by Elizabeth Hines | Apr 3, 2018 | Blog, Content Marketing, Current Events, Manufacturing & Distribution, Marketing, Supply Chain
In many cases, automation in manufacturing creates leaner, more efficient operations. Efficiency facilitates new opportunities and business growth, which in turn allow for job creation.
The rise of artificial intelligence (AI) and its applications in manufacturing have driven a palpable fear that mass job loss is on the horizon. We have to wonder: is the threat as real and as imminent as many think? Like many things, the answer is more nuanced than a simple yes or no.
A McKinsey Global Institute report predicts that automation could cause the loss of between 39 and 73 million jobs by 2030 in the U.S. alone. Clearly, the AI genie will not be put back into its bottle. However, this doesn’t mean that all jobs across all sectors will be affected evenly.
Generally, low-skill jobs are more susceptible to replacement by AI. This is especially true in industries like retail, which has worked to automate many aspects along the purchase journey, including processes designed to get packages into consumers’ hands faster.
Not the end of the world
Oddly enough, 73 million lost jobs doesn’t spell all doom and gloom. Yes, people will lose jobs — that is inevitable. Automation, however, will create many more.
Think about it: In many cases, automation creates leaner, more efficient operations. Efficiency facilitates new market opportunities and business growth, which in turn allow for expansion and job creation. And these new jobs aren’t the low-skill positions of their pre-automation predecessors. They’re operating new technology, supervising automated processes, and other higher-paying opportunities.
Amazon: Case in point
Consider the retail industry’s brick-and-mortar boom and bust and the rise of e-commerce. As stores shuttered, companies had to downsize the number of individuals they employed. Then, as e-commerce boomed, e-retailing companies were able to bring on more employees — often at higher salaries than in traditional retail.
Amazon’s expansion to the “once-thriving factory town” of Fall River, Mass., offers a prime example. The city, which boasted nearly 20,000 manufacturing jobs in 1991, saw that number dip below 4,000 by 2015 — in large part due to automation. The 2016 arrival of an Amazon fulfillment center was the single largest job-creation event in recent memory.
Employment at the Fall River center has crept above 2,000 in just over a year. And it’s apparent that number will keep rising and that humans won’t be phased out anytime soon. In fact, rather than replace human workers, Amazon’s technology helps each become more efficient. That stimulates Amazon’s growth and the need for more fulfillment centers and more talent to fill those jobs.
While the majority of the Fall River center’s jobs are not skilled and pay reflects that, other benefits such as overtime, tuition aid, and company shares make annual compensation comparable to or better than what local textile mills once paid. Fulfillment center jobs certainly pay above traditional retail and offer employees the opportunity to work withartificial intelligence — rather than in competition with it.
A double-edged sword
AI in the warehouse may stimulate job growth. But those most likely to lose their jobs to automation — low-skill workers — may not possess the transferable skills to be successful in the new wave of jobs created by technology. For example, would a former factory worker who put together boxes for fulfillment be hirable for a position operating custom box-cutting machinery?
Amazon, again, exemplifies a solution. The company offers its workers significant training and education to breach any skill gaps. Those who have never had experience in a warehouse or operating technology will need companies to invest in their training to ensure those who have lost their jobs to automation will have a place in the new economy.
History repeating
This isn’t the first time we’ve encountered such an issue. Before ATMs were the ubiquitous cash-dispensing machines, many thought them the great disruptor of the banking industry. The bank teller’s role was sure to become obsolete.
What actually happened is that ATMs led to more efficiently run banks. While some jobs were lost, banks were actually able to open up more branch locations, which led to the creation of more jobs.
Will automation in the warehouse cause the same scenario to happen? Will organizations become more efficient, allowing them to grow and hire more workers at better, higher paying jobs? In many cases, it looks like it already has.
