by Fronetics | Sep 17, 2019 | Big Data, Blog, Data/Analytics, Internet of Things, Robotics & Automation, Supply Chain
Machine learning is shaping the future of supply chain and logistics management, improving accuracy, speed, scale, and more. Here’s how.
Highlights:
- Machine learning refers to an application of artificial intelligence that lets systems learn and improve automatically based on experience.
- Experts predict that 95% of supply chain planning vendors will rely on supervised and unsupervised machine learning for their solutions by 2020.
- When paired with the Internet of Things, machine learning can provide cost savings around $6 million per year.
When it comes to the future of the supply chain, machine learning is one of the most exciting applications of artificial intelligence (AI) technology out there today. Machine learning is a mode of data analysis that provides systems with the ability to learn and improve automatically from experience, without being specifically programmed.
Gartner recently projected that by 2020, 95% of supply chain planning vendors will rely on supervised and unsupervised machine learning for their solutions. Furthermore, it isn’t just expert predictions that demonstrate the impact and potential of machine learning for the supply chain. Amazon, for example, is using machine learning to improve accuracy, speed, and scale for its Kiva robotics, and DHL relies on machine learning to power its Predictive Network Management system.
So, what is it about machine learning that makes it ideally suited to meet the challenges commonly faced by supply chain companies? The answer lies in the fact that machine learning algorithms are brilliant at detecting patterns, anomalies, and predictive insights. This makes it the ideal technology to help supply chain companies forecast error rates, reduce costs, improve demand planning productivity, and increase on-time shipments.
Here’s how these remarkable technologies are already revolutionizing supply chain management.
7 ways machine learning is improving supply chain management
1) Logistic solutions
Particularly when it comes to resource scheduling systems, machine learning algorithms are driving the next generation of logistics technologies. An April 2019 report from McKinsey predicts that “machine learning’s most significant contributions will be in providing supply chain operators with more significant insights into how supply chain performance can be improved, anticipating anomalies in logistics costs and performance before they occur.”
2) Internet of Things
The Internet of Things (IoT)’s sensors, intelligent transport systems, and traffic data generate a tremendous variation in data sets. Machine learning has the potential to deliver increased value by analyzing these data sets, thereby optimizing logistics and ensuring that materials arrive timely.
Additionally, machine learning can reduce logistics costs by uncovering patterns in track-and-trace data captured through IoT-enabled sensors. A December 2018 study by Boston Consulting Group determined that pairing machine learning (specifically Blockchain) with the IoT can contribute to cost savings of $6 million per year.
3) Preventing privileged credential abuse
A recent article in Forbes points to privileged credential abuse as “the leading cause of security breaches across global supply chains.” Machine learning can prevent these abuses by verifying the identity of anyone requesting access, as well as the context of the request and, most importantly, the risk associated with the access environment.
4) Reducing fraud potential
In addition to reducing risk and improving product and process quality, machine learning can reduce the potential for fraud in the supply chain. For example, machine learning startup Inspectorio is a solution to the problems “that a lack of inspection and supply chain visibility creates, focusing on how they can solve them immediately for brands and retailers.” Their algorithm provides insights that instantaneously reduce the risk of fraud.
5) Reducing forecast errors
According to a recent report from Digital/McKinsey, “Lost sales due to products not being available are being reduced up to 65% through the use of machine learning-based planning and optimization techniques.” The same report observes that “inventory reductions of 20 to 50% are being achieved today when machine learning-based supply chain management systems are used.”
6) Detecting inconsistent supplier quality levels
Machine learning can help manufacturers combat one of the biggest problems they face today, namely a lack of consistent quality and delivery performance from suppliers. These technologies can quickly detect and address errors, as well as determine highest and lowest performing suppliers.
7) Preventative maintenance
Preventative maintenance is a tremendous strategic asset for the supply chain. And, when paired with machine learning, it “allows for better prediction and avoidance of machine failure by combining data from the advanced IoT sensors and maintenance logs as well as external sources,” according to the same Digital/McKinsey study mentioned above. Not only that, “asset productivity increases of up to 20% are possible, and overall maintenance costs may be reduced by up to 10%.”
The bottom line: machine learning is reinventing supply chain management
Not only has machine learning already realized tremendous value for the supply chain, but the very nature of this technology means that the possibilities are virtually endless. Algorithms continue to become more sophisticated, and, as new challenges arise, machine learning grows and evolves to meet them.
