.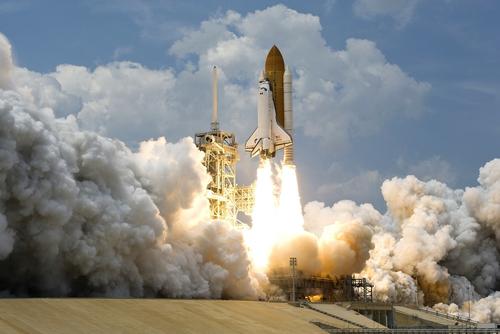
There is no easy answer to the burning question why the onshoring movement refuses to truly take off.
The issue of onshoring is frequently painted in black and white. While the media often likens the return of companies to the United States from overseas to a stampede, skeptics may be too quick to downplay the positive impact of the recent movement in manufacturing.
Nevertheless, those who were looking for a true Renaissance of American manufacturing have reason, at least so far, to be disappointed. Even among some high-profile companies — most notably Apple and GE — that announced their return with great fanfare, reality has set in. GE has battled high turnover rates at its re-opened Kentucky plants, as workers reportedly refused to perform certain tasks, while Apple has been stumped by the shortage of engineers.
Although the number of companies bringing production back home has risen significantly in recent years — from 64 in 2011 to 300 in 2014 — they are still outnumbered by those going in the opposite direction.
However, the issue is more complex than net gains or losses. According to new research by Morris Cohen, a Wharton School professor of operations and information management, and Hau L. Lee at Stanford University, “There is an unprecedented amount of restructuring going on.” In some cases, departments within the same company are onshoring and outsourcing at the same time, each weighing the perceived pros and cons differently.
In a Knowledge@Wharton interview, Cohen elaborated on the trend: “I’m going to go to China. I’m coming back from China. The same company simultaneously is making what seemed to be opposing decisions. And when you asked them why, they would give the same reasons. It’s because of labor costs. It’s because of market access. It’s because of this and that.”
In fact, they found there appears to be no dominant reason why companies make one decision or another in favor of onshoring or staying put.
And barriers seem to remain the same as when the onshoring movement began to gain momentum: The lack of skilled workers, coupled with an aging workforce, still rank high on the list of negatives. The rapid pace of offshoring in 1990s and early 2000s made younger generations lose faith in the viability of a manufacturing career.
Patrick Van den Bossche, the Americas lead partner at A.T. Kearney’s Strategic Operations Practice — which released its inaugural Reshoring Index last year — explained the problem on Manufacturing.net: “Think about it — if you have a kid in school, with everything that happened in the last few years, with manufacturing moving overseas as fast as it did, would you feel comfortable to tell your kid to develop a career in manufacturing? I don’t think so.”
At the same time, countries like China, Brazil, and Eastern Europe, previously known for their low-skilled labor, are quickly improving and investing in high-tech industries. With a greater pool of skilled workers abroad, a move back to the United States will seem less urgent. And with the arrival of robotics, the issue of labor costs will likely take on even less significance.
So the big question is, how should the United States stand up to the competition? What do you think?
A version of this article previously appeared on EBN Online.