Related posts:
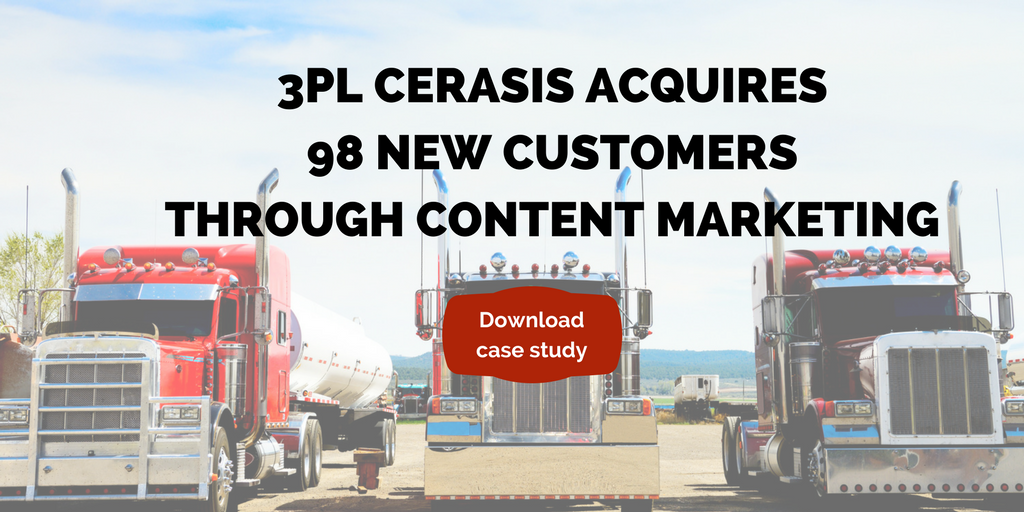
by Elizabeth Hines | Jan 4, 2018 | Blog, Current Events, Supply Chain, Transportation & Trucking
The FMCSA is not certifying ELD vendors’ products, which means carriers must ensure devices meet the organization’s technical specifications.
On December 18, new electronic logging device (ELD) regulations went into effect for commercial vehicle fleets across the U.S. The ELD mandate has caused major waves in the transportation industry. But it has the potential to rock supply chains and manufacturers around the globe — and not just because of anticipated transportation disruptions and increases in costs.
ELD manufacturers must comply with technical specifications outlined by the Federal Motor Carrier Safety Administration (FMCSA). They must also register their devices with the FMCSA. Motor carriers might assume that selecting a device that vendors are promoting as “FMCSA certified” would be a simple solution. Amazingly, however, that certification may not be worth the paper it’s printed on.
When does “certified” not mean “verified?”
Last year the FMCSA directed carriers to a site where they could find a list of registered ELDs. The problem with this is that the devices on this list are self-certified by the manufacturer. There’s no guarantee that they actually meet FMCSA guidelines.
To appear on the FMCSA’s list, ELD manufacturers must submit certain documents, including malfunction and diagnostics and product serial numbers. However, to gauge if their product is compliant, manufacturers must conduct their own tests. And the FMSCA is not vetting documentation of the testing.
The problem with this is fairly obvious. Without mandatory testing from a neutral, third-party source, devices are subject to only the rigor of their own manufacturer’s testing. They may not follow the FMCSA’s test specifications. And, of course, less-than-honorable manufacturers could use the lack of oversight to their advantage.
Consequences, however, will fall entirely on the shoulders of the operators and their carriers using non-compliant ELDs.
Compliant today, not tomorrow
Motor carriers purchase these systems under good faith that they will meet the FMCSA’s performance requirements once in use. But the possibility is looming that some ELDs may be noncompliant. Then what?
Carriers have eight days from the time an ELD is determined to be noncompliant to replace it with a compliant one. While drivers can temporarily use paper logs, this obviously isn’t a real solution, and will leave carriers scrambling to get their ducks in a row.
Due diligence
Before selecting an ELD vendor, carriers need to understand the details of compliance and hold vendors to those standards.
Carriers should push vendors for specific information about compliance with FMCSA test specifications. Or they should seek vendors who have opted to use third-party testing companies, such as PIT Group, to independently verify ELDs meet FMCSA standards. Either way, carriers should test and verify the ELDs they have chosen for their fleets on their own to ensure compliance as soon as possible.
The coming months are bound to see many headaches from the confusion caused by FMCSA-certified (but not regulated) ELD devices. Carriers need to be aware of this now, so they can properly prepare for any issues that may arise.
Related posts:
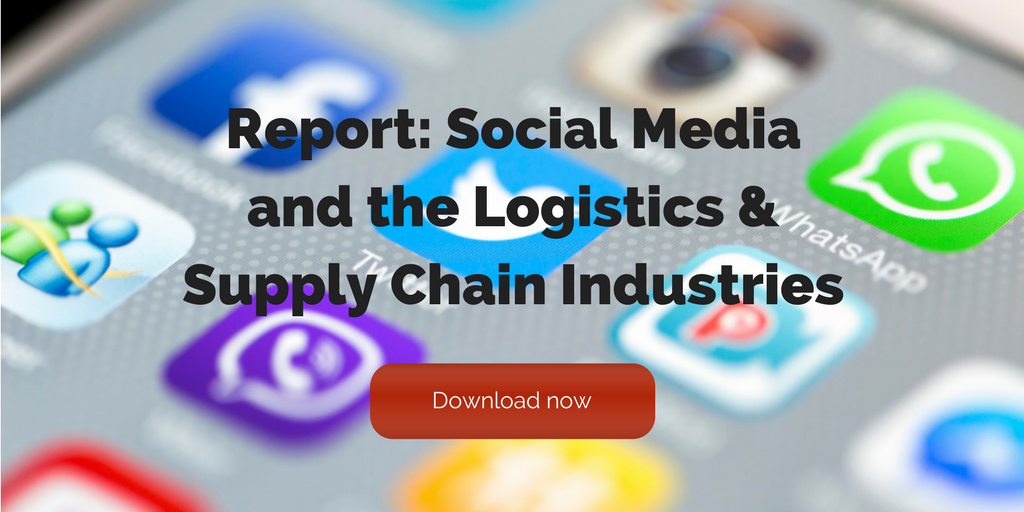
SaveSave
by Elizabeth Hines | Nov 13, 2017 | Blog, Consumer Electronics, Current Events, Manufacturing & Distribution, Strategy, Supply Chain
As sales and consumer desire continue to increase for drones and home assistants, the second-life market has a huge opportunity for growth.
Consumers are becoming ever-more enamored with their gadgets and toys. Drones and home assistants are becoming more ubiquitous in our homes (and flying around our skies). However, when these machines run their course — either because they break, or a newer model comes out — is there still use for them?
The market for gadgets
The marketplace for drones is an ever-growing one. Last year drone sales increased by an astounding 60%, and revenue grew to $4.5 billion. The drone market can be segmented into two categories — personal and commercial. Personal drones, which many consumers use for photography, is predicted to grow 40% this year, while commercial drones, which can be used for survey maps and delivery services, are expected to grow 60%.
While personal-use drones dominate unit sales, commercial-drone sales — which make up only about 6% of the market — are projected to represent 60% of the market’s revenue. This is due to the high cost of commercial drones, some with costs that exceed $100,000.
Home assistants are another intriguing category on the rise. These products are intended to control various devices in your home, such as thermostats, lighting, and security. These products also allow an individual to shop online using voice commands.
The frontrunner for this market has been Amazon’s Echo devices. As the primary nature of Amazon’s business is e-retail, the Echo device plays perfectly into this. By making it simple and easy to make Amazon purchases through voice command, these devices have great potential to bolster Amazon’s bottom line.
While this market is still in its early stages, Gartner Research expects tremendous growth, projecting $2.1 billion in consumer spending on personal home assistants by the year 2020.
The second-life market
So what becomes of these products as we replace them with newer models? Smart phones offer a sensible comparison when looking at the second-life market for these products. In 2016, consumers sold or traded in used cell phone devices for an average of $140 per device, generating a total of $17 billion worldwide. This selling and trading doesn’t just end after one transaction. It is predicted that at least 10% of premium ($500 and up) smartphones will have at least three users before they are retired.
We can draw a parallel about second-life potential between drones/home assistants and cell phones. Advances in technology render previous models obsolete or, at best, out of date. Consumers who can afford them will gravitate toward newer products. As with cell phones, they will generally look to recoup some of the cost for the newer product by selling or trading in the old one. These can then be sold to consumers looking for less expensive, older models. Even in the case of drones that crash, parts can be salvaged and sold to individuals that are looking to build their own drones.
The markets for these products are all still in early stages, so second-life markets are still in growth stages as well. As sales and consumer desire continue to increase for drones and home assistants, their life cycle will go on long after the first owners have moved on to newer models.
This post originally appeared on EBN Online.
Related posts:
by Elizabeth Hines | Oct 10, 2017 | Blog, Consumer Electronics, Current Events, Manufacturing & Distribution, Strategy, Supply Chain
Of legal obligation, financial incentives, and convenience, what best drives consumers to practice proper e-waste recycling?
The United States is a nation of consumers, and there are few things we enjoy more than our electronic gadgets. Unfortunately, for every new device — or upgrade — introduced to the market, there’s an older model that becomes obsolete.
The world produced 41.8 million metric tons of e-waste in 2014, according to a study published by the United Nations University. So how can we combat this growing problem?
The recycling option… and sometimes law
Recycling products that we’re no longer using is always good practice. It can help protect the environment from hazards that are in our electronics and batteries. And many times, the device can be refurbished and donated to a person in need.