Related posts:
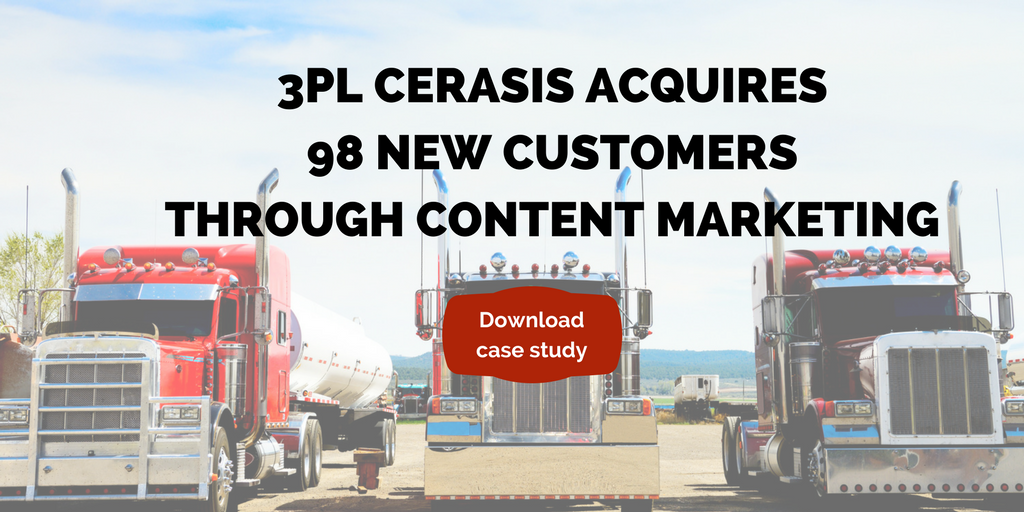
by Jennifer Hart Yim | Feb 14, 2019 | Blog, Content Marketing, Internet of Things, Logistics, Marketing, Supply Chain
Rogue Ales believes that their “Ground to Glass, Grow your Own Revolution” is a key tenet to their success. The company leverages the Internet of Things (IoT) to ensure that their supply chain is able to deliver the highest-quality ingredients to their breweries just in time.
Highlights:
- Consumer desire for freshness and high quality is influencing the beer brewing industry.
- Rogue Ales owns Rogue Farms giving the brewery a unique advantage in being able to produce specialty ingredients.
- The Internet of Things has enabled Rogue to capture and act on the data surrounding their supply chains.
Rogue Ales, headquartered in Newport, OR, is an alcoholic beverage company founded in 1988 that produces beer, wine, cider, and distilled spirits. Their ales have won over 1,800 awards at various brewing competitions.
Rogue’s brewing operation is unique in that the company’s subsidiary, Rogue Farms (founded in 2008), grows all of the ingredients used. The company believes that their “Ground to Glass, Grow your Own Revolution” is a key tenet to their success. Rogue Ales leverages the Internet of Things (IoT) to ensure that their supply chain is able to deliver the highest-quality ingredients to their breweries just in time.
The trend toward freshness
According to AT Kearney, 93% of consumers consider freshness to be the most important criterion when purchasing foods. According to the USDA, the sale of organic foods in the U.S. has more than tripled from approximately $12B in 2005 to over $35B in 2015 (data for 2016-2018 was not immediately available).
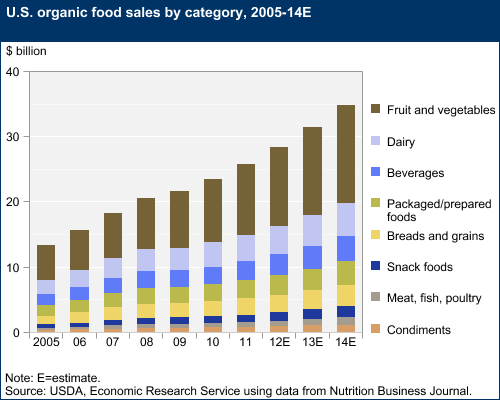
Consumer desire for freshness and high quality is influencing the beer brewing industry. According to the American Brewers Association, the number of craft breweries in the United States has increased from 122 in 1973 to over 6,300 in 2017.
