by Jennifer Hart Yim | May 28, 2019 | Blog, Talent
Soft skills are more important than ever, and emotional intelligence is arguably more important than all the rest.
Highlights:
- Because Supply Chain now touches on every aspect of a business, soft skills have become more important than ever.
- Emotional intelligence is the ability to understand one’s own emotions as well as the emotions of others.
- Emotionally intelligent people are more thoughtful about decisions within an organization. They’re able to see others’ points of view, and better judge how their decisions will impact others.
This guest post comes to us from Argentus Supply Chain Recruiting, a boutique recruitment firm specializing in Supply Chain Management and Procurement.
The rise of emerging technologies like big data and AI has changed the skills profile for a number of white collar careers – not the least of which is Supply Chain Management, which is our specialty at Argentus. Tools like SAP, other ERP systems and Supply Chain visibility software have opened up massive opportunities for people who can analyze data and draw intelligence. They’ve raised Supply Chain’s profile in companies. The function now drives and transforms big picture strategy instead of just fighting daily fires.
Supply Chain is a STEM field. People with engineering, data analysis, systems development, and other hard skills will always be important. But there’s something interesting happening in the skills profile for top Supply Chain people: because Supply Chain now touches on every aspect of a business, soft skills have become more important than ever. It’s a bit of a paradox, but it’s borne out in our conversations with clients, as well as executives across the field.
And in 2019, there’s one soft skill that reigns supreme: emotional intelligence.
[bctt tweet=”According to the World Economic Forum’s Future of Jobs report, emotional intelligence is the most important emerging soft skill heading into 2020. ” username=”Fronetics”]
According to the World Economic Forum’s Future of Jobs report, emotional intelligence is the most important emerging soft skill heading into 2020. This great article in Fast Company digs into the research. It examines the importance of emotional intelligence (EQ), and explains why hiring managers often prize EQ over IQ when identifying talent today.
What is emotional intelligence?
In short, it’s the ability to understand one’s own emotions as well as the emotions of others. It’s closely related with empathy, and leads to an increased ability to understand your team’s needs in the workplace. In general, research has found a correlation between high emotional intelligence and job performance, mental health, and leadership skills.
In a recent interview, Supply Chain VP Taras Korec identified emotional intelligence as one of the most crucial soft skills for everyone in the field, from the analyst level up to the VP level. He also said he hires based on attitude and emotional intelligence rather than hard skills.
But organizations don’t always see the value in developing their employees’ emotional intelligence, and this has big ramifications. As Taras put it, “if you’re an analyst and you go to your boss and say, ‘I want some training on the hard skills,’ that’s a pretty obvious sell. But how many people have the courage at the analyst level to say, ‘I want to take training on emotional intelligence’? A lot of leaders may not have invested in those skills themselves. They may not see the value in them, which reinforces that deficit throughout the organization.”
According to the research, these are some of the biggest career advantages enjoyed by people with high emotional intelligence (EQ):
- The ability to deal with pressure. Emotional intelligence helps you understand and regulate your own emotional state, which leads to better stress management and healthy coping mechanisms. Supply Chain is often a high-stress profession, with critical business outcomes riding on SCM planning and performance – so emotional intelligence is particularly helpful.
- Increased co-operation. The Fast Company analysis points out how workplaces are becoming more collaborative, as well as inclusive to people from different backgrounds. Emotional intelligent people are better relationship-builders, and that’s valuable in a field like Supply Chain where you’re often working with people from all over the world.
- The superpower of using feedback as fuel. In general, intelligent people tend to recognize the importance of self-improvement and skills development. But people with good emotional intelligence are also more open to others’ feedback – which is necessary to see what they need to improve. They don’t take criticism personally, so they’re better poised to turn feedback and areas of improvement in performance reviews into fuel for personal growth.
- Improved leadership skills. People with high emotional intelligence have better empathy, resilience, and ability to build influence – key traits for business leaders. Success in Supply Chain Management – especially in disciplines like Procurement – relies on an ability to build relationships and influence stakeholders from across the business. People with high emotional intelligence are great at rising above daily firefighting. They’re more likely to be seen as leaders within a business. They’re respected. People listen when they speak, even if they don’t have a “leadership” title. As Supply Chain VP Taras Korec said in our recent interview, “there’s no reason you can’t lead, regardless of your title.”
- Better decision making and ability to adapt to change. The business world is changing rapidly in the age of digital technology, and this is especially true within Supply Chain and Procurement, which are undergoing major transformations at top organizations. Emotionally intelligent people are more thoughtful about decisions within an organization. They’re able to see others’ points of view, and better judge how their decisions will impact others.
Like any soft skill, emotional intelligence can be intangible. It’s way harder for a Supply Chain professional to put emotional intelligence on a resume than their skills with a particular SAP module. Conversely, it’s also harder for a hiring manager to systematically screen for emotional intelligence than other “hard” skills. It’s harder to design a university course around. But the fact is, you know it when you see it, and truly great hiring managers know how to assess emotional intelligence in a job interview.
You might not find emotional intelligence in a list of SCM core competencies – but like any other soft skill, it’s crucial. And it’s only becoming more important.
Related posts:
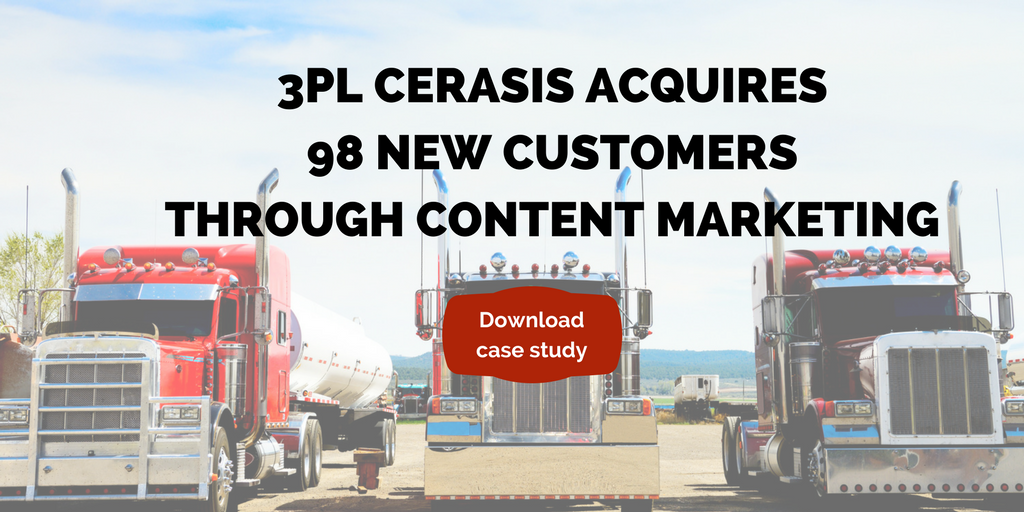
by Jennifer Hart Yim | Apr 25, 2019 | Blog, Supply Chain, Talent
New research backs up what we already know: the supply chain economy is a hotbed of innovation, and that opens up immense professional opportunities.
Highlights:
- New research assigns some numbers to two facts that every Supply Chain professional knows: the sector is full of opportunity for professionals and it is a hotbed for innovation.
- Supply Chain industry innovations have a tendency to reverberate and cascade throughout the wider economy as they filter from suppliers, to the companies they supply, and finally to the consumer.
- People who are able to harness and drive supply chain innovation have some of the brightest job prospects in tomorrow’s economy.
This guest post comes to us from Argentus Supply Chain Recruiting, a boutique recruitment firm specializing in Supply Chain Management and Procurement.
A new Harvard Business Review article lays out some striking research out of MIT about the role of Supply Chain Management within the broader economy. Written by Mercedes Delgado and Karen Mills, the study seeks to better define what constitutes the “Supply Chain” part of the economy, and what doesn’t. The goal? To better define Supply Chain Management’s place in the broader economy, and the role it plays in terms of innovation.
The researchers define “Supply Chain” industries as any industries that sell upstream to businesses and government entities. It excludes industries selling direct to consumer (B2C). It’s a bit of a curious definition – what about the B2C companies with strong supply chain and distribution networks? – but we’ll roll with it.
In short, the research assigns some numbers to two facts that every Supply Chain professional knows: the sector is full of opportunity for professionals. It’s also a hotbed for innovation which has a tendency to filter into other sectors of the economy.
The MIT researchers studied the historical role that these Supply Chain companies have played in American innovation. For example, Intel’s semiconductors and Microsoft’s enterprise software are innovations with their roots in the supply chain – supplying to companies – that are almost unparalleled in terms of their downstream effect on the overall economy, as well as the daily experience of the average person.
The researchers make an interesting point: compared to “B2C” industries, Supply Chain industry innovations have a tendency to reverberate and cascade throughout the wider economy as they filter from suppliers, to the companies they supply, and finally to the consumer. Technologies like cloud computing –which is now sold to 90% of industries – have their roots in the Supply Chain, which helps them diffuse across industries as they spread downstream and become integral to the economy. In Delgado and Mills’ estimation, this “trickling down” gives these innovations a multiplying effect that isn’t found in more consumer-facing industries.
Put aside the fact that the most successful consumer-facing companies of the past several decades have been tremendously innovative (Apple and Amazon, for example) – in part because of their Supply Chain practices – and it’s an intriguing idea. The fact is, Supply Chain management drives innovation, and the people who drive that innovation have some of the brightest job prospects out of anyone in the economy.
People in Supply Chain are more likely to be in STEM (Science, Technology, Engineering and Math) than the wider economy. They’re also better compensated – perhaps as an indirect result of their contributions to innovation.
Here are a few of the most interesting – and exciting – top-level stats from the research:
- In the U.S. – which the study examined – 44 million jobs are in Supply Chain, or 37% of the overall economy.
- The average wage of Supply Chain-related jobs was much higher than average, at $61,700 – compared to $39,200 for non-Supply Chain jobs.
- 4% of Supply Chain jobs were STEM-related jobs – considered a predictor of innovation – compared to only 2.1% of non-Supply Chain jobs.
- 6% of new patents in the U.S. evolve from the Supply Chain sector.
The researchers chart another interesting distinction and trend, towards the importance of Supply Chain Services from traditional manufacturing. Supply Chain services jobs – including logistics, engineering, cloud computing, and others – have grown massively to encompass 80% of jobs in the sector, but most still consider Supply Chain to mean traditional manufacturing jobs such as metal stamping or injection molding operators.
Supply Chain Services workers have the highest STEM intensity out of everyone in the economy (19%), which also coincides with the highest wages ($80,800 a year, on average). This tracks with a trend in the wider economy towards services and away from traditional manufacturing, and shows what we know to be the case: despite panic about automation, Supply Chain professionals who can innovate are in very high demand.
Whether you agree or disagree with Mills and Delgado’s definitions and findings, it’s clear to anyone paying attention that the Supply Chain is a force-multiplier for innovation to the economy. It’s truer now than it’s ever been, and people who are able to harness and drive that innovation have some of the brightest job prospects in tomorrow’s economy.
Do you agree with the authors’ definition of Supply Chain? Is it too broad, not broad enough, or is it right on the money? We’re curious to hear anything else you might have to add about the importance of Supply Chain for innovation in the wider economy!
In the meantime, we encourage everyone to check out the HBR article as well as the authors’ original study, which has some fascinating insights about the role Supply Chains play in innovation.
Related posts:
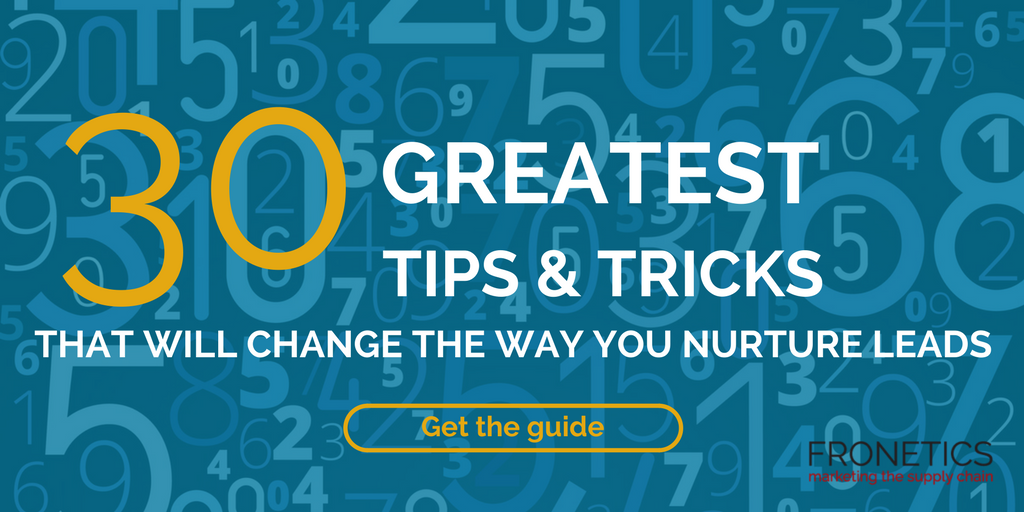
by Jennifer Hart Yim | Mar 27, 2019 | Blog, Content Marketing, Current Events, Leadership, Marketing, Supply Chain, Talent
In today’s job market, companies have to compete harder than ever before and candidates, realizing their position, have begun ghosting employers. Ghosting has never been in an issue in the professional setting until now.
Highlights:
- According to a new report, more companies and recruiters are getting ghosted, with thousands of users on LinkedIn chiming in about what seems to be a uniquely-millennial phenomenon moving into the workplace.
- Ghosting’s prevalence speaks to a talent attraction and retention problem that many companies are having in this marketplace.
- Recruiters who are specialized in your vertical have an established base of candidates, so you can remove ghosting from the equation entirely.
This guest post comes to us from Argentus Supply Chain Recruiting, a boutique recruitment firm specializing in Supply Chain Management and Procurement.
Many of us have (thankfully) been out of the dating game long enough that we’ve never experienced what most millennials have: the dreaded ghost. You meet someone new, hit it off, go on a few dates, maybe even tell your friends and parents about an exciting romantic prospect. Then the hammer drops: all of a sudden, radio silence. No “dear John” letter, no break-up text, and no explanation whatsoever. It’s a digitally-enabled way of severing ties that’s so casual it hurts, because the affected (dare we say victim?) never gets to find out what exactly happened. The imagination runs wild with possible motivations for this disrespect: was it them? Was it me?
You never really know. That’s what makes it so tough.
Now, according to reports, this peculiar social phenomenon has metastasized into the workplace:
The job market is so hot, more candidates are ghosting their employers. Or prospective employers.
Welcome to 2019.
It’s no secret that the hiring market is strong, with near-historic low levels of unemployment. Now, according to a recent NPR report, more companies and recruiters are getting ghosted. It’s also become a hot topic on LinkedIn, with thousands of users chiming in about what seems to be a uniquely-millennial phenomenon moving into the workplace. Reports about ghosting even made their way into a recent report from the U.S. Federal Reserve – which shows that ghosting isn’t just a meme, but something that’s really affecting companies’ hiring practices and their bottom line.
NPR – as well as this great article by LinkedIn Contributor Molly Mosley – identify three key species of ghost:
- The employee who accepts a role and gets into the job – thankfully, it’s not often a long-term employee, otherwise a missing person report might be in order – and leaves without a trace.
- The job candidate who books a job interview, or accepts a role, and doesn’t show up, or send any kind of communication or response when contacted.
- The candidate who works with a recruiter, asks to be submitted for a role, and then stops responding. There are quite a few reports about this, but we’re lucky that we haven’t experienced it as much in our recruitment practice at Argentus.
Ghosting is a very modern-feeling phenomenon. It’s a symptom of a more relaxed – dare we say, lax – approach to interpersonal and professional relationships brought about by digital technology. But it’s also a symptom of something more fundamental about this job market:
It’s a candidate’s market – especially in high-demand STEM fields like Supply Chain.
We’re willing to bet that in a recession, all these ghosts would become corporeal again. But for now, candidates have all the leverage, and what’s more, they’re beginning to realize this, which means that companies have to compete harder than ever before.
Don’t get us wrong: ghosting is unacceptable, and we don’t mean to excuse it. No one would want to hire a candidate who’s ghosted an employer in the past, and we’d stop working with anyone if we found out they’ve done it before. It’s, in short, the height of unprofessionalism. Any company who gets ghosted on has really dodged a bullet: who would want to work with someone who would resort to such a childish and cowardly tactic?
But ghosting’s prevalence still speaks to a talent attraction and retention problem that many companies are having in this marketplace. Consider this: if your company interviews someone, and never gives any form of feedback or follow-up – which still happens, believe it or not – you’re ghosting candidates as well.
It cuts both ways. And that gestures towards a few changes that companies can make to help minimize the risk of ghosting – which can waste thousands of dollars of company resources:
Smooth out the onboarding process.
In short, treat prospective candidates like a valuable strategic asset instead of a disposable endless resource. The accounts of ghosting from the workers in the NPR story, as well as others, share something in common: the workers felt disrespected or disregarded by their employers.
[bctt tweet=”The accounts of ghosting from the workers in the NPR story, as well as others, share something in common: the workers felt disrespected or disregarded by their employers.” username=”Fronetics”]
Treating candidates with respect is table stakes in this hiring environment. But consider the ways that you’re unintentionally depersonalizing the hiring and onboarding process: letting it get drawn out with endless approvals and interviews, resorting to impersonal communication methods, failing to have succinct and effecting onboarding policies to get new candidates up to speed.
Lastly, because we can’t resist: a specialized recruitment partner will forward pre-vetted candidates, often ones that they’ve known for years, who you know won’t ghost. Recruiters who are specialized in your vertical have an established base of candidates, so you can remove ghosting from the equation entirely.
But what’s your experience? Have you been ghosted by an employee or job candidate before? Why do you think this issue is coming into the zeitgeist right now?
Related posts:
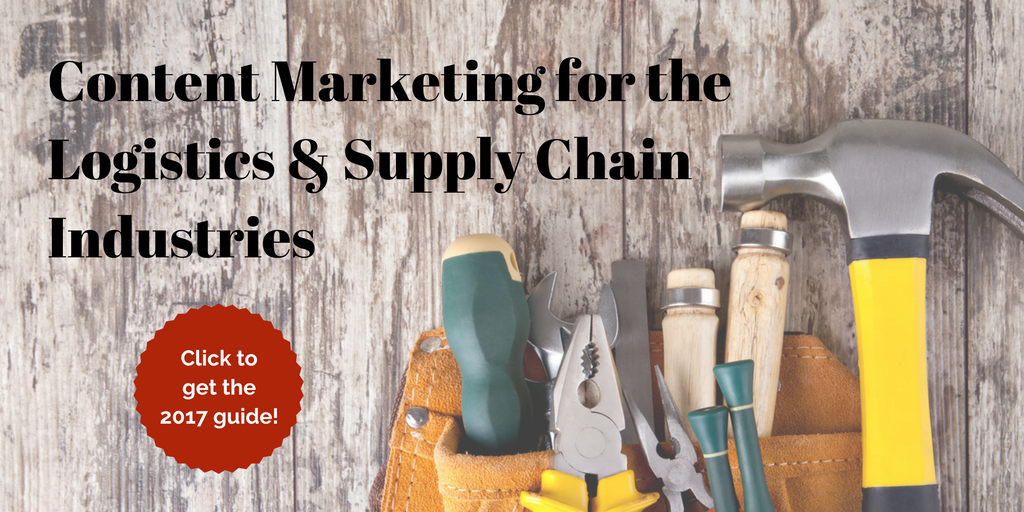
by Jennifer Hart Yim | Feb 28, 2019 | Blog, Strategy, Supply Chain, Warehousing & Materials Handling
If you want to keep your customers satisfied, you need to keep things moving in your facility. Use these tips to keep up the pace and increase warehouse and distribution center efficiency.
Highlights:
- Speed has become the name of the game when it comes to staying competitive in the global supply chain.
- Keep your priorities in mind when organizing your warehouse, including your fastest-moving products.
- Digital technology can take the guesswork out of inventory and warehouse management with employees scanning products every step of the way.
This guest post was written by David Maddenfor Argentus Supply Chain Recruiting, a boutique recruitment firm specializing in Supply Chain Management and Procurement.
Things can always be faster when you work in a warehouse or distribution center. Speed has become the name of the game when it comes to staying competitive in the global supply chain. Major players like Amazon and Walmart have distribution centers all over the world, pumping out packages at lightning speed.
If you want to keep your customers satisfied, you need to keep things moving in your warehouse or distribution center. Use these tips to keep up the pace and make your facility as efficient as possible.
1. Keep your warehouse organized
Nothing stymies operational efficiency like a poorly-organized warehouse. Your facility should have a thoroughly thought-out floor plan that your employees can navigate with ease. The space should be organized so that your staff members can access products and packages without getting in each other’s way. Your employees may need to process different orders simultaneously, so they should have plenty of space to avoid stepping on each other’s toes. Today’s warehouses are much larger than they were in the past, creating more space for speed and efficiency.
Items should be clearly labeled on the shelf and organized in a way that makes sense for your facility. You can group packages by their contents, destination or point of origin. This layout should make sense to your employees, so they’ll be able find the items they need without having to look at a spreadsheet.
2. Prioritize fast-moving products
Keep your priorities in mind when organizing your warehouse. Every element of your chosen layout should favor your fastest-moving products. Bestsellers don’t tend to sit on the shelf for very long, so make sure your employees can easily retrieve them at all times. Your employees shouldn’t have to go all the way to the back just to retrieve a product, especially if it’s one of your most popular items. You can help everyone save time by moving these fast-selling products to the front of your warehouse. They should be kept low to the ground and close to the loading dock.
Your entire warehouse layout should focus on moving better-performing products to the front, while keeping the less popular products at the back. Go over your inventory and rate your products based on how often your employees need to retrieve them. This should inform your thinking as you change the layout of your facility.
3. Automate the data collection process
Running a warehouse these days is all about data. Digital technology can take the guesswork out of inventory and warehouse management with employees scanning products every step of the way. Your facility should collect as much data on your products as possible, including where they’re coming from, when they arrive, what condition they are in, where they’re going and when they’re set to leave. You can use this data to keep tabs on the location of your products. At any given moment, you’ll know exactly how many products are being stored at your facility.
But in order to improve efficiency, you need to automate the data collection process as much as possible. Your staff members should automatically retrieve this data as they go about unloading and scanning items that have just arrived at the facility and getting them ready for the last leg of their journey. You can use handheld scanners and radio frequency identification tags to simplify this process. Automating data collection also reduces costly errors like inaccurate data entry.
Warehouse automation technology is already a $1.9 billion industry, and it’s expected to balloon to $22 billion by the year 2021. If you want to stay competitive, it might be time to invest in automation. You’ll have all the information you need at your fingertips without adding any additional steps to your operations.
4. Use inventory management software
As you collect all this data on the shipping containers and products moving in and out of your facility, you can save time by sending that info right to your company’s inventory management software. This technology helps you make sense of all the data in a matter of seconds. You can quickly see how many products are on the shelf, when shipments need to go out and when new shipments are due to arrive. Software programs are synced to your data collection devices, so you won’t have to worry about entering that information twice.
[bctt tweet=”Artificially intelligent software programs can even help you anticipate future outcomes like inventory shortages, delivery delays and other potential problems. ” username=”Fronetics”]
Certain artificially intelligent software programs can even help you anticipate future outcomes like inventory shortages, delivery delays and other potential problems. They keep a log of the history of your facility’s operations to help better predict what’s going to happen in the future.
5. Save time with cross docking
If you have fast-moving products coming through the door, you can save time with what’s known as cross docking. Instead of putting these products back on the shelf only to have your employees retrieve them hours later, direct them to a temporary staging area for scanning and inventory purposes. This temporary staging area should be close to the loading dock. When the products are ready for the next leg of their trip, your employees can quickly retrieve them and get them out the door without having to look for them on the shelf.
6. Increase visibility with better lighting
The key to operational efficiency isn’t always as complicated as it seems. Sometimes all you need is better lighting. Warehouses tend to have tall ceilings, and lighting the space, including all those individual shelves, can be a challenge. If you want to be speed up your warehouse operations, everyone should be able to see clearly as they go about their business. Staff members should be able to read labels and use containers without having to squint. Keeping the lights on also helps your employees stay awake, especially if they’re getting a shipment ready in the middle of the night.
Working towards warehouse efficiency
Making your warehouse more efficient starts with having the right layout in place. Your products should be organized according to their popularity. You should automatically collect data on your products as soon as they enter the facility. And always make sure your employees have enough space and light to do their jobs. Follow these steps and you’ll get orders out the door in record time.
Related posts:
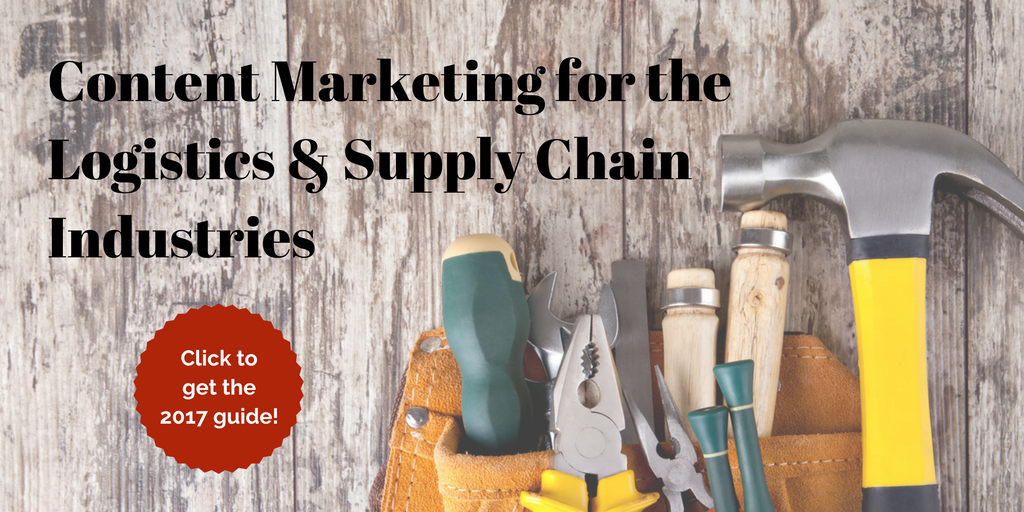
by Jennifer Hart Yim | Feb 14, 2019 | Blog, Content Marketing, Internet of Things, Logistics, Marketing, Supply Chain
Rogue Ales believes that their “Ground to Glass, Grow your Own Revolution” is a key tenet to their success. The company leverages the Internet of Things (IoT) to ensure that their supply chain is able to deliver the highest-quality ingredients to their breweries just in time.
Highlights:
- Consumer desire for freshness and high quality is influencing the beer brewing industry.
- Rogue Ales owns Rogue Farms giving the brewery a unique advantage in being able to produce specialty ingredients.
- The Internet of Things has enabled Rogue to capture and act on the data surrounding their supply chains.
Rogue Ales, headquartered in Newport, OR, is an alcoholic beverage company founded in 1988 that produces beer, wine, cider, and distilled spirits. Their ales have won over 1,800 awards at various brewing competitions.
Rogue’s brewing operation is unique in that the company’s subsidiary, Rogue Farms (founded in 2008), grows all of the ingredients used. The company believes that their “Ground to Glass, Grow your Own Revolution” is a key tenet to their success. Rogue Ales leverages the Internet of Things (IoT) to ensure that their supply chain is able to deliver the highest-quality ingredients to their breweries just in time.
The trend toward freshness
According to AT Kearney, 93% of consumers consider freshness to be the most important criterion when purchasing foods. According to the USDA, the sale of organic foods in the U.S. has more than tripled from approximately $12B in 2005 to over $35B in 2015 (data for 2016-2018 was not immediately available).
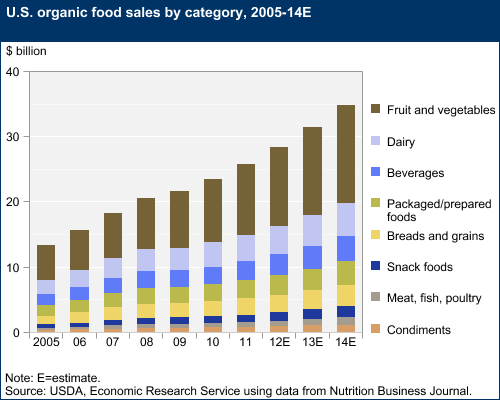
Consumer desire for freshness and high quality is influencing the beer brewing industry. According to the American Brewers Association, the number of craft breweries in the United States has increased from 122 in 1973 to over 6,300 in 2017.
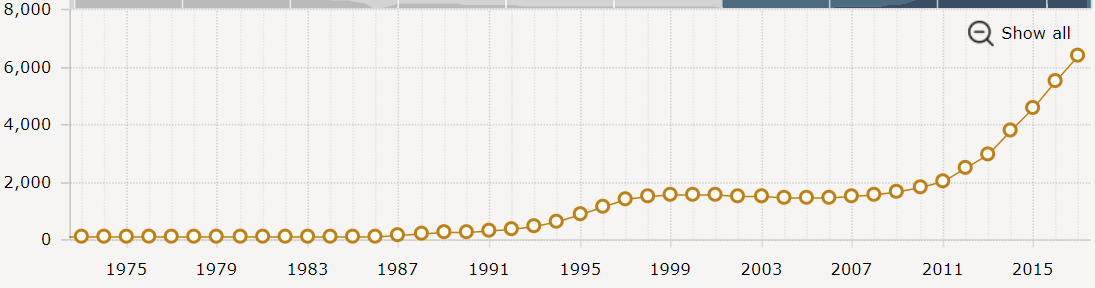
As the competition between breweries intensifies, brewers are constantly looking for key ways to differentiate their beers from their competitors in this $111.4B market. Most beer sales are through microbreweries (defined as a brewery producing less than 15,000 barrels per year and at least 75% of beer sold off-site via distributors or wholesalers). Rogue Ales has made freshness a key value-add differentiator for its brand, selling over 325,000 gallons in 2016. In a Market Watch article, Rogue’s president, Brett Joyce, says:
What it means is that we have to get better all the way around. The quality has to go up. Just having products isn’t enough. You better have a strategic plan to go to market, retailer support, good follow-up and good sales people. It’s a real business now.
With the establishment of Rogue Farms in 2008, Rogue began producing their own ingredients, breaking tradition with most breweries, who acquire ingredients from traditional wholesalers. Rogue has a 52-acre hop farm, located approximately two hours from the brewery, where it produces its entire hop supply. Rogue states that:
Growing hops is an expensive and time-consuming endeavor, but it also helps to guarantee our supply and quality while allowing us to keep our Brewmaster, John ‘More Hops’ Maier, happy with unique, aromatic hops.
The control Rogue Ales has over Rogue Farms gives the brewery a unique advantage in being able to produce specialty ingredients for its core and specialty beers. At Rogue Farms, Rogue grows or produces:
- 10 varieties of hops
- Two varieties of malting barley
- Rye
- Pumpkins
- Marionberries
- Jalapeños
- Honey
The challenges of using fresh “wet” hops in beer
A basic beer recipe only has four ingredients: malted barley, water, hops, and yeast. Of these ingredients, hops are the most difficult to source, store, and transport due to their perishability. Most brewers use pelletized, dried, hop pellets. Rogue uses fresh (or “wet”) hops in their ales, harvested from Rogue Farms. Fresh hops give their beer a fresher taste, as the hops’ aromatic qualities are not damaged by drying and pelletization.
Fresh hops, once harvested, must land in a brew vat within 12 hours and cannot be exposed to excessive heat, air, or humidity during transport or their volatile aroma compounds will degrade and produce aromas of “skunk” and “compost”. To ensure the highest quality of hops, Rogue has turned to technology to ensure that its supply chain is delivering the freshest possible hops to the brewery.
Using the Internet of Things to build quality into Rogue’s supply chain
The vertical integration of Rogue Ales and Rogue Farms gives Rogue a unique advantage in being able to leverage new technologies to ensure it sources the highest quality ingredients possible directly from their farm to their brewery. Rogue Ales uses Intel’s Connected Logistics Platform to manage its hops supply chain. Intel’s platform is a logistics management solution that couples Internet of things (IoT) devices with a cloud-based data analytics system. These IoT devices are one-time-use sensor tags that attach to shipments and collect data (e.g. temperature, humidity, location, etc.). This data is sent over a proprietary wireless protocol to a central server where the data is aggregated and analyzed in real time.
[bctt tweet=”The Internet of Things has enabled companies like Rogue to capture and act on the data surrounding their supply chains. Companies are able to make smart decisions that bring cost savings and flow directly to their bottom line.” username=”Fronetics”]
The system tracks shipments and collects data during every facet of the supply chain, ensuring that quality thresholds are maintained and any problems with the shipped goods can be immediately corrected (for example, if one of the trucks runs into traffic, the others can be intelligently rerouted). It is estimated that 30% of all perishable products shipped in the United States become spoiled during their journey from the farm.
After the wet hops are picked, Rogue attaches three trackers to each shipment: at the top, middle, and bottom of the bale of hops. These trackers measure temperature, humidity, and location. Rogue can ensure that the hops have been kept in the proper environment and that they have not spent too much time in transit.
If a shipment does not meet quality standards, it can be discarded before it is used in a beer batch, reducing waste and ensuring that Rogue does not waste its precious brewing capacity brewing beer that will later need to be dumped for quality reasons. The location of the shipment is updated every ten minutes, and once the hops have reached the halfway point, Rogue starts the brewing process. This ensures that the hops arrive just in time and go directly from the truck into the brewing kettle.
The Internet of Things has enabled companies like Rogue to capture and, more importantly, act on the data surrounding their supply chains. Companies are able to make smart decisions that bring cost savings and flow directly to their bottom line.
This article was written by Zachary Richards, an MBA student at the Peter T. Paul College of Business and Economics at the University of New Hampshire. Zach is a Software Engineer at Pegasystems, Inc., where he specializes in back-end Java development, data structures, and agile development practices. He graduated from Worcester Polytechnic Institute in 2016 with a B.S. in Computer Science.
Related posts:
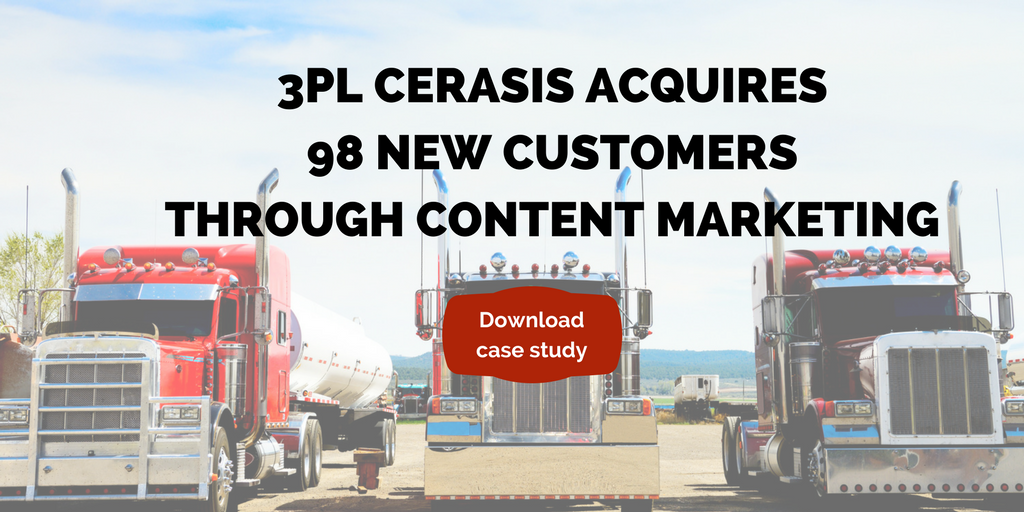