, Logistics, Marketing, Social Media, Strategy, Supply Chain, Transportation & Trucking
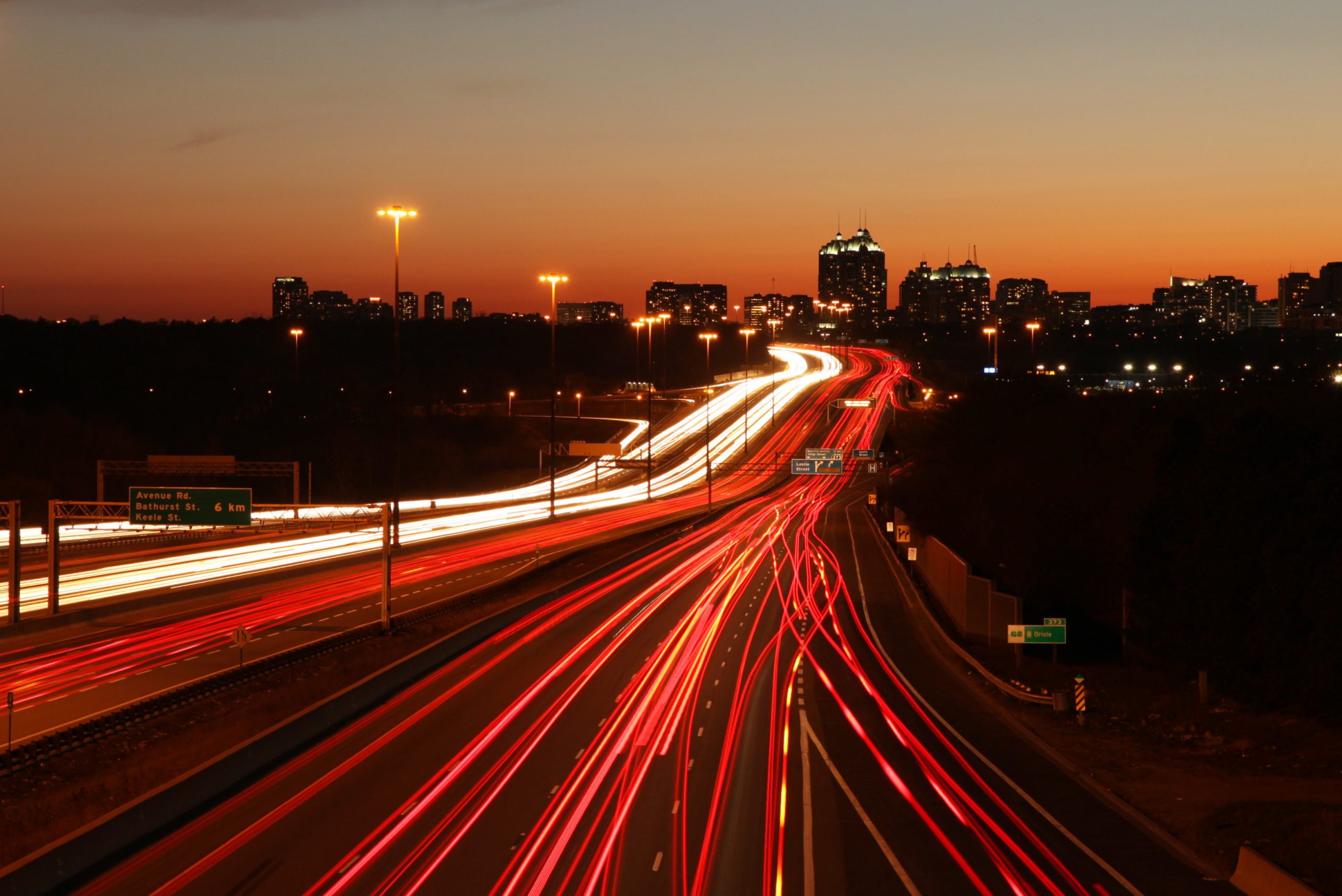
Drew McElroy, founder of the start-up Transfix, is no newcomer to the trucking industry. McElroy was born into the business; his parents owned and operated the freight brokerage Andrew’s Express, affectionately naming it after McElroy.