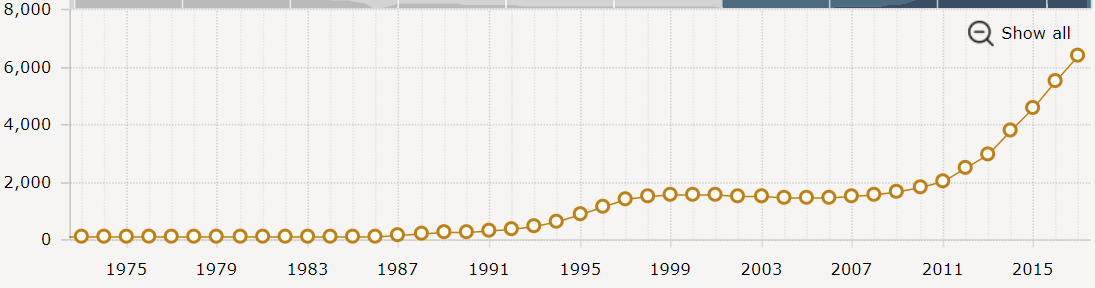
As the competition between breweries intensifies, brewers are constantly looking for key ways to differentiate their beers from their competitors in this $111.4B market. Most beer sales are through microbreweries (defined as a brewery producing less than 15,000 barrels per year and at least 75% of beer sold off-site via distributors or wholesalers). Rogue Ales has made freshness a key value-add differentiator for its brand, selling over 325,000 gallons in 2016. In a Market Watch article, Rogue’s president, Brett Joyce, says:
What it means is that we have to get better all the way around. The quality has to go up. Just having products isn’t enough. You better have a strategic plan to go to market, retailer support, good follow-up and good sales people. It’s a real business now.
With the establishment of Rogue Farms in 2008, Rogue began producing their own ingredients, breaking tradition with most breweries, who acquire ingredients from traditional wholesalers. Rogue has a 52-acre hop farm, located approximately two hours from the brewery, where it produces its entire hop supply. Rogue states that:
Growing hops is an expensive and time-consuming endeavor, but it also helps to guarantee our supply and quality while allowing us to keep our Brewmaster, John ‘More Hops’ Maier, happy with unique, aromatic hops.
The control Rogue Ales has over Rogue Farms gives the brewery a unique advantage in being able to produce specialty ingredients for its core and specialty beers. At Rogue Farms, Rogue grows or produces:
- 10 varieties of hops
- Two varieties of malting barley
- Rye
- Pumpkins
- Marionberries
- Jalapeños
- Honey
The challenges of using fresh “wet” hops in beer
A basic beer recipe only has four ingredients: malted barley, water, hops, and yeast. Of these ingredients, hops are the most difficult to source, store, and transport due to their perishability. Most brewers use pelletized, dried, hop pellets. Rogue uses fresh (or “wet”) hops in their ales, harvested from Rogue Farms. Fresh hops give their beer a fresher taste, as the hops’ aromatic qualities are not damaged by drying and pelletization.
Fresh hops, once harvested, must land in a brew vat within 12 hours and cannot be exposed to excessive heat, air, or humidity during transport or their volatile aroma compounds will degrade and produce aromas of “skunk” and “compost”. To ensure the highest quality of hops, Rogue has turned to technology to ensure that its supply chain is delivering the freshest possible hops to the brewery.
Using the Internet of Things to build quality into Rogue’s supply chain
The vertical integration of Rogue Ales and Rogue Farms gives Rogue a unique advantage in being able to leverage new technologies to ensure it sources the highest quality ingredients possible directly from their farm to their brewery. Rogue Ales uses Intel’s Connected Logistics Platform to manage its hops supply chain. Intel’s platform is a logistics management solution that couples Internet of things (IoT) devices with a cloud-based data analytics system. These IoT devices are one-time-use sensor tags that attach to shipments and collect data (e.g. temperature, humidity, location, etc.). This data is sent over a proprietary wireless protocol to a central server where the data is aggregated and analyzed in real time.
[bctt tweet=”The Internet of Things has enabled companies like Rogue to capture and act on the data surrounding their supply chains. Companies are able to make smart decisions that bring cost savings and flow directly to their bottom line.” username=”Fronetics”]
The system tracks shipments and collects data during every facet of the supply chain, ensuring that quality thresholds are maintained and any problems with the shipped goods can be immediately corrected (for example, if one of the trucks runs into traffic, the others can be intelligently rerouted). It is estimated that 30% of all perishable products shipped in the United States become spoiled during their journey from the farm.
After the wet hops are picked, Rogue attaches three trackers to each shipment: at the top, middle, and bottom of the bale of hops. These trackers measure temperature, humidity, and location. Rogue can ensure that the hops have been kept in the proper environment and that they have not spent too much time in transit.
If a shipment does not meet quality standards, it can be discarded before it is used in a beer batch, reducing waste and ensuring that Rogue does not waste its precious brewing capacity brewing beer that will later need to be dumped for quality reasons. The location of the shipment is updated every ten minutes, and once the hops have reached the halfway point, Rogue starts the brewing process. This ensures that the hops arrive just in time and go directly from the truck into the brewing kettle.
The Internet of Things has enabled companies like Rogue to capture and, more importantly, act on the data surrounding their supply chains. Companies are able to make smart decisions that bring cost savings and flow directly to their bottom line.
This article was written by Zachary Richards, an MBA student at the Peter T. Paul College of Business and Economics at the University of New Hampshire. Zach is a Software Engineer at Pegasystems, Inc., where he specializes in back-end Java development, data structures, and agile development practices. He graduated from Worcester Polytechnic Institute in 2016 with a B.S. in Computer Science.
Related posts:
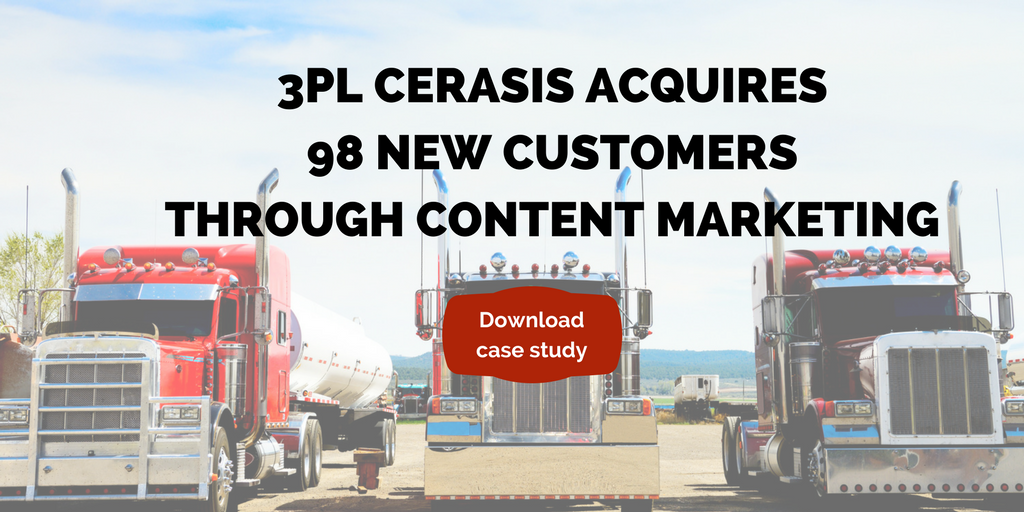
by Elizabeth Hines | Jul 24, 2018 | Blog, Current Events, Data/Analytics, Internet of Things, Logistics, Manufacturing & Distribution, Supply Chain
Automation in manufacturing can help create more, better paying jobs. But two leading economists have examined real-world data and concluded that the robots may be winning after all. Is it true?
Last year I wrote about artificial intelligence (AI) and the potential loss of American jobs. At the time, I thought; “Yes, people will lose jobs — that is inevitable. Automation, however, will create many more.”
Automation would create leaner, more efficient operations. Efficiency facilitates new market opportunities and business growth, which in turn would allow for expansion and job creation.
It felt like a good argument! And I wasn’t alone. If one looks at media coverage from last year, one can find plenty of references to “beating the robots.”
There was a palpable feeling, an energizing hope, that automation would, in fact, ultimately create more, better paying jobs. And these new jobs wouldn’t be the low-skill positions of their pre-automation predecessors, but rather higher-paying opportunities operating new technology and supervising automated processes.
In a paper last year, two of the most respected researchers on the subject said it was likely that increased automation would create new, better jobs, so employment and wages would eventually return to their previous levels.
It all seemed positive.
This year’s news
But wait. The same researchers — Daron Acemoglu of M.I.T. and Pascual Restrepo of Boston University — published an updated study that has gained a tremendous amount of attention. It was covered in-depth by the New York Times, with the title: Evidence That Robots are Winning the Race for American Jobs.
Sadly, their study appeared to be the first “to quantify large, direct, negative effects of robots.”
In referencing the difference in prognosis from last year to this year, the NYT article noted that the older paper was “a conceptual exercise” and the new study “uses real-world data — and suggests a more pessimistic future.”
I thought, I’m going to have to write a new article. It was tentatively titled, “I Take It Back: The Data Says the Robots May Be Winning.”
But as I sat down to write, something just didn’t add up. How did all this jive with the latest employment news? Only days ago, unemployment rates hit 3.9%, a rare low, mimicking rates we haven’t seen since 2000.
Taking in the whole picture
As I looked further into the study, I found that it covered 1990-2007, a lengthy but rather unique time in our economic history. The years from 1990 to 2007 saw a dotcom boom and burst. (Just for reference, unemployment rates rose sharply in 2009 and 2010, but have been on a steady decline since then.)
The robot vs. man study said that robots were to blame for up to 670,000 lost manufacturing jobs between 1990 and 2007. I’m not arguing with the study.
But they then go on to conclude the following: The numbers will rise because industrial robots are expected to quadruple. And from where I sit in 2018, I simply don’t see the facts to support that assumption.
Let’s look at manufacturing specifically. Are machines and automation blowing up the manufacturing sector? Well, yes and no.
Certainly manufacturing jobs have had a sharp decline over the last 20 years; that’s undeniable.
But since 2000, their percentage of the overall job market has held generally stable between 8 and 9%. And current employment statistics for 2018 show increases in the manufacturing sector.
Now, I’m not suggesting manufacturing jobs are “roaring back” by any stretch. But a positive trend line is … well … positive. The prognosis of a “pessimistic future” just doesn’t seem widely supported yet by the facts. Time, as always, will tell.
Of course, economists warn that employment rates aren’t the whole picture. While they may mimic that of 2000, they warn that the economy isn’t the same and that it is concerning that wages have been slow to rise even though unemployment has fallen.
From what I see now, however, I still feel optimistic that AI and automation will create leaner, more efficient operations that will, in turn, create new (even if different) jobs. To me, it still looks like the ones winning from the increasing technological advances in the manufacturing industry are, in fact, we humans.
This post originally appeared on EBN Online.
Related posts:
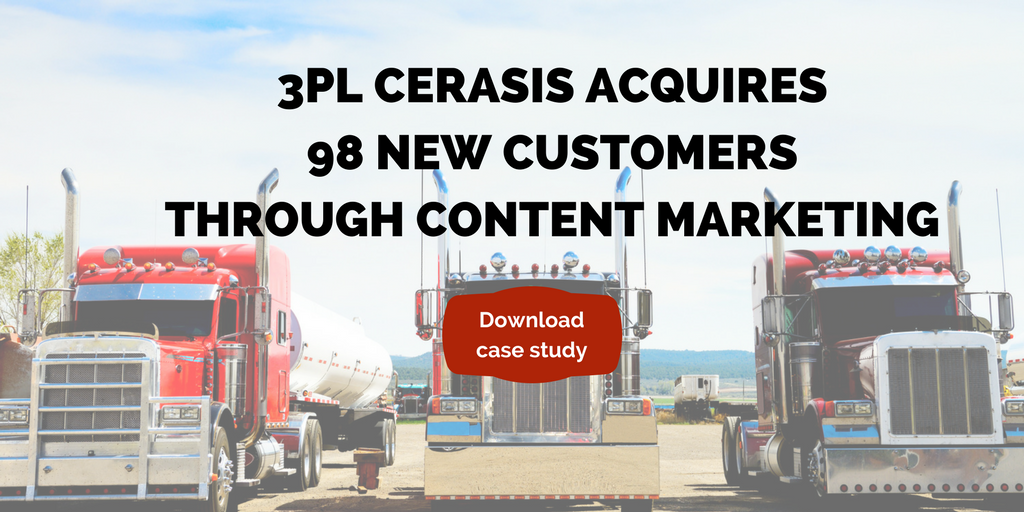
by Jennifer Hart Yim | Jun 5, 2018 | Blog, Content Marketing, Data/Analytics, Internet of Things, Logistics, Manufacturing & Distribution, Marketing, Strategy, Supply Chain
The Internet of Things is revolutionizing manufacturing and supply chain. Is your organization prepared?
This article is part of a series of articles written by MBA students and graduates from the University of New Hampshire Peter T. Paul College of Business and Economics.
“If you think that the internet has changed your life, think again. The Internet of Things (IoT) is about to change it all over again!”
This famous quote from co-founder of Aria Systems, Brendan O’Brien, sums up the significant role that the Internet of Things is playing now, and also its unlimited potential in the near future. The technology can be defined as the networked connection of physical objects.
[bctt tweet=”More than 1.2 trillion items on earth now have the potential to join the IoT network, but less than one percent of them are connected to the internet.” username=”Fronetics”]
Since 2014, Internet of Things is no longer a new term for most companies. However, this is just the beginning of the IoT revolution. More than 1.2 trillion items on earth now have the potential to join the IoT network, but less than one percent of them are connected to the internet.
And if we look at estimated worldwide spending on IoT through 2020, manufacturing, logistics and utilities are the industries that will spend the most money on this technology. This is partially due to their reliance on supply chain management. In addition, their supply chain networks are usually much more complex then companies from other industries.
The real value of Internet of Things is the data captured during the process, instead of the devices themselves. Nowadays customers are expecting higher quality products delivered in the shortest amount of time. That trend requires companies to have a more efficient supply chain in order to fulfill the demand. Brand matters less as it did a decade ago.
How to move products from the factory to consumers’ hands more efficiently becomes the new challenge for all players across all industries. Meanwhile, saving cost, adding asset velocity through enhanced transparency, as well as visibility are also the potential benefits by embracing the Internet of Things.
There are a number of IoT practices in supply chain:
Operational efficiency
Warehouses always play a vital role in a supply chain. It is also an area where IoT technology shows its magic by providing competitive advantages through data acquired from sensor networks. And generally, it can be improved from four aspects:
- Manufacturing maintenance – Sensors and robots linked to the internet increase up-times, reduce operational costs, and improve overall service quality. By visualizing and collecting data — such as temperature and equipment malfunction — managers are able to see and control operations on the floor in a real-time manner. Data collected in the IoT process can also be used in setting alerts for predictive maintenance. It works like HP Instant Ink, which will automatically order new ink when you the printer is about to run out of the old one.
- Inventory forecasting – As Vice President of IT at DHL Supply Chain Javier Esplugas said: managers no longer have to wait for weeks or months to get a report to have an understanding what happened during the last quarter. Instead, managers can make decisions on things that are happening now. Even companies using a 3PL can closely monitor the distribution centers and warehouses so that they can avoid prolonged cycle times and receive warnings in advance.
- Asset tracking – In a warehouse, scales and visual sensors can alert workers about fulfillment needs. The IoT also reduces human error for inbound and outbound records, requiring less human capital for one warehouse.
- Freight transportation – Logistics also holds a great potential for IoT networks. Today, sensors can track and monitor a container in a freighter in the middle of the sea or on a cargo flight. In the future, IoT will also be used to provide a more secure freight transportation environment. In 2016, around $3.7 million worth of consumable goods was stolen in cargo thefts in the U.S. The number of incidents reported in 2016 was 692. Through IoT technology, owners will have access to real-time information on the movement of goods.
Real-world examples
We’ve already seen leading car manufacturer BMW using IoT to improve its product lines efficiency. That is the most basic level of optimization within a warehouse.
A more thorough example would come from DHL. This global company actively involves IoT in different stages of its logistics process.
The journey of a package at DHL starts at the time it’s received by a carrier. By scanning the bar code or QR code on the package, it is formally recorded in the company’s system.
When the package arrives at the warehouse, basic information such as height, weight, and goods type will be collected as it enters the gate, providing accurate inventory control for workers. Sensors in the facility will be constantly monitoring the condition, as well as location of the items, giving workers a visual graph on the computer. When the package leaves the warehouse or sorting center, sensors built in the gate will collect information again for outbound items. Cameras attached to the gateways could also be used for damage detection.
They call the warehouse with all those systems the Smart Warehouse. And now they are testing the solution in multiple locations.
Due to the fact that DHL has been focusing on global logistics, its activities always include freight transportation. To reduce the inventory delays as well as the cost of stolen goods, DHL expects to set up location and condition monitoring through IoT. Ultimately, transport visibility and security functions will be enhanced.
What’s more, DHL’s Supply Chain segment is developing a software that gives clients a way to manage global supply chain risk by providing alternatives. The tool can find other optimized solutions by leveraging data collected from connected objectives.
Last-mile delivery
It makes a lot of sense to introduce IoT to warehouse management or freight transportation. However, for last-mile delivery, it can be a very different story. This final part is highly dependent on labor.
Carriers use data collected from vehicles for road condition in order to optimize the route. Before delivery, they would send notification to the end-customer, who has the choice to either accept the scheduled delivery time or re-schedule the delivery.
The future
By the year of 2020, the number of devices connected to the IoT will be over 50 billion. But that’s still just 3 percent of the number of all things on earth.
JDA’s Intelligent Manufacturing Survey discovered that 57 percent of manufacturers were going to incorporate IoT into their digital supply chain strategy. However, according to an Accenture report, up until the beginning of 2017, 88 percent of manufacturing executives were not prepared to adopt the technology. This is going to benefit companies that are willing to be the first movers and create barriers for the rest to catch up.
So, is your company ready for the digital revolution?
About the author
Xiaoxue Liu, originally from China, is a current MBA student at University of New Hampshire, with a huge interest in supply chain digitalization.
Related posts:
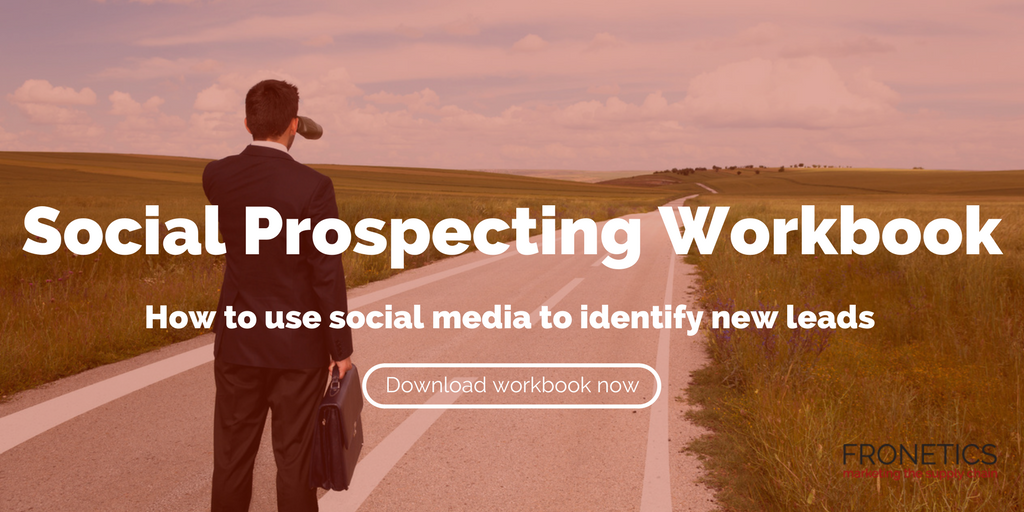
by Fronetics | Mar 23, 2017 | Big Data, Blog, Current Events, Data/Analytics, Internet of Things, Logistics, Manufacturing & Distribution, Strategy, Supply Chain, Talent, Warehousing & Materials Handling
Our series by MBA students and graduates at Peter T. Paul College of Business and Economics highlights some of the most pressing issues in supply chain management today.
A few years ago, the Wall Street Journal called supply chain management the “hot new MBA.” Many universities have been introducing related degree programs, majors, and concentrations in response to a growing demand for new hires with supply chain expertise. Graduates of these programs are heavily recruited by employers, which is helping to attract ambitious, young talent to the industry.
Fronetics had the opportunity to collaborate with some of these rising stars by inviting MBA students from the University of New Hampshire Peter T. Paul College of Business and Economics to author guest posts on our blog. They covered a variety of pertinent topics, from the Internet of Things and Big Data to pet food and Chipotle. Their pieces are summarized below.
In the coming weeks, we’ll be partnering with another MBA class at UNH to author a second series of posts covering some of the most pressing issues in supply chain management today. Make sure you receive our blog e-newsletter (sign up to the right) or follow us on social media so that you don’t miss out.
Steve Mondazzi writes about how the Internet of Things is now being used to improve factory workflow, increase material tracking, and optimize distribution to maximize revenues. Everything from turning lights on and off to security systems can be controlled from your smartphone, and that technology is moving to the manufacturing industry. Mondazzi examines Mark Morely’s theory that the IoT will impact the industry in three main ways: pervasive visibility, proactive replenishment, and predictive maintenance. He also explores hurdles to implementation — such middleware and a common protocol for businesses regarding IoT. Read article
Mikayla Cadoret focuses on the barriers to entry in the pet food industry. New brands have three options: manufacture product themselves, choose a co-packer who uses a private label, or choose a co-packer who will manufacture the food to the specifications of the brand. She discusses the challenges of those choices as well as high-profiles recalls resulting from co-packer error. She recommends strategies that companies implement to keep tabs on co-packers’ sourcing and manufacturing. Read article
Nicole Brooks explores Amazon’s mission to be earth’s most consumer-centric company. The e-commerce giant not only offers low prices, it also exceeds consumer expectations and shifts industry standards with benefits like same-day shipping. Brooks examines Amazon’s biggest technological assets, and looks forward to up-and-coming innovations like Kiva robots in warehouses, drones, Prime Air, and Amazon Business. Read article
Corey Ducharme discusses the traditional four-step problem-solving method and how it isn’t effective in solving needle-in-a-haystack issues resulting from limited business resources. Six sigma can address these issue with its six-step process. With the addition of an analysis phase, solutions become more effective, leading to better results and higher revenue for businesses. Read article
David Chadwick explores whether advances in radio-frequency-identification technology (RFID) will render humans obsolete in the supply chain. RFID could dramatically improve efficiency and accuracy in warehouses by reducing the need for human interaction. But it is uncertain to what degree this technology will be implemented in all aspects of supply chain management. Read article
Dario Cavegn discusses how increasing size and complexity of global supply chains open them up to increased risk. Supply chain disruptions can vary from insignificant to extremely threatening. But regardless of disruption size, supply chains can remain resilient with a business continuity plan, which acts as a road map to continue operations during or after a disruption. Cavegn outlines the development process from analysis to feedback. Read article
Josh Hutchins explores the limitations of big data. The real value lies in the analytics applied to the data. As an example, Solid Gold Bomb drove its prospering t-shirt business into the ground from an oversight and misapplication of data. Hutchins concludes that companies must have an intimate understanding of big data applications to avoid a similar fate. Read article
Michael Hickey discusses third-party logistics providers as a resource for a company’s operations arm. 3PLs offer an outsourcing opportunity for order fulfillment, inventory and warehouse management, as well as transportation of finished goods. But businesses should ask themselves these questions when determining whether a 3PL is a good fit for their needs. Read article
Sarah Hebert discusses Chipotle’s high-profile pork-supplier conundrum. The chain cut their pork supply by a third due to a supplier’s violation of their animal welfare standards. While this affected sales by 7-8%, Chipotle embraced the situation as a strategic PR opportunity. But behind the scenes, the company was scrambling to address long-term supply concerns associated with its rapid growth. Hebert asks, “At what point do you scale back the growth for the sake of maintaining brand integrity?” Read article
Connor Harrison discusses GM’s recall of 2.6 million vehicles. The company’s faulty ignition switches were linked to 13 deaths and 31 front-end collisions, but the company managed to contain the crisis. Harrison examines the root causes of the issue, including faulty ignition switches from GM’s supplier Delphi, a strained business relationship, and legal complications. Read article
Related posts:
by Fronetics | Aug 30, 2016 | Blog, Internet of Things, Logistics, Strategy, Supply Chain
New research shows how supply chain and logistics companies currently are using the Internet of Things and how they plan to expand use in the future.
The Internet of Things is already here — monitoring our footsteps, heartbeats, lighting, home temperature, and environment. And it will continue to expand at a rapid rate. Frost & Sullivan estimates that connected objects will total more than 50 billion by 2020. Morgan Stanley says 75 billion. Either way, it’s clear that the number of internet-connected devices is growing exponentially.
For the supply chain and logistics industries, this is exciting news The transparency and end-to-end visibility afforded by the IoT creates new opportunities that businesses can leverage in order to optimize supply chains and generate value.
Eft, a logistics and supply chain solutions provider, recently polled 600 supply chain decision-makers to understand their “existing and future plans for leveraging the IoT within their operations.” The results offer an interesting picture of the changing relationship between supply chain and logistics and the Internet of Things.
Key findings include:
- 41% have an IoT solution in place.
- 87% plan to expand use of the IoT.
- 61% are analyzing less than half of their IoT data.
What kind of information are companies looking to gain with the IoT?
- Location
- Security
- Temperature
- Speed
What are companies hoping to achieve?
- To improve customer service with better information
- To provide customers with more frequent updates on shipment pick-up or delivery
- To improve speed, delivery timeframes
What types of solutions are companies using?
- Bar codes
- Data logger
- IoT sensor and monitoring technology
In which area are you hoping to improve operational visibility the most?
- 80% land shipments
- 50% air shipments
- 33% sea shipments
What level of threat is cyber security to your IoT strategy?
- 17% major threat
- 47% moderate threat
- 32% minor threat
- 5% non threat
What is the primary purpose of your IoT network?
- 59% alarms and real-time monitoring
- 41% optimization and prediction
Read the full report to get even more insight into how the supply chain and logistics industries are engaging with the IoT.
Related posts: