This article is part of a series of articles written by MBA students and graduates from the University of New Hampshire Peter T. Paul College of Business and Economics.
Corey Ducharme is Green Belt Certified in Six Sigma. He has a BA in Business and is currently in the MBA program at the University of New Hampshire. He has consulted at major corporations including Johnson & Johnson, Universal Studios, Sony Pictures, Oklahoma Oil & Gas, and Suncor as a management consultant at D&A Management. He can be reached via e-mail.
We all use Six Sigma problem solving whether we know it or not
How do humans tend to solve problems? Consciously or unconsciously humans use a four-step method that is defined as:
Table 1: Traditional Problem Solving Process
In the above example, the root cause is identified – exercise and eating less equals losing weight – and verified. The conventional wisdom is proven true and there is little need to consider a more robust or analytical method. Most humans solve their day-to-day issues in this manner whether consciously or unconsciously. My root-cause analysis in this case (I exercise and eat less) is verified by the fact that I lost ten pounds and sustainable until my goal is achieved. (Losing 20 pounds).
Six Sigma Problem Solving 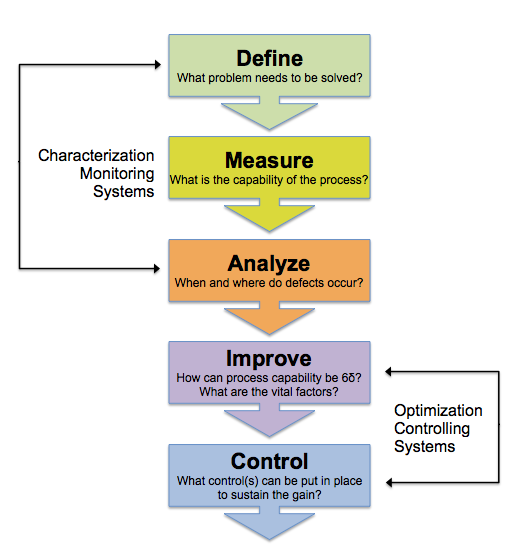
What if the root-cause lies outside of conventional wisdom or is difficult to determine?
These needle-in-a-haystack problems – due to limited business resources – cause businesses to lose revenue and lead to process failures, poor quality, and poor customer service. These types of problems are at the heart of Six Sigma Problem Solving and are a way to find the needle-in-the-haystack.
The Six Sigma methodology is based on the DMAIC process and using our weight loss example we begin to see the similarities between the two methods.
- Define Phase: What is the problem and set the end goal.
- Measure Phase: What is the current state?
- Analyze Phase: 1. Develop cause-and-effect analysis of problem. What are the real causes and prove cause and effect links.
- Improve Phase: Action
- Control Phase: 1. Verify improvement and 2. Sustainability
What differs between the phases of conventional and Six Sigma problem solving begins in the Analyze Phase. Six Sigma methodology demands the proof of cause be determined before a clear course of action is taken. The proof of cause must be data-driven as root-cause analysis is at the core of Six Sigma problem solving. It is also the reason that the Analyze phase is divided into the development of cause-effects and proof of cause-effect links.
The second difference is in the fifth phase. In the Traditional problem-solving methodology, verification comes in the form of losing weight. I can prove it by weighing myself. In Six Sigma problem solving, a two-step process is needed. Verification is essential (Did I improve?) and if so, a plan to sustain our gains is created. This is not necessary in a Traditional methodology because our cause-effect is proven (exercise/eat less = weight loss); however, in the Six Sigma methodology our cause-effect must be tested and verified.
The Linguistics of Six Sigma: Y=f(X)
To speak in the language of Six Sigma, we need to change ‘problem’ with ‘Y’ and ‘cause’ with ‘X’. The Y is the output and the X(s) are any inputs that are involved in producing the output. In other words, the Y = 100% customer satisfaction and X(s) are the variables that affect the level of customer satisfaction. For more, click the following link: Y=f(X).
Using Six Sigma linguistics and the DMAIC process, we can combine the Traditional problem solving steps in Table 1 and we see that our four-step process has become a more robust seven-step process. We can now use DMAIC to ask ourselves the most essential question:
If our root-cause analysis is discovered and proven true, then can the problem be solved or reduced by controlling or removing the cause(s)?
Table 2: DMAIC Problem Solving
Real World Example: Boeing
Boeing’s Six Sigma team in Everett, WA discovered that root cause analysis is often like finding a needle-in-a-haystack, especially for the maker of the world’s largest commercial twin-engine airplane with millions of components. (To read the entire story, click the following link: Problem-solving approach helps team pinpoint solution). Boeing discovered that recirculating air fans were being rejected during production, costing Boeing money in waste, removal, testing, and cost of replacing the component.
Boeing assembled a cross-functional ‘detective squad’ that included employees from Engineering, Quality, Manufacturing, Supply Management, Procurement, and their supplier Hamilton Sundstrand who began the problem-solving techniques of the DMAIC process by examining data from the fans and beginning root-cause analysis.
This analysis determined that Foreign Object Debris (FOD) damaged the fans and the test tools. Job done, right? Not according to Kent Kuiper, Six Sigma expert at Boeing, the team had to dig deeper. “For example,” he said, “when we found that FOD was a problem and determined the source for it, removing the FOD and replacing the fan wasn’t going to get us where we needed to go. We had to figure out a way to keep the FOD from happening again.”
Further inspection led the team to discover failures in ductwork caps and plastic sheeting – two items ironically intended to prevent FOD damage and two electrical issues. One failure of improperly modified test equipment and the second issue related to crimping procedures in manufacturing process that improved connections in the fans. The results? Although the FOD in the fans was the main X, the results were clear. “After 18 fan failures in two years, we went four and a half months without a rejection,” said Max Limb, a supplier field service representative. “We haven’t completely eliminated the rejections, but we’re close.”
“Our team has become well-versed in the concept of Six Sigma,” said Valerie Feiberti, Supply Management and Procurement Director of the Lean Promotion Team. “We feel very strongly that it provides a way to correct production-related problems and proactively design-in quality.”
Summary
The DMAIC methodology is essentially a series of common sense questions to determine root-cause analysis, identification of X(s), elimination of problems, and maintaining of gains. The DMAIC process asks the following questions:
- Define: What is the Y that is performing poorly?
- Measure: What is Y’s current performance?
- Analyze: What are the X(s)? Are they real?
- Improve: How can X(s) be controlled/eliminated?
- Control: How can X(s) be controlled to sustain gains in Y?
Six Sigma problem solving is the data-driven representation of the conscious or unconscious thinking we use to solve problems in our lives and can be used to solve may needle-in-a-haystack problems that vex businesses.