“I remember listening to my father structure deals. As a kid, it was all utterly confusing to me,” recalls McElroy. “I finally started to get my head around the economics of the business in my teens. From that point on, I became increasingly aware of the industry’s inefficiencies.”
Not long after McElroy graduated college, his father passed away unexpectedly. McElroy, already working for the family business, took over as president. In that time, McElroy successfully increased annual revenues from $4 million to $12 million. While impressive, McElroy still struggled with how the industry traditionally operated. “It was clear that our family business wouldn’t be the platform for world domination,” laughs McElroy. “But I believed that, fundamentally, there was a better way to get things done.”
Determined to build a new foundation based on his belief in “a better way,” McElroy left the family business and set out for San Francisco. He would spend the next year and a half couch surfing and networking in order to gain the expert business and tech insight he needed to plan what would become Transfix. “I knew logistics and I knew trucking, but I knew nothing about venture capital, or how to move from idea to implementation,” says McElroy. “I decided I should try – and try big. If I fail, I fail, but at least I tried.”
In 2013, McElroy was introduced to Jonathan Salama. Salama was among Gilt’s early engineers, and was pivotal in building the flash sale giant’s infrastructure and inventory software. McElroy knew Salama would be key in taking his idea to the next level; Transfix had claimed its co-founders, and its recipe for industry-leading success.
Transfix is a fully automated marketplace that is all about getting things from one place to another. What sets Transfix apart is the company’s platform and approach is vastly more efficient than the traditional approach, and it is much more user-friendly.
Transfix takes the industry’s inefficiencies head on. Transfix is a digital on-demand freight marketplace. It provides industry-leading mobile technologies and location-based jobs offers for independent over-the-road truck drivers, as well as cloud-based management platforms for small carriers and shippers
Here’s how it works:
A customer logs into the Transfix TMS and enters a new shipment. The platform automatically identifies the best driver depending on location, size of truck, etc., sending a load offer alert to the driver or company dispatcher by mobile SMS message or email. The load is accepted by electronic signature, at which point the customer receives automatic notification and the driver becomes fully visible within the customer’s real-time dashboard. Load management from that point on becomes “as simple as Tinder.” Transfix geofences the driver with a five mile radius, immediately alerting Transfix of any issues. Once the load is delivered, the driver is paid within 24 to 48 hours, significantly faster than the industry standard.
Transfix just launched an app (iOS and Android) that is focused on truck drivers. Transfix’s app integrates with the company’s digital marketplace and is driver-centric. The app gives drivers the ability to manage loads, map their itinerary, and manage payments. The app also provides truck drivers with trip planning essentials including the location of showers, ATMs, weigh stations, fuel prices, and weather. The app is free and can be used by anyone with a valid motor carrier number – the driver does not have to associated with Transfix. “Developing this app and making it freely available to all drivers is just the right thing to do,” says McElroy. “Without drivers, this industry would not exist. We need to do right by drivers by making their lives easier.”
Things are moving fast for McElroy and Transfix. Within 15 minutes of updating his LinkedIn profile, McElroy got a call from a logistics Manager at Barnes & Noble and, before he hung up, had freight loads to manage. Fast forward a few months – with Transfix, Barnes & Noble has realized improvements in their processes and has seen their deadhead runs (times driving without cargo) cut by at least 50%.
Transfix has raised close to $2.5 million to date and is already generating several thousand a month in revenue.
McElroy and Transfix are poised for world domination – mind you, a win-win benevolent hegemony – a la Uber.
Fronetics Strategic Advisors is a leading management consulting firm. Our firm works with companies to identify and execute strategies for growth and value creation.
Whether it is a wholesale food distributor seeking guidance on how to define and execute corporate strategy; a telematics firm needing high quality content on a consistent basis; a real estate firm looking for a marketing partner; or a supply chain firm in need of interim management, our clients rely on Fronetics to help them navigate through critical junctures, meet their toughest challenges, and take advantage of opportunities. We deliver high-impact results.
We advise and work with companies on their most critical issues and opportunities: strategy, marketing, organization, talent acquisition, performance management, and M&A support.
We have deep expertise and a proven track record in a broad range of industries including: supply chain, real estate, software, and logistics.
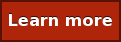
by Jennifer Hart Yim | Jun 18, 2015 | Blog, Logistics, Manufacturing & Distribution, Strategy, Supply Chain
This article is part of a series of articles written by MBA students and graduates from the University of New Hampshire Peter T. Paul College of Business and Economics.
Ben Minerd received his B.S. in Computer Engineering from the University of New Hampshire in 2011 and will be completing his MBA from UNH in May 2015. When not working as a systems engineer, Ben enjoys skiing, hiking, and flying drones.
Some of you technologically curious readers may be familiar with Moore’s Law which predicted that the number of transistors in a dense integrated circuit would double every two years. What all that nerd speak (as a nerd I can use that phrase) boils down to is that the processing capability of electronic chips is increasing at a crazy rate. Like, scary fast.
On the flip side, electronics are really cheap these days. Yes, the $10,000 Apple Watch might be a tad pricey, but I’m talking about the industry as a whole. You can buy a computer that fits in your pocket for $200 that is many hundreds, maybe thousands, of times more powerful than my first computer and I’m one of those whiny millennial youngsters.
How can consumer electronics companies afford to sell their scary fast devices this cheaply? One reason is that the devices are being made by other devices (cue ominous music), as automation and electronics manufacturing are natural complements of each other. But another big factor in the cheap tech equation is the ever-increasing separation of technology development from technology manufacturing.
Contract Manufacturing
Big name companies like Apple, Google, Microsoft, and Amazon are doing less and less of their own widget building these days in favor of contract manufacturing (or CM). Contract manufacturing is essentially the outsourcing of your products’ fabrication and assembly to some other company (who is hopefully better at it than you are).
In theory, using a contract manufacturer should lower your costs and give you access to capabilities that you wouldn’t have access to otherwise. This is especially true of small businesses looking to produce physical goods (versus intangibles like software), where the up-front cost of building your own factory is immense and maybe even a non-starter. Or maybe you’re a big tech company who isn’t good at making hardware (ahem, Google) and you want to stick to your core competencies.
Whatever your reason, contract manufacturing is the unicorn that will slash your costs with its rainbow laser beam eyes. Well, maybe not entirely.
Hidden Costs
To loosely paraphrase Pee-wee Herman, every decision we make in business has a big ‘but’. For the economist reader, you can equate this with TANSTAAFL—There Ain’t No Such Thing As A Free Lunch. One action almost always leads to some other potentially unexpected outcome. Certain people have even gone so far as to say this is always the case (some guy named Isaac Newton).
One of the biggest contributors to hidden costs within contract manufacturing is the loss of control over your production processes. While this might be obvious or even desired, there may be some complications as a result of this new relationship that you hadn’t thought of previously.
Communication is always an important topic, but even more so when it comes to contract manufacturing. Not only may your production team physically reside on the other side of the globe, but things like language, culture, and time zone differences can make it difficult to keep good lines of communication open.
Quickly ramping up or ramping down production to meet changing demand can become a lot more challenging, too. This is partly due to the nature of the shared resources that you are buying access to when you team up with a CM.
A classic example of a culmination of these issues came from Cicso in the early 2000’s, back when out-sourcing was in its infancy. Cisco had been riding the surging wave of growth in the telecommunications industry which starting leading to supplier shortages. Shortly thereafter, the bottom fell out of telecom and Cisco forgot to turn off the contract manufacturing tap. Before long, Cisco’s raw-parts inventory rose by more than 300% from Q3 to Q4 2000, leading to a $2.2 billion write-off of inventory. Wall Street responded as you might expect, causing Cisco’s stock to fall by 50%.
The Human Cost
Perhaps the greatest hidden cost is one that may never make it to your company’s balance sheet: exploitation of workers in the developing countries where many contract manufacturers do business. It’s no secret that the biggest driver behind outsourcing is low labor costs. While it’s not always apples-to-apples to compare a production worker’s wage in China to one in the U.S., by any measurement the difference is more than a factor of 10 (although that number is dropping).
This dirty little secret of the consumer electronics industry came to light in 2012 when it was discovered that Foxconn, the largest electronics CM with over $100 billion in revenue and manufacturer of the Apple iPad, was mistreating some of their workers. Conditions grew so bad that in some cases workers decided to jump to their death rather than survive in that environment.
Bottom Line
Contract manufacturing might very well still be the right choice for you, just keep in mind that you may have more “unknown unknowns” than you had, well, known about. The more you can discuss with your CM candidate up front, the better your relationship will likely be. Also, some of these “gotcha’s” can be planned for in the agreement between you and your CM, so don’t skimp on the up-front work. And remember, there is no unicorn with rainbow laser beam eyes. That I know of.
by Fronetics | Jun 10, 2015 | Blog, Logistics, Marketing, Social Media, Strategy, Supply Chain
Fronetics Strategic Advisors conducted a survey focusing on social media and logistics and supply chain companies. Respondents shared information on their social media use, motivation, preferences, benefits, and challenges. One-hundred percent (100%) of respondents reported that they have used social media for five years or less, indicating that social media is a relatively new strategy for logistics and supply chain companies. Mirroring other industries, including those in Fortune 500 status, social media is playing an increasingly important role in company branding, marketing, and client engagement.
For the current state of social media and logistics, here is an infographic that summarizes many of the key points from the full report.
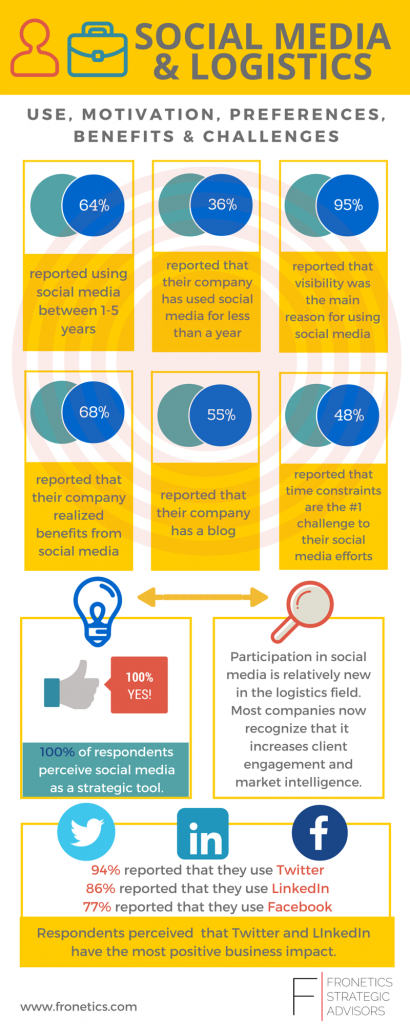
by Fronetics | Jun 9, 2015 | Blog, Logistics, Marketing, Social Media, Strategy, Supply Chain
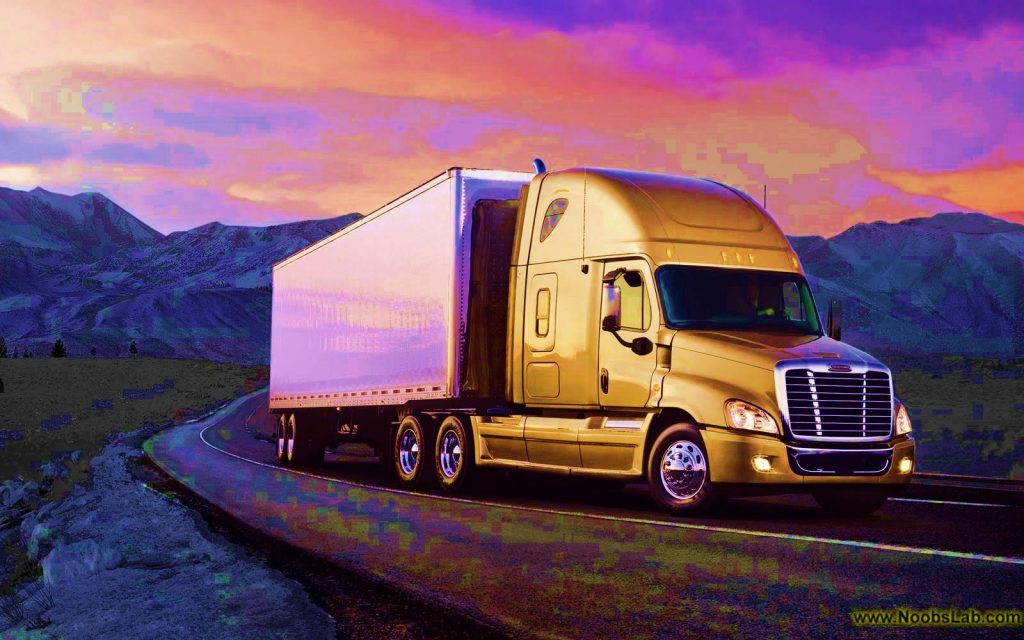
Transfix is poised to disrupt and transform the trucking industry.
Uber, the on-demand driver for hire mobile service, has come to stand for disruption. The company has not only transformed the taxi industry, it has changed everything. Uber, Aaron Levie notes, is a “lesson in building for how the world *should* work instead of optimizing for how the world *does* work.” NY-based start-up Transfix is doing just this. With the launch of the company’s new app, Transfix is poised to disrupt the trucking industry.
The trucking industry is huge. Valued at $800 billion, the industry moves the majority (67%) of freight tonnage in the US. To move this volume of freight, more than 3 million trucks log close to 100 billion miles annually. It is, therefore, not surprising that “truck driver” is the most common job across the US. What is surprising is that the industry is riddled with inefficiencies. One of the greatest inefficiencies has to do with needless miles. Drew McElroy, co-founder of Transfix, estimates that U.S. commercial trucks drive 19 billion needless miles each year. That’s a lot of needless miles.
Together, the industry’s inefficiencies have a significant impact not just on the bottom line, but also on the cost of goods, the environment, our country’s infrastructure, traffic, and on the truck drivers themselves.
Transfix takes the industry’s inefficiencies head on. Transfix is a digital on-demand freight marketplace. It provides industry-leading mobile technologies and location-based jobs offers for independent over-the-road truck drivers, as well as cloud-based management platforms for small carriers and shippers.
Transfix’s app integrates with the company’s digital marketplace and is driver-centric. The app gives drivers the ability to manage loads, map their itinerary, and manage payments. The app also provides truck drivers with trip planning essentials including the location of showers, ATMs, weigh stations, fuel prices, and weather.
The app is available for iOS and Android.
Barnes and Noble is one of Transfix’s early adopters. According to McElroy, Barnes and Noble has realized improvements in their processes and has seen their deadhead runs (times driving without cargo) cut by at least 50%.
Transfix co-founders Drew McElroy and Jonathan Salama have identified how the trucking industry should work and have provided industry stakeholders with the tools to make it happen. Transfix is poised to disrupt and transform the trucking industry. With Transfix, we are witnessing the Uberfication of trucking.