Sometimes just asking people to recycle isn’t enough, though. Some governments have made it illegal not to recycle. For example, the EU has gone so far as to institute the Battery Directive. Understanding that batteries commonly contain elements such as mercury, cadmium, and lead, the EU has set an objective of improving environmental performances of batteries, and setting a standard for their waste management as well.
In the United States, cities like New York City have made it illegal to simply throw out electronic devices. Instead, residents need to bring their devices to a recycling center, many of them conveniently located at other electronic retail outlets.
Incentives
If less hazardous waste in landfills, a cleaner environment, and compliance with laws and regulations aren’t enough, how about saving money as an incentive to recycle e-waste?
Many manufacturers and retailers offer discounts on purchases with the return of old devices. Best Buy, for example, has experimented with trade-in and recycling programs that offer gift cards or cash for customers who bring in old devices. As programs like this can leave the retailer struggling to break even, they often aren’t financially attractive enough to be the sole incentive drawing consumers to recycle e-waste.
But one incentive that is very effective is also, probably, the most obvious — convenience. One survey found that 43% of respondents would be more likely to recycle e-waste were cell phone and battery recycling part of curb-side pickup.
The convenience of curb-side pickup for paper, plastic, and aluminum helped to make recycling ubiquitous in neighborhoods across the country. It’s the same thought process that leads researchers to believe that the convenience of a curb-side pickup will encourage more individuals to recycle their electronic devices and batteries.
This post originally appeared on EBN Online.
Related posts:
by Elizabeth Hines | Aug 21, 2017 | Blog, Manufacturing & Distribution, Strategy, Supply Chain
The DoD is gravitating toward advanced authenticating technologies as a means to root out counterfeit electronics in the U.S. military.
Counterfeit electronic parts are a well-documented problem in the military supply chain. At the time of a 2012 Senate Armed Services Committee report that brought the issue to the forefront, over a million counterfeit electronic parts had entered the U.S. military supply chain. The year-long investigation behind the report found 1,800 cases of counterfeits within military systems, ranging from thermal weapon sights to computers to airplanes.
The dangers of fake parts go without saying: Counterfeits not only threaten U.S. national security, but also endanger the lives of servicemen. So what steps is the Department of Defense (DoD) taking to forestall this problem?
A number of firms have developed advanced technologies that aim to authenticate genuine parts and root out counterfeits. Let’s look at a few of the projects for which the government has chosen to see where we might be heading in terms of amelioration.
DNA marking
When you think of computer chips, the first thing that comes to mind probably isn’t plant DNA. But that’s where the Pentagon’s procurement arm, the Defense Logistics Agency, is turning. DLA has contracted biotechnology firm Applied DNA Sciences to rearrange DNA from plants into unique sequences that are encrypted and attached to chips and other electronic components to distinguish authenticity.
Users simply shine a light on the part in question, on which a mark will light up to confirm the existence of the DNA. A quick swab of mark is then submitted for DNA analysis, which determines whether the part is genuine.
If an individual attempts to tamper with the chip in any way, it will distort or remove the DNA mark. The smudged or missing mark should immediately trigger a red flag for whoever is inspecting the part.
Optical scanning
Sometimes the best innovations are the byproducts of other innovations. That’s what happened with optical scanning.
The army originally brought on ChromoLogic LLC for a separate project looking at DNA’s tagging and tracking capabilities. The goal of the research was to find out if a barcoding system could be used with the DNA to improve security.
However, ChromoLogic researchers discovered that optical scanning technology developed to tag and track the DNA code also was capable of distinguishing an authentic part from a counterfeit by reading the component’s surface layer. Because counterfeit parts are forged primarily by altering the surface layer, optical scanning takes as little as one second.
SHIELD
The Defense Advanced Research Projects Agency’s (DARPA) Supply Chain Hardware Integrity for Electronics Defense (SHIELD) program is in the process of developing a small “dielet” that can verify the authenticity of electronic components.
Manufacturers insert the dielet into a component during production without compromising the part’s performance or design. A user can later employ a hand-held probe to provide power to the dielet. The dielet’s serial number uploads to a server, which sends back an encrypted message and data that could indicate tampering.
The goal, according to DARPA Program Manager Kerry Bernstein, is to “build the world’s smallest, highly integrated computer chip.” Success for this program, he says, means that any untrained operator along any point in the supply chain would be able to check and authenticate any component used by the Department of Defense or the commercial sector.
These three advanced authenticating technologies offer promising solutions to this widespread problem compromising the U.S. military supply chain. Which will prevail — if any? With counterfeits infiltrating the system at an alarming pace, the firms developing these technologies have a weighty task in front of them.
This post originally appeared on EBN Online.
Related posts: