by Jennifer Hart Yim | Feb 28, 2019 | Blog, Strategy, Supply Chain, Warehousing & Materials Handling
If you want to keep your customers satisfied, you need to keep things moving in your facility. Use these tips to keep up the pace and increase warehouse and distribution center efficiency.
Highlights:
- Speed has become the name of the game when it comes to staying competitive in the global supply chain.
- Keep your priorities in mind when organizing your warehouse, including your fastest-moving products.
- Digital technology can take the guesswork out of inventory and warehouse management with employees scanning products every step of the way.
This guest post was written by David Maddenfor Argentus Supply Chain Recruiting, a boutique recruitment firm specializing in Supply Chain Management and Procurement.
Things can always be faster when you work in a warehouse or distribution center. Speed has become the name of the game when it comes to staying competitive in the global supply chain. Major players like Amazon and Walmart have distribution centers all over the world, pumping out packages at lightning speed.
If you want to keep your customers satisfied, you need to keep things moving in your warehouse or distribution center. Use these tips to keep up the pace and make your facility as efficient as possible.
1. Keep your warehouse organized
Nothing stymies operational efficiency like a poorly-organized warehouse. Your facility should have a thoroughly thought-out floor plan that your employees can navigate with ease. The space should be organized so that your staff members can access products and packages without getting in each other’s way. Your employees may need to process different orders simultaneously, so they should have plenty of space to avoid stepping on each other’s toes. Today’s warehouses are much larger than they were in the past, creating more space for speed and efficiency.
Items should be clearly labeled on the shelf and organized in a way that makes sense for your facility. You can group packages by their contents, destination or point of origin. This layout should make sense to your employees, so they’ll be able find the items they need without having to look at a spreadsheet.
2. Prioritize fast-moving products
Keep your priorities in mind when organizing your warehouse. Every element of your chosen layout should favor your fastest-moving products. Bestsellers don’t tend to sit on the shelf for very long, so make sure your employees can easily retrieve them at all times. Your employees shouldn’t have to go all the way to the back just to retrieve a product, especially if it’s one of your most popular items. You can help everyone save time by moving these fast-selling products to the front of your warehouse. They should be kept low to the ground and close to the loading dock.
Your entire warehouse layout should focus on moving better-performing products to the front, while keeping the less popular products at the back. Go over your inventory and rate your products based on how often your employees need to retrieve them. This should inform your thinking as you change the layout of your facility.
3. Automate the data collection process
Running a warehouse these days is all about data. Digital technology can take the guesswork out of inventory and warehouse management with employees scanning products every step of the way. Your facility should collect as much data on your products as possible, including where they’re coming from, when they arrive, what condition they are in, where they’re going and when they’re set to leave. You can use this data to keep tabs on the location of your products. At any given moment, you’ll know exactly how many products are being stored at your facility.
But in order to improve efficiency, you need to automate the data collection process as much as possible. Your staff members should automatically retrieve this data as they go about unloading and scanning items that have just arrived at the facility and getting them ready for the last leg of their journey. You can use handheld scanners and radio frequency identification tags to simplify this process. Automating data collection also reduces costly errors like inaccurate data entry.
Warehouse automation technology is already a $1.9 billion industry, and it’s expected to balloon to $22 billion by the year 2021. If you want to stay competitive, it might be time to invest in automation. You’ll have all the information you need at your fingertips without adding any additional steps to your operations.
4. Use inventory management software
As you collect all this data on the shipping containers and products moving in and out of your facility, you can save time by sending that info right to your company’s inventory management software. This technology helps you make sense of all the data in a matter of seconds. You can quickly see how many products are on the shelf, when shipments need to go out and when new shipments are due to arrive. Software programs are synced to your data collection devices, so you won’t have to worry about entering that information twice.
[bctt tweet=”Artificially intelligent software programs can even help you anticipate future outcomes like inventory shortages, delivery delays and other potential problems. ” username=”Fronetics”]
Certain artificially intelligent software programs can even help you anticipate future outcomes like inventory shortages, delivery delays and other potential problems. They keep a log of the history of your facility’s operations to help better predict what’s going to happen in the future.
5. Save time with cross docking
If you have fast-moving products coming through the door, you can save time with what’s known as cross docking. Instead of putting these products back on the shelf only to have your employees retrieve them hours later, direct them to a temporary staging area for scanning and inventory purposes. This temporary staging area should be close to the loading dock. When the products are ready for the next leg of their trip, your employees can quickly retrieve them and get them out the door without having to look for them on the shelf.
6. Increase visibility with better lighting
The key to operational efficiency isn’t always as complicated as it seems. Sometimes all you need is better lighting. Warehouses tend to have tall ceilings, and lighting the space, including all those individual shelves, can be a challenge. If you want to be speed up your warehouse operations, everyone should be able to see clearly as they go about their business. Staff members should be able to read labels and use containers without having to squint. Keeping the lights on also helps your employees stay awake, especially if they’re getting a shipment ready in the middle of the night.
Working towards warehouse efficiency
Making your warehouse more efficient starts with having the right layout in place. Your products should be organized according to their popularity. You should automatically collect data on your products as soon as they enter the facility. And always make sure your employees have enough space and light to do their jobs. Follow these steps and you’ll get orders out the door in record time.
Related posts:
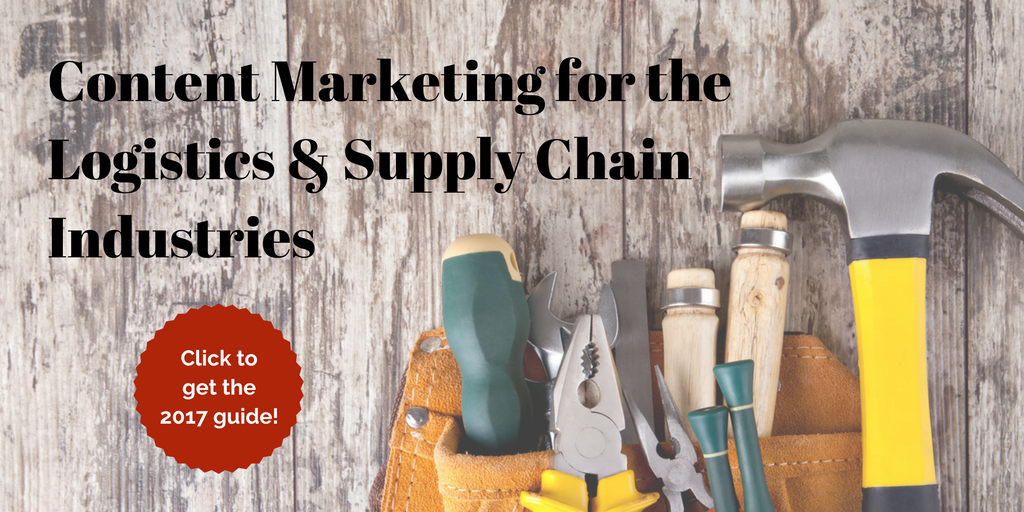
by Fronetics | Feb 27, 2019 | Blog, Marketing, SEO, Website Development
SEO helps your website rank higher in search engine results pages. Here are the SEO basics to get your website performing better and in front of your target audience.
Highlights:
- SEO stands for search engine optimization — that much has stayed the same. It refers to techniques that help your website rank higher in search engine results pages.
- SEO works by optimizing a website’s pages, conducting keyword research, and earning inbound links.
- To rank well in the long term, build your SEO marketing strategy around topics, not keywords.
Video transcript:
I’m Jennifer Yim and I’m the Director of Strategy here at Fronetics. Today’s topic is SEO. SEO seems pretty straightforward. You pick a few keywords and your page is magically optimized for SEO, right? Not quite.
People understand the basic principles of SEO, but a lot has changed in the last decade. Let’s take a look at the basics to get your site ranking higher.
SEO stands for search engine optimization — that much has stayed the same. It refers to techniques that help your website rank higher in search engine results pages. This makes your website more visible to people who are looking for solutions that your brand, product, or service can provide by search engines like Google, Yahoo!, and Bing.
What hasn’t stayed the same are the techniques we use to improve our rankings. This has everything to do with the search algorithms that these companies constantly change.
SEO works by optimizing a website’s pages, conducting keyword research, and earning inbound links. You can generally see results of SEO efforts once the webpage has been crawled and indexed by a search engine.
There are a ton of ways to improve the SEO of your site pages. Search engines look for elements including title tags, keywords, image tags, internal link structure, and inbound links.
