by Elizabeth Hines | Jan 22, 2014 | Blog, Strategy, Supply Chain
This post was originally published on EBN.
Packaging optimization is critical to supply chain optimization. To catch big advantages, change your mindset and make packaging a forethought rather than an afterthought.
In a Packaging World article, Elisha Tropper, president and CEO of Cambridge Seals Security (CSS), describes how packaging is typically thought of by manufacturers:
An afterthought… for most [manufacturers of industrial products] packaging is not a consideration. They are manufacturers; they are not packagers. They make an industrial product, and industrial products are dropped into boxes. But whether a box is an inch bigger or an inch smaller, what does it matter?
The truth is, it matters a lot. If you want to optimize your supply chain you need to optimize your packaging. This means changing your mindset when it comes to packaging — packaging needs to become an early consideration.
There are several components of packaging. For example, the product itself, the box or container in which the product is placed to sell, and the box or container the items are placed in for shipping. Each of these components are opportunities for optimization.
Package (re)design
A May 2013 industry study by Freedonia forecasts that pallet use in the US will grow 2.4 percent annually to 2.6 billion in 2017. The study also reported that demand for new pallets is expected in increased by 3.5 percent annually to 1.3 billion units.
The International Organization for Standardization sets the standards for pallet size; there are currently six pallet standards. The most common size used in the United States is Grocery Manufacturers pallet, which measures 48 inches by 48 inches. The dimensions of a pallet are not always considered with respect to packaging; this is a costly mistake.
Let’s look at an example previously highlighted in Supply Chain Digest. Adalis (now H.B. Fuller Adhesive Coated Solutions) worked with a telecommunications company to redesign their packaging to optimize pallet use. By reducing the size of each unit package by 1.5 inches in one dimension, the company was able to increase the number of units that could fit on the pallet by 150 percent (from 120 to 300 units). The result was a signification reduction packaging (materials) costs and transportation costs.
Product (re)design
Product design or redesign is another way to optimize packaging to optimize your supply chain.
Let’s go back to Elisha Tropper. Tropper was the former owner of a packaging convert and his packaging consultancy, T3 Associates, acquired CSS in 2010. When Tropper took over at CSS he challenged the company to take packaging optimization into consideration at the point of product design. The company took the challenge and redesigned the product. A significant reduction in package size and materials usage resulted. According to Trooper: “A standard pallet of our boxes can hold about 120,000 seals, while that same pallet will hold only about 80,000 of our competitor’s seals.”
Ikea provides another example, which Colin White outlines in his book Strategic Management. When Ikea first began manufacturing its Bang mug, 864 mugs could fit on a pallet. Ikea redesigned the rim of the mug so as to maximize pallet efficiency — Ikea was able to increase the number of mugs per pallet to 1,280. The company decided it could go further. Another redesign increased the number of mugs per pallet to 2,024. As a result of the product redesign, the company reduced shipping costs by 60 percent.
Outside the box
Ikea has taken packaging optimization for supply chain optimization even further and has created a system called OptiLedge, which eliminates pallet use. Retailers using OptiLedge have realized a savings of been $200 to $300 per container.
Major factors for cost savings include a reduction in man hours to off-load (a savings of between 15 to 23 hours or more of labor per container), space savings (one truckload of OptiLedges would be the equivalent of 23 truckloads of traditional pallets), and weight (OptiLedge weighs under two pounds as compared with the 50 to 75 pounds that a traditional pallet weighs). In addition, OptiLedge eliminates underhang and increases fill rates.
Too often, everyone thinks of packing as the thing that gets thrown away. Smart manufacturers, though, will ensure that good money isn’t tossed out with the box or pallet.
by Elizabeth Hines | Jan 21, 2014 | Blog, Logistics, Strategy, Supply Chain
This post was originally published on EBN.
Summer is over, fall has arrived, and winter is right around the corner. As the days grow shorter and colder, don’t let inertia take over. Instead, put your packaging on a diet.
Here are three reasons why a packaging slim down will improve the health of your company’s supply chain and the world:
1. You can save money. By reducing the amount of packing you use for a product and/or by using right-size packaging, you can reduce transportation costs and materials costs.
For example, the packaging used for Apple’s iPhone 5 is 28 percent smaller than the packaging that was used for the original iPhone. The reduction in the size of the packaging translates into being able to fit 60 percent more iPhones on each shipping pallet. Apple points out that this saves the company one 747 flight for every 416,667 units they ship.
Poland Spring provides another example. Poland Spring has reduced the amount of resin that goes into the making of their bottles by a significant amount — from 14.6 grams of resin per bottle in 2005 to 9.2 grams of resin per bottle in 2012. Not only is the bottle 40 percent lighter (read: reduced transportation cost), the company also saves a sizeable amount of money each year in materials. In a recent Slate.com article Kim Jeffery, CEO of Nestle Waters North America (Poland Spring’s parent company), is quoted as saying:
You can’t be a public company and ask shareholders to bear the burden of higher costs just so you can be green. It has to be consistent with creating shareholder value. There needs to be a return on these investments. So, for example, when you use 200 million fewer pounds of resin a year, at 90 cents a pound, that’s a huge savings.
By my calculations, that’s a savings of $180 million annually.
2. It is better for the environment. Putting your packaging on a diet can reduce the amount of waste, CO2 emissions, deforestation, water use, water contamination, and hazardous material use.
In a September 2013 Packaging Digest article, Ron Sasine, senior director of packaging for private brands for Walmart, wrote that as a result of the company’s efforts to reduce packaging it was “able to reduce the overall greenhouse gas impact of our packaging by an average of 9.8 percent in our Walmart U.S. stores, 9.1 percent in our Sam’s Clubs in the U.S. and 16 percent in our Walmart Canada stores.”
3. It makes your customers happy. A 2012 survey conducted by Packaging World and DuPont Packaging & Industrial Polymers found that the primary focus of the packaging world over the next 10 years will shift from cost to sustainability. Specifically, the report found that 45 percent of those surveyed believe that perceived “greenness” will be important to consumers.
Additionally, a 2012 study released by Perception Research Services reported that in 2011 significantly more shoppers were more likely to choose environmentally friendly packaging than in 2010 (36 percent versus 28 percent), and that half of shoppers surveyed were willing to pay for environmentally friendly packaging.
Tell us your thoughts on packaging trends in the electronics industry. What’s important to you and your customers?
by Elizabeth Hines | Jan 21, 2014 | Blog, Logistics, Strategy, Supply Chain
This post was originally published on EBN.
Summer is over, fall has arrived, and winter is right around the corner. As the days grow shorter and colder, don’t let inertia take over. Instead, put your packaging on a diet.
Here are three reasons why a packaging slim down will improve the health of your company’s supply chain and the world:
1. You can save money. By reducing the amount of packing you use for a product and/or by using right-size packaging, you can reduce transportation costs and materials costs.
For example, the packaging used for Apple’s iPhone 5 is 28 percent smaller than the packaging that was used for the original iPhone. The reduction in the size of the packaging translates into being able to fit 60 percent more iPhones on each shipping pallet. Apple points out that this saves the company one 747 flight for every 416,667 units they ship.
Poland Spring provides another example. Poland Spring has reduced the amount of resin that goes into the making of their bottles by a significant amount — from 14.6 grams of resin per bottle in 2005 to 9.2 grams of resin per bottle in 2012. Not only is the bottle 40 percent lighter (read: reduced transportation cost), the company also saves a sizeable amount of money each year in materials. In a recent Slate.com article Kim Jeffery, CEO of Nestle Waters North America (Poland Spring’s parent company), is quoted as saying:
You can’t be a public company and ask shareholders to bear the burden of higher costs just so you can be green. It has to be consistent with creating shareholder value. There needs to be a return on these investments. So, for example, when you use 200 million fewer pounds of resin a year, at 90 cents a pound, that’s a huge savings.
By my calculations, that’s a savings of $180 million annually.
2. It is better for the environment. Putting your packaging on a diet can reduce the amount of waste, CO2 emissions, deforestation, water use, water contamination, and hazardous material use.
In a September 2013 Packaging Digest article, Ron Sasine, senior director of packaging for private brands for Walmart, wrote that as a result of the company’s efforts to reduce packaging it was “able to reduce the overall greenhouse gas impact of our packaging by an average of 9.8 percent in our Walmart U.S. stores, 9.1 percent in our Sam’s Clubs in the U.S. and 16 percent in our Walmart Canada stores.”
3. It makes your customers happy. A 2012 survey conducted by Packaging World and DuPont Packaging & Industrial Polymers found that the primary focus of the packaging world over the next 10 years will shift from cost to sustainability. Specifically, the report found that 45 percent of those surveyed believe that perceived “greenness” will be important to consumers.
Additionally, a 2012 study released by Perception Research Services reported that in 2011 significantly more shoppers were more likely to choose environmentally friendly packaging than in 2010 (36 percent versus 28 percent), and that half of shoppers surveyed were willing to pay for environmentally friendly packaging.
Tell us your thoughts on packaging trends in the electronics industry. What’s important to you and your customers?
by Elizabeth Hines | Nov 19, 2013 | Blog, Leadership, Strategy, Talent
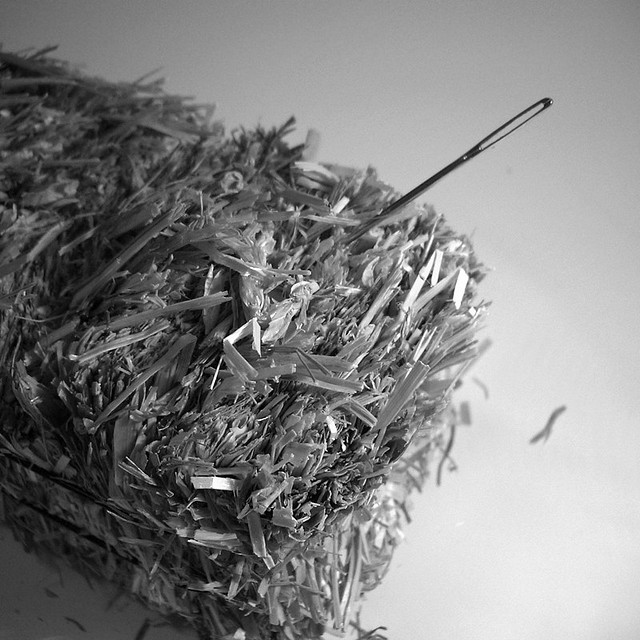
Career Builder identified Supply Chain Manager as a Top Growth Job for 2013. Why did supply chain manager make the short list (just 18 jobs made the list)? Supply chain manager has experienced an 8 percent job growth since 2010 and there is just one active candidate for every five posted jobs. Colleges and universities have recognized the demand – and opportunity. The Wall Street Journal recently reported that supply chain management is the “hot new MBA” and that “more than a half-dozen universities have recently introduced undergraduate majors, M.B.A. concentrations and even entire degree programs dedicated to procurement, inventory management and global supply-chain strategy.”
Finding the right person for a job opening is essential. Hiring the wrong person is a costly mistake not only financially, but also in terms of team morale and productivity. Given the demand for supply chain talent, the dearth of experienced talent, and an increasing number of newly graduated talent entering the job market – how do you find and hire the right person? Here are a few tips on how to hire.
Look across the industry
Look across the industry and identify individuals who are a good match to your company and the role.
Look within the company
Look inside your company. Is there someone who would thrive in a new role – even if the role is outside of their current field?
Look outside the industry
While this may seem counter intuitive, bringing in a talented professional from outside the industry could provide the fresh ideas and insight that your company.
Work with colleges and universities
Develop a relationship with colleges and universities. Work with the schools to identify upcoming or recent graduates who are/were stars. Another option is to establish an internship program with a school.
Work with a strategic advisory firm
Working with a strategic advisory firm is an option as well. This type of partnership, such as the ones I build with our clients, can make identifying the right talent for the right position easier. An advisory firm often has the pulse on where the most talented people are in the supply chain and logistics industry. This type of partner can launch a successful candidate search process, get new hires up and running, and help retain talent for the long run.
Be creative and have vision
Throughout the hiring process remember that creativity and vision are key.
Offer an out
Here is a great example of offering an out. Zappos pays new employees to quit. You read that right – the company pays new employees to quit their jobs. Once new employees have completed their 4 wee training program they are given “The Offer.” That is, they can choose to remain with the company or quit. If they choose to quit they will be paid for the time they worked and given an additional $3,000. The employee has 24 hours to decide. Why does the company do this? If the employee is not happy in the new position and not committed, it makes sense for both parties to cut and run.
by Elizabeth Hines | Nov 12, 2013 | Blog, Leadership, Strategy
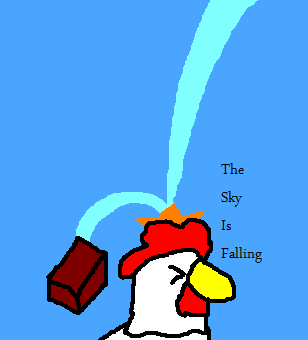
Source: www.Chickenmaker.net
A 2013 study conducted by Deloitte found that 64 percent of the global executives surveyed reported they had a risk management program in place that is specific to the supply chain. That being said, 45 percent of the respondents said their programs were somewhat effective or not effective at all. Respondents — especially those in the technology, industrial products, and diversified manufacturing sectors — reported that supply chain disruptions have become more costly over the past three years. They also cited margin erosion and sudden demand change as two of the most costly problems. Moreover, the 2013 Global Supply Chain and Risk Management Survey conducted by the MIT Forum for Supply Innovation and PricewaterhouseCoopers found that in the last 12 months more than 60 percent of companies surveyed reported that their performance indicators had dropped by more than three percent due to supply chain disruptions. While there are many factors which are likely to contribute to the issues pointed to in these studies, I believe that one is that companies focus largely developing risk management strategies to mitigate and cope cataclysmic events and not the day-to-day bumps in the road. As such, companies tend to be ill-prepared to handle the day-to-day bumps.
Big events are outlier events
Because big events such as hurricanes, tornados, tsunamis, and terrorist attacks can have a long-lasting impact and often visual impact on the logistics and supply chain industries they tend to stay top of mind. That being said, these events are outlier events. “Outlier events have much more influence than they should,” Professor Ananth Raman of Harvard Business School told David Stauffer for an article for the school’s website. M. Eric Johnson, director of the Center for Digital Strategies at Dartmouth College’s Tuck School of Business, told Stauffer for the same article, “Managers will often consider the giant risk but ignore the smaller risks that create friction in the supply chain.” When companies ignore the smaller risks, they do so at their peril.
You can’t ignore the day-to-day
Creating risk management strategies that focus on the everyday events is critical. Dealing with these events in a reactive and piecemeal fashion is inefficient and ineffective and can significantly hurt your company. The following are some tips on what to consider when developing an effective risk management strategy which focuses on the everyday risks:
- Employ a strategy that is robust and closely monitored.
- Put a leader in charge.
- Clearly define your process and make it comprehensive. Establish a well-defined process to mitigate events such as cashflow contingencies, client credit risk and default, competitor interruptions, inventory risk, data backup and recovery, key client attrition, employee satisfaction and retention, social media use and abuse, and reputation recovery.
- Make sure the strategy is both nimble and flexible. Being intractable can exacerbate issues.
- Don’t forget about human resources. Don’t be afraid to move employees into new roles. Moving an employee into a new role permanently (or for a specified period to deal with an event) is a powerful and effective strategy.
- Be first. If there is a problem, be sure that the clients hear about the problem from you. When you contact clients, tell them what the issue is and what you are doing to address it. Be clear, concise, and honest.
- Educate. Take the time to make sure everyone is educated about the strategy. If just one person knows the strategy, it will not be effective.
A big event might happen, but everyday events will happen… every day. Don’t give your company Chicken Little syndrome by focusing only on big events.