Search engines also look at site structure and design, visitor behavior, and other external, off-site factors to determine how highly ranked your site should be in their results pages.
To rank well in the long term, build your SEO marketing strategy around topics, not keywords. If you do that, you’ll find you can naturally optimize for important keywords, anyway. Understanding your target audience and what interests them is key to attracting relevant visitors to your website through search engines.
For more tips on improving SEO and building your digital marketing strategy, visit us at Fronetics.com.
Related posts:
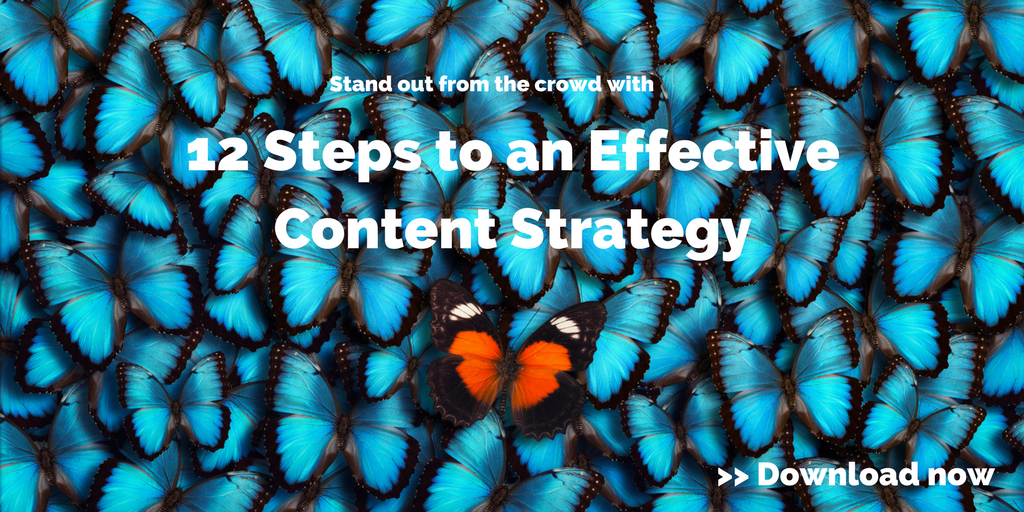
by Fronetics | Feb 20, 2019 | Blog, Content Marketing, Logistics, Marketing, Supply Chain
These 6 robotics blogs are our favorite reads for gathering information, analyzing issues, and staying current in an industry that is rapidly changing.
Highlights:
- Follow these 6 blogs for the latest on the robotics industry
- Featuring a variety of expert perspectives analyzing issues and trends
- Get everything from the big headlines to niche opinion pieces
It’s not easy keeping pace with the latest developments in robotics, an industry where changes are happening swiftly and often. Not only that, sorting through masses of media sites and conversations to find informed, up-to-date coverage of these changes can be utterly overwhelming.
Why Following Robotics Blogs Matters
The robotics field is experiencing unprecedented growth and innovation. From collaborative robots revolutionizing manufacturing to AI-driven autonomous systems reshaping transportation, the pace of change is staggering. These carefully selected blogs offer a curated lens into this dynamic landscape, helping you:
- Navigate complex technical developments
- Understand market trends and investment opportunities
- Gain insights from leading thinkers and practitioners
Luckily, there are places where you can find the kind of information and analysis you need. These 6 robotics blogs are on our reading list — and we think they should be on yours, too. Here, you’ll find blogs that focus completely on covering news, trends, and issues within the robotics industry.
Top 6 robotics blogs for industry news, trends, and insights
1. Robohub
What you’ll find:
- Global community perspective
- Frequent, in-depth content
- Covers research, startups, business, and education
Robohub remains a cornerstone of robotics news and analysis. Its diverse contributor base ensures a well-rounded view of the industry.
2. IEEE Spectrum Robotics
What you’ll find:
- Technical depth from a trusted engineering authority
- Cutting-edge research and breakthroughs
- Explores ethical and societal implications
IEEE Spectrum’s robotics channel offers unparalleled insight into the technical frontiers of the field.
3. TechCrunch Robotics
What you’ll find:
- Startup and investment focus
- Breaking news on product launches and funding rounds
- Interviews with industry leaders
For those interested in the business side of robotics, TechCrunch’s dedicated robotics section is invaluable.
4. The Robotics Report
What you’ll find:
- Comprehensive industry coverage
- Market analysis and investment trends
- Curated by robotics expert Frank Tobe
The Robot Report continues to be a go-to source for business-focused robotics news and analysis.
5. Robotics Business Review
What you’ll find:
- In-depth industry analysis
- Focus on robotics applications across sectors
- Paid membership for full access
While some content remains behind a paywall, RBR offers high-quality insights for serious industry professionals.
6. MIT Technology Review: Robotics
What you’ll find:
- Academic perspective on breakthrough technologies
- Long-form articles exploring future implications
- Balances technical and accessibility
MIT’s renowned publication offers a forward-looking view of robotics and its impact on society.
Staying Informed in a Fast-Paced Field
Following these blogs will provide a comprehensive view of the robotics landscape. However, the field is vast, and new sources of information emerge regularly. We recommend:
- Setting up RSS feeds or email subscriptions to stay current
- Engaging with robotics communities on social media
- Attending industry conferences and webinars for deeper insights
The robotics industry continues to push boundaries, reshape industries, and create new possibilities. By following these top blogs, you’ll have the knowledge and insights needed to navigate this exciting field, whether you’re a researcher, entrepreneur, investor, or simply an enthusiast.
Which robotics blogs are you following?
Related posts:
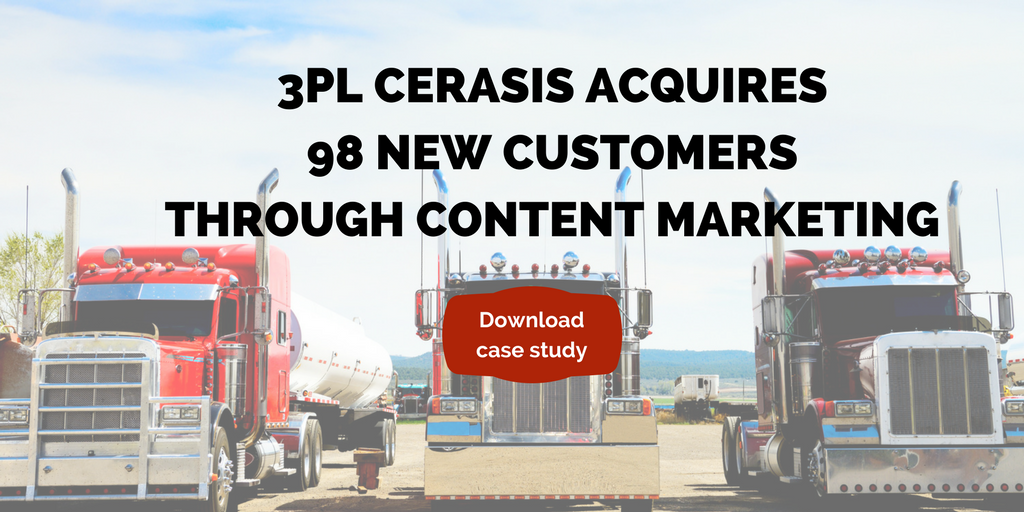
by Jennifer Hart Yim | Feb 14, 2019 | Blog, Content Marketing, Internet of Things, Logistics, Marketing, Supply Chain
Rogue Ales believes that their “Ground to Glass, Grow your Own Revolution” is a key tenet to their success. The company leverages the Internet of Things (IoT) to ensure that their supply chain is able to deliver the highest-quality ingredients to their breweries just in time.
Highlights:
- Consumer desire for freshness and high quality is influencing the beer brewing industry.
- Rogue Ales owns Rogue Farms giving the brewery a unique advantage in being able to produce specialty ingredients.
- The Internet of Things has enabled Rogue to capture and act on the data surrounding their supply chains.
Rogue Ales, headquartered in Newport, OR, is an alcoholic beverage company founded in 1988 that produces beer, wine, cider, and distilled spirits. Their ales have won over 1,800 awards at various brewing competitions.
Rogue’s brewing operation is unique in that the company’s subsidiary, Rogue Farms (founded in 2008), grows all of the ingredients used. The company believes that their “Ground to Glass, Grow your Own Revolution” is a key tenet to their success. Rogue Ales leverages the Internet of Things (IoT) to ensure that their supply chain is able to deliver the highest-quality ingredients to their breweries just in time.
The trend toward freshness
According to AT Kearney, 93% of consumers consider freshness to be the most important criterion when purchasing foods. According to the USDA, the sale of organic foods in the U.S. has more than tripled from approximately $12B in 2005 to over $35B in 2015 (data for 2016-2018 was not immediately available).
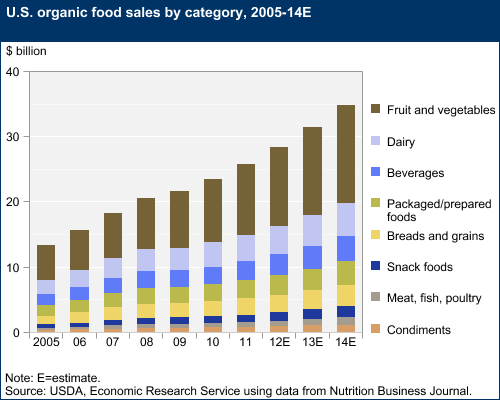
Consumer desire for freshness and high quality is influencing the beer brewing industry. According to the American Brewers Association, the number of craft breweries in the United States has increased from 122 in 1973 to over 6,300 in 2017.
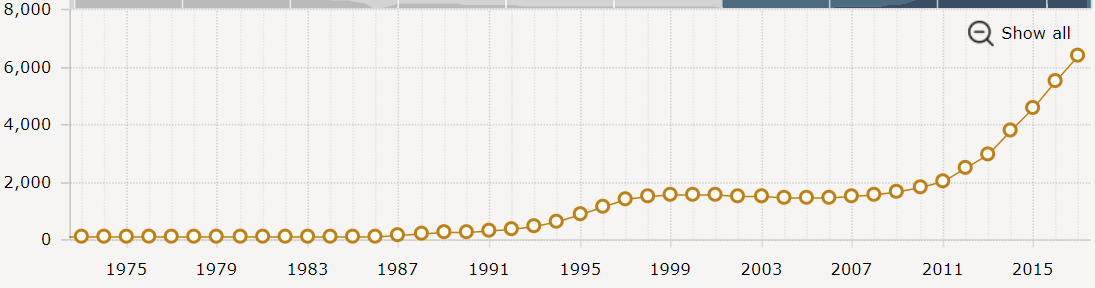
As the competition between breweries intensifies, brewers are constantly looking for key ways to differentiate their beers from their competitors in this $111.4B market. Most beer sales are through microbreweries (defined as a brewery producing less than 15,000 barrels per year and at least 75% of beer sold off-site via distributors or wholesalers). Rogue Ales has made freshness a key value-add differentiator for its brand, selling over 325,000 gallons in 2016. In a Market Watch article, Rogue’s president, Brett Joyce, says:
What it means is that we have to get better all the way around. The quality has to go up. Just having products isn’t enough. You better have a strategic plan to go to market, retailer support, good follow-up and good sales people. It’s a real business now.
With the establishment of Rogue Farms in 2008, Rogue began producing their own ingredients, breaking tradition with most breweries, who acquire ingredients from traditional wholesalers. Rogue has a 52-acre hop farm, located approximately two hours from the brewery, where it produces its entire hop supply. Rogue states that:
Growing hops is an expensive and time-consuming endeavor, but it also helps to guarantee our supply and quality while allowing us to keep our Brewmaster, John ‘More Hops’ Maier, happy with unique, aromatic hops.
The control Rogue Ales has over Rogue Farms gives the brewery a unique advantage in being able to produce specialty ingredients for its core and specialty beers. At Rogue Farms, Rogue grows or produces:
- 10 varieties of hops
- Two varieties of malting barley
- Rye
- Pumpkins
- Marionberries
- Jalapeños
- Honey
The challenges of using fresh “wet” hops in beer
A basic beer recipe only has four ingredients: malted barley, water, hops, and yeast. Of these ingredients, hops are the most difficult to source, store, and transport due to their perishability. Most brewers use pelletized, dried, hop pellets. Rogue uses fresh (or “wet”) hops in their ales, harvested from Rogue Farms. Fresh hops give their beer a fresher taste, as the hops’ aromatic qualities are not damaged by drying and pelletization.
Fresh hops, once harvested, must land in a brew vat within 12 hours and cannot be exposed to excessive heat, air, or humidity during transport or their volatile aroma compounds will degrade and produce aromas of “skunk” and “compost”. To ensure the highest quality of hops, Rogue has turned to technology to ensure that its supply chain is delivering the freshest possible hops to the brewery.
Using the Internet of Things to build quality into Rogue’s supply chain
The vertical integration of Rogue Ales and Rogue Farms gives Rogue a unique advantage in being able to leverage new technologies to ensure it sources the highest quality ingredients possible directly from their farm to their brewery. Rogue Ales uses Intel’s Connected Logistics Platform to manage its hops supply chain. Intel’s platform is a logistics management solution that couples Internet of things (IoT) devices with a cloud-based data analytics system. These IoT devices are one-time-use sensor tags that attach to shipments and collect data (e.g. temperature, humidity, location, etc.). This data is sent over a proprietary wireless protocol to a central server where the data is aggregated and analyzed in real time.
[bctt tweet=”The Internet of Things has enabled companies like Rogue to capture and act on the data surrounding their supply chains. Companies are able to make smart decisions that bring cost savings and flow directly to their bottom line.” username=”Fronetics”]
The system tracks shipments and collects data during every facet of the supply chain, ensuring that quality thresholds are maintained and any problems with the shipped goods can be immediately corrected (for example, if one of the trucks runs into traffic, the others can be intelligently rerouted). It is estimated that 30% of all perishable products shipped in the United States become spoiled during their journey from the farm.
After the wet hops are picked, Rogue attaches three trackers to each shipment: at the top, middle, and bottom of the bale of hops. These trackers measure temperature, humidity, and location. Rogue can ensure that the hops have been kept in the proper environment and that they have not spent too much time in transit.
If a shipment does not meet quality standards, it can be discarded before it is used in a beer batch, reducing waste and ensuring that Rogue does not waste its precious brewing capacity brewing beer that will later need to be dumped for quality reasons. The location of the shipment is updated every ten minutes, and once the hops have reached the halfway point, Rogue starts the brewing process. This ensures that the hops arrive just in time and go directly from the truck into the brewing kettle.
The Internet of Things has enabled companies like Rogue to capture and, more importantly, act on the data surrounding their supply chains. Companies are able to make smart decisions that bring cost savings and flow directly to their bottom line.
This article was written by Zachary Richards, an MBA student at the Peter T. Paul College of Business and Economics at the University of New Hampshire. Zach is a Software Engineer at Pegasystems, Inc., where he specializes in back-end Java development, data structures, and agile development practices. He graduated from Worcester Polytechnic Institute in 2016 with a B.S. in Computer Science.
Related posts:
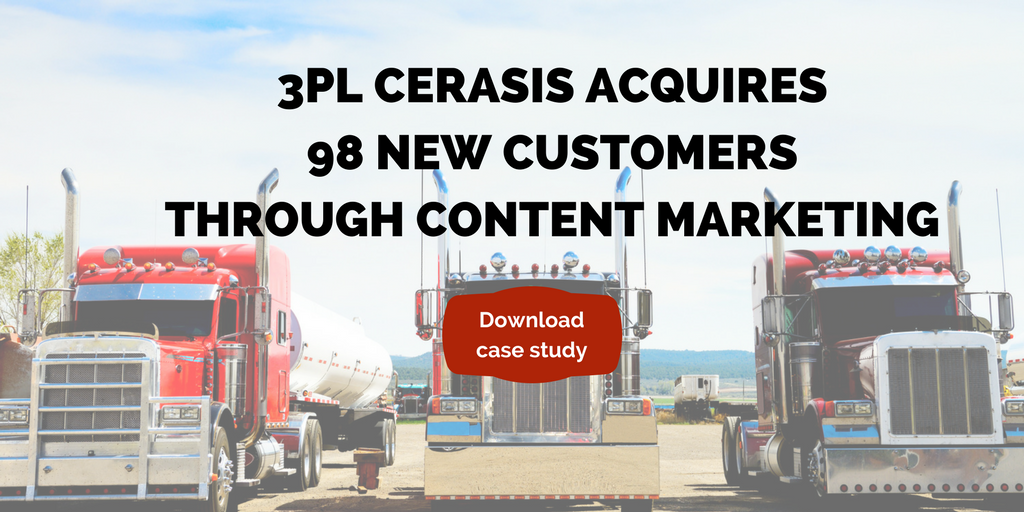
by Fronetics | Feb 13, 2019 | Blog, Content Marketing, Marketing, SEO
Search engines are constantly changing, but these 5 tips will ensure that supply chain marketers can boost SEO in 2019.
Highlights
- People are changing how they search, and search engines are adapting accordingly.
- Simple changes to the structure of your site can have a big impact on your search engine rankings.
- Sites rich in quality content, like blogs and video, are poised to rank high for relevant search queries.
If there’s one constant when it comes to writing to boost Search Engine Optimization (SEO), it’s change. As users change the way they search online, search engines are continually adapting their algorithms to meet their needs. While it’s easy to get overwhelmed, it’s important for supply chain marketers to stay up-to-date and adapt their content strategy to boost SEO.
The year is just getting into full swing, and it’s a great time for savvy marketers to look ahead and make strategic decisions for SEO in 2019. These five tips will help you get ahead of the curve.
5 ways to boost SEO in 2019
1) Cluster content
Gone are the days of keyword rankings. Rather than prioritizing keyword focus, search engines have shifted to rewarding sites that produce strong content and arrange it in focused, niche topics.
Cluster content, a method of on-site SEO, might sound daunting. But it doesn’t require reinventing the wheel, just changing the structure of your site. For a detailed look at topic clusters and pillar content, check out part three of our four part series on writing for SEO.
We’ll give you the short version here: Select several core topics that most closely align with your brand, and reflect the knowledge you have to share. Evaluate your existing content, and categorize it based on which core topic or topics it falls under. Going forward, keep these core topics top of mind when planning and creating content. Next, arrange your site to reflect core topics with content clustered and linked from pillar pages.
2) Use header tags
As they become more and more sophisticated, search engines increasingly mirror human preferences. It doesn’t take an expert to tell you that text is more accessible to the eye when broken up by relevant subheadings — and search engines are no different. Headings make your text easier to skim and allow search engines to pick out content relevant to search queries.
Subheadings make your site more visually appealing, orienting readers and providing structure within your content. Remember that you’re creating headings for the dual purpose of guiding readers and optimizing for search engines. For this reason, stick to headings that are short and informative, reflecting the content below them, rather than teasing your readers with click-baity phrases.
[bctt tweet=” Stick to headings that are short and informative, reflecting the content below them, rather than teasing your readers with click-baity phrases.” username=”Fronetics”]
3) Blog
This one is evergreen. We’ve been writing for years about how blogging is crucial for supply chain companies, for all kinds of reasons — not the least of which is SEO. If increased lead generation and site engagement isn’t reason enough, you should know that blogging is one of the best ways to boost SEO.
A blog is your space for high-quality content that’s fresh, well-researched, and relevant. If you’re choosing your topics based on the needs and preferences of your target audience, chances are, you’re creating content that is perfectly aligned to search engine queries.
4) Make sure your page speed is high
Page speed is crucial for boosting SEO. If your page is loading slowly, Google logs it, and your ranking suffers. Not only that, visitors who do click on your site will be frustrated and turn away.
In fact, research shows that 40% of visitors will abandon sites where the page takes longer than three seconds to load.
One of the best ways to improve page speed is to switch to HTTP/2. If you haven’t already, switching your site from HTTP/1.1 (which has been the norm since 1999) is crucial. HTTP/2 was first published in 2015, with the goal establishing a faster, more secure internet. Search Engine Journal has published this great guide to HTTP/2, where you can learn more about the benefits, and how to switch.
5) Video
We’ve been talking about the benefits of video for a while now. Having video on your landing page will robustly improve your SEO. Video increases conversion rates, improves bounce rates, and boosts overall time on sites.
Search engines use bounce rate to rank pages — a low bounce rate and high user retention rate are indicators of strong content and high relevance to your target audience. Consequently, Google is strongly emphasizing these metrics in its ranking algorithm. Video keeps users on your site better than just about anything else and is therefore one of the most effective ways to boost SEO.
Related posts:
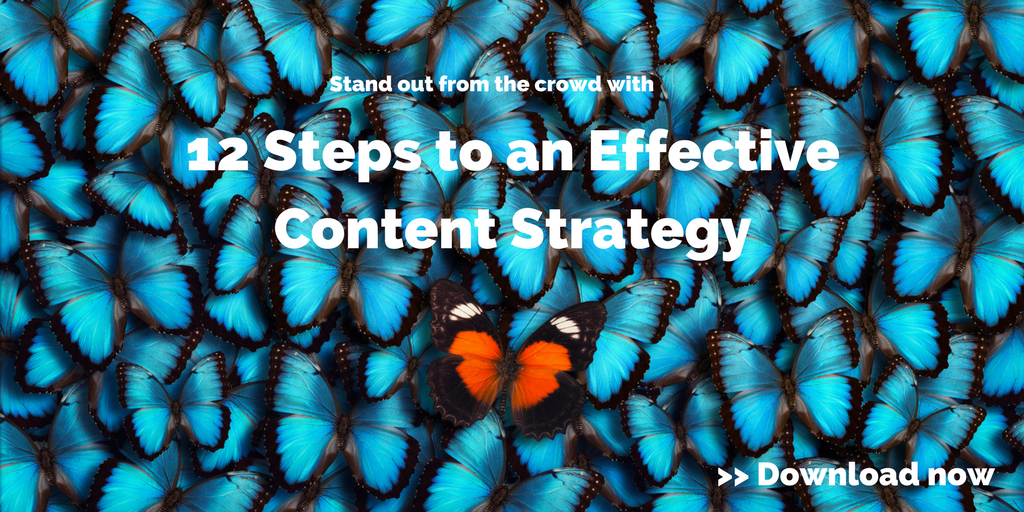
by Fronetics | Feb 12, 2019 | Blog, Marketing, Social Media, Supply Chain
Transparency in your supply chain through social media outlets can give a look inside your company in a way that your customers are craving.
Highlights:
- Customers have been demanding more visibility into supply chains of the products they purchase.
- Through social channels like Twitter , LinkedIn , and Facebook, companies are greatly enhancing their two-way communication with customers and sharing information with their stakeholders.
- The top reason that supply chain companies are choosing to participate in social media is to increase the visibility of their company.
Supply chain management is such a complicated web of factors that most companies choose to keep operations behind the scenes and unveil a finished product with an intense marketing roll-out.
But what if that’s backwards and an outdated approach to marketing? (Hint: It is.)
The complexity of supply chain management
There is no question that SCM can be deeply and frustratingly complex. Consider TechTarget’s definition of SCM: “the broad range of activities required to plan, control and execute a product’s flow, from acquiring raw materials and production through distribution to the final customer, in the most streamlined and cost-effective way.”
With so much intense analysis at every step, the details your supply chain management (SCM) team considers can seem endless, and the impressive knowledge they hold is certainly not something most people can understand.
Or can they? What if that mindset – the one that thinks that your SCM is so complex that it wouldn’t interest or be able to be grasped by your customers – is wrong?
In fact, what if it’s so wrong that you are missing something important? Customers today want to understand your supply chain.
Transparency in your supply chain
A common misconception is that most customers are interested in a final product. Of course, your final product better be outstanding, but there are other factors fueling today’s buyers, business-to-business (B2B) customers included.
For a few years now, customers have been demanding more visibility into supply chains of the products they purchase. For example, they want to ensure sustainable practices around the earth’s scarce resources, to know where their food is sourced, and to confirm ethical pay and conditions for any laborers involved. B2B buyers are no exception. They want their vendors to be more than just a final product too, and are constantly searching for value outside the sales funnel.
Transparency with social media
What if you shared what fueled your daily SCM decisions with your customers, stakeholders, and suppliers? Not every last complex detail…but some of them, and the intangibles too:
- What drives SCM decisions besides cost?
- Who is your SC team?
- Where are you sourcing?
- Why do you do things as you do during production?
Transparency of SCM through social media outlets can give a look inside your company in a way that your customers are craving. Through social channels like Twitter , LinkedIn , and Facebook, companies are greatly enhancing their two-way communication with customers and sharing information with their stakeholders.
Of course, the benefits of social media to SCM don’t stop there.The supply chain needs social media for enhanced customer communication, increased industry education, and an ability to socially monitor the market. Social media has the capability to empower your supply chain in multiple ways.
According to a survey we conducted, the top reason that supply chain companies are choosing to participate in social media is to increasing the visibility of their company (95%). Don’t simply focus on your final product(s) and leave out your supply chain! When you make your supply chain transparent to your customers and stakeholders, everyone wins.
This post originally appeared on EBN Online.
Related posts: